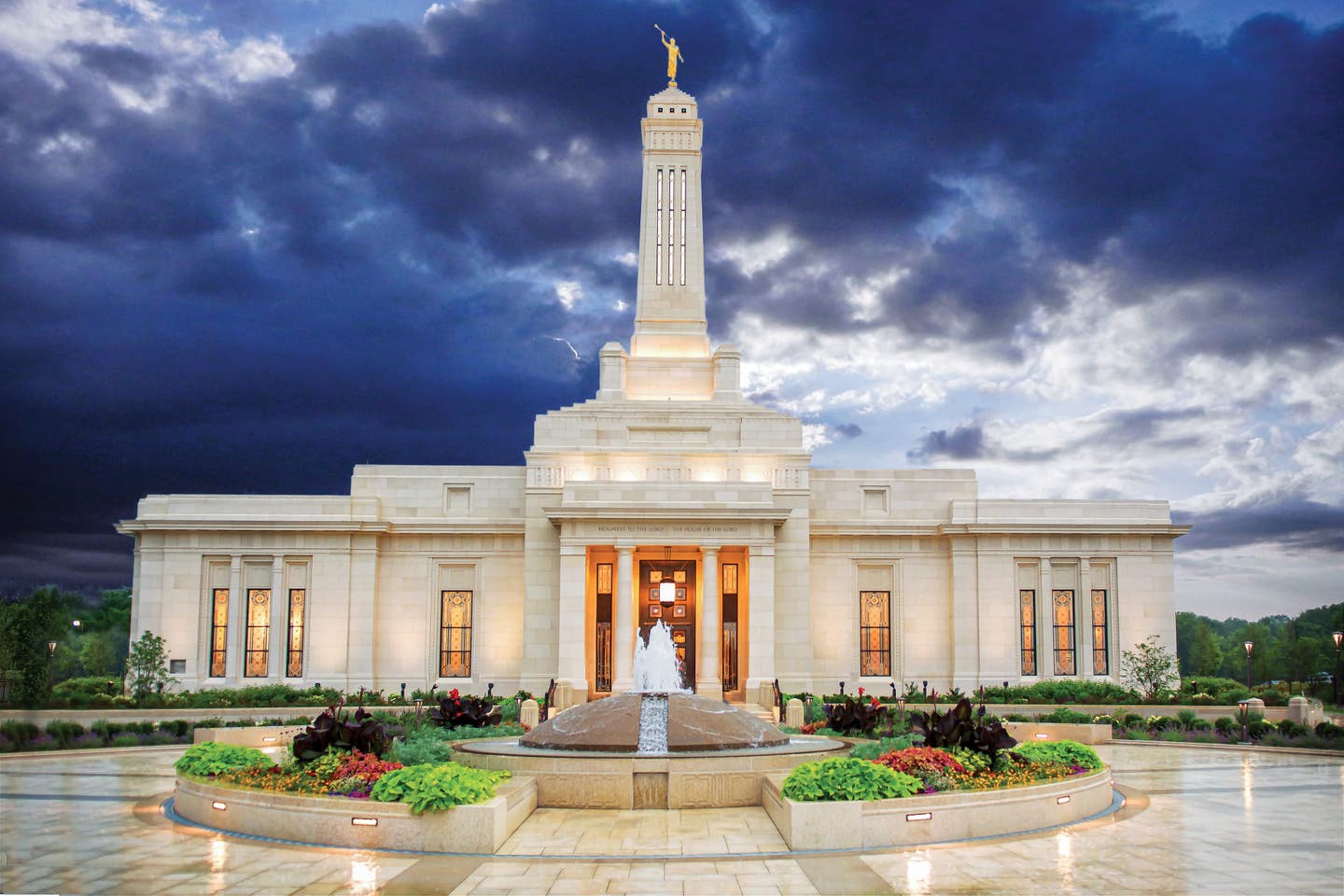
Product Reports
Regional Motifs in Classical Architecture
Borrowing from the classical canon, the Indianapolis Indiana Temple uses the Doric order to lend heft and strength to the single-story structure. Five years in the making, the limestone building was informed by the city’s historic Monument Circle, which is evidenced in the two carved spires, the taller of which reaches 86 feet above the roof, the other being 150 feet from grade. A circle-and-square motif—common in Latter-day Saints temples—was particularly important here, given Indianapolis is named “The Circle City.” MHTN Architects, the team behind the project, took cues from the city’s organization around a central circle. To inform the stepping of the stones and the design of the battered walls, they looked at significant civic monuments including the Indiana State Soldiers and Sailors war memorial. Regionally inspired design motifs include carvings of the state tree’s leaf and flower, which are visible in the stone window surrounds. Interestingly, a few of the carved-stone capitals have a lotus motif said to be of Egyptian influence. Other decorative elements feature Celtic knot line work in continuous bands and ribbons; and topping the temple is a gold leaf–gilded fiberglass finial of Angel Moroni.
A strong east-west/north-south orientation is demarcated at each cardinal point with a portico defined by freestanding limestone columns. The north-south porticos are broader than the others, the north being the broadest with an additional column. According to lead architect Randall Knight, the attic of each portico is ornately treated to highlight the center point of each façade; and each center point corresponds to important ritualistic interior spaces. The exteriors also feature ten fluted limestone pilasters incorporated between windows.
The temple’s materiality was imperative. The 35,000 square feet of stone is predominantly a Turkish limestone. “Knowing this is Indianapolis, the heart of limestone building country, the church determined it would be most appropriate to do limestone, which is not typical for temples,” Knight explains. “They are usually clad in a light-gray granite and are a brighter white. But Indiana limestone has a deep, buff-gray color.” Because that color was problematic, the church asked the team to look at alternative limestones. Ultimately, they chose Aero Creme, which comes from a quarry outside of Antalya, Turkey, and is fabricated by Metamar.
Façade specialists KEPCO+ played a large role in selecting the stone. “Our understanding of this client’s expectation for ‘temple quality’ stone meant there needed to be a very thorough quality control program in place, and an equally diligent inspection and monitoring procedure,” KEPCO+ president Bruce Knaphus recalls. Knight adds: “The client didn’t want any elements in the stone [such as markings, fissures, veins, or mineral deposits] that would be a distraction or would compromise the serenity of the temple. The Aero Creme limestone does have some movement and figure in it, which is great because it looks like natural stone, but it needed to be consistent with no dark spots.” To that end, the team traveled to Turkey for multiple quarry inspections as well as stone slab and block reviews, during which they identified the color and quality criteria to guide Metamar’s team. Mock-ups were then made with precise attention paid to how the various architectural elements would come together in the final installation and what those details would need to achieve aesthetically.
Of course, nothing is truly perfect. But additional measures were taken to get as close as humanly possible. “We purposely chose a much harder limestone than Indiana’s limestone,” Knight notes, “and that’s good for longevity but it can be a little unforgiving in terms of chips and spalling. Though it was expertly fabricated, it was disconcerting to see chipping. But KEPCO+’s master cosmetic masons came behind with special epoxy mortar mixes and color matches—you would never know that here and there were some imperfections.”
According to Knaphus, everything above the 20-ft. mark was panelized in order to minimize labor costs, speed up the schedule, and reduce the need for high scaffolding. KEPCO+ fabricated and installed a total of 98 panels; they included the entablature detail around the main roof level, the roof attic, the screen walls, and the spire cladding. The tower was also panelized and erected in eight sections. The company performed the work in their Indianapolis facility, where back-up frames were galvanized and the stone was attached prior to the panels being trucked to the site and installed with a crane.
Because the temple is a 21st-century building, the stone façade needed to be able to move and react to lateral forces like high-velocity winds; there’s also a slight seismic-load potential. Hence the need for movement joints, which, Knight notes, the team wanted to incorporate in an artful way. Among the benefits of using the panelization system was the opportunity to conceal those joints where the panels are clipped back to the roof diaphragm. Drift joints are visible at every corner, where there’s a quirk miter detail—near the base of the building that miter resolves into a scoop. “That’s how we could get those drift joints to work without interrupting the beauty of the building,” Knight explains.
Set to withstand climate zone–related conditions as well as centuries of occupancy, the temple is a celebration of classical architecture, regional identity, modern-day craftsmanship, and the beauty of natural stone.
RESOURCES
Exterior: Aero Cream Limestone cladding, quarried in Myra, Turkey, and fabricated in Isparta, Turkey. Managed and installed by KEPCO+ of Salt Lake City, Utah.
Art Glass: Glass images of Orem, Utah. Much of the glass came from Kokomo Opalescent Glass in Kokomo, Indiana. It was assembled by artisans in Tijuana, Mexico.
Fountain: Both granites were fabricated and carved in Fujian Province, China. The fountain stone was installed by KEPCO+ of Salt Lake City, Utah.
Landscaping: The landscape architect was Ratio Architects of Indianapolis, Indiana. Featured are many varieties of plants, flowers, and trees native to Indiana.
Fence, Walkways and Plinth Garden: The plaza, curbs and plinth gardens were constructed from granite, quarried, fabricated and carved in China. The fence was fabricated and installed by Capital City Ironworks of Indianapolis.
Flooring: Blocks of stone were quarried in Italy, Pakistan, and Iran. They were fabricated in China and installed by Bedrock Quartz of Utah.
Pilasters: Aero Cream Limestone pilasters and columns were quarried and fabricated in Turkey. Perlatino marble pilasters were quarried in Iran and fabricated and carved in China. These stone elements were installed by KEPCO+ of Salt Lake City, Utah.
Interior Glass (Baptistry): The clear interior glass in the Baptistry viewing wall, curved railing, and doors were fabricated by Glass Images of Orem, Utah.
Lighting: Lighting for the temple was fabricated and installed by HB Lighting of Bronx, New York.
Millwork: Fabricated and carved by Granite Mill & Fixture Co., Salt Lake City, Utah. It was installed by Glen’s Custom Cabinetry, LLC.
Baptismal Font Railing: The bronze railing surrounding the font was fabricated and installed by Stewart Iron Works of Erlanger, Kentucky.
Baptismal Oxen: The twelve bronze oxen supporting the baptismal font were designed, cast, fabricated, and installed by Atlas Bronze Casting of Kearns, Utah.
Baptismal Tile Work: The marble mosaic came from Iran and Pakistan and was installed by Bedrock Quartz of West Jordan, Utah.
Bas Relief Mural: This unique marble panel depicting the baptism of Jesus Christ was sculpted by Jacob E. Dobson Studios, LLC.
Painted Mural: The original oil painting wall mural, depicting nature landscape scenes of Indiana, was done by Michael Albrechtsen of Olathe, Kansas.