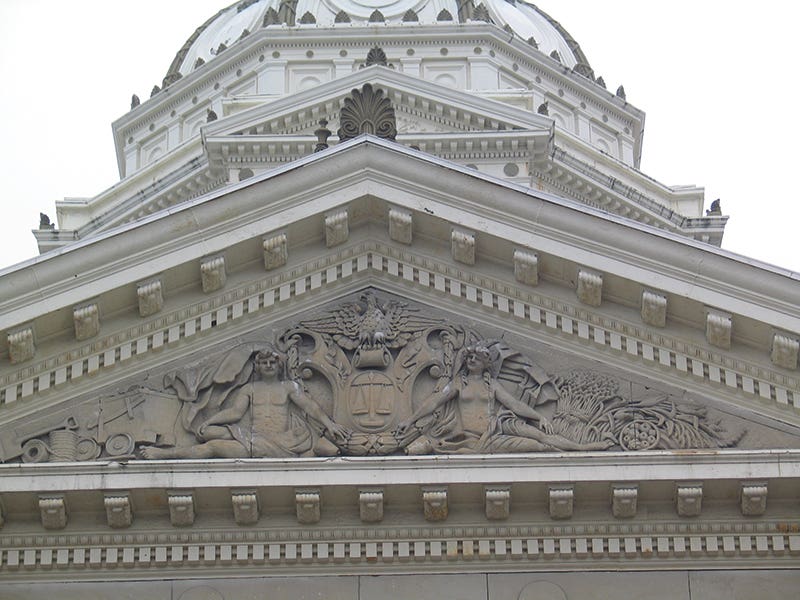
Product Reports
Metalwork Restoration at the Marion County Courthouse
Along with the Boone County Courthouse and the Jefferson County Courthouse, the Marion County Courthouse in downtown Fairmont is regarded as one of the finest examples of Beaux Arts Classicism in West Virginia. It was designed by W.D. Priest of the firm Yost & Packard of Columbus, OH, and built ca. 1900 as testament to Marion County’s status as a center of coal and gas production, and to demonstrate that the county was no longer subordinate to neighboring Clarksburg and Morgantown. The building’s exterior is impressive in scale and detail. Fluted Corinthian columns support massive porticoes and a domed clock tower, and the stone façade is adorned with cast-iron symbols of justice, power, agriculture and industry, including a figure holding the scales of justice, an eagle with outstretched wings, a shovel and a mining car.
The courthouse occupies the corner of Adams and Jefferson streets, in a popular visitors’ area that encompasses the Marion County Museum and the Marion County Military Veterans Plaza. However, by last year, more than a century’s worth of lead paint applications, weather and pollutants had taken their toll on the courthouse’s once-proud exterior. The white epoxy paint had failed in places, leaving areas of surface rust, cracking, checking and coating failure. And, prompted by the building’s visible deterioration, the State Historic Preservation Office carried out a survey that revealed structural failures in the roof and drainage systems.
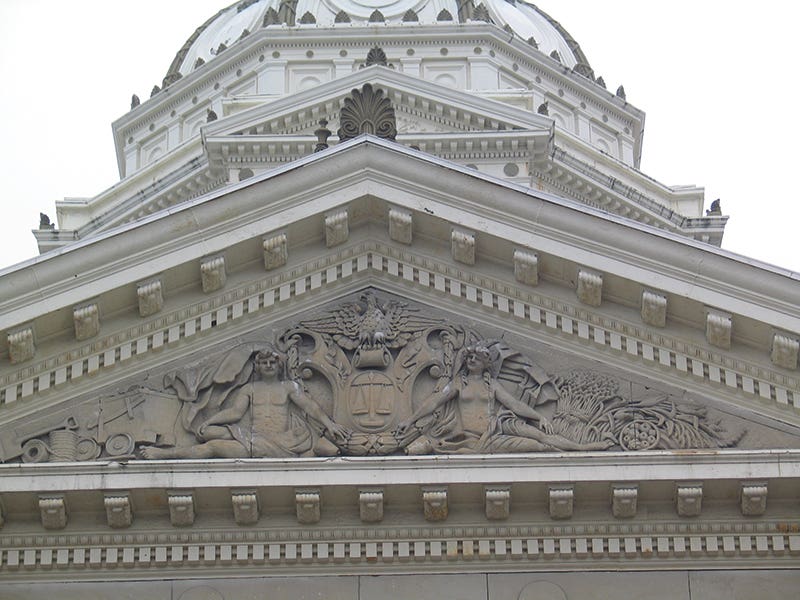
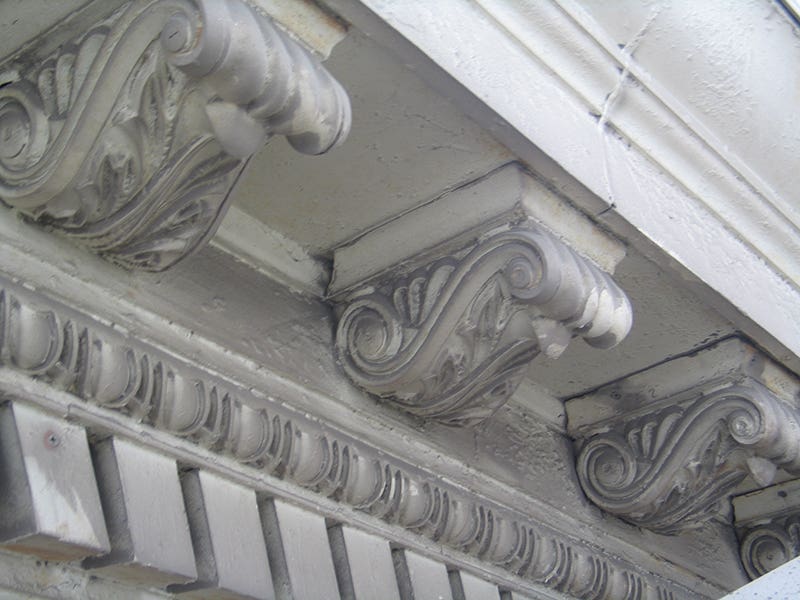
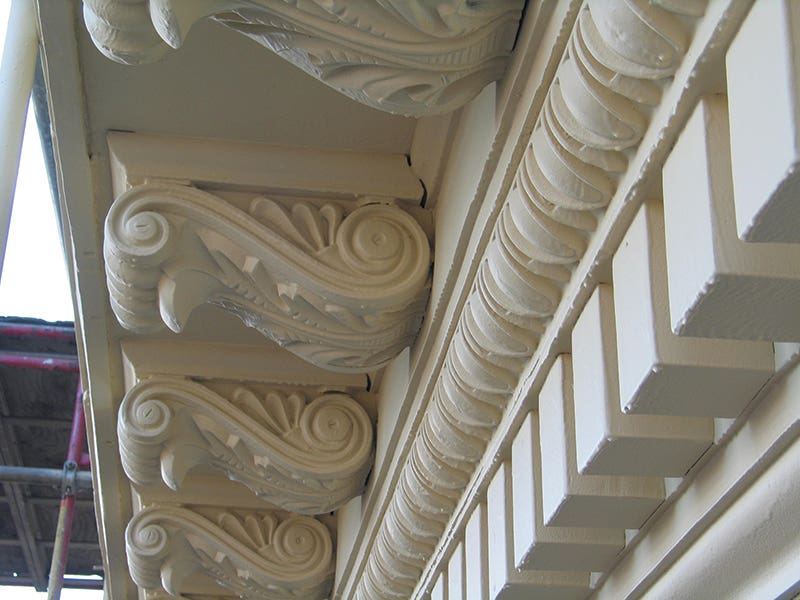
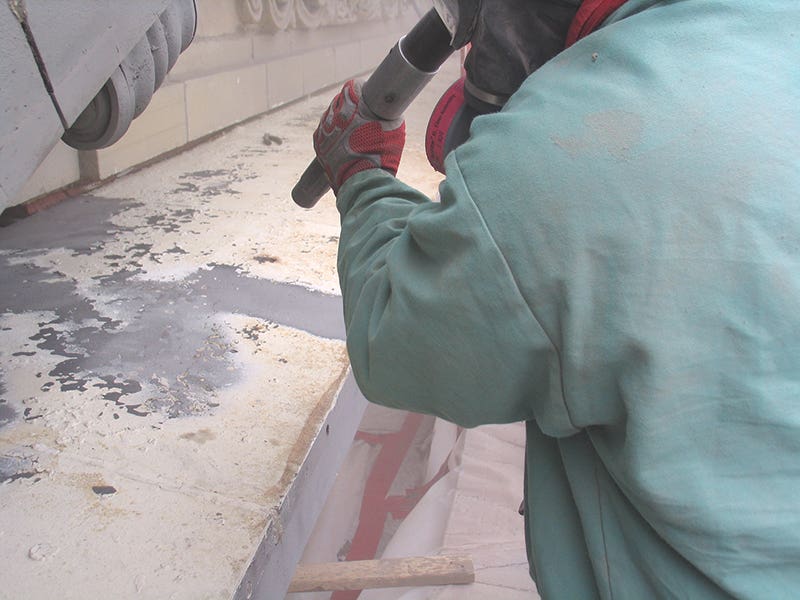
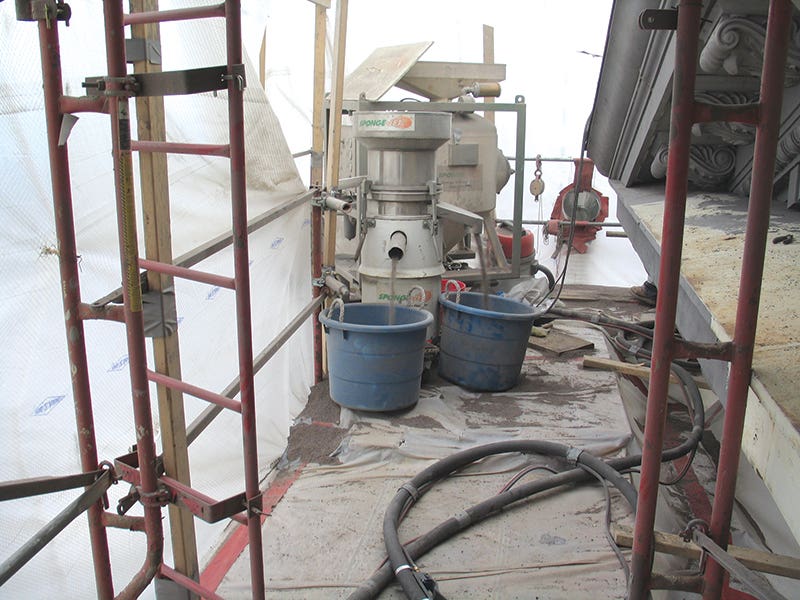
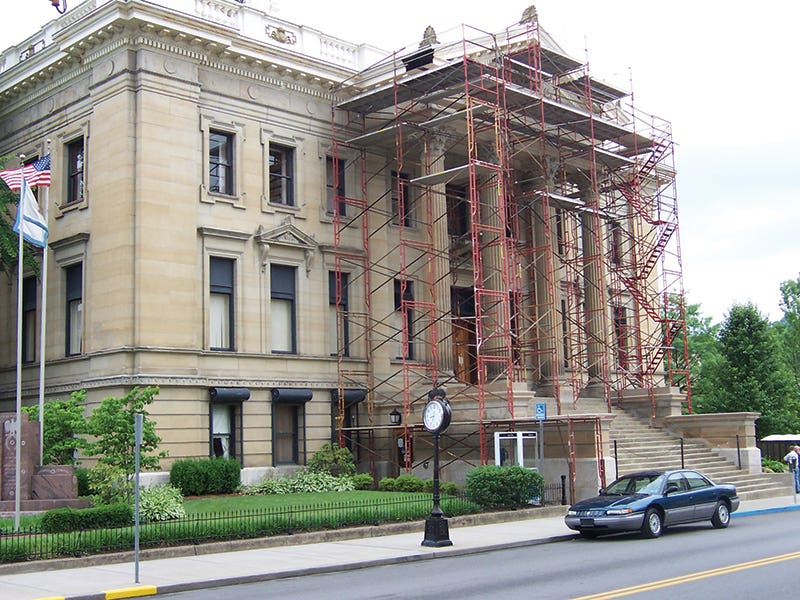
Aided by a grant from the State Historic Preservation Office, the Marion County Commission enlisted Powe Jones Architects of Washington, DC, to begin the courthouse’s phased restoration. The firm’s preservation director, David Kemnitzer, was more than qualified for the job, having preserved several federal government buildings in the nation’s capital. Phase one, completed in the fall of last year, addressed Marion County Courthouse’s poor appearance with the restoration, surface preparation and painting of the cast-iron architectural details surrounding its tympanum.
Earlier repairs with concrete had prevented the cast iron from flexing properly, which in turn had caused cracks and corrosion. The first task for general contractor G.A. Brown & Son was to re-anchor the cornices and modillions to the façade, removing the risk to the public. “The building was extremely well-built, but it had not been well-maintained and there was a lot of damage to the structural cast iron, up high on the building,” says Kemnitzer. “The cracks were allowing moisture to get in, and the resulting corrosion was causing the anchors to lose their structural strength. Nobody had been injured, but it was a very precarious situation.”
Once secured, the cast-iron elements were cleaned and repainted. The goal – to remove multiple layers of lead-based paint without causing appreciable damage, or falling foul of EPA and OSHA requirements – posed significant challenges for conventional cleaning methods. Technologies such as sandblasting, high-pressure water cleaning, chemical cleaners and paint removers have been found to reduce the ability of the cleaned surface to resist water and frost, as well as producing by-products that are both difficult to dispose of and damaging to the environment. “We had lead-based paint, and we were working in a downtown area,” says Kemnitzer. “We really couldn’t spread lead dust all over the town, so we had to keep it contained.”
Sponge-jet cleaning, a dry alternative to conventional abrasives, first came to Kemnitzer’s attention in 2003. Developed in the late 1980s, it combines a recyclable sponge-like polymer with conventional abrasive grit, in a range of particle sizes for aggressive or clean-only applications. Although most conventional abrasives can be engineered into sponge media, the most commonly used types are aluminum oxide, metal grit, calcium carbonate, 40-60 mesh type III melamine, 30/40 and mesh type II plastic urea. The sponge particles are fired at the surface, where they flatten on impact, exposing banded abrasives and dislodging contaminants. After dropping from the surface, the sponges regain their original shape. A vacuum system recovers the sponges, transports them to a machine that removes contaminants, and then reloads them for almost continuous blasting, all within feet of the treated surface.
The Sponge-Jet system had been successfully applied in the masonry restorations of the Wisconsin and Idaho state capitols, returning the white-granite facades to their original condition. And with no run-off, low dust emissions and, in some applications, only 3% of the waste generated by conventional abrasives, it fit the criteria for the cast iron at the Marion County Courthouse. “I read a lot of the literature and it seemed to be ideal,” says Kemnitzer. “It had the advantage of keeping all of that lead contained. And they had worked out a process for cleaning the lead out of the sponge and then reusing the sponge. So we could get up there and remove the lead completely, and very easily.”
Prior to the restoration, the white epoxy paint on the cast-iron elements had clashed with the stone façade. But this wasn’t always the case, as originally the cast iron had been painted to complement the stone. Finding a match had proven so difficult over the years that the city had abandoned the idea, but after achieving bare metal, the firm took the opportunity to correct this with a tan color that is a little lighter than the exterior’s Ohio brown sandstone. “The building didn’t look right before,” says Kemnitzer. “The color that we chose is deliberately lighter than the stone – that helps make the transition to the sky and lighten the top of the building. It looks a lot better than it did before and I’m very happy with the result.”
The phased restoration of Marion County Courthouse will continue as funding is released by the State Historic Preservation Office. Kemnitzer estimates that repairs to the dome, clock tower and balustrade could keep the firm busy for 10 years or more. ”There’s a lot more work to be done there,” he says. “They deferred maintenance for many, many decades. We don’t know exactly what’s coming next, but we’re making good progress.”
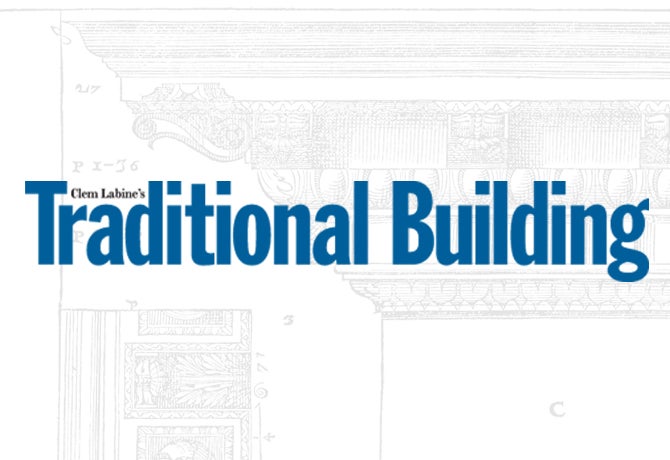