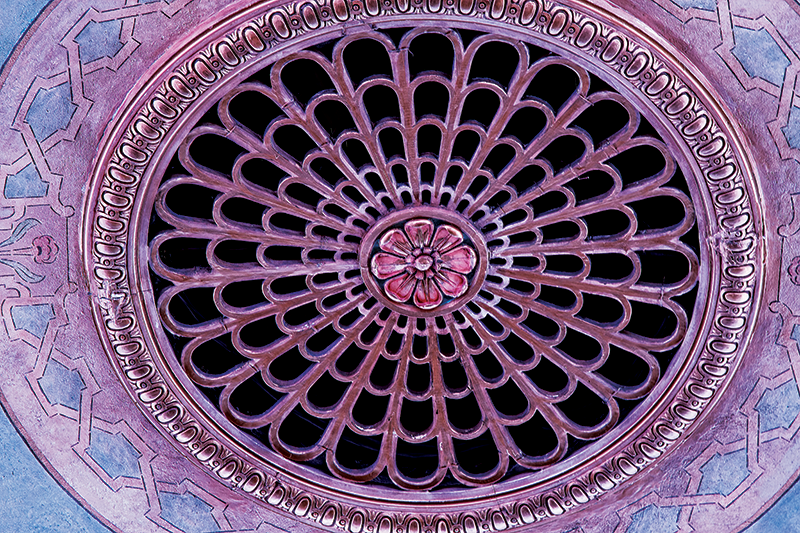
Product Reports
Ornamental Plaster in Today’s Traditional Market
By many measures, interior ornament is part of what defines traditional architecture – especially compared to modernism. Seemingly easiest to understand from a materials standpoint when it already exists, many kinds of ornament can become confusing, especially when the call is to create anew or resurrect in a restoration. To help understand more about plaster, experts in architectural ornament share some insights on what can be done and what architects should keep in mind for the best results.
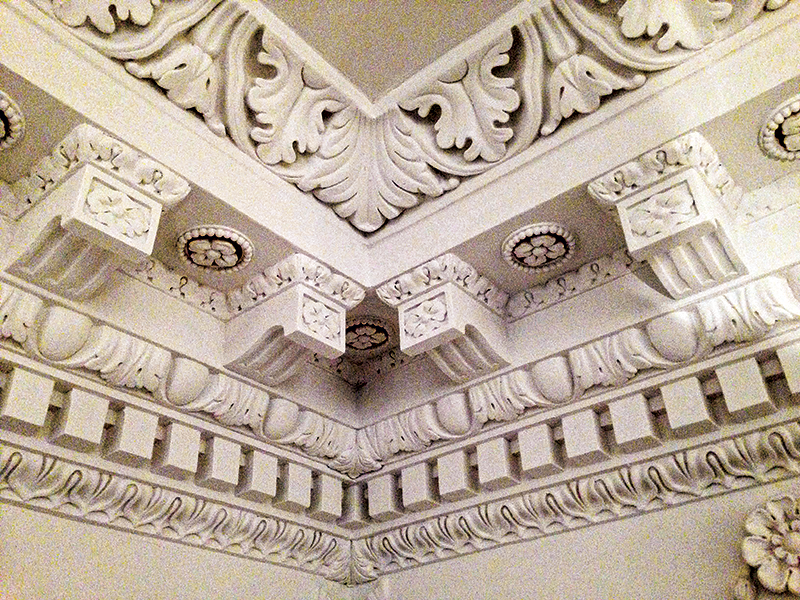
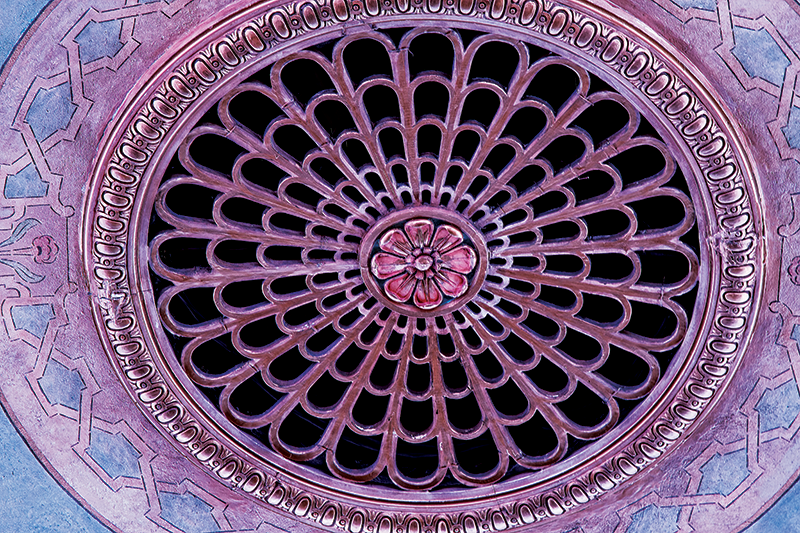
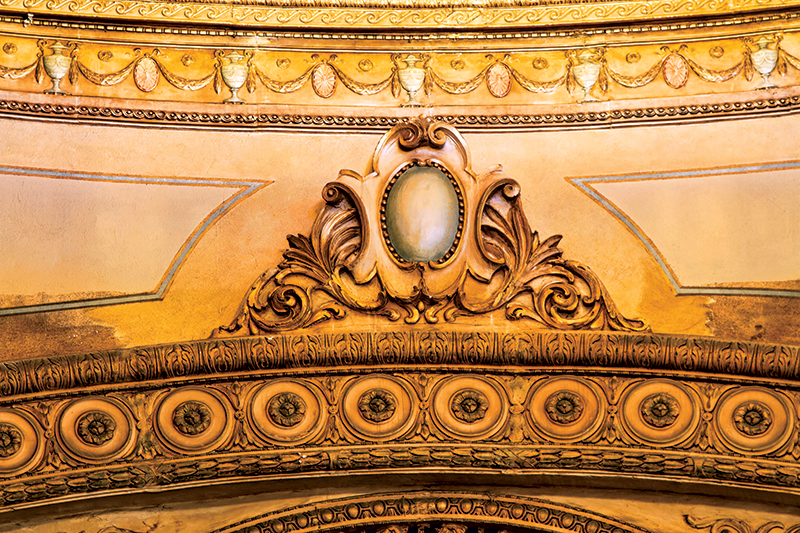
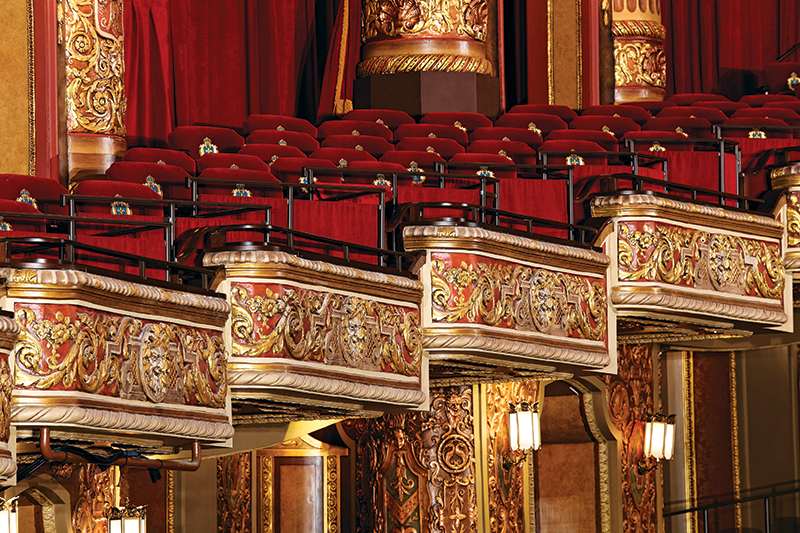
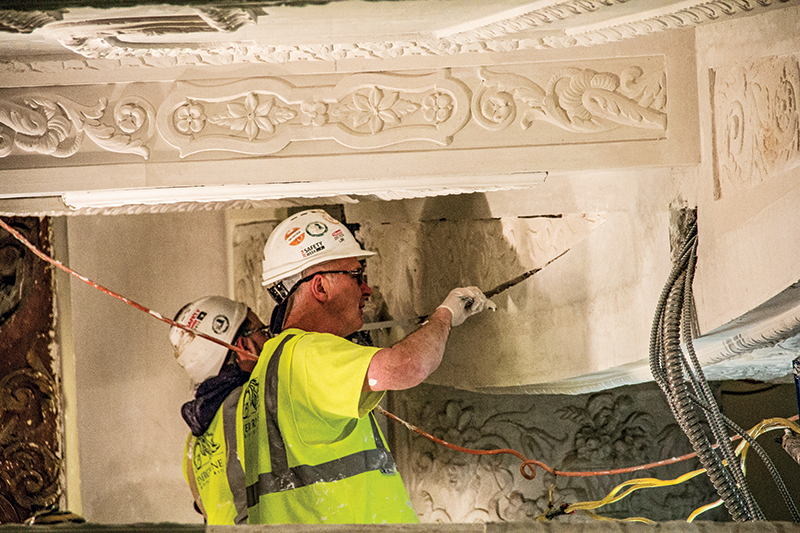
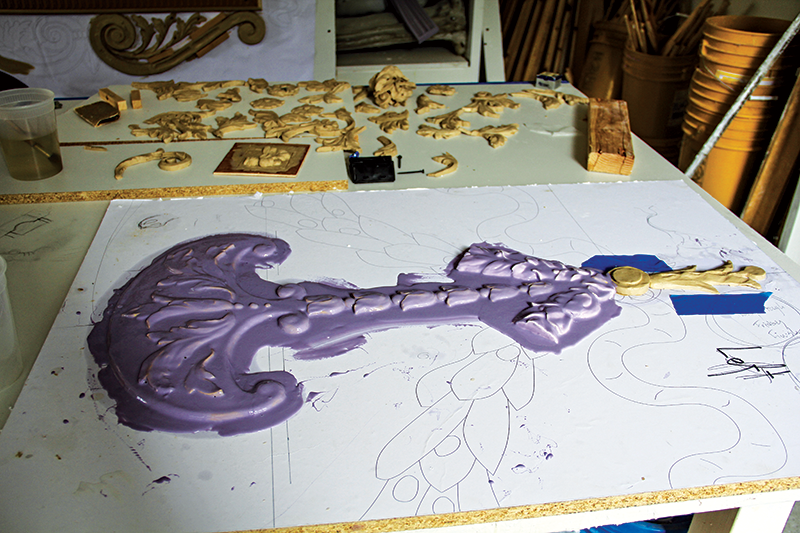
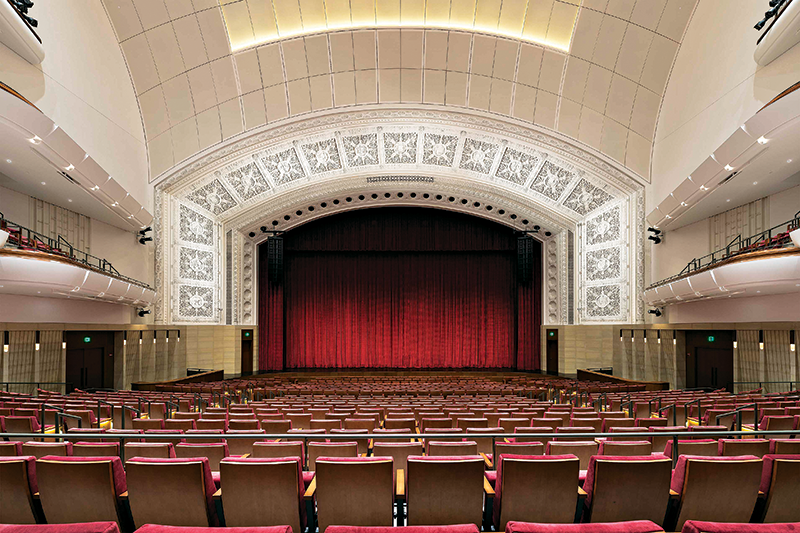
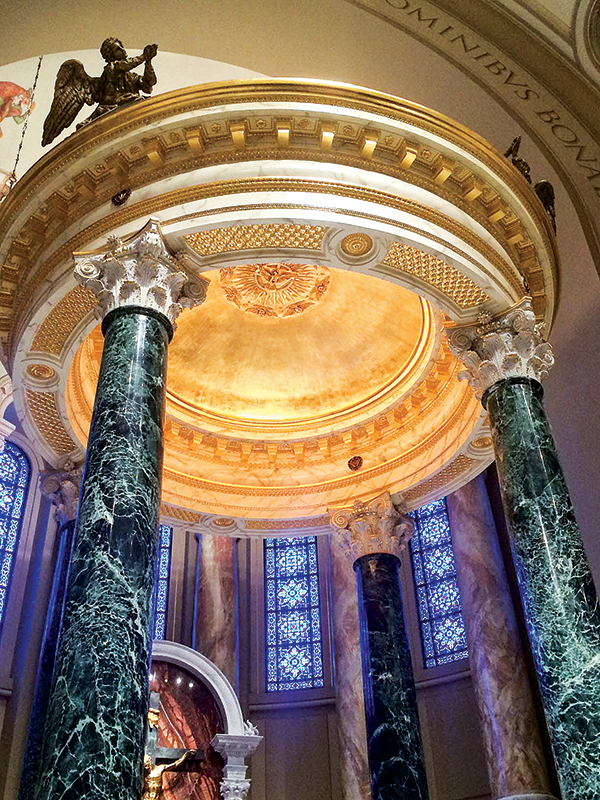
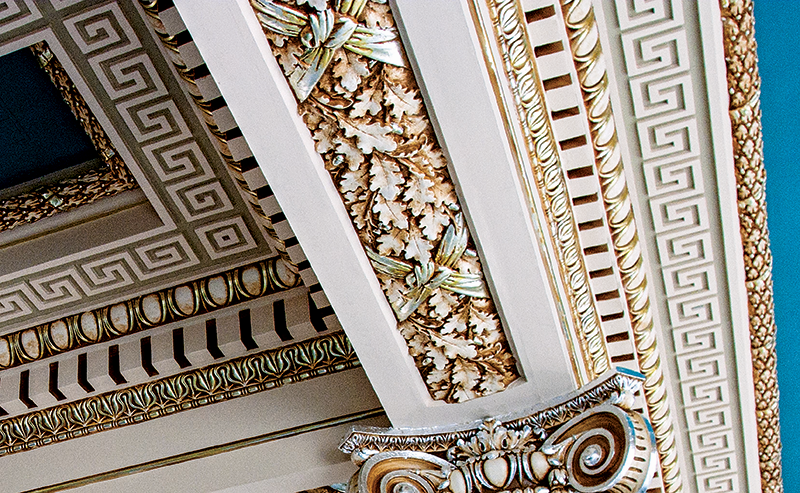
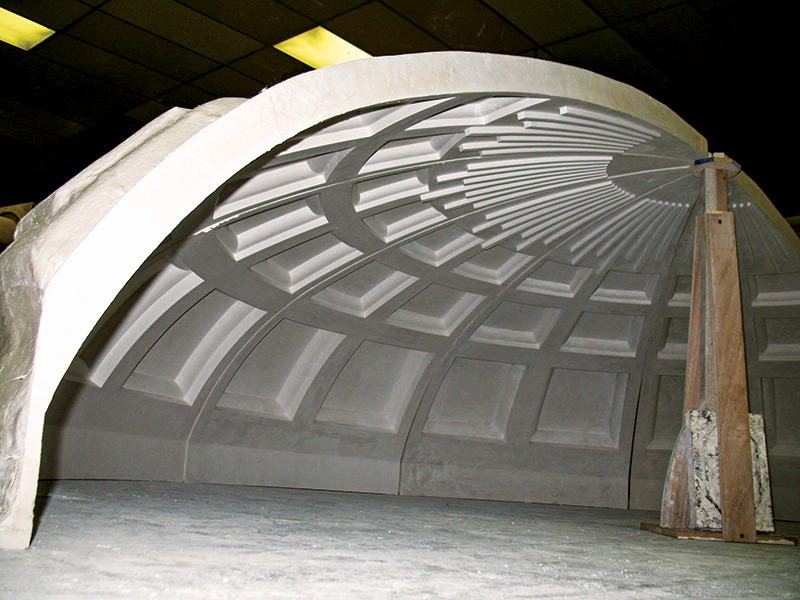
“Every job is different,” says Gunar Gruenke, president of Conrad Schmitt Studios of New Berlin, WI. “Plaster is often less complex than a decorative painting project because it is usually one material. The plasterer and painter are brothers and sisters on a project. They work together.” Conrad Schmitt works closely with Chicago Ornamental Plastering Co., of Chicago, for its plaster projects.
Explains Jeff Greene at Evergreene Architectural Arts in New York, “Some architects either think traditionally (which can be wonderful up to a point), or they don’t realize what the possibilities are. Therefore they don’t utilize all the advances in the plaster and ornament industry, which are basically from the last 10 or 20 years.”
James Kuryloski at Felber Ornamental Plastering Corp., Norristown, PA, concurs. “I think what a lot of architects don’t understand is that there are craftsmen around today that know not only how to recreate and put back old ornamental plaster, but also to make it look exactly as it did, but by employing some of the newer methods and materials.” Adds Greene, “The skills of three-dimensional ornament are basically sculptor’s skills, and all the innovations that have occurred in sculpture for fine art can be applied to architecture – and even in the technology of ornament conservation and preservation.”
“The possibilities are limitless with plaster,” says Matt Luczak, owner, Chicago Ornamental Plastering Co., whose firm has been in the business since 1896. “Most people think of plaster as white walls and ceilings, but it has so many applications such as ornament, statuary, exterior stucco, tinted finishes and scagliola.”
“Plaster is a very broad material and has many uses and applications,” says Brett Swiatek of Swiatek Studios, Buffalo, NY. “A lot of it can be preserved, whether it is in a church, a theater or another type of building.”
Materials New and Old
For a design field as wide as traditional ornament, it should be no surprise that its materials are no less varied and malleable. “Plaster is a big term that covers both lime and gypsum,” says Greene, “and since you can mix them, there’s also an intersection of the two.” As he explains, traditional plaster is based on lime (calcium carbonate) and gypsum (calcium sulfate), but today there are also modern versions.
“Gypsum manufacturers have calcined (high-heated) it to different temperatures and incorporated different admixes, so now we have high-tensile strength gypsums like Hydrocal or Hydro-Stone that cure very, very hard, producing very high strength in very thin applications,” he adds. Nonetheless, these modern versions can be crafted with the same casting skills and techniques as traditional materials. “When you talk about GFRG, which is glass fiber reinforced gypsum, it only means that you’re using some high-tensile strength plaster with glass reinforced fiber, which substitutes for the natural hemp or hessian or burlap used in the past.”
Kuryloski agrees and notes that, in his view, modern gypsums and GFRC are just a few of the many materials at the artisan’s disposal. He says that while his company often still makes features such as cornices using the traditional, softer plaster and burlap, the harder gypsums are much better for domes, columns and elements prone to abuse. “When you bear in mind that, in a lot of cases, this plasterwork is going to be installed by carpenters, not plasterers, they have to be able to handle the pieces in order to install them, so you want your columns or cornices strong enough to not break as they take it off a truck or out of a crate, as well as stand up in the installation.”
Modern materials open up possibilities because they permit the construction of thin-walled ornaments and features that are still plaster, and thus won’t burn or give off smoke, but are much lighter and therefore require much less elaborate framing. Says Greene, “In the old days, if you did, say, a large cornice in a theatre, court house or church you would often have to frame it out and then lath it with wood lath. Cornices three- or four-feet high certainly couldn’t be solid plaster because they wouldn’t stay up. However, with new materials you can build lighter and stronger, which also changes the way you install them, for example by building in an internal armature.”
Another advantage of modern materials and systems, adds Kuryloski, is that you can make bigger plasterworks. With domes, for example, he says, “there’s really no limit to the size you can do.” He describes an 80-ft. dome project for a casino in Atlantic City. “It was produced in segments – some 75 or 80 sections -- and more elaborate than pieces of pie because there was an outer perimeter ring, and then a next tier ring, and then another tier ring, and then a skull-cap in the center.” All were hung from wire and cast with bevels around all four sides so that when they were butted together they could be taped and skim-coated. “We were able to install the entire dome from a high-reach lift as other work proceeded on the floor. The whole thing was installed in much less time, with much less framing, and without an entire scaffold, so the clients were very happy with it.”
What’s more, new ideas don’t have to come from the latest technologies. Greene says that by restoring significant historic interiors made with odd – even weird – techniques, they learn about how craftsmen ‘pushed the envelope’ on materials 100 years ago. “We worked on the Illinois State capitol, which is ornamented redominantly with carton Pierre – a fascinating material that’s somewhere between paper mache and plaster.” He says it’s pressed into molds (as opposed to poured in), and after being heated with steam, it gets sticky and the molded ornaments are stuck to the ceiling. “From the dust heap of history we’re sort of picking up all these arcane, wonderful techniques that can be revitalized, either for the purposes of preservation or for making new.”
Swiatek points out that he often uses acrylic injection to conserve existing plaster. “Acrylic modified plasters increase the breathability and the elastic effects of plaster for improved movement. A specific project that outlines our capabilities is the Hollywood theatre of Gowanda, NY. It was built in 1926 by Rochester architect Leon H Lempert & Son and was abandoned in 1992. Swiatek Studios was employed to conserve the original fabric of the theatre, including the friable and delaminating plaster and conserving all decorative painting. We used molding plaster reinforced with fiberglass.”
He notes that he uses basic materials such as baking soda, alcohol and water for cleaning plaster.
Gruenke points out that there is often efflorescence on the walls of historic buildings. “You need to go in and scrape and remove everything and get the wall to a neutral ph. Then you put on bonding and then other coats.”
He adds that cracking is often a problem in the plaster in historic buildings. “We see a significant amount of cracking in historic buildings plaster, and the telegraphing of lath and rafters coming through ceilings due to lack of insulation. Buildings are always contracting and expanding. Sometime just scraping and patching cracks is not going to solve the problem. The plasterer or painting contractor has to put a fiberglass wall system over the flat surfaces – using a polymer, then fiberglass (18-22 ml. thick), then another coat of polymer, then HiBuild paint (thicker paint so you don’t see the fiberglass). This prevents spider cracking and things like that.”
“There are instances where it is just a minor repair, just dovetailing the crack and then filling,” Gruenke adds.
Luczak says that there are some developments in the technology, but “the basic craft really hasn’t changed. We still use gypsum and cement plaster. “My family used to use animal glues and waxes for mold making, today we use urethane and silicone rubbers, but the basic elements for casting ornament are still the same.”
Digital Details
As with every other industry, digital technology has expanded the capabilities of ornament as well. “There are a lot of things that can be done with computers now,” says Greene, “either to take material off, as with CNC routers, or to create prototypes for molds, or to create the molds themselves.” Not surprisingly, computers have become a tool for scaling plasterwork to new proportions.
“Suppose you have an ornament that is a small prototype and you want to do it at three times the size, you can scale it up by computer, create it with rapid prototyping, such as 3D printing, and then finish it by hand,” he says. “That last part is most critical because, with all of these modern technologies, the challenge is to keep the quality in it.”
Kuryloski describes another use of computers and prototyping to help recreate 18th-century plasterwork that no longer exists. “The architects made 3D scans of ornamental plaster in other buildings they thought were done at the same time and by the same craftsman and from these they made 3D printed models. Although not the right size or of the quality where you could just make molds over them, the models were very faithful to the originals and good for reference.”
Beyond computers, ornament and the decorative arts increasingly benefit from the cross-pollination between different industries. “We recently did a job at Kings Theatre in Brooklyn where we used a spray-on mold technology that came out of the special effects industry in Hollywood,” says Greene. “The idea is to use materials as creatively as possible to express what the designers and architects are trying to achieve.”
From Imagination to Ornamentation
With all these opportunities then, what is the typical process for taking a concept or project to finished ornament? “It depends upon the skill of the architect,” offers Kuryloski. He says they’ve worked with architects who are so adept at, say, designing churches, that when the drawings arrive they are fully detailed. “When you flip through the pages of details and cross-sections it’s like following a road map. You’re almost walking around the building and seeing, ‘OK, I have to look at this here, and this there.’ This way, you begin to break the project down in your mind and, for me, it becomes the way I bid it.”
However, both Kuryloski and Greene agree that this is the exception rather than the rule, and the more common scenario is a dialogue between designer and plasterer. Says Greene, “Frequently, when architects come to us with a new building, they have a very clear idea of what they want, and they will hire us to detail out their drawings to help them realize their idea.” In that capacity, he says they’re also often brought in very early as part of the design team to flesh out mechanical issues, such as whether there’s an internal armature and how is it connected.
“We’re doing a ceiling now in Cleveland where we’re telling the general contractors, ‘Put in these clips or backing boards so we can hang the units.’” This way he says the installation is all conceived ahead of time as opposed to the ornament being an afterthought. “An architect has an idea; he wants to express something. We tell him, ‘Here’s the limitations, and here’s how you overcome those limitations. Here’s how you make it economically viable,’ because all of this pre-planning equals money saved.”
This kind of collaboration can reach its peak in a historical plaster restoration where, while new work, it does not have the benefit of detailed drawings or existing examples, and only the barest historic documentation to work from. Kuryloski describes such a project in restoring the old senate chamber at the Maryland State House. “It was restored on two earlier occasions, in the late 1800s and early 1900s, and the clients wanted it to look the way it did in 1773 when George Washington resigned his commission as general of the Continental Army.”
The touchstone for the project was an 1824 painting by John Trumbull depicting the event and the architecture of the room at that time. “So it was a combination of looking at the painting, very grainy photographs from the latter 1800s, the architect’s interpretation, and our skill and knowledge of the ornamental business.”
He says they went detail by detail, model by model, and rosette by rosette, to first painstakingly sculpt the ornaments out of clay and then have the architects come up and approve them. “We’d go back and forth with photographs until we finally got the look with which everybody was happy. It was not the kind of job where someone could have sat down and drawn it completely to be made it as-drawn; it had to be a collaborative effort.”
“I deal with a lot of architects that really appreciate the craft,” says Luczak, “but we also work with some who aren’t familiar with plaster and we help educate them with information and specification material. There is a preconceived notion that the only plasterers who know how to perform specialized work are 80 years old and from the old country. Most of the plasterers we have trained and work with are younger guys who have a passion for this type of work.”
He adds that when his family started working with plaster in Chicago in 1896, they did mostly new churches and cathedrals. Most of his work now is restoring churches, theaters and new ornamental and flat plaster for high-end residences. “If anything, the interest is historic plaster has been increasing in recent years,” Luczak says. “There is a new appreciation for the craft, and a tendency to preserve and restore as opposed to demolishing and replacing.”
Greene sums it up: “The things that one can do with plaster are not a world, but a whole universe.”
This article was researched and written by Gordon Bock with assistance from Martha McDonald. Bock, co-author of The Vintage House (www.vintagehousebook.com), lists his upcoming seminars, workshops, and keynote addresses at www.gordonbock.com.
Gordon H. Bock is an architectural historian, instructor with the National Preservation Institute, and speaker through www.gordonbock.com.