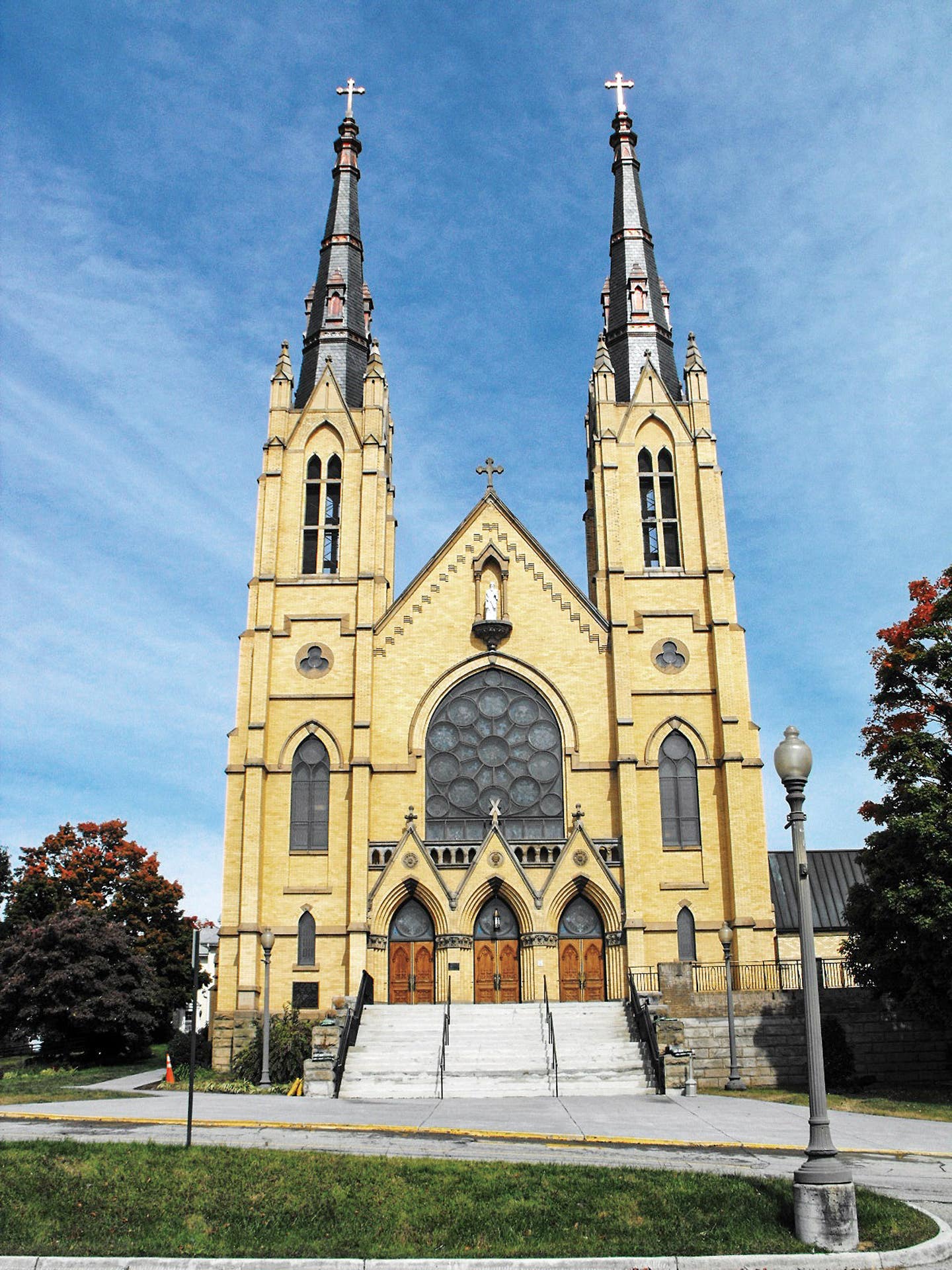
Roofing
Steeplework at St. Andrew’s Catholic Church
Historic twin spires, slender and pointed, grace many a Gothic-style cathedral with their skyward reach, but by the 2010s the pair fronting St. Andrew’s Catholic Church in Roanoke, Virginia, weren’t looking so heavenly. Explains Gary Howes, Chief Operating Officer at The Durable Slate Company in Columbus, Ohio, each of the 53 ft. tall spires sits on a brick masonry bell tower that extends 74 ft. down to the ground. “Those spires were originally built in 1902 on a wood-timber frame structure integrated into the brick, but because of termite damage, water infiltration, and fire in one of them, the frames had really grown beyond repair.”
Further detailed evaluation confirmed the structural deterioration and that both spires were out of plumb by 10 in. to 12 in. at their tips. Adds Shane Day, senior project manager at Durable, “When they started keeping track of any movement, the east spire had drifted another 3/8” over six months, so that’s when the church knew they had to do something.”
The Church decided that, long term, it would be more beneficial to remove the spires down to the internal wood framing and replace them with new, termite proof, steel-framed spires that reproduce the original ornamental copper-and-slate design. “There are cheaper ways to fix these problems,” observes Howes, “say, by putting up prefabricated fiberglass spires, so the Church congregation, led by Wayne Gould, and the Catholic Diocese of Richmond deserve a lot of praise for preserving the building without altering it.”
Durable worked with Gary Loomis of Master Engineers and Design to come up with a steel frame system that was light enough not to add any burden to the brick walls, yet strong enough to withstand the wind loads expected on a prominent hill just off the edge of the Appalachian Mountains. After fabricating all the components off-site, they were trucked in, assembled, then craned up into place. “We also fabricated steel structural cages to insert inside the bell towers and sit on the structural wood columns further down in,” says Howes, “then the steel framing for the spires themselves bolted onto that.”
As in the original construction, Day says they chose Buckingham slate, the legendary blue-black slate quarried since the 1700s and renowned for its unfading durability and 150-year plus life expectancy. “We went back to the same quarry in Arvonia, Virginia, and used the same size, same pattern, same coursing—everything.” Being restoration contractors, he says Durable likes to work with many of the same tools as used originally and very similar techniques. “We matched the same width 1” wood decking as used in 1902—not switching to a plywood or sheet good—and covered it with 30-lb. felt paper; we did add a synthetic underlayment on top (GAF Deck Armor) so the paper won’t blow off during construction.” Slates are attached in time-tested manner too. “There’s a dab of caulk on the back, and then two copper nails.” They also use slate hooks. “In case a slate ever breaks in the future, the hook keeps it from sliding off the roof. (Sometimes wind will shake or work them loose.) Plus, hooks keep the chattering down, but mainly they’re for safety.”
Though Durable finished the twin spires in 2014, the team embarked on a second phase: reroofing of church main body and restoring the center spire, but with a different spin. As Howes recalls, scaffolding the twin spires was pretty straightforward because they could go straight to the ground. “But for the center spire in the nave, we were right on the threshold as far as weight limit for that structure to hold the scaffold, plus the material load. So we proposed to the structural engineer and the church that we take all the fabricated skin off the spire, cut the timbers in a nice clean way, and actually crane the spire off to the ground.”
As Day explains, the process actually took two cranes: one for a man in a basket to be the eyes for the crane and a 210 ton crane to reach over the building and pick the spire off the roof. “The engineer told us how to proceed and, after numbering everything, we hooked the crane up to the spire, cut the timbers with a chainsaw, and lowered it down to the ground in one piece.” As they lowered, they slid the spire inside a scaffolding tower. “I think it was a 10 ft. by 10 ft opening leaving about 6 in. clearance on each side.” From here they moved forward with restoration— copper work, louvers, everything but the cross. Then the spire was craned back in place and bolted to the original framing using custom steel sleeves, as strong or stronger than before.
Howe adds, “The children from the Church elementary school got to watch the raising of the center spire as well as the new copper cross. Plus, parishioners and children signed their names on the spires before craning them into place—an opportunity for everyone to feel connected to the project and historic buildings.”
SUPPLIERS
Wayne Gould - Facilities Maintenance Coordinator
Engineering: Gary Loomis - Master Engineers & Design
Architect: Derek Cundiff - Cornett & Cundiff, Inc.
Tim Winther - Dominion Traditional Building Group
Douglas Redmond and Kendrick Von Davis - Sunbelt Scaffolding
Greg Dooley CSE Inc. - Steel Fabrication and Crane Company
GAF Deck Armor - synthetic paper used on steeples
Ornamentals Supply
Gordon H. Bock is an architectural historian, instructor with the National Preservation Institute, and speaker through www.gordonbock.com.