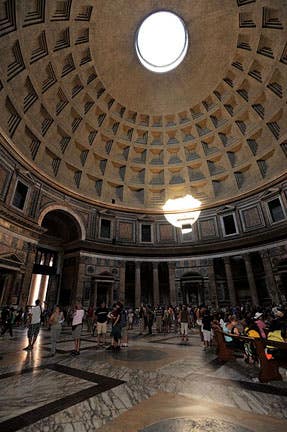
Patrick Webb
Roman Cement and Pozzolans
“There is also a kind of powder which from natural causes produces astonishing results. It is found in the neighbourhood of Baiae and in the country belonging to the towns round about Mt. Vesuvius. This substance, when mixed with lime and rubble, not only lends strength to buildings of other kinds, but even when piers of it are constructed in the sea, they set hard under water.” - Vitruvius; The Ten Books of Architecture, Book II, Chapter 6 Pozzolana
The secret of Roman Cement was the mixing of lime with pozzolana, called harena fossicia or “pit sand” by Vitruvius. Pozzolana was distinguished from river and sea sands (the common harena) and receives this contemporary name from the town of Pozzuoli (Roman Puteoli, neighboring Baiae) in the Bay of Naples just 25 miles east of Mount Vesuvius. The entire region is heavily covered with meters thick beds of pozzolana, volcanic pumice and ash from previous eruptions.
In addition to Pozzuoli, Vitruvius mentions deposits of pit sand at Mount Aetna and there is evidence indicating the Roman exploitation of German trass, a sedimentary stone of lightly compacted volcanic ash having similar properties. Although the Romans typically are credited with inventing pozzolana based cement, there is archeological evidence that the Greeks were using their own pozzolana from the eruption at Thera (Santorini) for water cisterns as early as 600 B.C. as well as for methods of wall construction only later adopted by the Romans.
Roman Cement
The volcanic ash constituting pozzolana is high in amorphous silica and also contains finely constituted alumina. “Amorphous” literally means “without form.” Under most natural conditions silica organizes itself into a highly stable, non-reactive, crystalline state such as sand or quartz. However, with the explosive debris of certain volcanic eruptions, the disorganized molten silica is finely dispersed in the atmosphere where it rapidly cools before having time to crystallize, precipitating as a fine ash. This ash is relatively inert by itself or even in the presence of water. However, blended with lime the resulting mortar is “awakens” as a Roman Cement sharing many of the properties and specifications of the Natural Cement considered in our previous article.
Roman Cement was used for exterior stucco, plastering water cisterns, the mortar of aqueducts, and even for casting the greatest unreinforced dome in human history: the Pantheon. The very same sources of pozzolana from Vesuvius, Aetna, Santorini and German trass are all still mined and used in similar ways today.
Other Pozzolans
The term “pozzolans” has extended to man-made aggregates and powders that have a similar hydraulic effect when blended with lime. Pliny the Elder indicated one used extensively by the Romans over two thousand years ago:
“There are three kinds of sand. Sand which has been quarried (pozzolana) requires one-fourth its weight of lime, while river sand or sea sand requires one third. If one third of pounded earthen ware is also added, the mortar will be improved.”
The improvement he referred to was the moderate hydraulic action imparted by finely ground burnt terra cotta which has been used for millennia by the Minoans, Greeks, Romans, Indians (surkhi) and Egyptians (homra). In the Veneto it is called “cocciopesto,” quite literally referring to “baked and crushed” terra cotta. Cocciopesto lime has been traditionally used for stucco as well as plaster floors in Venice and imparts a superior resistance to the relentless attack of salts in the brackish water of the Venetian lagoon. Similar to the previously considered Natural Hydraulic Lime mortars, these lime plasters with ground terra cotta or brick crushed to powder are not as impermeable or brittle as Roman Cements and are very useful for plaster and stucco applications.
Today, many other pozzolans have been discovered, many of them being waste products of industry including: Pulverized Fuel Ash from coal fired power stations, Ground Granulated Blast-Furnace Slag from steel production, Silica Fume from electric arc furnaces and Rice Hull Ash as a byproduct of agricultural production. All of these have slightly varied but related properties, reacting with lime to produce mortars resembling traditional Roman Cement.
That concludes our consideration of the lime family and thus all of the traditional plaster binders. Until we've been looking at each binder individually. However, many of these binders play nicely with each other (and a couple don't). In our next article we'll mix things up and see some interesting possibilities available from mixing plaster binders.
My name is Patrick Webb, I’m a heritage and ornamental plasterer, an educator and an advocate for the specification of natural, historically utilized plasters: clay, lime, gypsum, hydraulic lime in contemporary architectural specification.
I was raised by a father in an Arts & Crafts tradition. Patrick Sr. learned the “decorative” arts of painting, plastering and wall covering as a young man in England. Raising me equated to teaching through working. All of life’s important lessons were considered ones that could be learned from the mediums of tradition and craft. I found myself most drawn to plastering as I considered it the richest of the three aforementioned trades for artistic expression.
This strong paternal influence was tempered by my grandmother, Geraldine Webb, a cultured, traveled, well-educated woman, fluent in several languages. She made a point of instructing her young grandson in Spanish, French, formal etiquette and opened up an entire worldview of history and culture.
After three years attending the University of Texas’ civil engineering program with a focus on mineral compositions, I departed, taking a vow of poverty, living as a religious aesthetic for a period of seven years. This time was devoted to clear reasoning, linguistic studies, examination of world religions, exploration of ethics and aesthetics. It acted as a circuitous path leading back to traditional craft, now imbued with a deeper understanding of interconnection in time and place. I ceased to see craft as simply work or labor for daily bread but among the sacred outward expressions of the divine anifest
within us.
From that time going forward there have been numerous interesting experiences. Among them study of plastering traditions under true masters here in the US as well as in England, Germany, France, Italy and Morocco. Projects have included such high expressions of plasterwork as mouldings, ornament, buon fresco, stuc pierre, sgraffito and tadelakt.
I’ve been privileged to teach for the American College of the Building Arts in Charleston, SC, where I currently reside and for the Institute of Classical Architecture & Art across the US. “Sharing is caring” – such a corny cliché but so true. I hardly know a
thing that hasn’t been practically served to me on a platter. I’m grateful first of all, but now that I might actually know a few things, it becomes my responsibility to be generous as well.