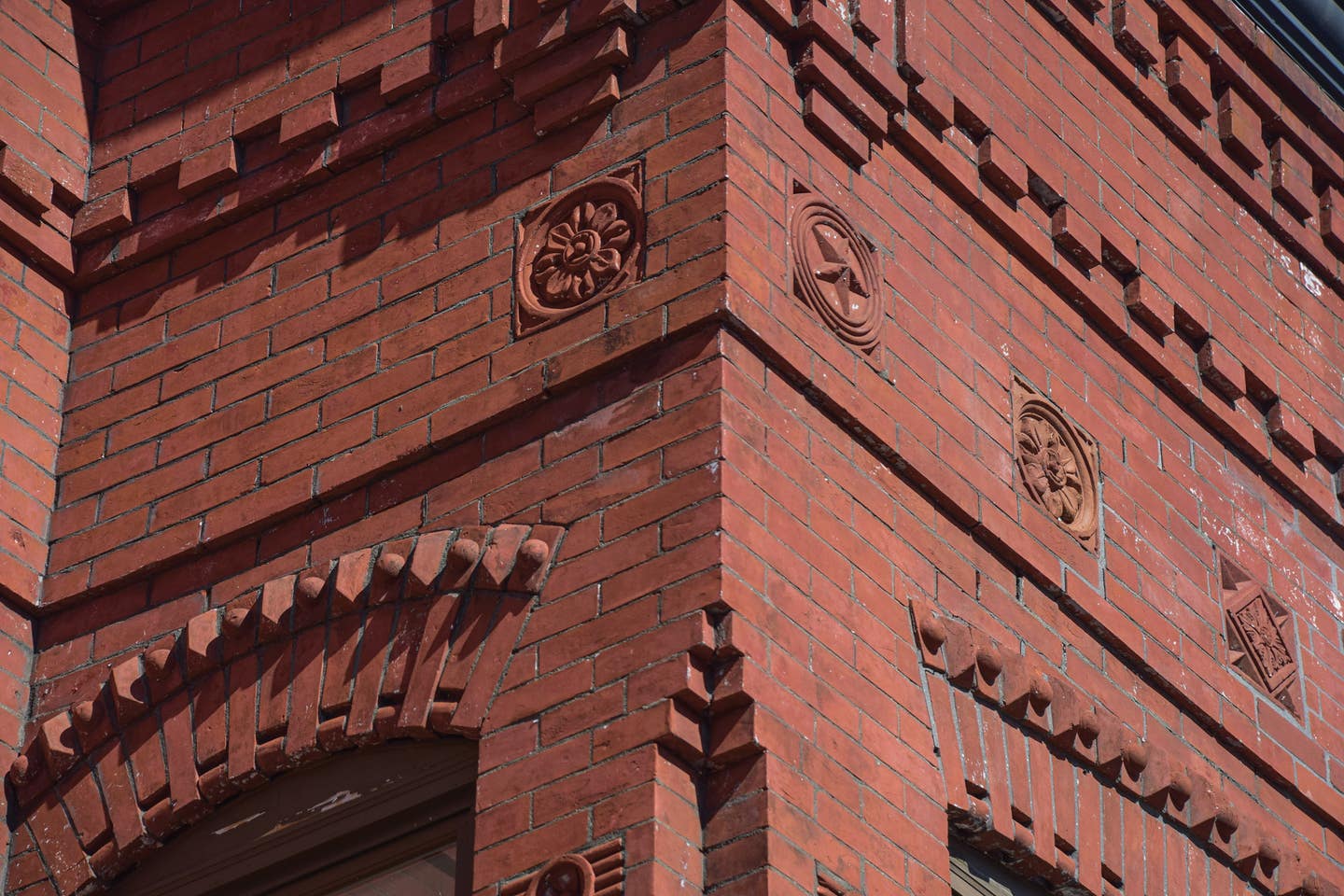
Product Reports
The Trick to Matching Brick
Sourcing bricks for repairing or enlarging historic masonry takes finding equivalents not only in color and texture, but mechanically in shape and performance. The problem is, bricks have been made in many ways over the last 400 years—and seldom uniformly due to differences in clays, shrinkage from drying, or morphing during firing. Since matching historic bricks starts with understanding how they were produced in the past, and why they look the way they do, here’s some clues to the most widely seen types and characteristics.
Pressed (dry-clay process)
The logical, next development in brick-making was to all but eliminate water by compressing dry or semi-dry clay into molds with the immense pressure of hydraulic machinery. This dry-clay process not only obviated the need to dry bricks before firing, expediting manufacture, it enabled bricks of exceptional density and detail. Pressed bricks are noticeably heavy, hard, and smooth, with sharp edges and shapes, and therefore ideal for face brick. The primary developer of pressed brick in the 1860s was what became the Hydraulic-Press Brick Co. of St. Louis, who held patents on the technology for many years. Their products enjoyed extensive popularity from the 1880s on as highly ornamental brick replaced stone for decorative features like window and door lintels, and refined face brick became the cladding of choice for new, steel-skeleton buildings.
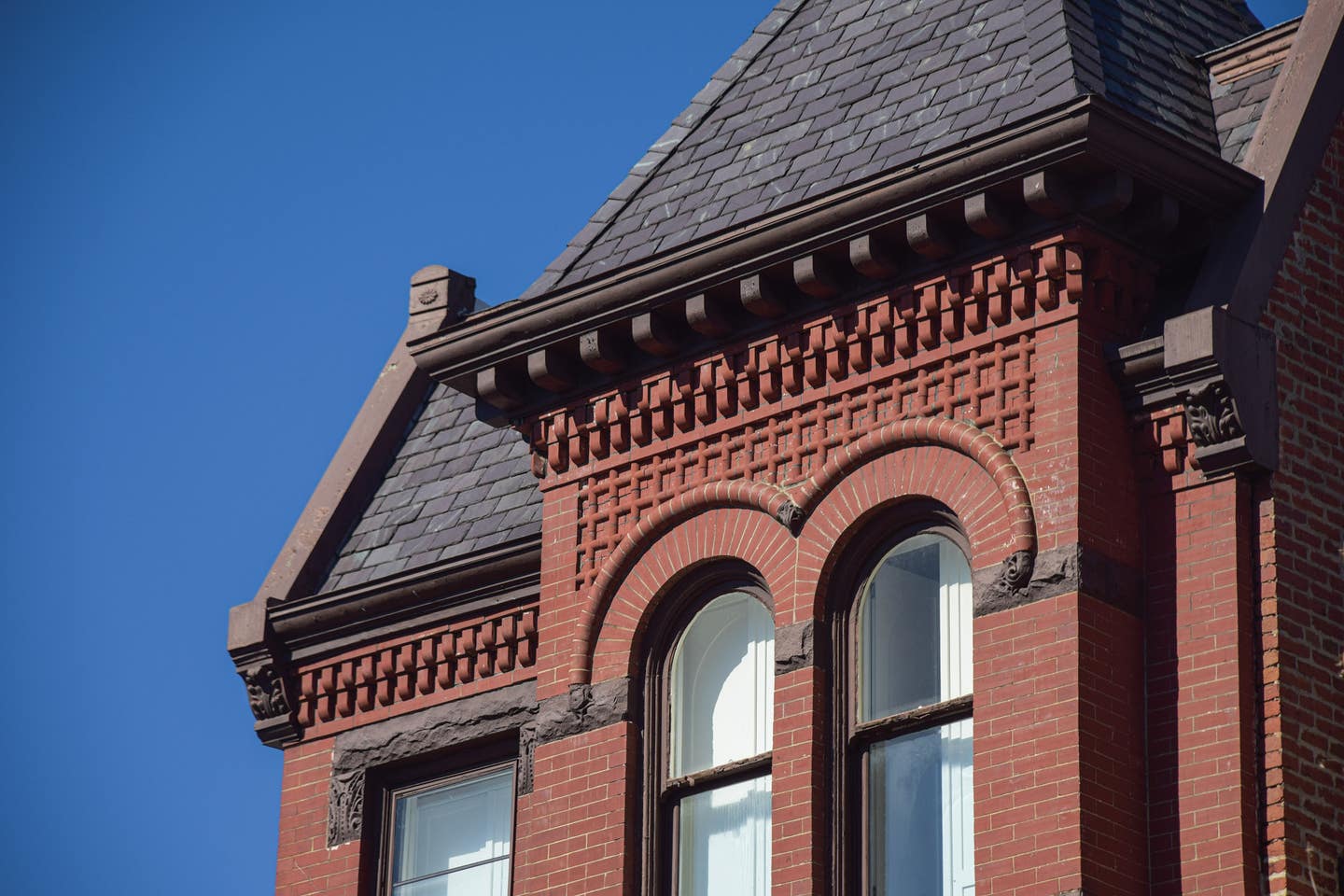
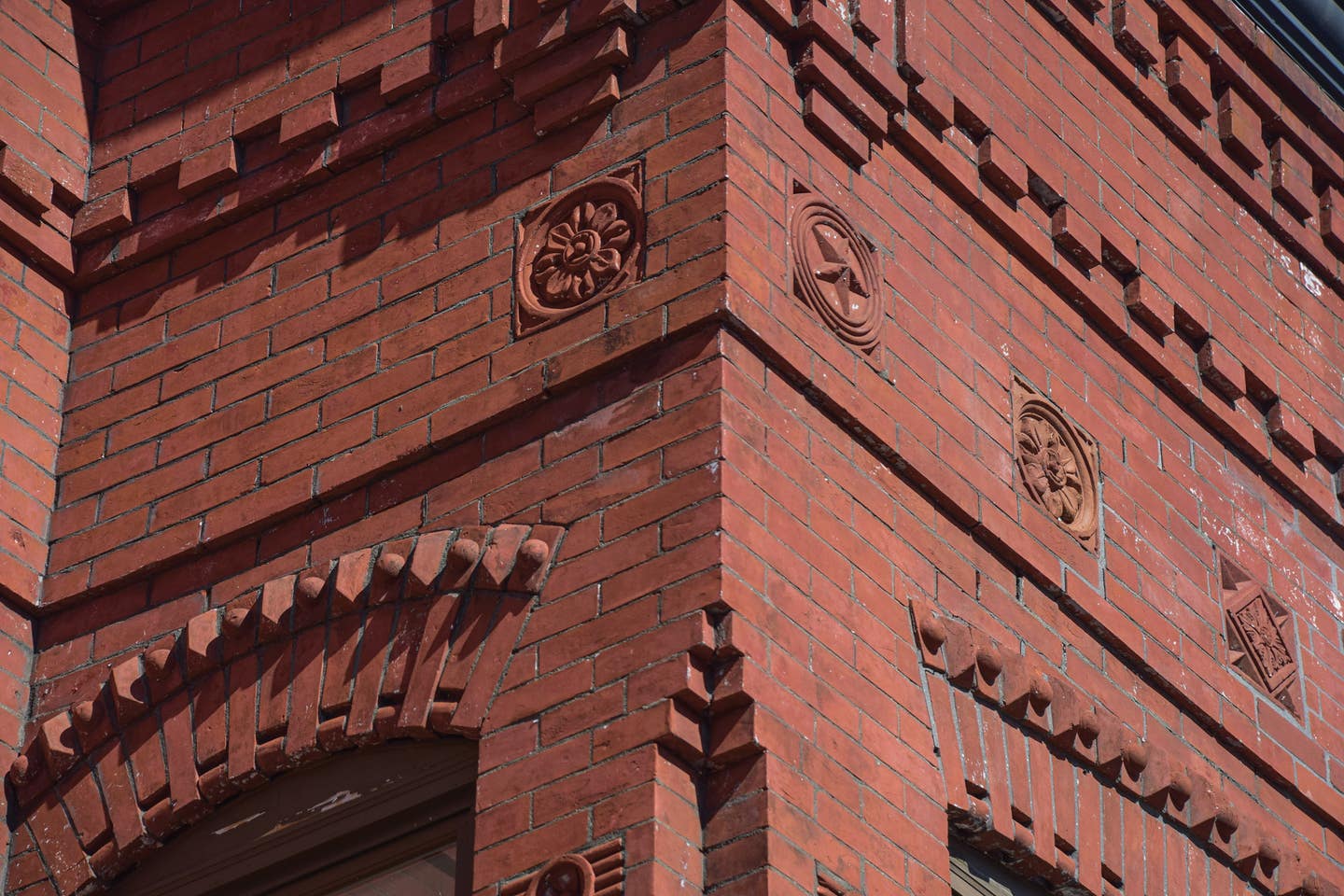
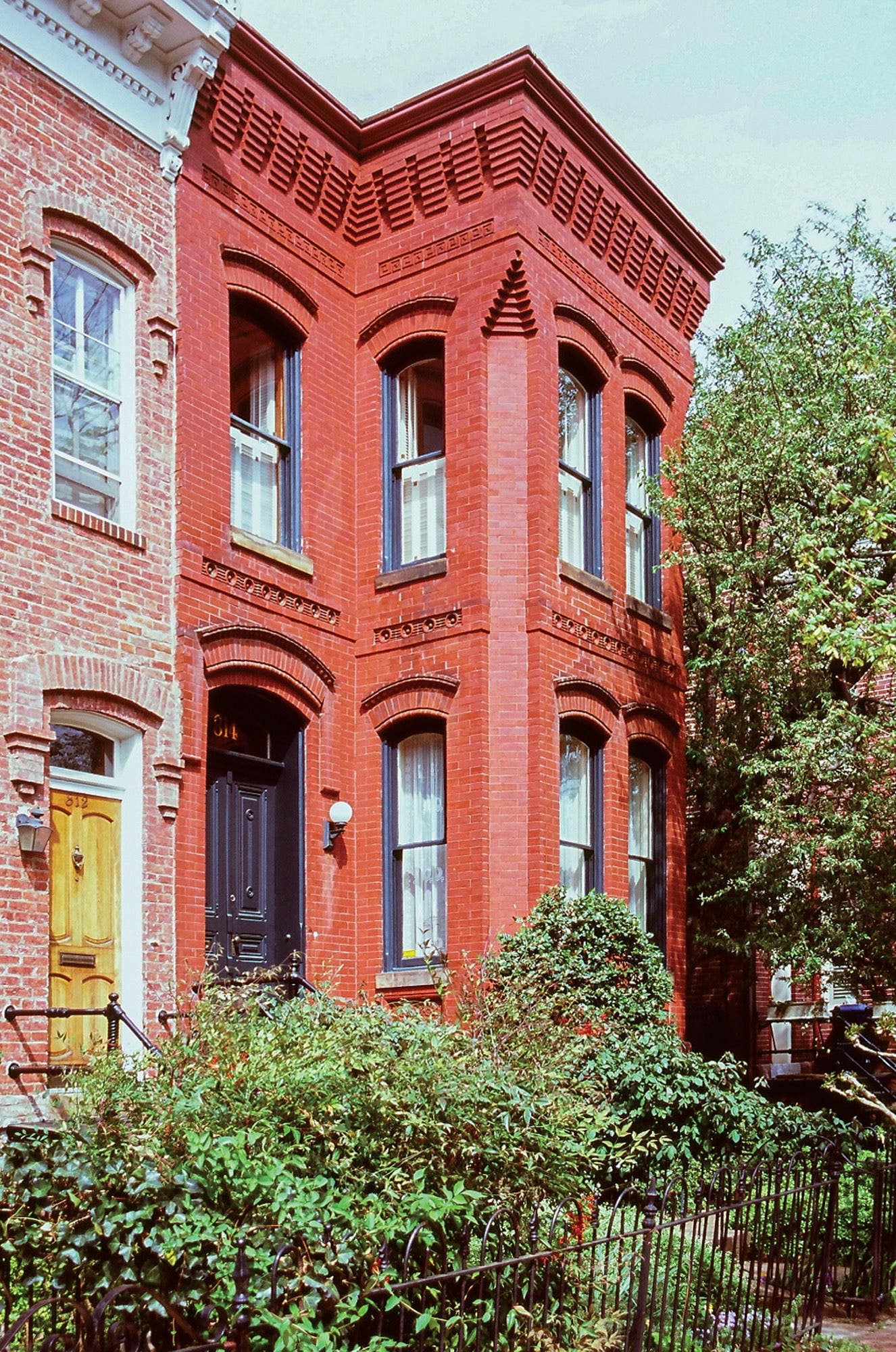
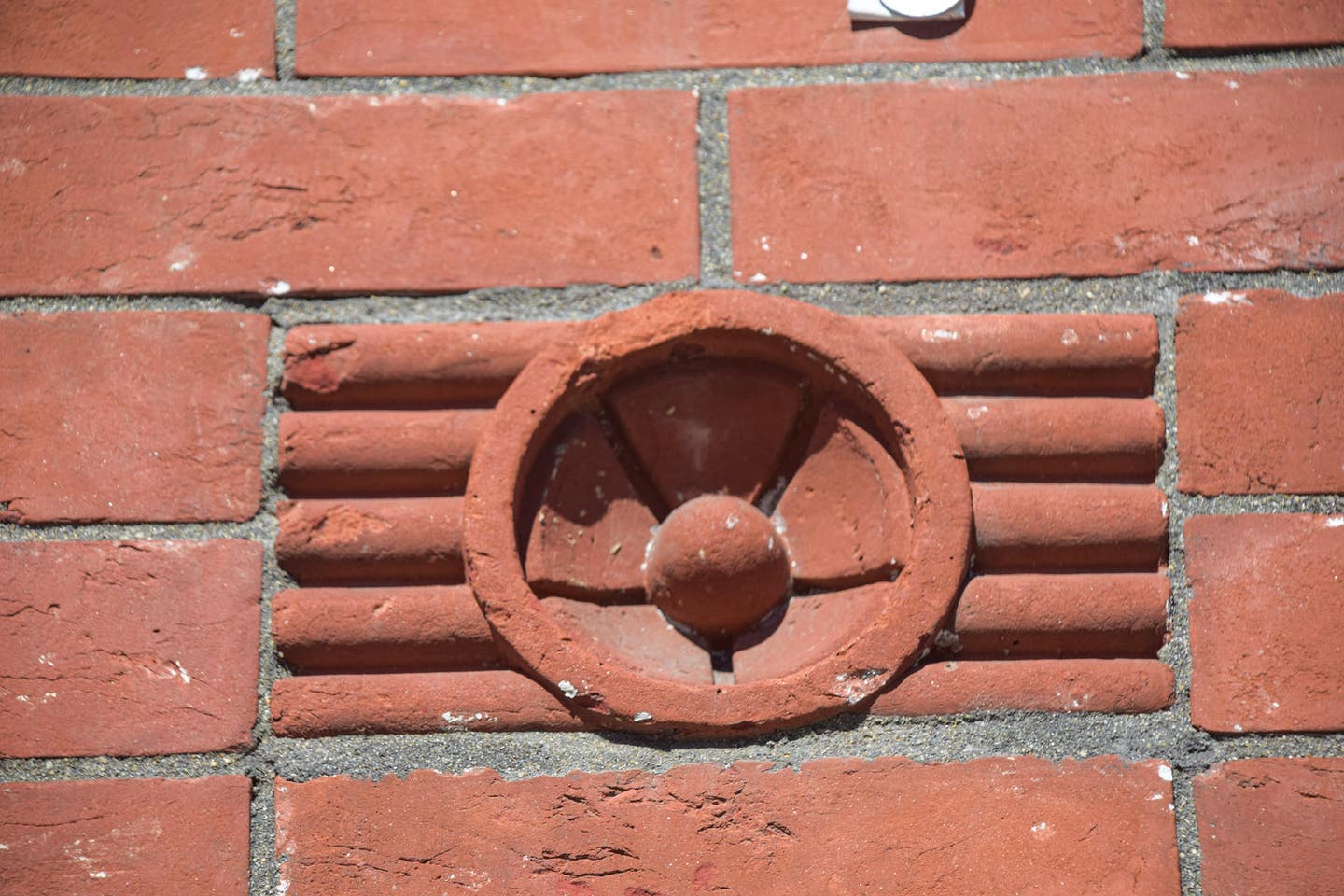
The vagaries of natural raw materials and crude kilns increased the chances a brick would turn out either desirable, charmingly distinctive, or useless. While bricks from high-temperature zones became hard-fired, high-strength, and durable, those from low-temperature zones would be under-fired, low-strength, and slightly larger and lighter in color than hard-fired bricks. Under-fired bricks were also more porous and water-absorbing, making them unsuitable for exteriors and weather exposure. If not immediately culled as rejects, these lighter-colored “salmon bricks” might be salvaged for laying up inner walls where they would remain dry. Even today, salmon brick will not endure if recycled for exterior use. Bricks too close to the heat would be over-fired and twist and distort as they melted into a glassy state. Where minimal over-firing only glazed and darkened brick ends, these units were saved for decorative patterns in walls.
Early brick color varies widely according to the clay minerals and the makers’ limited control of them. The classic hues of red or orange come from the presence of 5% to 6% ferric oxide, an iron compound. Lime content produces cream, yellow, or greenish bricks; magnesia and alumina are the source of buff-colored bricks; blues and purples are common too. Bricks could also be face-colored with treatments such as salt glaze (sodium chloride added during firing) or, after the latter 19th century, actual colored glazes. Presence of iron salts yields an iron-spot effect, coarse grit or pebbles in the clay creates a textured surface, and the list goes on. While longstanding producers can be a source for some of the many types of historic bricks, recycled brick companies are a growing option for local or long-gone makes.
Molded (soft-mud process)
From pre-history until well into the 19th- and early-20th centuries, bricks were hand-made by hand-packing soft, wet, clay paste into wood or later metal molds to form one to six bricks at a time. After unmolding, these bricks were laid out by the thousands to dry before firing in a kiln. In the 1800s, machines mechanized the molding step somewhat, but the basic process remained the same. Molded bricks are readily identified by a frog, an indentation that typically bears the maker’s name. The soft-mud molding, as well as subsequent drying and firing, typically produces slightly rounded arises (edges) and corners and an imperfect shape. Molds might also be first dipped in water or sand to aid unmolding. Such water-struck bricks had comparatively smooth sides but rounded edges and corners. Making sanded bricks might leave sand or streaks on surfaces or a sand-finished texture, if desired.
Wire-Cut (stiff-mud or extruded process)
Brick makers attempted machines in the 1830s, but true mechanization had to wait until steam provided the power to thoroughly mix clay and ingredients, then manipulate it as a stiff paste. While an early stiff-mud machine was perfected in 1852, the invention that really propelled the industry was the wire-cut process, patented in 1863. Here a drier, stiff paste is extruded through a die (like making pasta) to produce a continuous clay ribbon that is then sliced into bricks (like cheese) by wires on a rotating wheel. The wire may cut off bricks at their sides (side-cut bricks) or ends (end-cut bricks). Bricks so produced are very consistent in composition, with precise sides and edges due to the knifelike wire. Wire-cut brick grew increasing popular throughout the Victorian era for refined brickwork and, in one form or another, extrusion is the dominant process today. The die also makes possible textures in the brick face or holes in the body that reduce weight.
Gordon H. Bock is an architectural historian, instructor with the National Preservation Institute, and speaker through www.gordonbock.com.