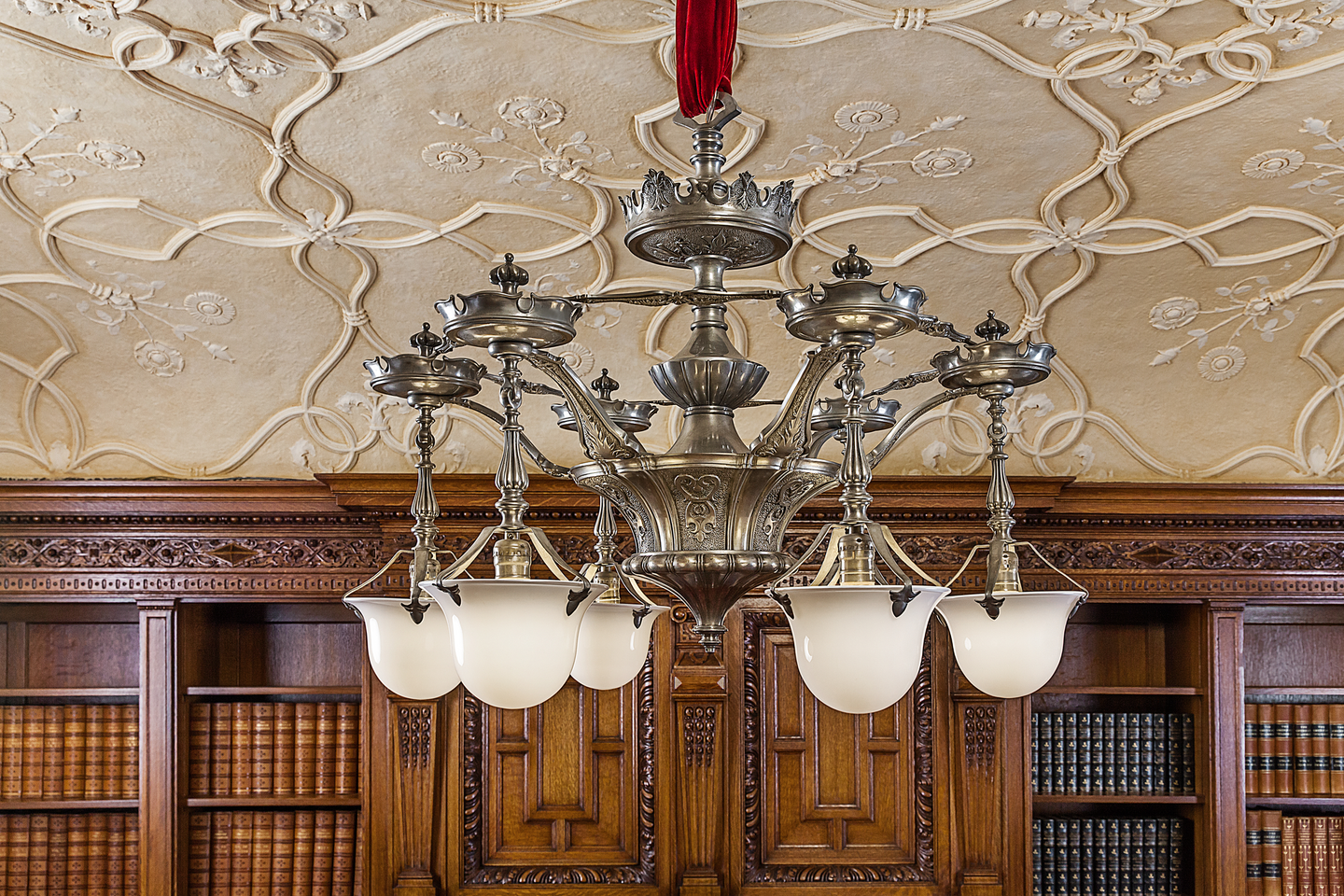
Palladio Awards 2022
Heritage Metalwork: Fair Lane the Home of Clara and Henry Ford
It is the historically accurate details and the master craftspeople who execute them that lend authenticity to reproduction projects and bring them to life.
In the case of Fair Lane, the 1915 Dearborn, Michigan, estate of automobile mogul Henry Ford and his wife, Clara, it is the period lighting fixtures created by Heritage Metalworks of Downingtown, Pennsylvania, that really shine the light on its history.
Heritage Metalworks, a metal fabrication shop with an in-house foundry, blacksmith, and copper shop that specializes in creating signature lighting, period-correct hardware, and architectural metalwork, spent five years and an astounding 3,349 hours reproducing the lighting fixtures in the 31,000-square-foot limestone mansion’s music room, library, billiards room, and swimming pool room.
“In terms of the amount of research, the amount of time, and the prestige of the project, this stands apart from just about anything we’ve been a part of,” says Heritage Metalworks owner Matt White. “What made it so different was the fact that we only had period photos to go by. They were really good photos, but some of the details that we needed to make the replications were lost.”
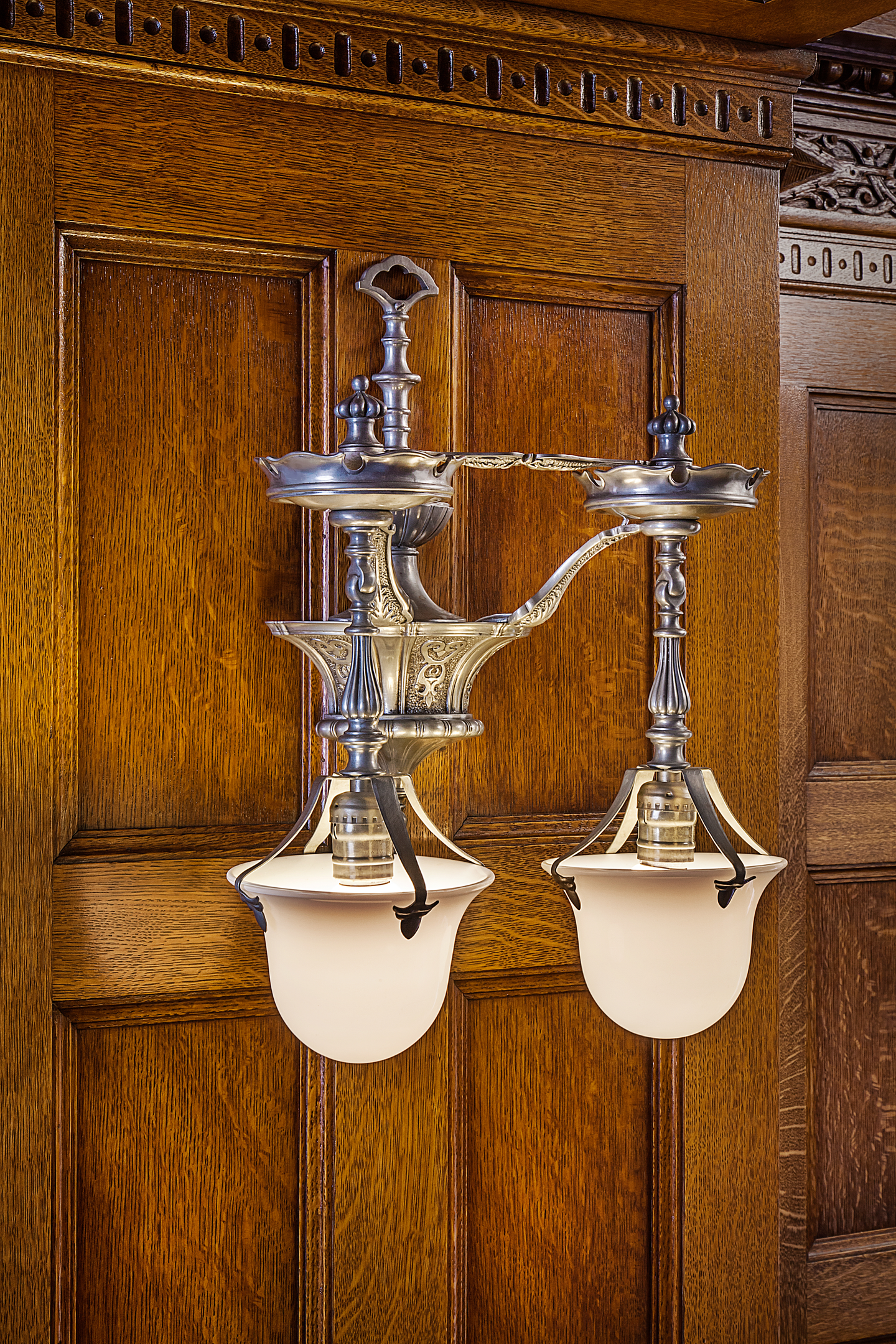
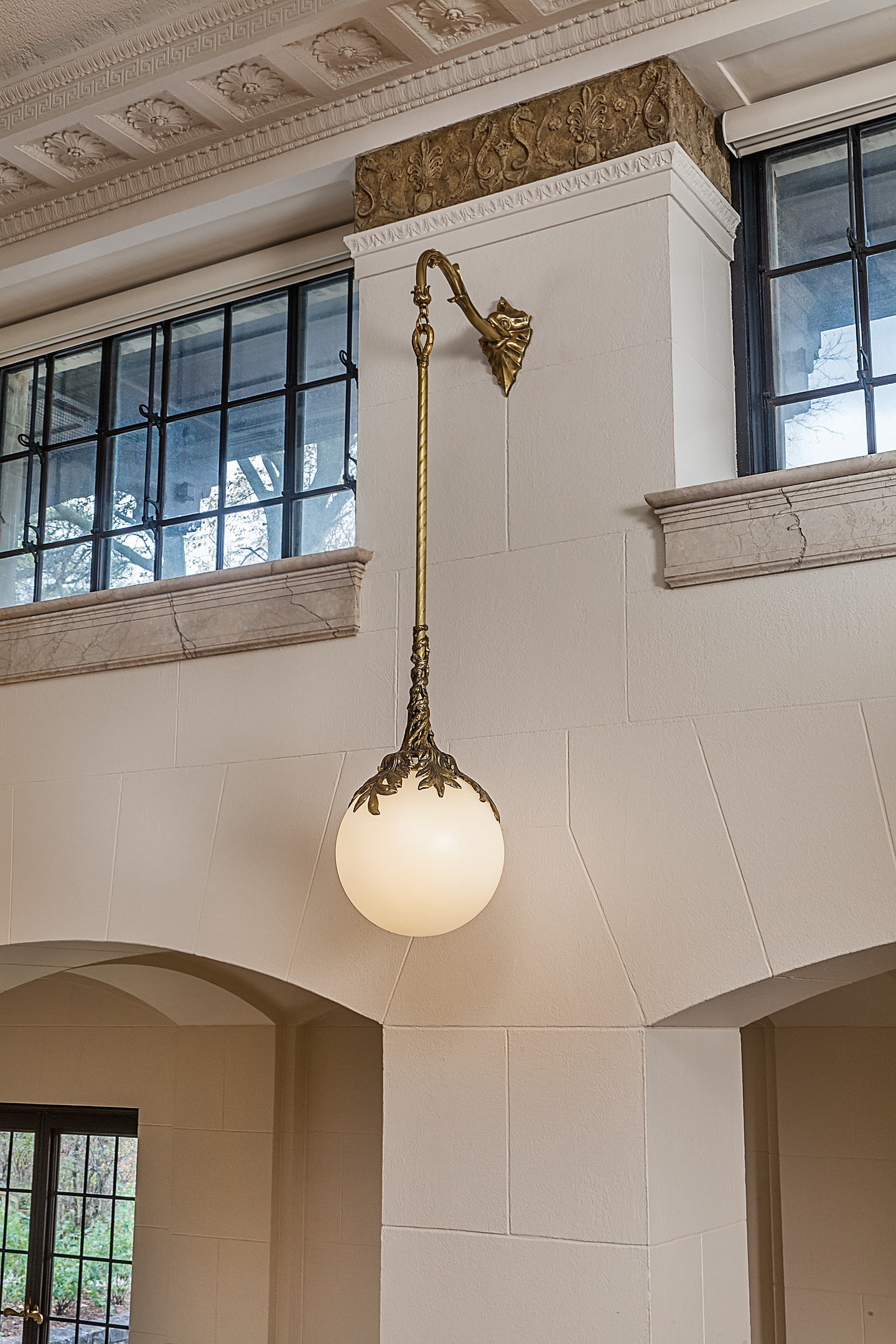
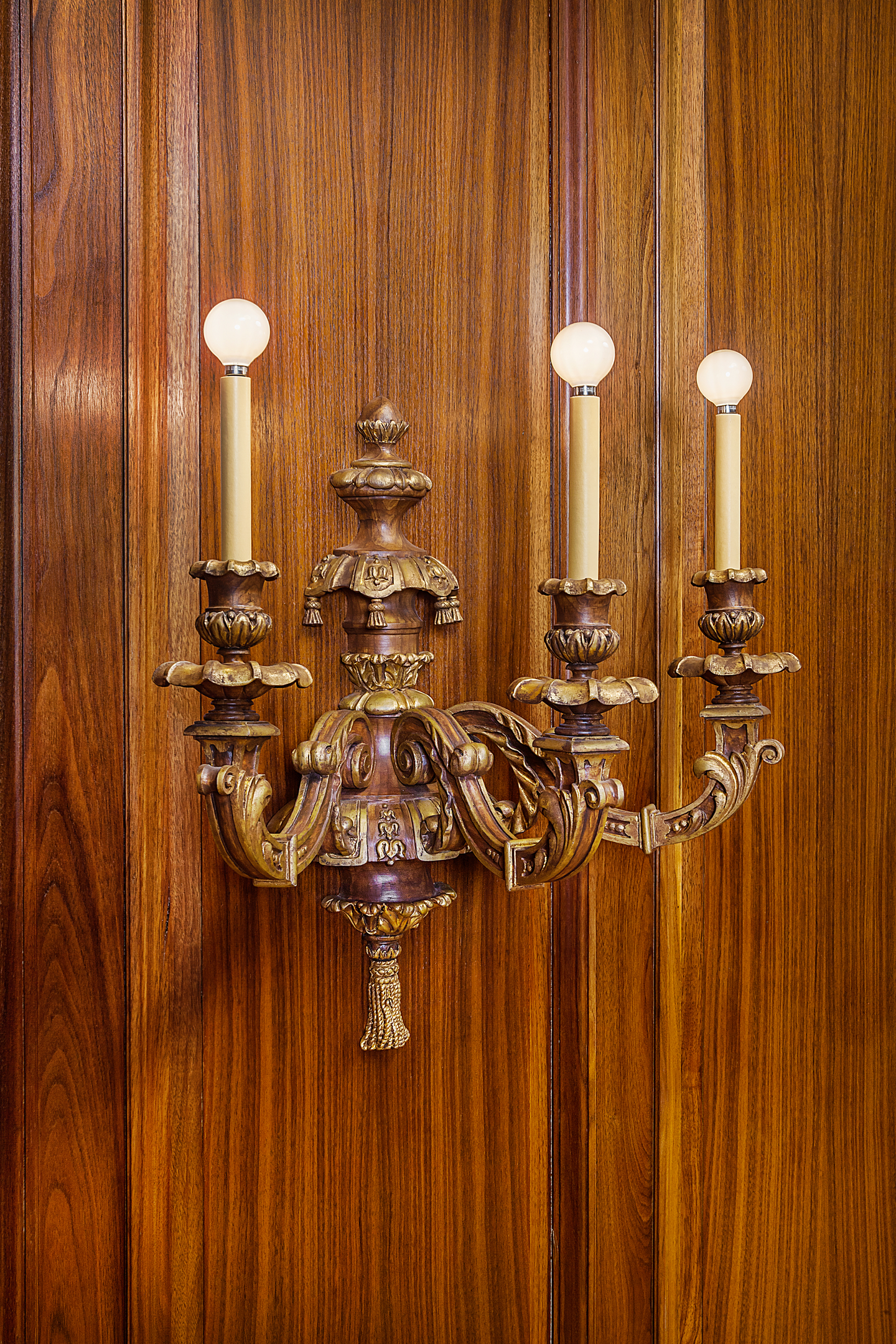
Noting that there was “a lot of back and forth in the design phase,” White says that “we visited the house twice; the second time, we took hand-sketched 2D models and held them up in the middle of the room at the same angle they were in the old photos to make sure they were the correct size and scale. We also asked the conservators working on the woodwork to carefully scrape off some of the top layers of the old paint to help reveal the shadow created by the back plate of the original sconces. That really helped us get the size and shape accurate.”
Each part of the project presented its own challenges, with the firm producing concept sketches, CAD drawings, 2D cutouts, printed patterns, and 3D mock-ups, and investigating metal finishes and fabrication processes from the period. “We went way over budget on the project,” White says, “but we wanted everything to be accurate, and we didn’t want to cut corners, so we absorbed the cost.”
For the music room, Heritage Metalworks fabricated eight sconces, hand sculpted and molded using the traditional lost-wax investment process. “We reproduced them using a single arm of the original chandelier, which was the only existing fixture in the room,” White says. “The primary challenge was to reduce the size of the solid mahogany chandelier design into cost-affordable sconces. That’s why they were cold cast in resin, allowing the fingerprint detail of the wooden texture, instead of building each individual piece from wood. Multiple coats of paint were meticulously applied with different techniques to match the precise depth of the original. The fixtures were then hand-gilded.”
The library chandelier and wall sconces were reproduced using the same lost-wax process and then hand-sculpted into patterns. Each piece was cast in brass to pick up the refined details.
Some of the pieces were 3D printed, sculpted, and hand-carved. The brass was plated with zinc and antiqued to match the original pewter finish. Two floor lamps made of brass and plated with zinc also were reproduced for the room.
“We had to make the replicas based solely on archival photos,” White says. “Without existing fixtures, we used the distinct millwork in the room to help scale the fixtures for a 2D sketch. These 2D drawings created an accurate representation of the fixtures prior to creating patterns, molding, and casting.”
It took the team more than two years to reproduce the massive chandelier and wall sconces for the billiards room. The pieces, cast in brass, have a finish that simulates ormolu and feature hand-blown glass shades.
“We used details from existing wall sconces, refinished in a non-specific patina, to reproduce the additional wall sconces and the missing chandelier,” White says. “The archival photos of the unusually long chandelier were shown at an angle, making it extremely complicated to scale. I spent over a year working out the dimensions and researching finishes from the period, and I must have spent 80 to 120 hours just trying to position the four flame motifs on each column correctly.”
Although there were no original pool wall fixtures, the Heritage Metalworks team did have a single original glass globe, as well as archival photos, for reference.
“There was a ceiling fixture in an adjoining room that had some sculpted detail that we assumed was similar to what had been in the pool room,” White says. “We could see in the photos that there was a leafy vine, but the details were fuzzy, so we had to make some educated guesses that I feel are pretty accurate. The only way we’ll know for sure is if one of the originals surfaces.”
The restored Fair Lane, complete with the Heritage Metalworks lighting fixtures, is set to open in 2023.
“I can’t wait to see it with everything lit up,” White says.
KEY SUPPLIERS
LIGHTING REPRODUCTION AND REPLICATION
Heritage Metalworks hmwpa.com