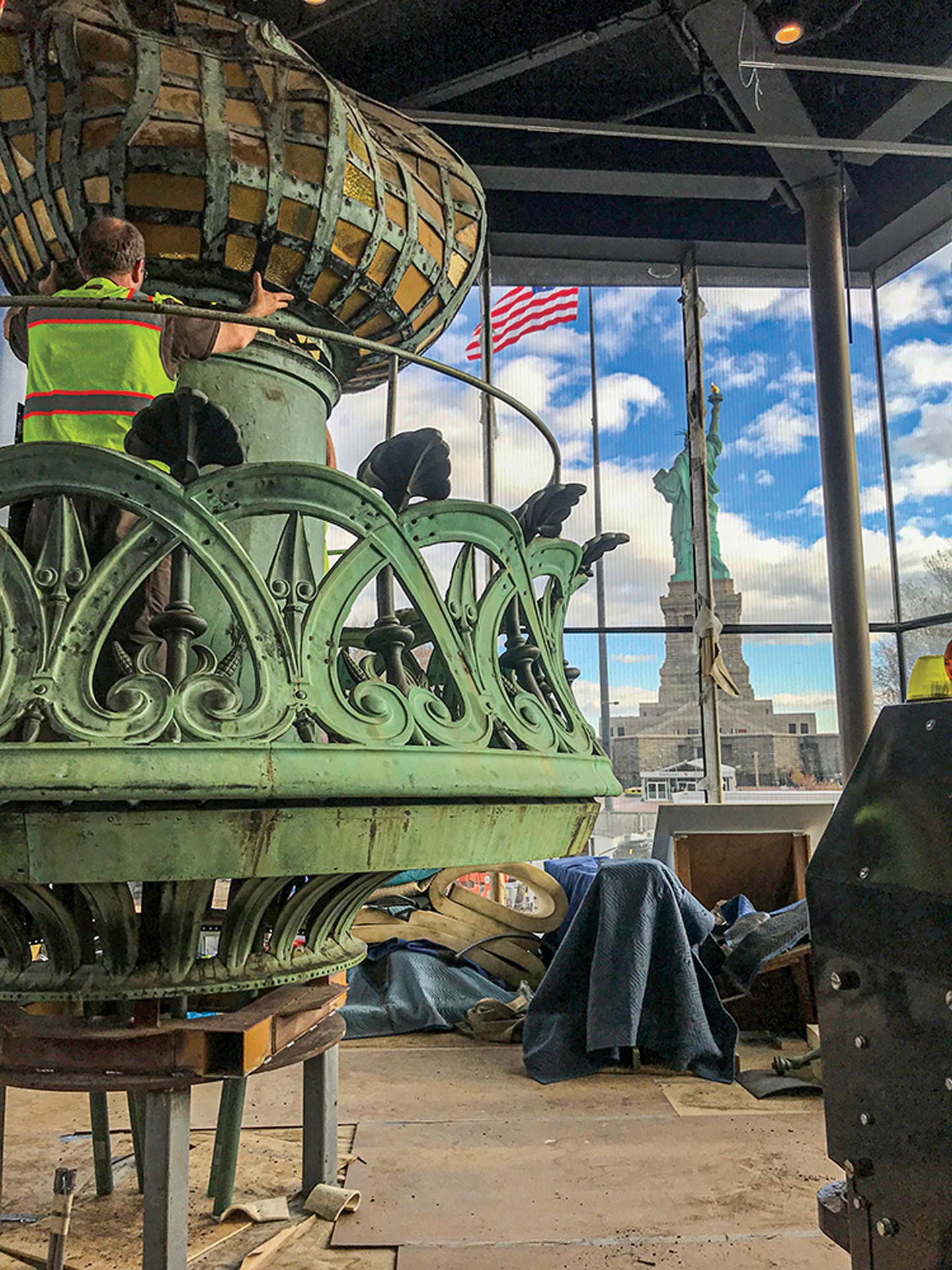
Product Reports
Relamping Lady Liberty
Client National Park Service/Statue of Liberty-Ellis Island Foundation
General Contractor Phelps Construction Group, Boonton, NJ
Rigging J. Supor & Son, Kearny, NJ
Conservation Rambusch Decorating Company, Jersey City, NJ
Museum Architect fxcollaborative, New York, NY
The Statue of Liberty enjoyed a comprehensive renovation to commemorate its centennial in 1986, but it took until 2019 for the iconic torch to be blessed with its own renaissance. “At the time of the centennial renovation, the original torch was replaced with a replica of sculptor Frederic Auguste Bartholdi’s intent,” explains Martin Rambusch of Rambusch Decorating Company of Jersey City, New Jersey, “while the original moved to a museum in the pedestal underneath the Statue.” Recently, as part of $100 million project that includes building the new Statue of Liberty Museum, the original torch has now been cleaned and conserved as the feature of the museum’s Inspiration Gallery right there on Liberty Island.
Just relocating the 16-ft tall, 3,600 lb. torch out of the pedestal became a significant project on its own. “This is an important artifact and we agreed that, prior to any move, the torch required a condition survey. So we at Rambusch, along with our colleagues and associates, Phelps Construction and J. Supor & Son, mocked up the lighting and surveyed every single piece of glass as to its color, texture, and condition, as well as the metal, and how those pieces should be addressed in their new environment.”
“It became very clear that, although wonderful, this was an old object that has lived in the ever-changing, harsh environment of New York Harbor for a long period and been radically altered three times.” Indeed, the torch and hand were the first sections to arrive in the U.S., and displayed at the 1876 Centennial Exhibition in Philadelphia as well as later in Manhattan. Initially, flame was a closed copper shell (with two flame tips relocated in the 1880s) but just before the 1886 dedication, the U.S. Light-House Board cut a double row of holes in the torch and placed lights inside, later expanded with windows in 1892. “Until a nearby munitions explosion impacted the torch in 1916, visitors had access to the balcony around the flame,” reports Rambusch. Shortly thereafter, the torch was redesigned by Gutzon Borglum, the sculptor of Mount Rushmore, to add 600 various pieces of tinted yellow cathedral glass.
Once the torch was in the new space, Rambusch and team began to clean, stabilize, and conserve the glass and metal finishes, and then install a new, flexible lighting system.
Over time, pieces of glass had cracked or failed and been replaced. “Some glass is original and slumped to shape; in other cases, subject to location on the flame, the glass is less dynamic. They’re all in the range of yellow but, depending upon the fabrication, there are slight differences in texture and tonalities. There was a program in the 1950s to repair and waterproof, and while those men did the very best they could, sometimes the replacement glass isn’t a perfect match.”
The metalwork of the flame, however, is all copper in two different forms. “The lower portion, which was changed multiple times, is an assemblage of shaped and formed copper strapping. The upper portion is closer to shaped copper that has been cut out to accommodate the glass.” Like the rest of the Statue, the shaped copper is repousse: sheets heated and formed with wooden hammers. “Replaced parts sometimes used fasteners that were not copper, so there were some dissimilar metal issues, but we didn’t feel they put the torch in jeopardy structurally.”
The goal was not to have the torch look brand-new, he says. “It was to be a century-plus-old artifact that tells a story, so we didn’t try to clean or conserve it back to perfection, but to a weathered, patina-ed surface.” They used de-ionized water (water purified of all charged particles so that it readily dissolves or leaches any salts or ions), and other surfactants where appropriate. “We found a variety of different conditions—some oils, some tar, some dirt—so in all cases we first treated with de-ionized water, and then ascertained what the stain was and how it would be best cleaned and/or stabilized. At all times we took a very conservative approach—that is, when in doubt leave dirt instead of try to get the surface clean.”
The lighting itself is all state-of-the-art LEDs moving through a Lutron dimming system that allows for wide flexibility. “The client—the National Park Service, supported by the Statue of Liberty Ellis Island Foundation (SOLEIF)—was not sure what they wanted for a final color, so we gave them the most opportunity.” The flexible lighting system controls volume, density, and hue, and can produce an infinite variety of color. “It’s as simple or sophisticated as desired; they can have one setting or multiple settings. The lights can only turn on or off, or they can move through a sequence of low, high, low, changing color densities throughout the day.”
Preparation, estimating, and planning the move consumed many months in advance of the two weeks of actual site work for relocating the torch. Cleaning, stabilization, and conservation on-site took another several weeks before the final cleaning and rededication in May 2019. “You have to be careful what you’re doing,” observes Rambusch, “because this is a truly unique, once-in-a-lifetime project.”
Gordon H. Bock is an architectural historian, instructor with the National Preservation Institute, and speaker through www.gordonbock.com.