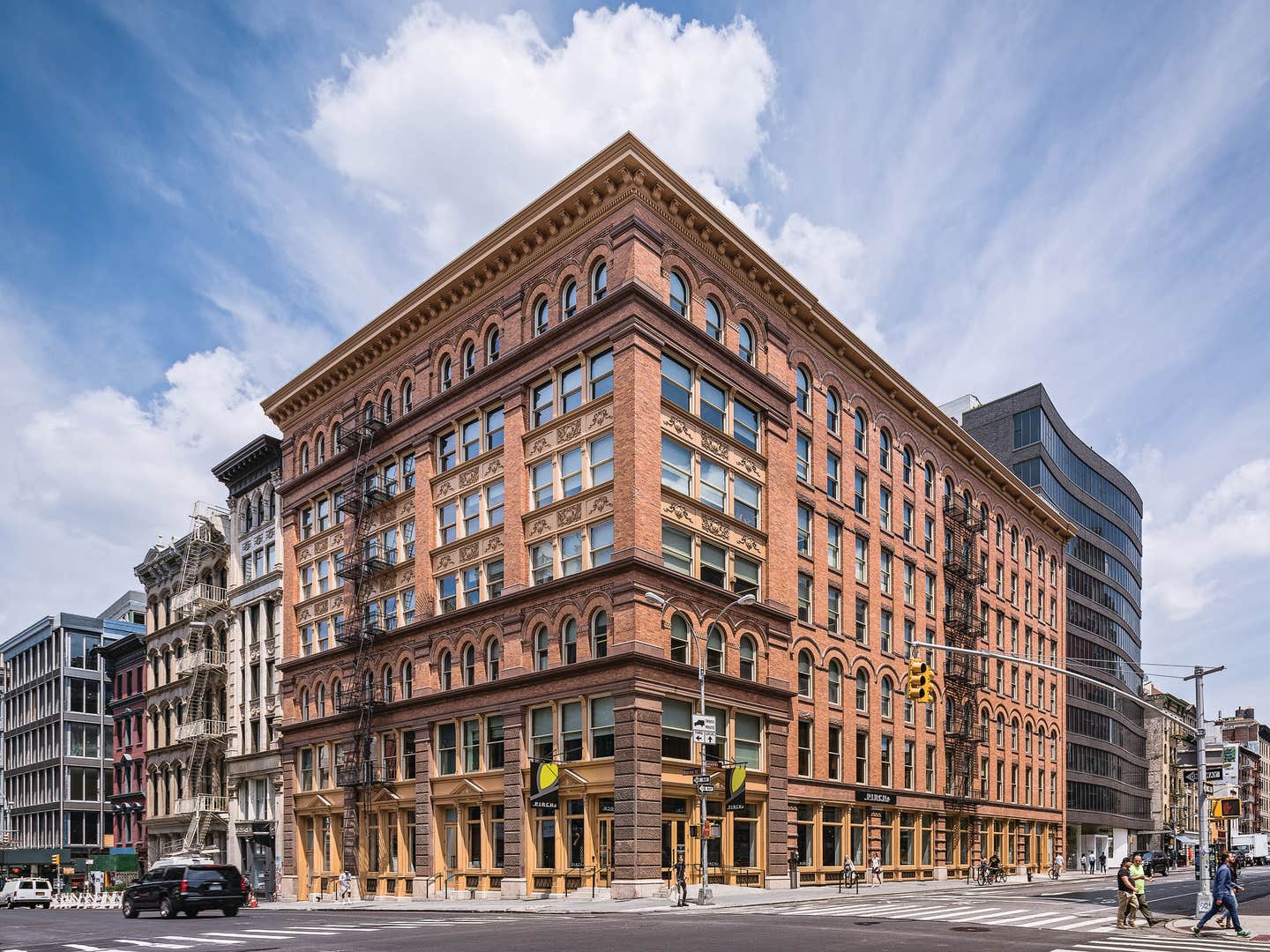
Palladio Awards 2017
Saving History in SoHo: The Knickerbocker Telephone Company Building
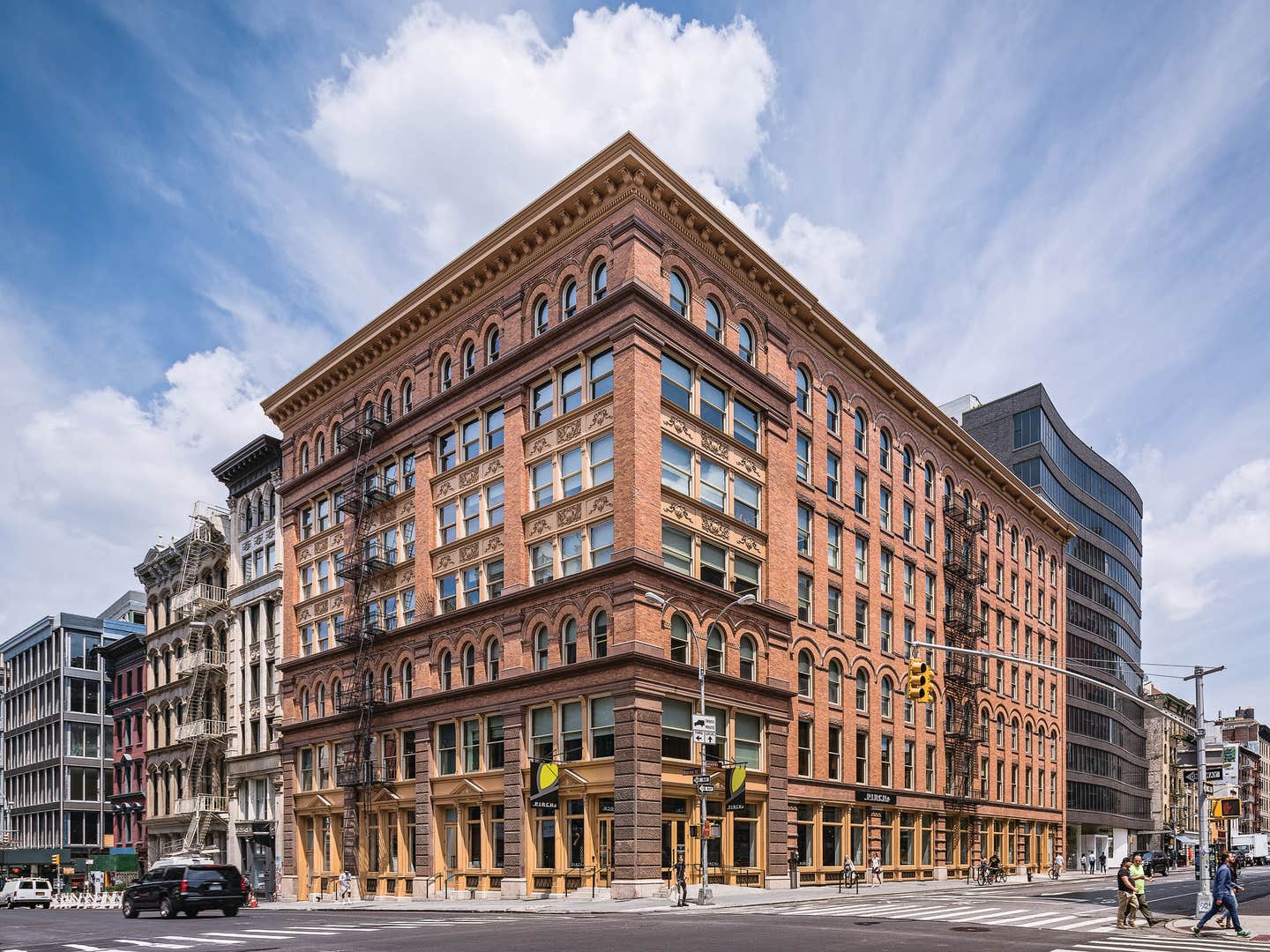
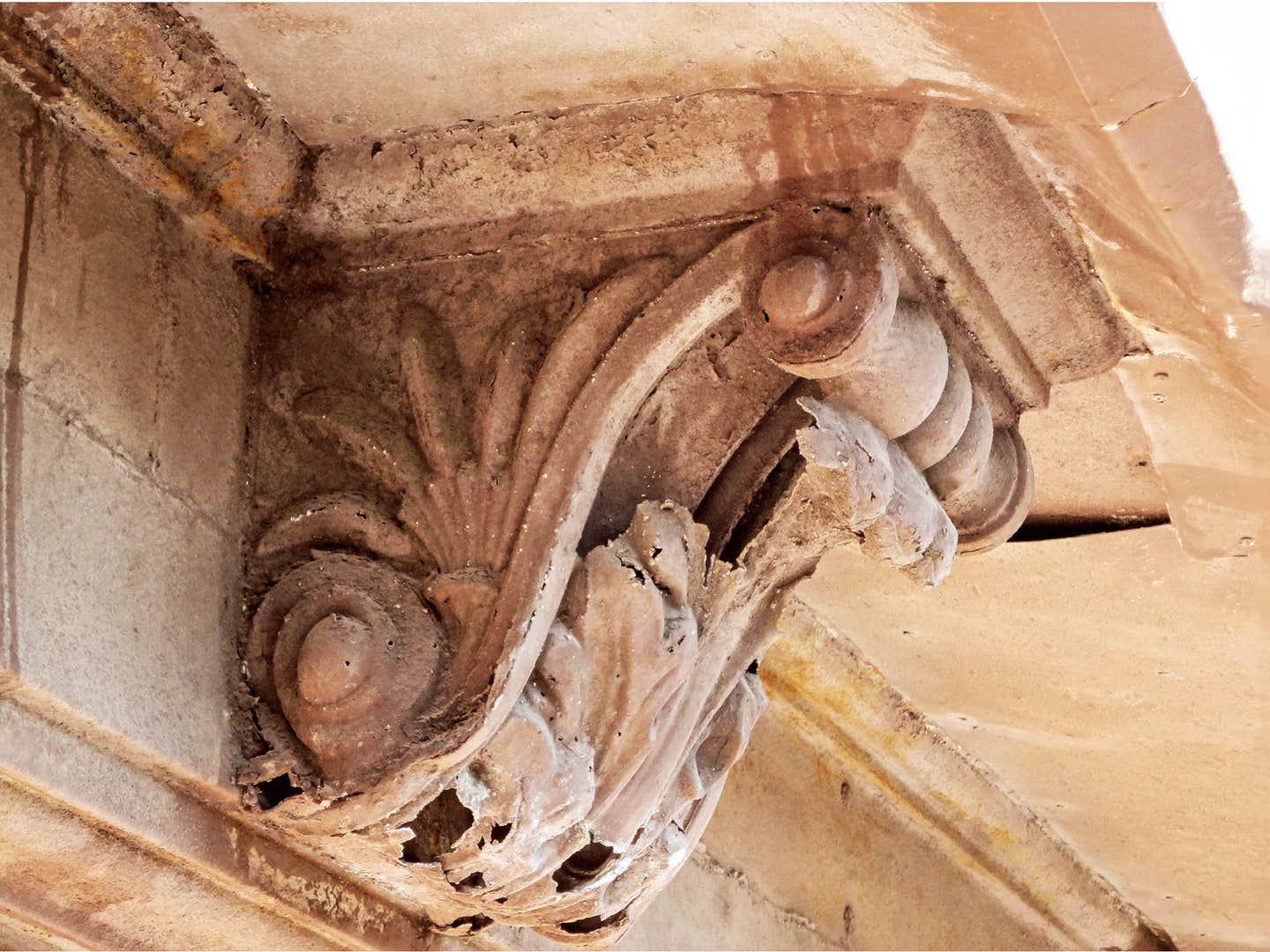
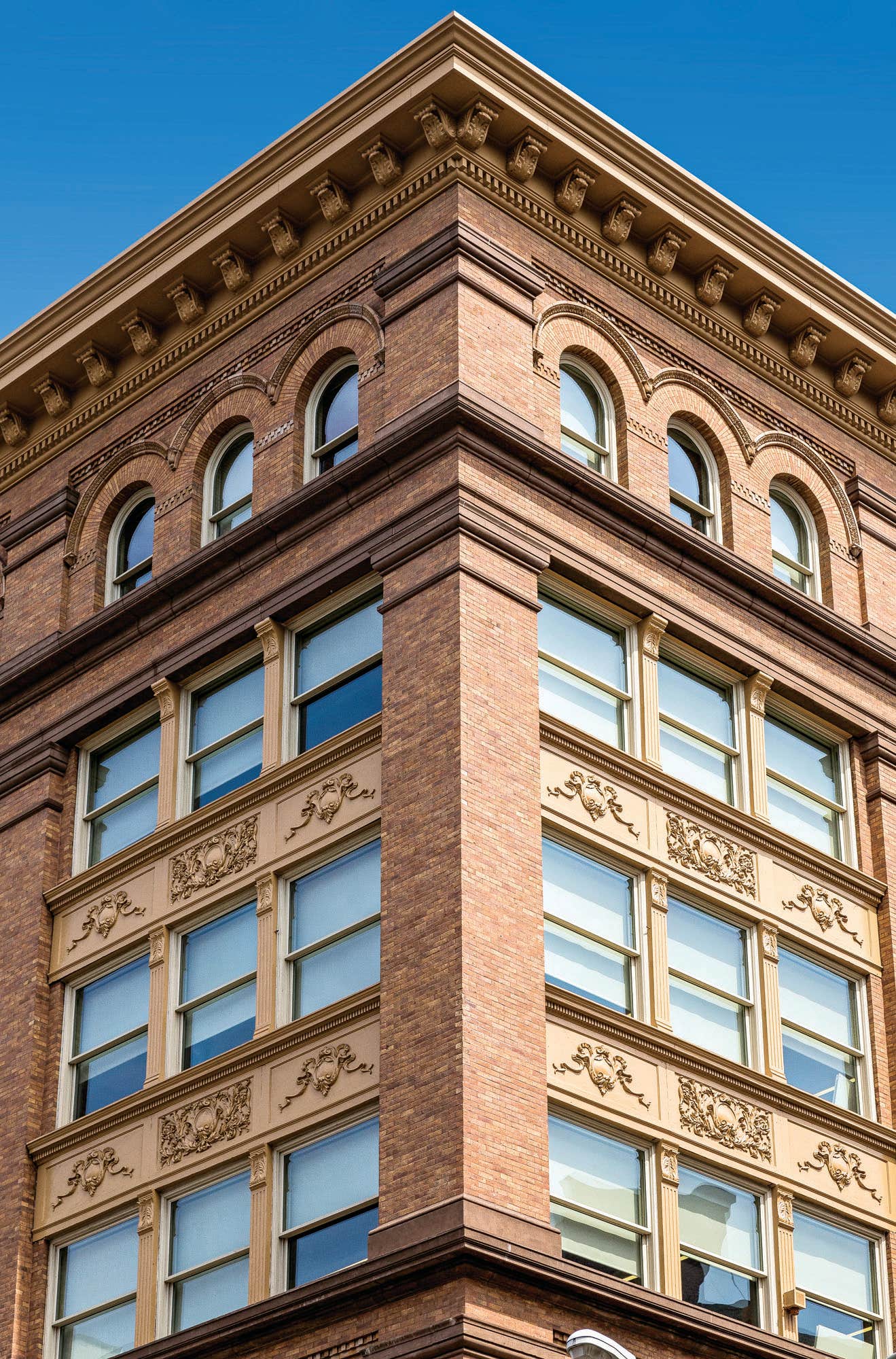
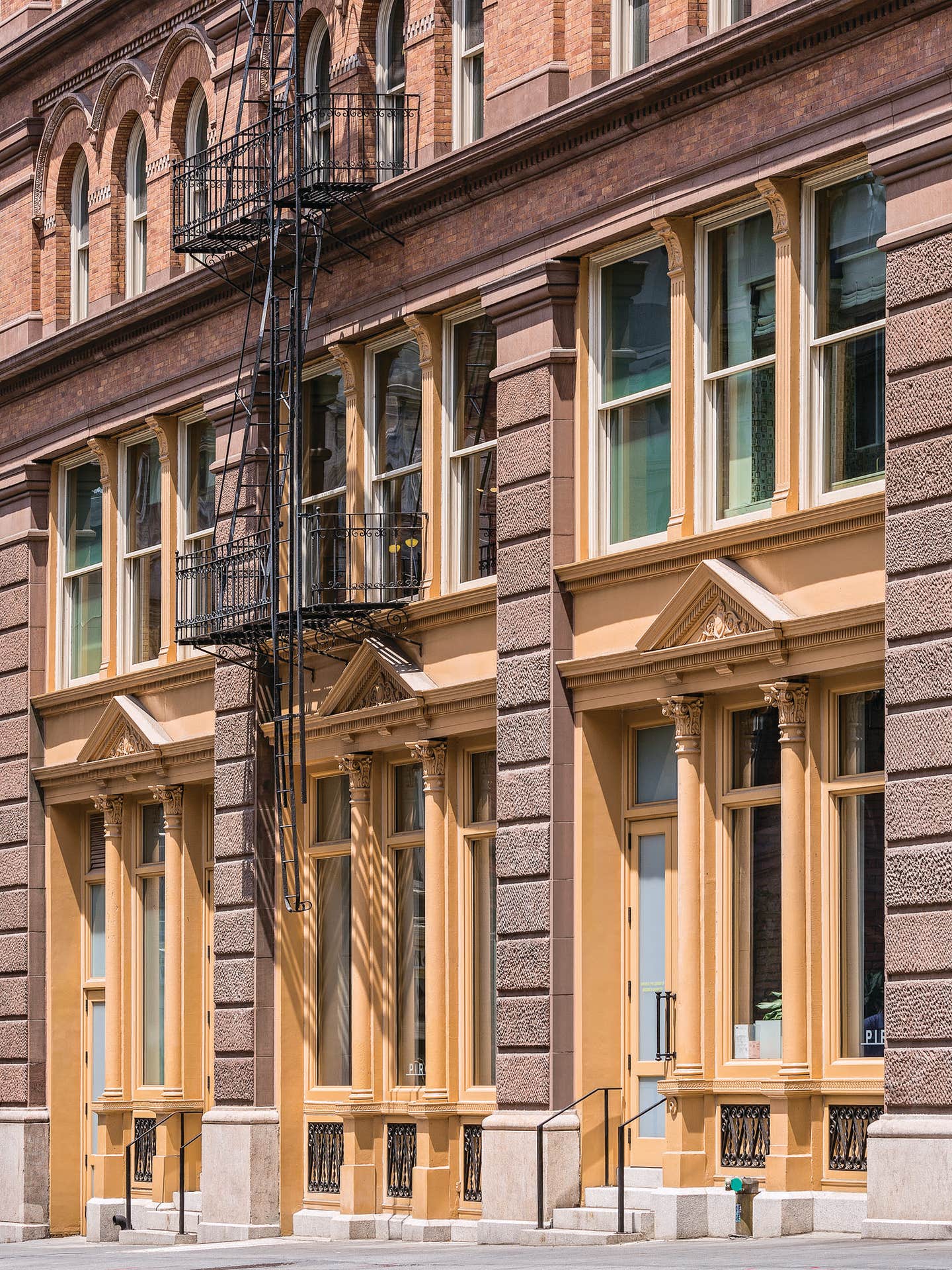
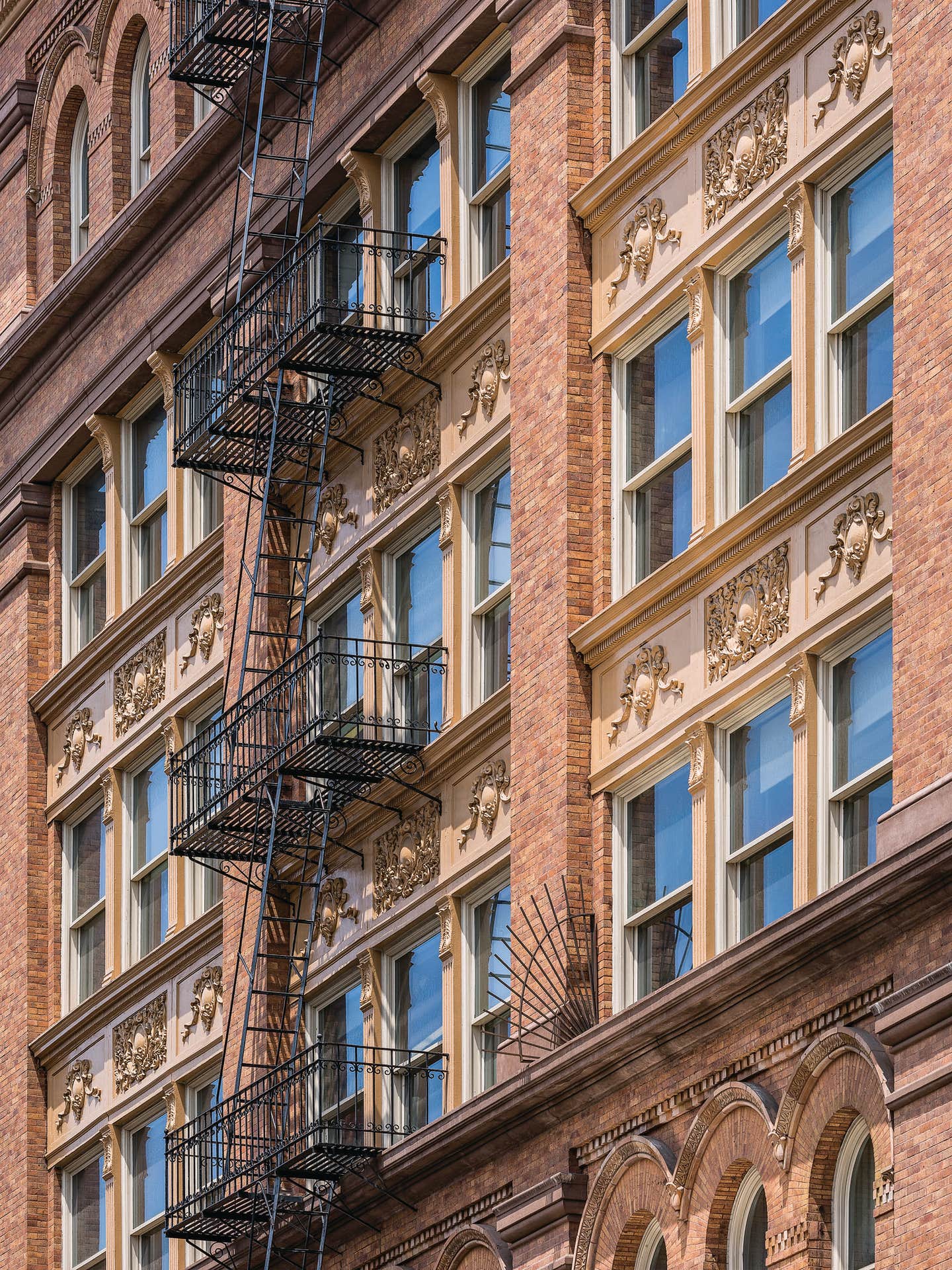
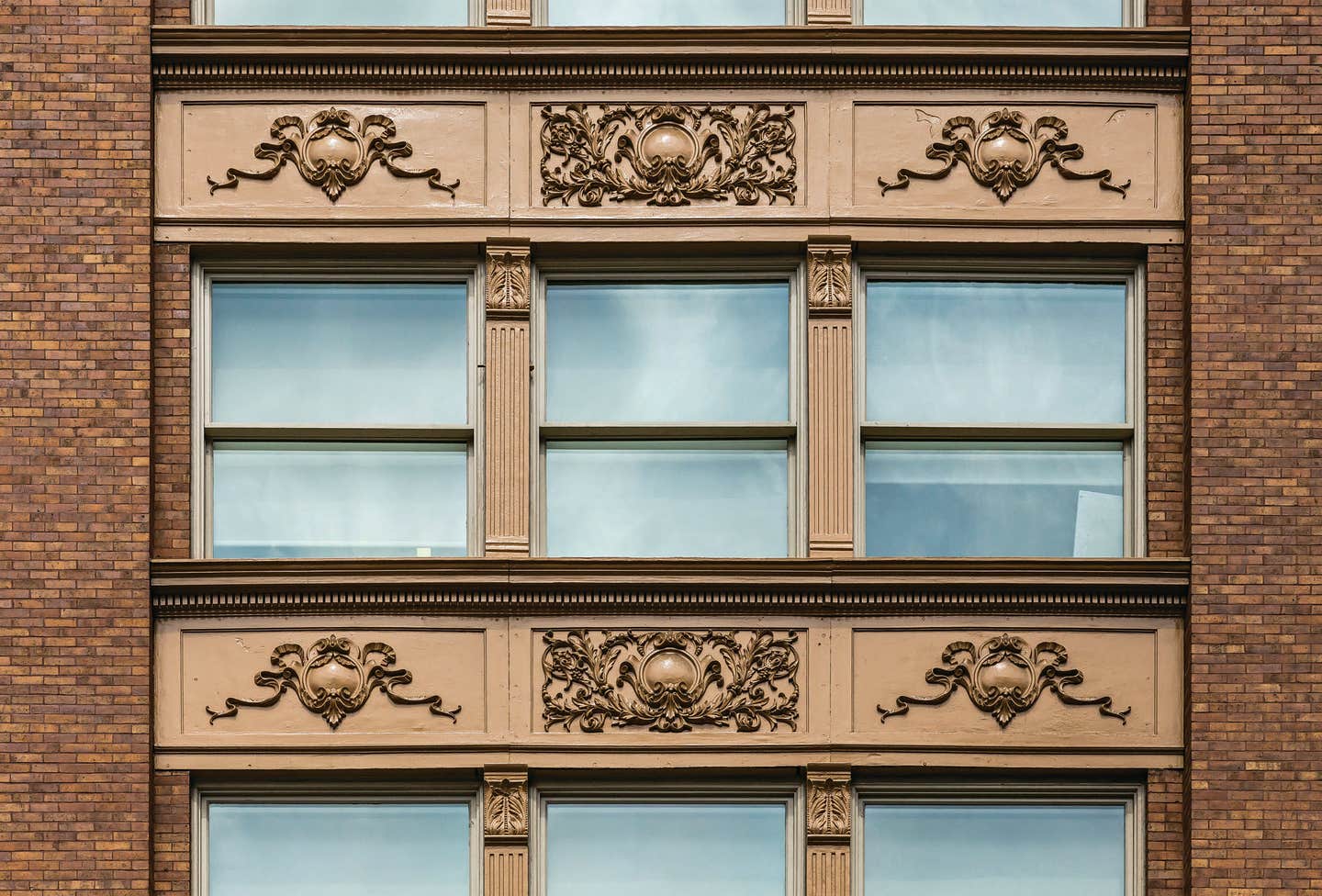
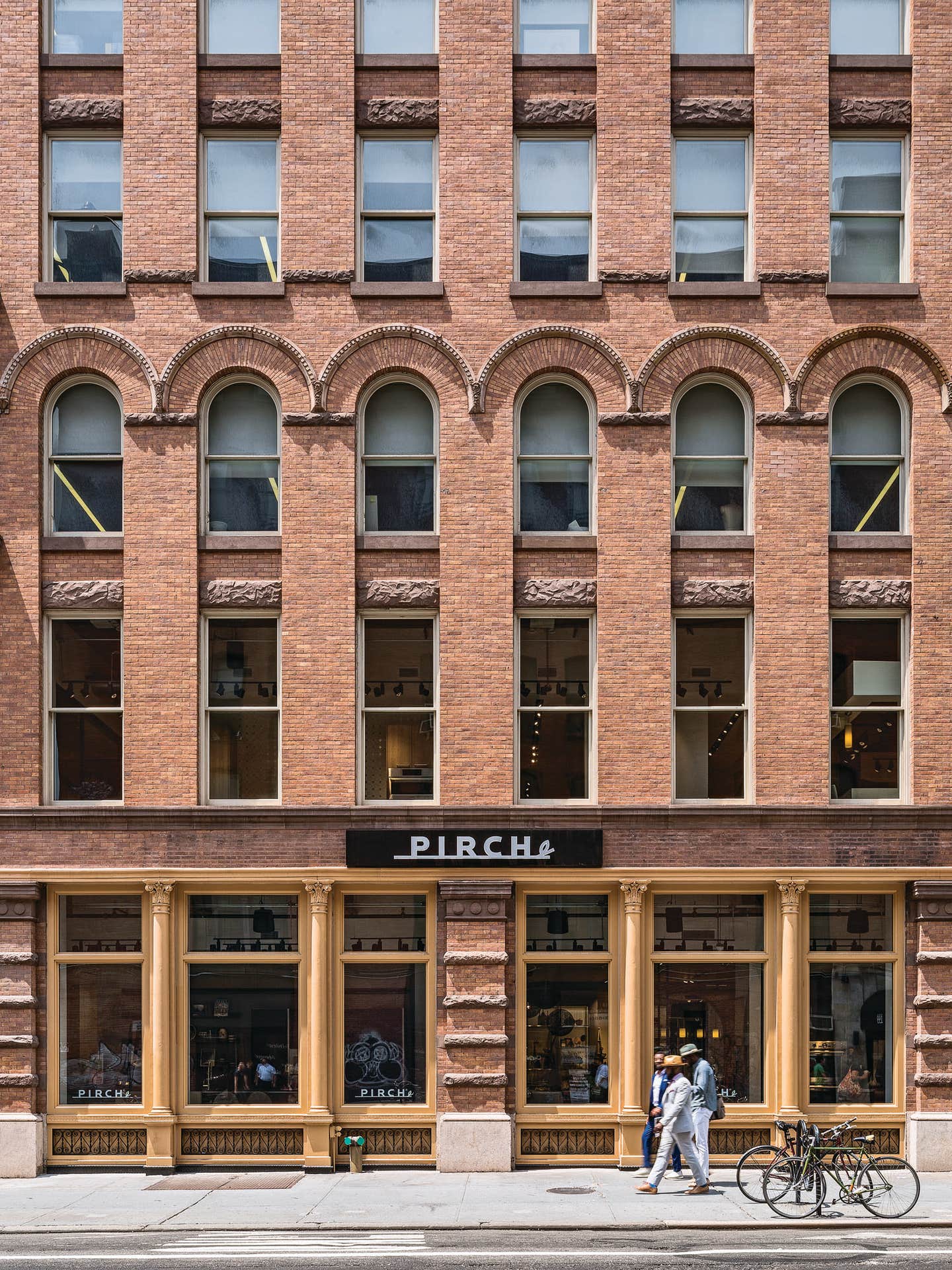
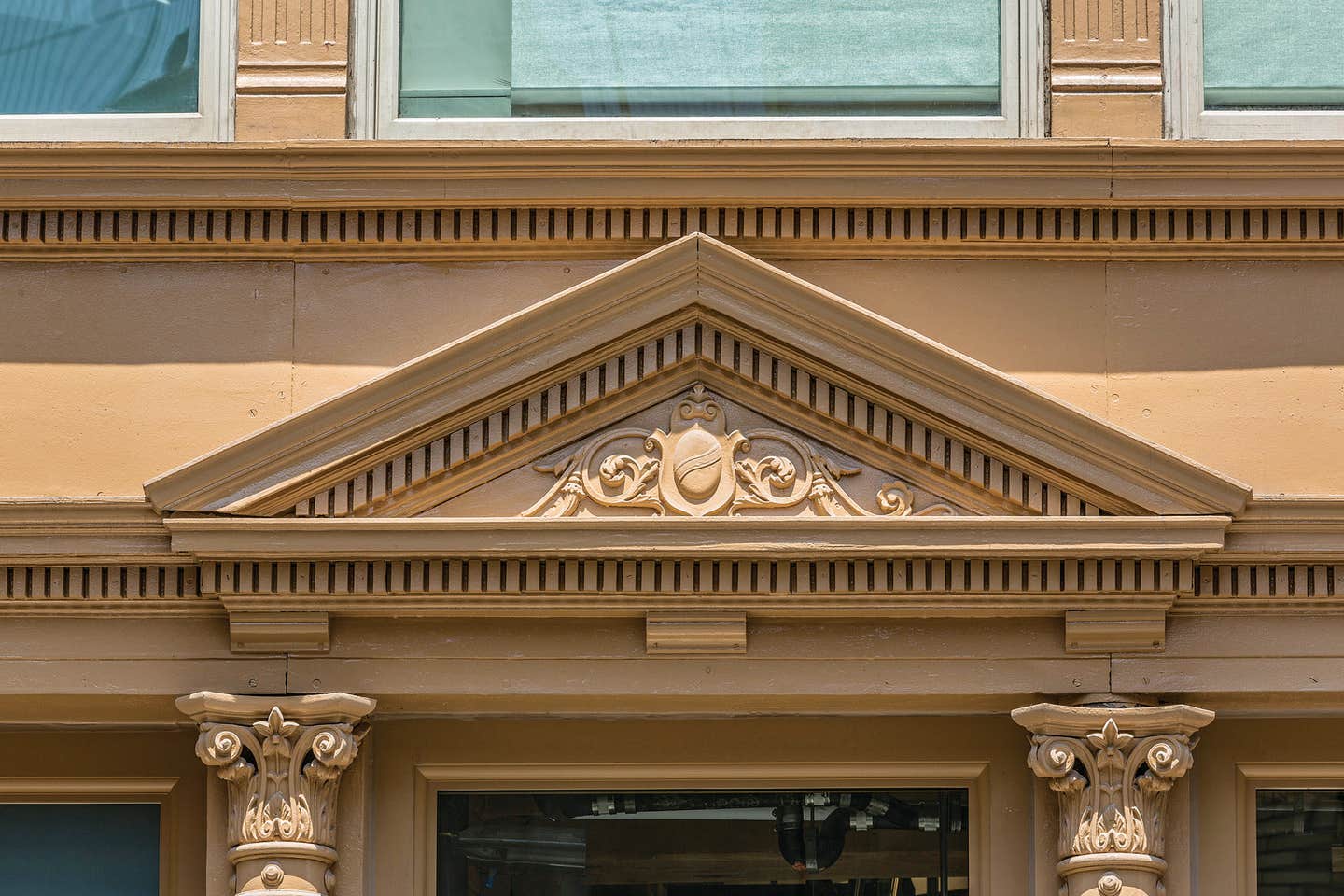
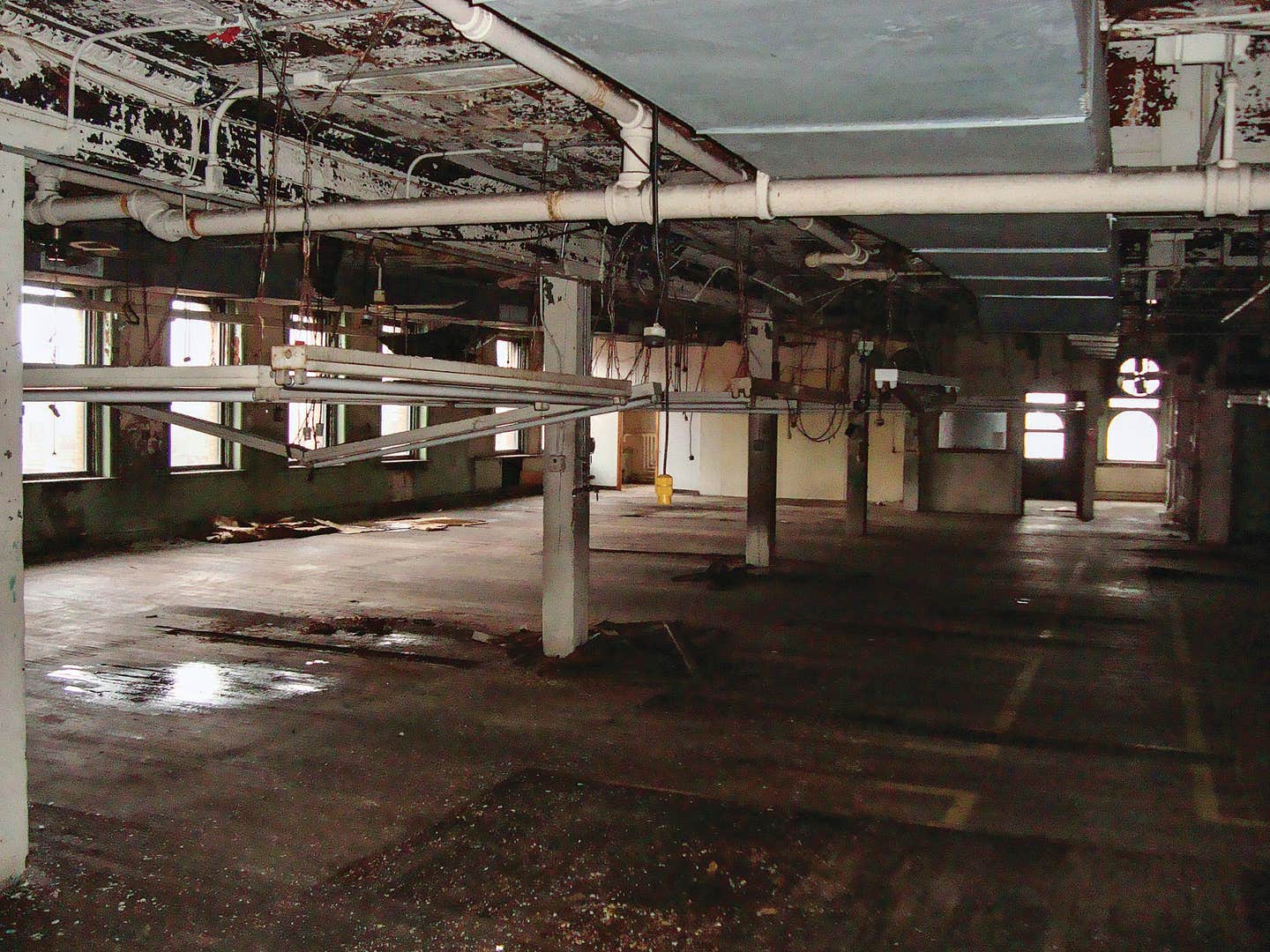
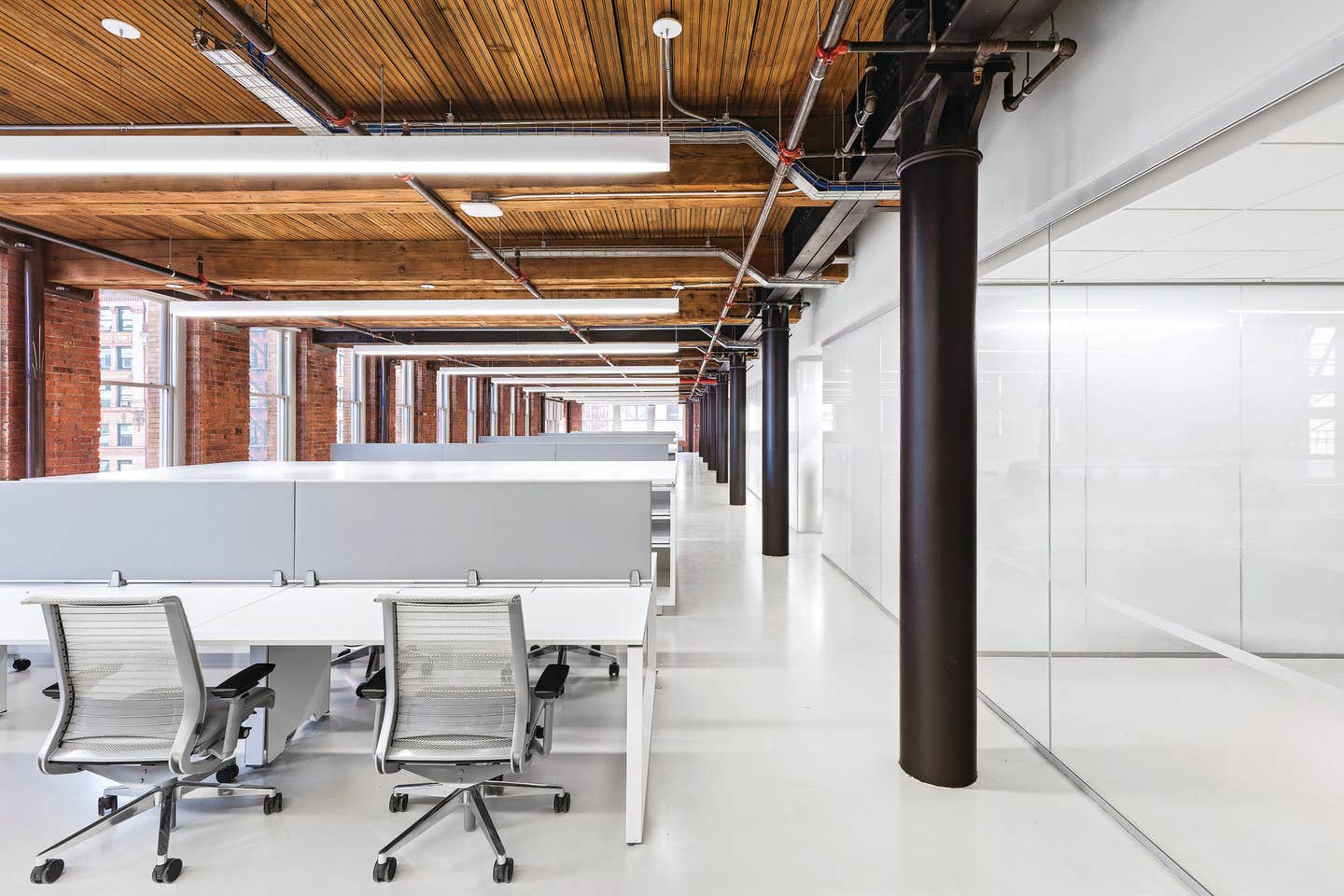
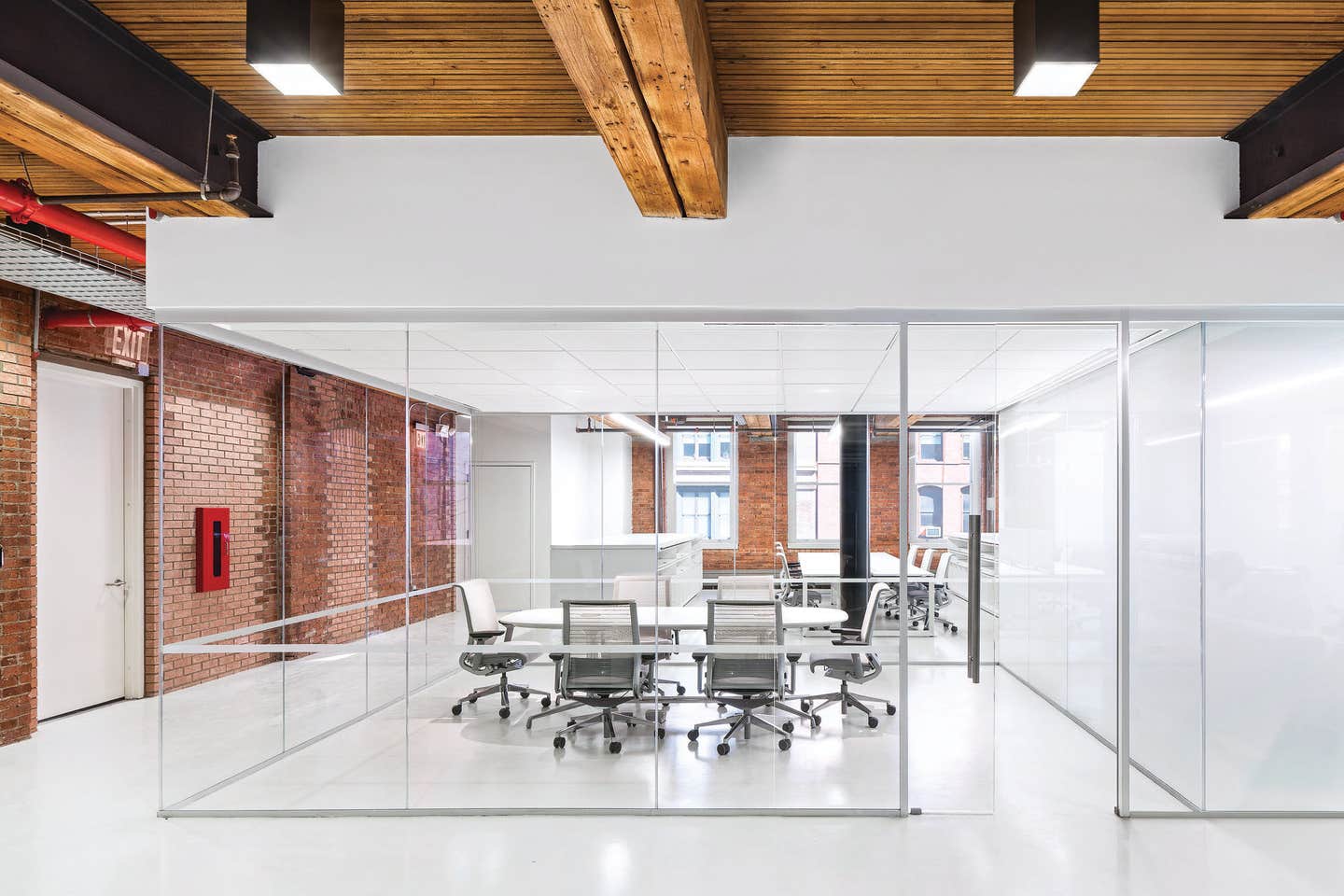
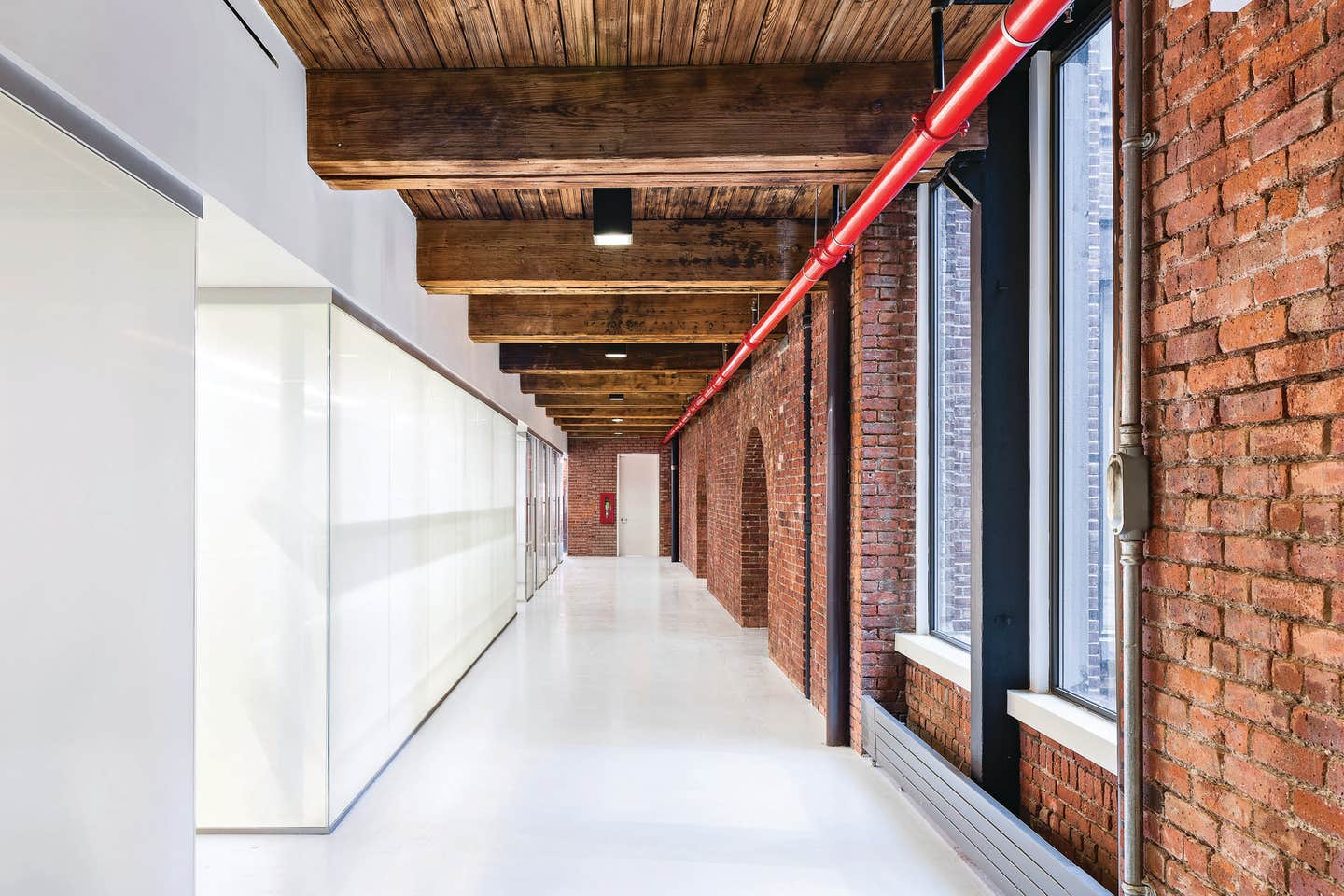
2017 Palladio Winner Adaptive Reuse: Scott Henson Architect, New York, NY
Project: The Knickerbocker Telephone Company Building, New York, NY
Architect: Scott Henson Architect, New York, NY; Scott Henson, Principal; with the Stephen B. Jacobs Group, New York, NY; Isaac-Daniel Astrachan, Principal
Like some inner-city Cinderella story, New York City’s fabled SoHo district in lower Manhattan began as a humming 19th-century mercantile and machinery enclave that slid into dormancy after World War II until rediscovered in the 1960s by loft-loving artists and preservationists.
Though later recast as a swanky wonderland of art, fashion, and shopping, it is even more importantly a stunning showcase of restored cast-iron façade architecture—at 500 buildings, the largest such collection in the world. A model of how this metamorphosis continues to reanimate the industrial is the 2012-16 rehabilitation of The Knickerbocker Telephone Company Building at 200 Lafayette St., which has earned Scott Henson Architect and Stephen B. Jacobs Group the 2017 Palladio Award for Adaptive Reuse/Sympathetic Addition.
Constructed in 1894 by architect and builder John T. Williams, The Knickerbocker Telephone Building is a 105,000-sq.ft., seven-story, Renaissance-Revival style, factory-type structure that originally housed The Knickerbocker Telephone Company, one of many early local phone companies, the high-tech start-ups of their day. Knickerbocker planned to outmaneuver the Bell Telephone Company and dominate the New York City market with a novel wiring system, but by 1901 it had disappeared into its parent, the nearby Telephone, Telegraph, and Cable Company, and the building went on to other uses.
Henson, who has specialized in New York historic buildings for nearly two decades, got his first glimpse of The Knickerbocker in a sadder, later life through a kind of preservation preja vu. “Around 2000, I was working on a neighboring building and could look over into the interior courtyard of 200 Lafayette,” he recalls. “There were lots of people operating sewing machines and textile equipment, and the building was in really, really bad condition, so for me to return some 15 years later as the architect for its rehabilitation feels pretty amazing.”
As befits a late 19th-century building from New York’s booming industrial heyday, The Knickerbocker Building exterior is brick and brownstone, with a pronounced sheet-metal cornice, wood windows, and a cast-iron-and-glass storefront. “Working with our client, General Growth Properties from Chicago, and the New York City Landmarks Preservation Commission, our job was to restore the outside of building to what it resembled when first built, so most of our work was on the exterior and the roof, as well as the structural vaults in the cellar and underneath the sidewalk (a common Manhattan feature).”
Henson adds that Stephen B. Jacobs Group of New York was responsible for repurposing the interiors, from restoring the original exposed brick and cast-iron columns to adding new mechanical systems, elevators, and glass office partitions. “It was a complete, full, adaptive reuse of the building, from industrial to office/commercial.”
For the most part, Henson says the brickwork was in pretty good shape. “Originally, this was an industrial building, so it’s quite substantial—load-bearing masonry walls with large timber beams and floor joists on a grid of cast-iron columns.”
Nonetheless some exterior bricks needed to be replaced. “We matched those as close as we could to the originals,” he says, also repointing 100% of the brickwork with mortar in the existing, original color.
The massive bearing walls, a structural feature, became a highlight of the interior restoration. “These are a good five and six wythes of brick in thickness, three and four feet deep at the base, with incredibly beautiful brick arches inside—all restored as part of the interior design of the building,” Henson adds.
The cornice was another matter. “It was so deteriorated, we were only able to keep about 25% of the original fabric,” explains Henson. Once they opened up the cornice, he says they were able to get inside and re-support it with new steel brackets that hold the cornice out from the building, while tying support farther back into the roof. “It’s a sizeable cornice, large enough to bend down and get inside it.”
They then replaced deteriorated sheet metal with new, galvanized and painted sheet metal, rather than alternative materials like fiberglass or GFRG used today for rebuilding cornices. “A lot of what we do in my office is preservation work, salvaging the existing material and only replacing where needed, so on this project we specified authentic materials as much as possible.”
However, the biggest threat from the façade was the brownstone. Recalls Henson, “When I first toured the building for the client and got up on the sidewalk shed (those eternally temporary New York pedestrian shelters) there were large pieces of fallen brownstone everywhere you looked.” The Knickerbocker Building it turns out, originally had very large, projecting water tables made of brownstone, and these had been crumbling and falling down on both sides of the building. “One of the many problems with brownstone is that it’s porous and therefore disintegrates easily with water infiltration and freeze-thaw cycles. When these forces get inside the stone, they pop it off the building.”
Henson says that rather than replacing the failing brownstone with new brownstone, which is difficult to obtain, or a substitute material, such as cast stone or synthetics, they chose to rebuild the water tables. “Basically, we cut back all the deteriorated material until we reached sound stone, reinforced it with stainless steel pins, and then built out the water tables with brownstone patching material custom-formulated to match the consistency and chemical make-up of the original brownstone.”
Window lintels and sills are also brownstone and almost all of these needed patching as well. “We recreated all the original profiles, so now the water tables and all the other brownstone details are ready to last another 100 years.”
What did require major reconstruction was the northeast corner of the building. “On the top floor, there’s an original freight elevator shaft just inside that corner, and in order to install a new elevator, we had to rebuild the beautiful, brick arches up on the outside of the building.” As Henson describes them, the arches are three courses of brick high with a very large span, but they had collapsed as the building had shifted or settled, most likely due to the loads of the freight elevator.
“Not only did we have to very carefully pull apart the remaining sections of each arch and rebuild, it was a very difficult location in which to work,” he says. “We had scaffolding outside, but we were not able to put any kind of scaffolding in the elevator shaft itself, so it was a tricky process for the contractors.”
The rebirth most apparent to the public is the street-level storefront space of the building. While not radically altered from the original appearance, the storefronts nonetheless had been modified over the decades not to mention suffered typical wear. “Between the glass storefront windows there are cast-iron columns, with decorative cartouches and swags above the windows, and after a century a lot of those pieces had either fallen off the building or had been removed during various renovations.”
Using the original features that remained on the building as patterns, Henson’s firm had a fabricator in upstate New York make molds and cast new iron pieces, which were shipped down to Manhattan for installation onto the building by the contractor.
Since all windows and doors were in varying state of deterioration, with some later replacement doors unlike the original, historic design, they replaced the storefront window glass and had new entry doors made for the building. “The bases in between the storefront windows are granite, and many had been damaged over the years from deliveries and all the other traffic common on sidewalks and streets.”
They patched and repaired some bases and rebuilt others with new granite, all the while removing many coats of paint. Major window restoration even went on inside the building. “At the first level is an interior courtyard with a large skylight for the first floor—a really beautiful space. That skylight was replaced as well.”
Adding a granite ramp on the Lafayette St. side was part of bringing the building up to code and ADA accessibility. “We also found historic photos that showed long-gone grillework at the base level of the storefronts, so we recreated all these in cast iron.”
The finishing touch for windows and other exterior details was repainting in the original, rich yellow, determined through historic paint analysis to be a color called Richmond Gold.
The $36-million project was completed in May, 2016. It saved a historic building, and contributed to a dynamic historic neighborhood. The building, now office space and a storefront showroom, is ready to serve the community for at least another 100 years.
Key Suppliers
Primary Contractor: Rally Restoration Corp., Newark, NJ
Historic Preservation & Rehabilitation Consultant: Higgins Quasebarth & Partners, New York, NY
Interior Designers: Eight, Inc., New York, NY
Storefront Granite Bases and Ramp: Arte Tile & Masonry, Inc., Astoria, NY
Restoration Mortar: Cathedral Stone Products, Hanover, MD
Sheet-Metal Cornice: CCR Sheet Metal, Inc., Brooklyn, NY
Roof Membrane: Kemper Systems, Teaneck, NJ
Windows/Storefront: Dover Windows and Doors, Harrington, DE
Storefront Cast Iron: Antique Cast Iron LLC, Cherry Valley, NY
Façade Brick: Casa Building Materials, Bronx, NY
Gordon H. Bock is an architectural historian, instructor with the National Preservation Institute, and speaker through www.gordonbock.com.