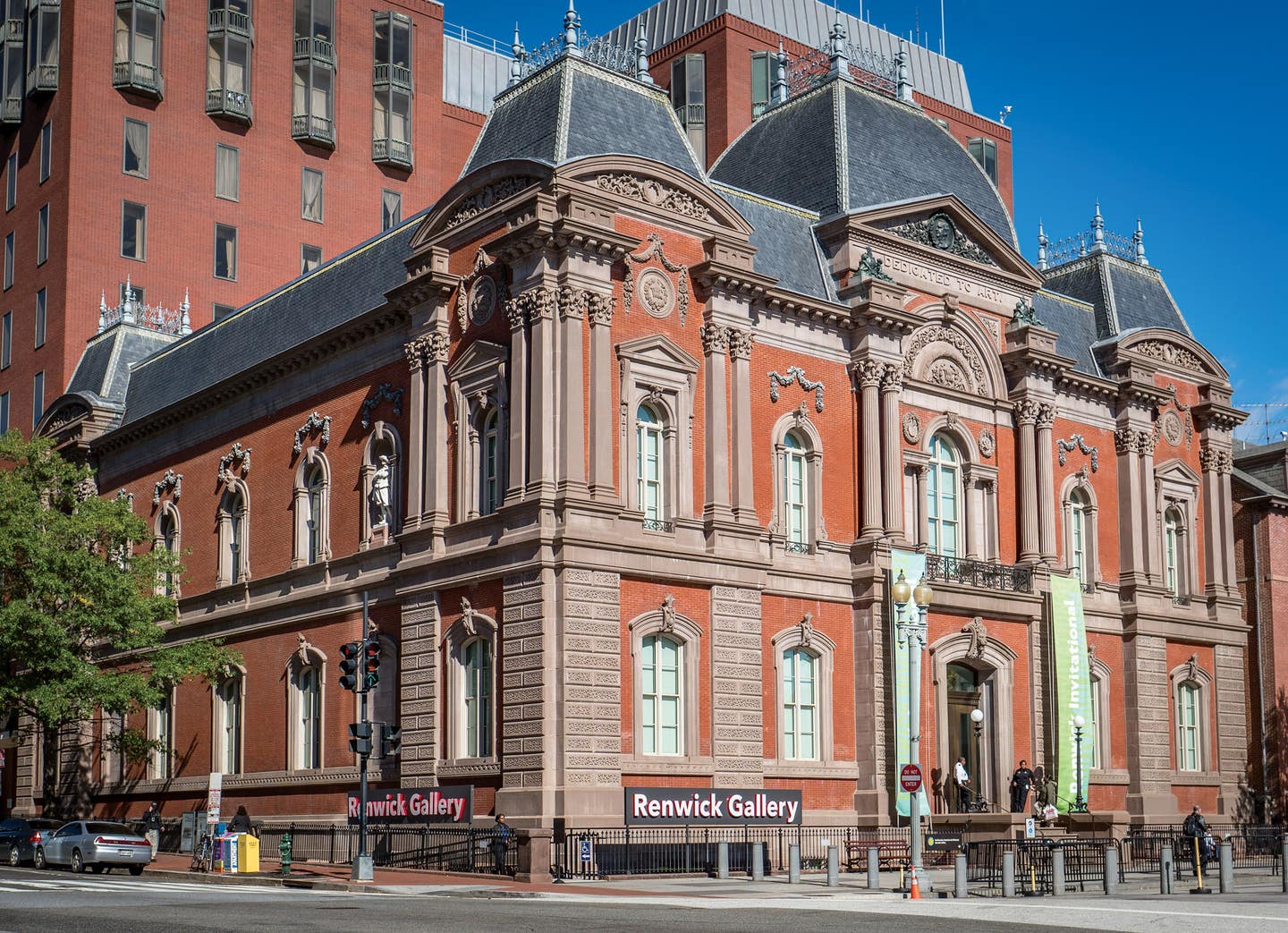
Windows & Doors
Reproduction Windows for The 1874 Renwick Gallery
Making new windows that are faithful matches with historic buildings is tricky enough, but when they must also resist the new reality of potential terrorism blasts, the task can be daunting. The challenge is juggling myriad dimensions, along with code and energy specs, but specialists like the St. Cloud Window Inc. of Sauk Rapids, Minnesota, are experts at finding that sweet spot.
When it comes to the window business, St. Cloud Window divides their expertise into three window types: acoustic, historic, and custom. “In any given year, about 40 percent of our revenue is historic, and about 40 to 45 percent is acoustic,” explains Casey Mahon, president and CEO, “and sometimes it’s both. We don’t necessarily target the blast resistance market specifically, but a lot of times we find it’s one of the performance parameters, with some projects requiring it, some not.”
That was certainly the case with the 1874 Renwick Gallery in Washington, D.C. A $30 million renovation completed in 2015, it included replacing all exterior windows with new, energy conserving units that replicate the originals. Near the top of that to-do list was the force protection requirement for blast resistance—no surprise at a site paces away from the White House and where the consequences of 9/11 are an ever-present reality.
The blast resistance of a window is only as strong as the building’s ability to hold it in place, explains Mahon. “I think the principle driver is to retain the frame in the hole and, in the event of a blast, prevent glass shards from spraying into the room. So, if you want that force protection, you need to secure the window frame.” At the Renwick, Mahon reports that the walls were actually quite sound. “The sills needed some steel reinforcement,” he recalls, “but the jambs and the heads are all brick and stone, so we had good anchorage points there.” They used epoxy anchors—basically threaded rods inserted into epoxy-filled holes and bolted through the window frame—with anchor points located anywhere from 5½ inches to 18 inches on center. “So, it’s a little different than simply driving a few screws, as it were.”
The window frames are thermally broken aluminum, with profiles designed to meet the sight line requirements for replicating the historic windows. “I believe we cut over 30 new shapes for that particular project in order to achieve very precise historical proportions and dimensions, and that’s typical for us when we do historic jobs of this nature.”
Mahon says they work off a basic frame design, then elaborate it with new shapes to achieve the required sight lines. “That’s the beauty of aluminum. You can replicate those shapes relatively easily, so long as you don’t invade the primary frame itself. However, if you get into a significant change in the primary frame, then you need to retest and recertify the entire window design.”
Indeed, performance parameters—from thermal and structural requirements to air and water penetration—can present challenges. “At times they work against your ultimate design objective, and some historic dimensions simply cannot be replicated today because they’re so small.” The answer he says is to be prepared for those challenges. “What we find is that if you can’t go wider to meet the design objective, you can go deeper; so, you can get a little narrower sight line by extending the frame depth, or the mullion depth, a little deeper into the wall section. That will help with the structural load requirements.”
564 Series
Mahon says that the base model for the Renwick windows was their 564 series, which is a 5-inch system. “Everything in that window was fixed glass, but it has an offset sash arrangement so that it appears as a double-hung window.” After adding the profiles for the brick mould and interior finishes, the overall frame depth grew to 9½ inches. They created the separate brick moulds on the outside and interior trim shaped for the inside, both for the sake of the extrusion process and ease of handling at the time of installation. “Windows the size of Renwick’s get extremely heavy, so typically you first set the exterior brick mould—the ‘pan’ in our lexicon—and get everything sealed up. Next you set the primary frame inside of that, then you set your interior trim pieces inside of that.” This way everything can be installed from the interior, “which is nice too because you don’t have to scaffold the building.”
As he explains, the blast-resistant window—here designated 564-I for impact—is essentially an insulated glass unit but with greatly enhanced physical properties. “The composition gave it an overall 1½-inch thickness comprised of ¼-inch glass on the outboard light, and 9/16-inch laminated glass on the inboard light separated by an 11/16-inch spacer.” This configuration not only affords blast protection but also all the coatings that are needed to achieve the required thermal performance.
Balancing all these dimensions and requirements within a historical window is no open-and-shut case. “But today’s window is so far superior to the windows of old,” reflects Mahon. “It keeps it interesting, and it keeps it fun.”
Gordon H. Bock is an architectural historian, instructor with the National Preservation Institute, and speaker through www.gordonbock.com.