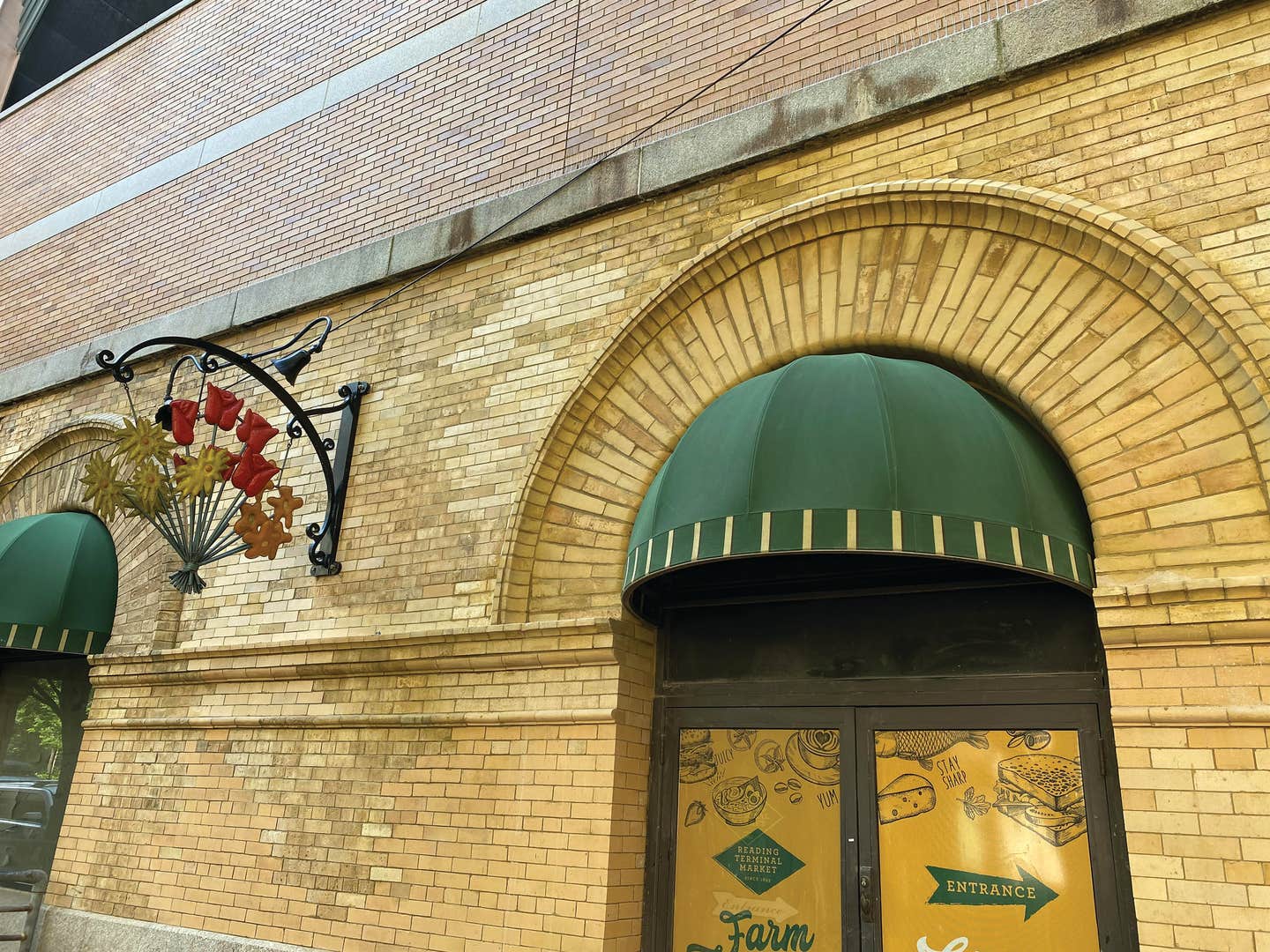
Product Reports
Restoration of Reading Terminal Marketplace
In 1890, the Philadelphia and Reading Railroad Company purchased the site that would become both Reading Terminal and Reading Terminal Marketplace. The site was part of the city’s first public market, and because its merchants refused to relocate, the railroad integrated the market into the terminal design, later opening in 1893.
Reading Terminal Marketplace, designed by Wilson Brothers & Co. architects and engineers, is an approximately 78,000-square-foot structure located at 1115-1141 Market Street. The proximity of the market to a major transportation hub would prove to be a symbiotic relationship. The Pennsylvania Convention Center Authority took its stewardship of the building seriously and revitalized the market beginning in the early 1990s; the marketplace continues today. Granted Landmark Status, the structure was listed on the National Register of Historic Places in 1976.
Time had taken its toll on the structure’s masonry. Repointing is an essential maintenance procedure for brick, terra cotta, and stone, and Reading Terminal Marketplace features all three materials. After nearly 130 years in service, including a repointing campaign in the 1990s, it was time to make repairs.
There are slender, distinctly colored bricks and a granite water table. The brick arches that surround the arch-topped windows are tapered to distinguish the window openings and give interest, light, and shadow to the building’s exterior. Some of the bricks were exceptionally soft and needed to be replaced. In order to get the proportions exactly right for some of the replacement brick, a custom approach to the mortars for the granite and brick and custom brick was called for. Materials Conservation did the mortar analysis, Limeworks completed the custom mortar simulations, and the custom bricks were molded and fired by Stone Art.
The masonry work got underway in 2019, and despite a shutdown during the pandemic, was finished in about a year, according to project manager Chris Hertz of Premier Building Restoration.
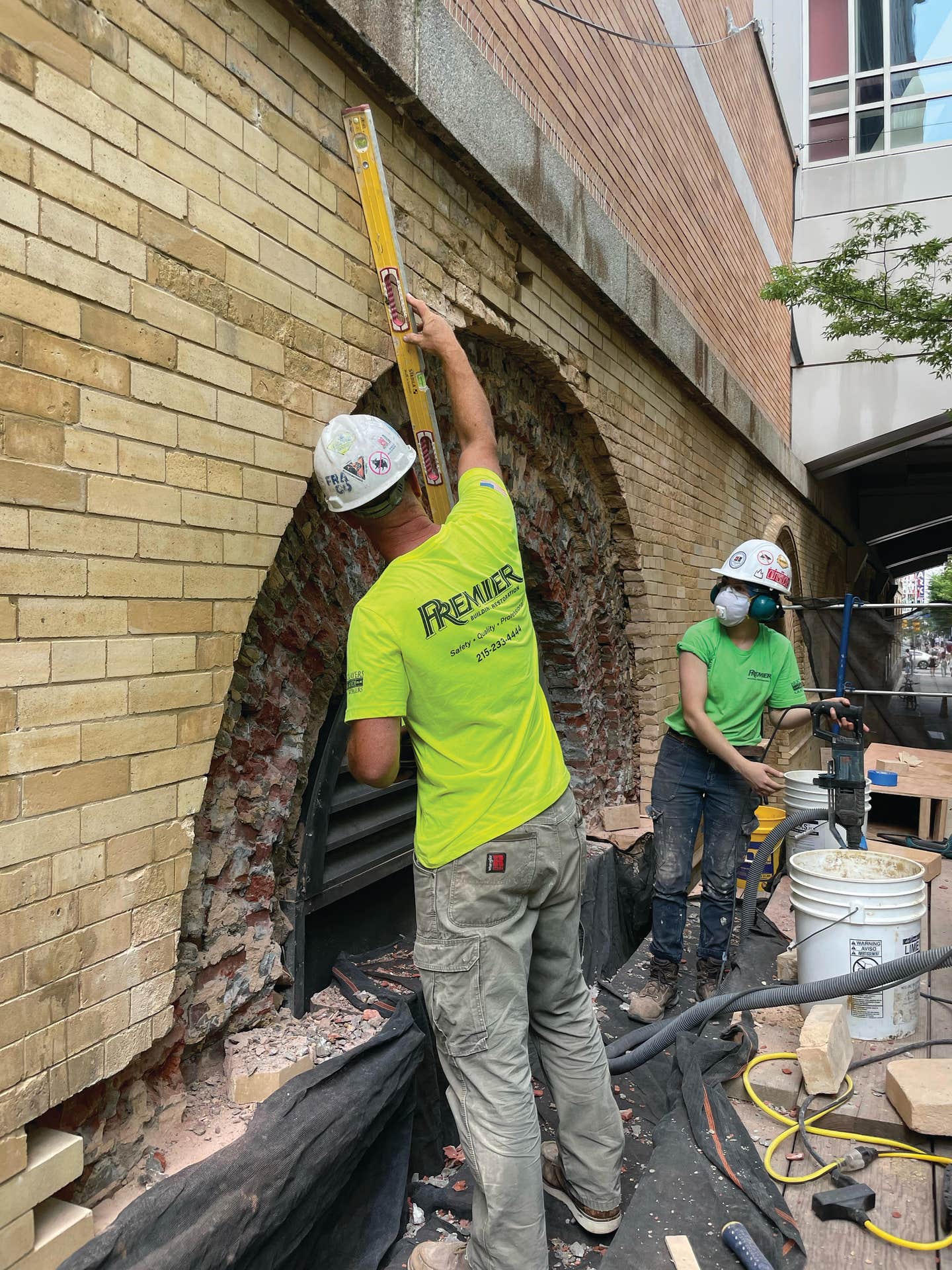
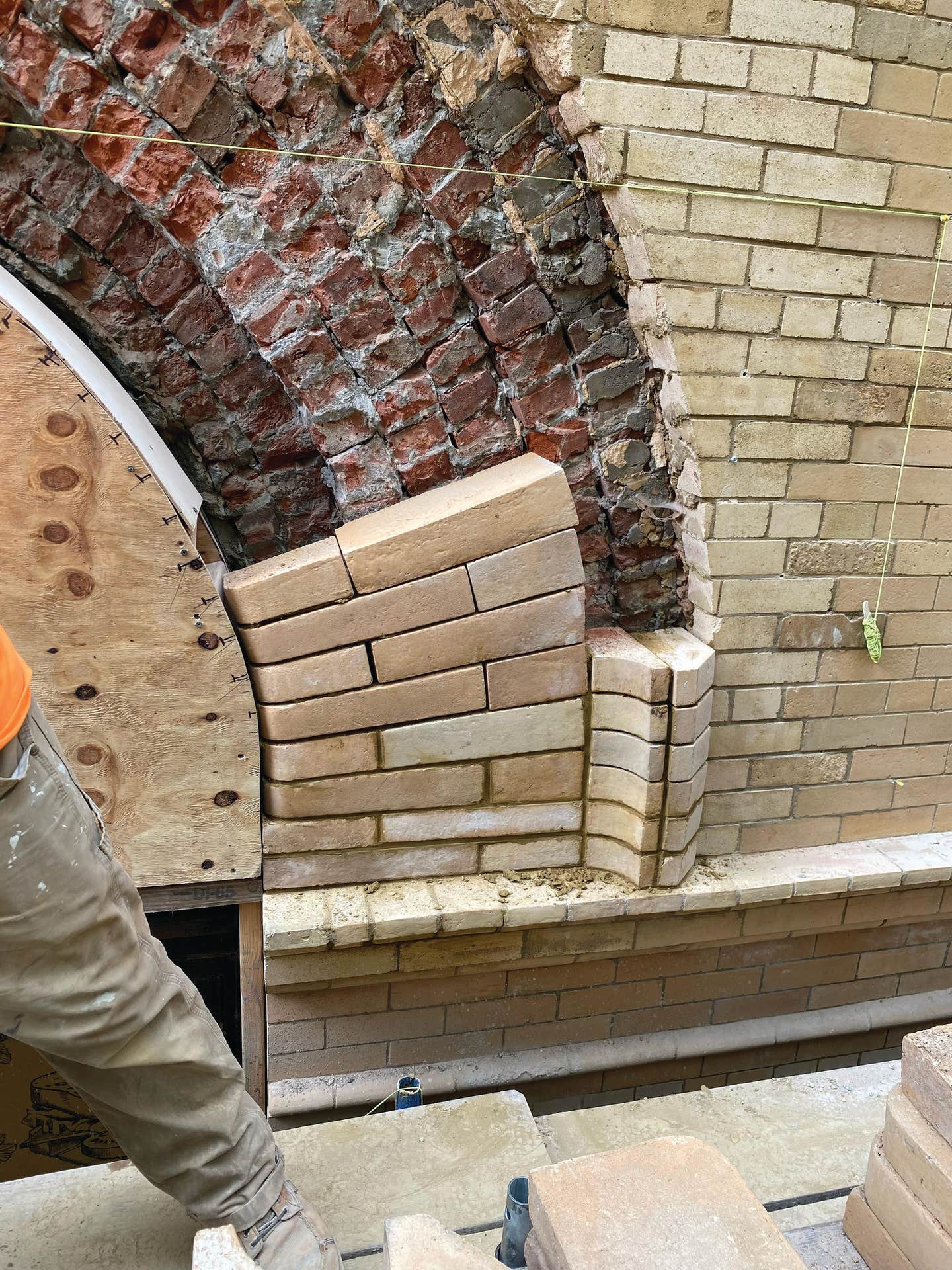
This project had four distinct phases: analysis and documentation; masonry repairs for the north elevation of the building and the final phases; cast iron and wood window restoration for the east side of the buildings; and now, the same for the west side, a phase that will get underway in spring 2022. A veteran of many preservation projects, Nan Gutterman, FAIA, Vitetta, is the project architect/manager.
To accurately duplicate the sizes and shapes of the window surrounds, the team made templates of the original arches. “Every brick had to go back into the right place, new and old,” notes Hertz.
Determining that the 1890s mortar was composed of lime and sand, the team selected a natural hydrated lime (NHL 3.5) with marble dust so that the repairs matched the softness of the brick and the mortar. It was important to soak the bricks in water but wait until they had dried some before applying the mortar. The goal was to control the suction of the bricks and prevent the mortar from drying out too quickly. Hertz explains that as they were working with extremely thin joints, the mortar was applied to the sides of the brick and the top and bottom at only one-eighth of an inch, a thin mortar application called a butter joint. The masons ground their pointers to help achieve this thin, tidy appearance. Once the mortar was applied, wet burlap kept the wall damp to permit a slow curing of the mortar, which they didn’t want to dry out too quickly. Typically, the burlap was kept in place for 72 hours.
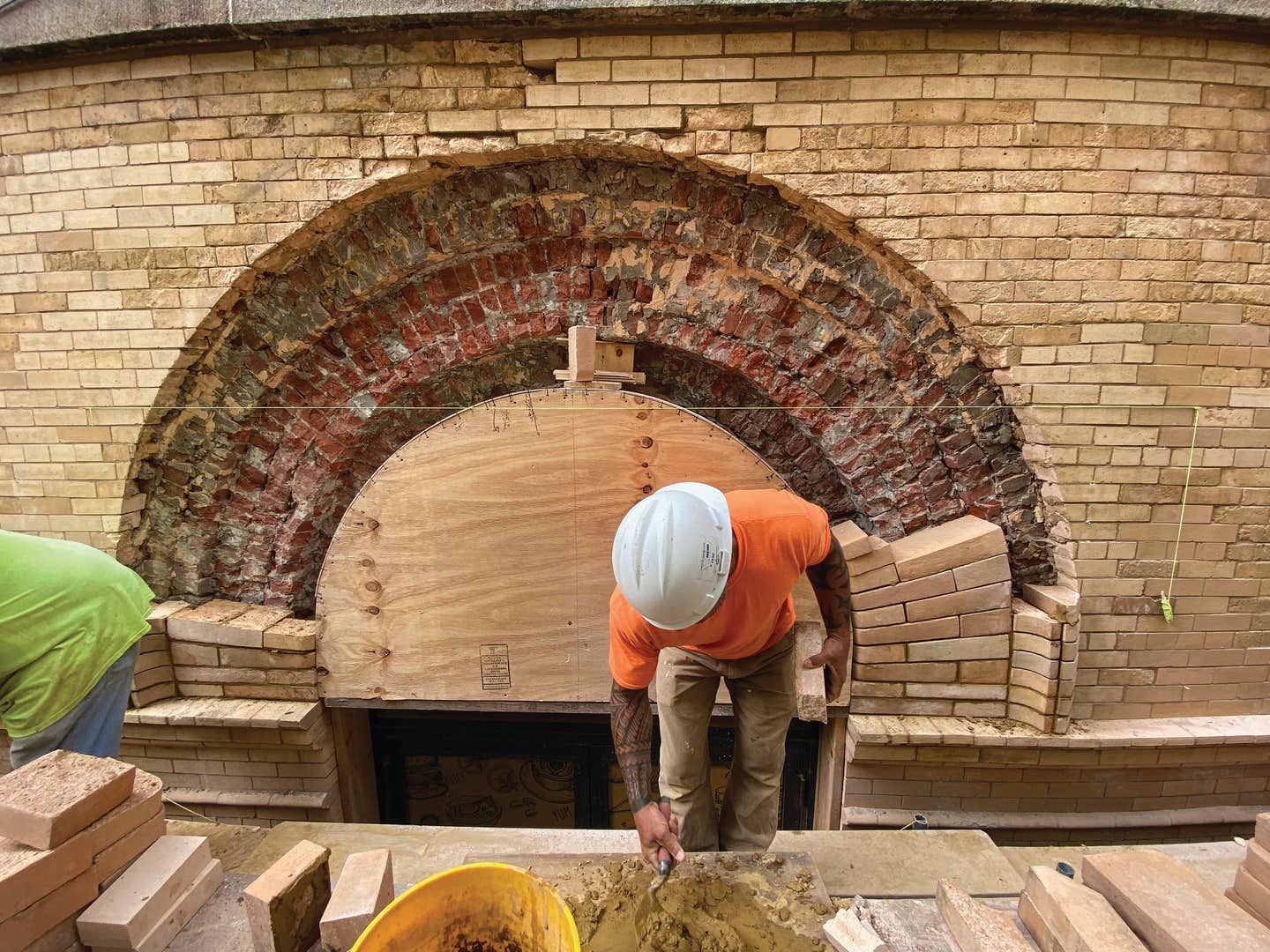
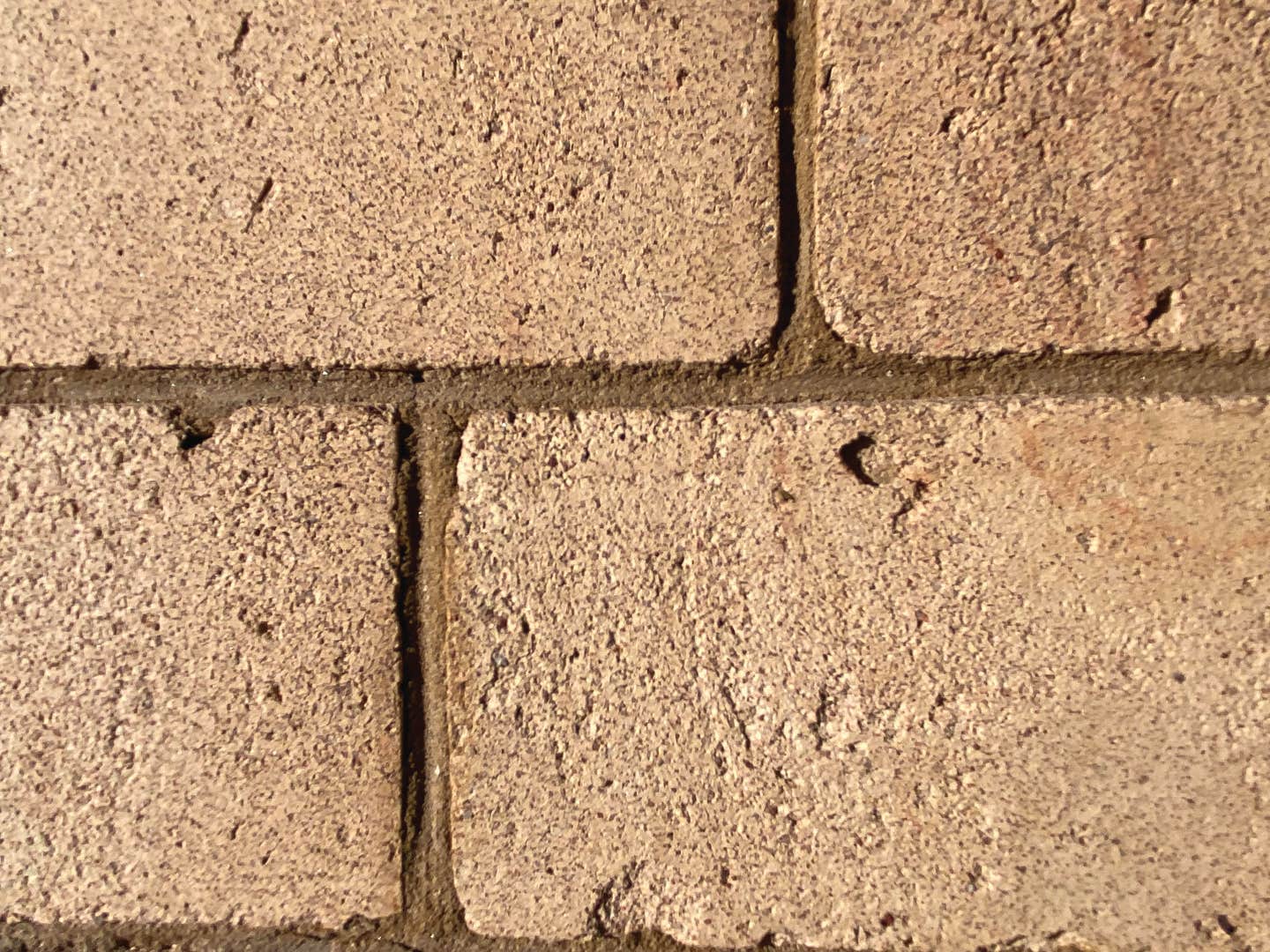
The mortar composition was important for both the structural integrity and the appearance of the building. In order to achieve a color that would weather consistently with the existing bricks and mortar, the mortar was tinted with earth pigments and iron oxide. The mortar should achieve stability for UV light absorption and respect the alkaline nature of the mortar. Marble dust was used as the aggregate for this fine butter joint.
The mortar for the granite comprised NHL 3.5 and sand, and required assorted colors for the match as well. The aggregate was a combination of sharp, well-graded, and clean sands.
Stone Art works in small batches for custom brickwork. In some instances, only 500 to 800 bricks of a given size or shape were needed for this project, along with ten different shapes and sizes. Some of the bricks required tapering to fit into the arches. Intact full samples were used to support the molding and custom color of the new bricks. Stone Art produced mockups for review of the color, size, shape, and texture with the contractor, the architect, and the owner’s representative. A range of colors was agreed upon, and Clemson University tested the brick according to ASTM standards. The International Masonry Institute performed a third-party review of the results.
According to Hertz, the biggest challenge was getting the taper right in the arches. The bricks were fourteen inches long and eight inches deep, and the tapers were four to six inches, depending on the location in each arch.
Keeping the marketplace open during the project was essential, says Hertz, explaining further that with every entrance open, the project had to be “crowd-safe and pedestrian-friendly.” Supports were especially important to keep the wall intact while the work on the arches progressed from demolition through final reinstallation.
Reading Terminal Marketplace, is located at 12th and Arch Streets. If you visit, allow time to stroll around the outside of the building to admire the craftsmanship of matching brick, granite, terracotta, and mortars. Ahead of its time, the National Historic Landmark has successfully integrated access to and delivery of good food for 130 years.
KEY WEBSITES
- STONE ART brickmatch.biz
- PREMIER BUILDING RESTORATION premierbuildingrestoration.com
- READING TERMINAL MARKETPLACE readingterminalmarket.org
Judy L. Hayward spends her days pursuing a passion for historic architecture and the ways in which it can be reused to sustain and grow healthy communities. She develops courses in partnership with builders, architects, traditional craftspeople and others to teach both historic preservation and traditional building skills. She has one foot in the nonprofit world as executive director of Historic Windsor and the Preservation Education Institute and the other foot in the world of media and information services as education director for the Traditional Building Conference Series and Online Education Program.