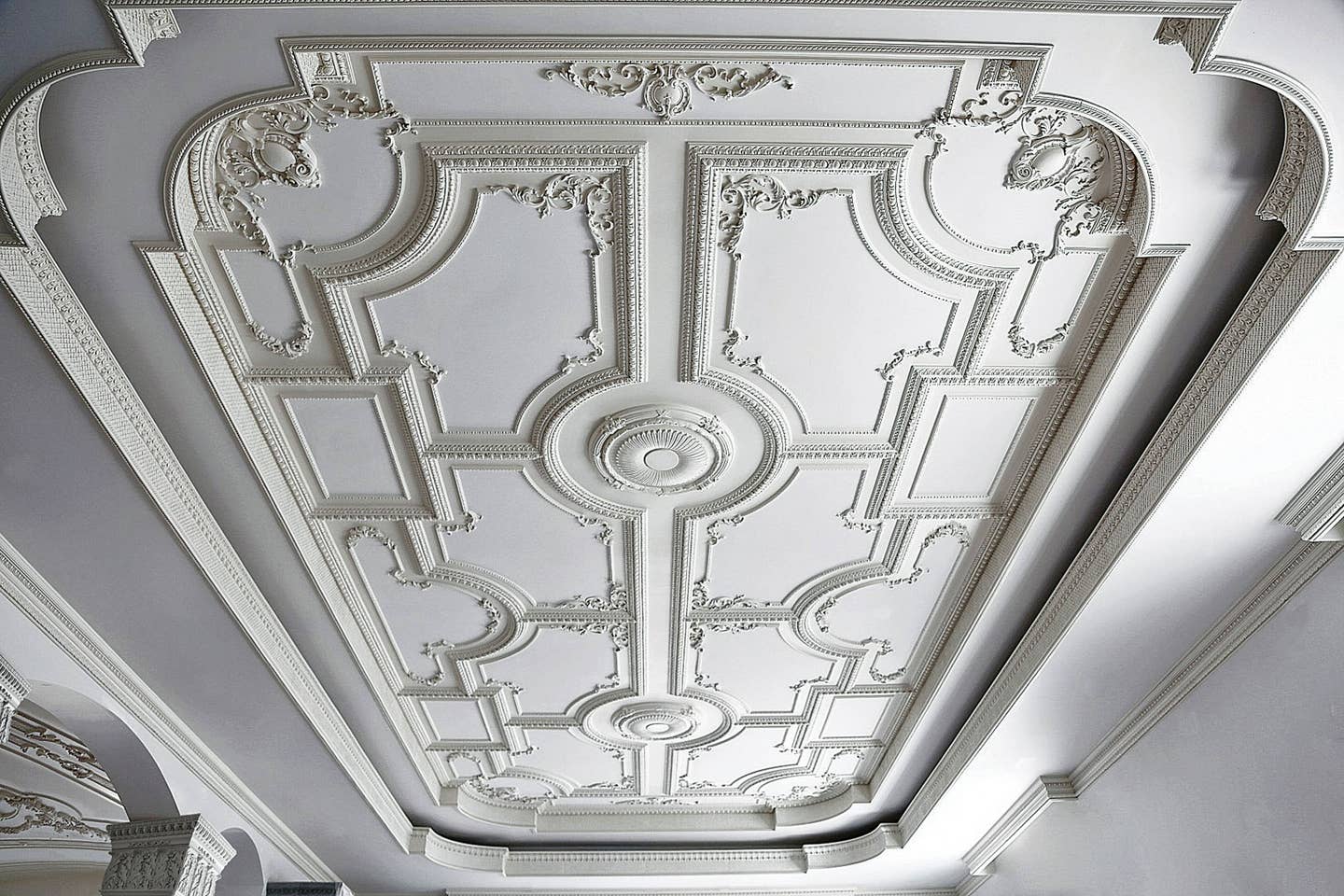
Product Reports
How Suppliers Design Traditional Ornamental Ceilings
Changing styles in ornamental ceilings come as no surprise to companies in the decorative features industry for generations. With their perspective, they know how the pendulum of preference swings back and forth between modest and magnificent, and they’re ready to serve their clients no matter which way the winds of fashion blow.
According to Jack Meingast at Decorators Supply in Chicago, IL, a company known for its classical architectural detailing, “This is our 135th year of business, where everything we’ve done has been ornamented and traditional. I think we all knew traditionalism, which has had such a long run, would eventually taper off, and now we’ve had to re-evaluate the entire market and develop some simpler types of relief ceilings.”
Among his clients, the shift in ceilings became apparent within the last three years. “They’re plainer, with an open tracery that’s mounted on an existing ceiling—similar to what used to be called Gothic tracery,” referring to the complex patterns inspired by window stonework.
At Driwood, makers of millwork and architectural embellishments in Florence, SC, Mitchell Powell reports, “Here in the Southeast, we’ve seen a trend predominantly toward a plainer, cleaner style. It’s got a traditional feel, but it doesn’t necessarily adhere completely to the classical orders or other traditional styles.”
As an example, he points to a recent large-scale commercial building project right outside of Savannah. “We did the majority of the interior woodwork at the Pooler, Georgia, City Hall, and it was almost exclusively plain, hardly any ornamentation at all.”
The firm’s specialty is embossed millwork that replicates the hand-carved moldings found in historic buildings in Greco-Roman styles—egg-and-dart, acanthus leaves and so on. “We do those same ornaments but with embossing, and we have hundreds and hundreds of designs.”
Stephanie Croce at J.P. Weaver Co., architectural ornament and design in Los Angeles, CA, agrees. “Tastes have changed over roughly the last 10 years, from very ornate, dripping-off-the-ceiling decoration to very refined, almost minimalist designs.”
Every zeitgeist comes and goes, she reminds us, “but what’s really big right now are strapwork-style ceilings, using very geometric forms with interlocking parts.” The trend she says is definitely away from complexity but she still sees plenty of ornamental interiors. “We’ve done quite a few Adam-style ceilings,” she notes, “and we try to create whatever the client is envisioning, whether it’s a Rococo-style ceiling from the 18th century or Baroque or Neoclassical.”
Decorative Ceilings
One ornamental ceiling type that appears to float above whatever the day’s vogue is decorative pressed metal. “People get interested in new ideas unrelated to ‘tin ceilings’ all the time,” observes Mark Quitno of W.F. Norman in Nevada, MO, “but I don’t think anybody has thought of a new use or purpose for the material.” The current market he says, “really just goes down the ‘center lane’ of the history of the product. It’s especially appropriate if the room or building is going to have a little bit of turn-of-the-20th-century style—not chrome or glass, but décor popular from the late 1800s up to the Great Depression.”
Whatever the reason for the sea change in ceilings, it has sought its own level in a new normal. “Here at Decorators, we use the term transitional,” says Meingast, “that is, not necessarily traditional and not necessarily modern, but a design that can be used in both cases.”
His company was quick to respond to the shift. “We developed six or seven new designs in plaster (our sole medium for ceilings) that can be used in a very ‘clean,’ cut-and-dry building or a very traditional home, and they’ve received an incredible response.”
The feedback has been so positive, he says, that they’ve even adapted some of their old designs to fit the new call. “For example, we took two of our existing ‘Old English’ ceiling designs with complete panels and made them plain with just the raised ribbing.” Another benefit he says is that the designs are easy to install. “Just pre-drill, screw up, fill the screw holes and joints, and then move on—nothing complicated whatsoever.”
According to Powell of Driwood “Even though public buildings lean towards plainer ornament interpretations these days, it’s nice to do these jobs because they tend to be a little bit more by-the-book in terms of design, proportion and the orders.” His company which is known for maintaining architectural authenticity, has supplied architectural millwork and design services for nearly a century and been involved with scores of commercial projects. “We’ve done numerous court houses, and some work on the State Capitol here in South Carolina, the Augusta National Golf Club, and even the Pentagon in Washington, DC.”
Croce points out another trend. “We get a lot of clients who want a very ornate ceiling or room, but they want to paint it all white—like a wedding cake!” She notes this is a departure from the heavy gold that was so popular in many places 10 or so years ago, and a move more towards background.
“The other work we’re doing a lot more of is restorations” she says, “particularly in the Los Angeles area. We’re asked to basically replicate what was existing where the building is water damaged or the room has to be gutted to add modern services but they’re saving the moldings and having us clean and remake them.”
In fact, Quitno says his customers just want an authentic stamped metal ceiling, and come to a company that still offers the exact same patterns they did 120 years ago. “There aren’t any types of traditional and historic buildings where people don’t use metal ceilings.” The material was once ubiquitous in small-town shops, he explains, from 5&10-cent stores and barber shops, to taverns, restaurants and pool halls. “They were—and still are—used in every kind of government building,” he says. “It’s amazing how many small-town churches used pressed metal back then, for walls as well as ceilings. We still help fix those up today, and even do some new churches.”
How Do You Spell Relief?
For ceilings, Croce says her company’s material of choice is usually either cast plaster or their polyester resin Petitsin product. “It’s a two-part system that’s poured into a silicone mold, and then cures to an almond color.”
Croce explains that she uses plaster and resin ornament a lot in her design work because it’s ship-able and installation is well within the realm of a good trim carpenter. In fact, if they have the proper molds, her company can make an ornament item in either plaster, resin or even ‘compo’ composition ornament—“it really depends upon the delicacy of the part.”
But that doesn’t mean all-white ceilings need to be flat or bland. “The heavier the detail, and the more undercuts in the detail, the more the light picks up the shapes of the moldings. So one of the things we like to do, which is made possible by the plaster and resin products, is to give the ornamentation a lot of undercuts.” She explains that undercuts have long been a technique of wood carving, but because wood is dark, the effect is even more successful with cast plaster.
Powell says his company is exclusively wood. “We work in various hardwoods, tropical and domestic, and we’ve made just about everything. If you can think of it, we can manufacture it.” As he explains, embossing is a special process that, at his company, uses machinery over a century old. “We basically take a steel or bronze die carved with the design and, by applying a lot of pressure and a little bit of heat in the right proportions, we create a decorative molding.”
He adds that the company prides itself on the ability to produce really heavy, deep designs—nothing like the paper-thin impressions seen at big box stores. “Our embossing profiles are cut so much deeper than you find in most places that sometimes you can pass them off as actual carvings.”
Pressed metal too has historically offered ceilings rich with deep design but without the effort of complicated construction. “It’s always been lightweight,” explains Quitno, “so for ceilings you didn’t have to build an additional structure for support; existing ceiling beams and furring are sufficient.”
He says that the drop-press stamping of the late 1800s made pressed metal relatively mass-produced, so it was inexpensive enough for homeowners and small shop owners. “And it doesn’t require special installation skills. If you can hang wallpaper, or do some simple, around-the-house DIY projects, you can install a pressed metal ceiling just fine.” He adds, “We can help with all the technical issues: layout questions, sending samples, or talking to installers.”
Fashion cycles aside, ornament remains alive and well in some interesting places. “We find the seaboards of the Northeast and the Southeast are strong, and that trickles down into Florida,” says Meingast. California is hit-or-miss, he says, “but Canada is very strong.”
The hospitality and entertainment industries too are often ornament omnivores. Croce says that along with many residential commissions, their non-residential clients are mostly restaurants and hotel ballrooms. “When the Plaza Hotel in New York City underwent a major renovation eight or ten years ago, we were selected to do all the moldings in the lobby of the hotel portion.”
She adds that being based in Southern California since 1914, “Movie studio designers also come to us to create backdrops for their sets, and we have documentation of our ornament used in early films right up to today.”
For Quitno as well, the entertainment industry and period TV and movie sets are longstanding customers, along with theme parks around the world. “Besides the big parks that have Old New York-type attractions for visitors, we’ve done a lot with clients like Disney that also film at different parts of their parks.”
In fact, Meingast recalls that by good fortune, when the building industry flattened out after 2008, his company got involved with a lot of TV shows and movie sets. “Believe it or not, I think what got that ball rolling was Game of Thrones. While we didn’t work on that program, it had offshoots, such as Outlander shot in Scotland and Rome in Canada, and we supplied ornaments to both of those sets and their designers.” He too works regularly with Disney. “They revitalize their parks a lot and, since we often supplied original ornamentation, they come to us just to put back what was there.”
Powell reports that when he hears people exclaim, “Wow, we didn’t know companies exist that do this stuff anymore,” he has a ready reply. “Yes, there are still people out there, like ourselves who know how interiors should be done with proportion, scale, and architecturally correct detail, and who are capable of and willing to work in the old-world style.”
Key Suppliers
Above View, Milwaukee, WI
Chelsea Decorative Metal, Houston, TX
Decorators Supply, Chicago, IL
Driwood, Florence, SC
J.P. Weaver Co., Los Angeles, CA
W.F. Norman, Nevada, MO
Gordon H. Bock is an architectural historian, instructor with the National Preservation Institute, and speaker through www.gordonbock.com.