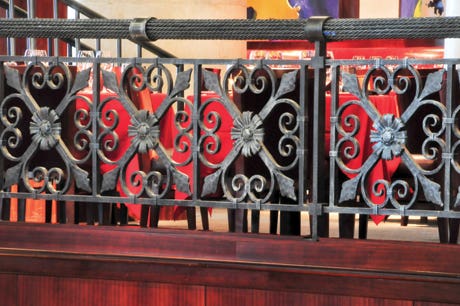
Product Reports
Metalwork for Historic Buildings
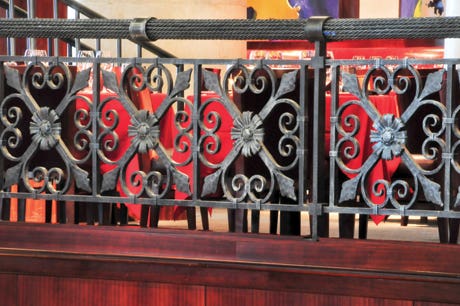
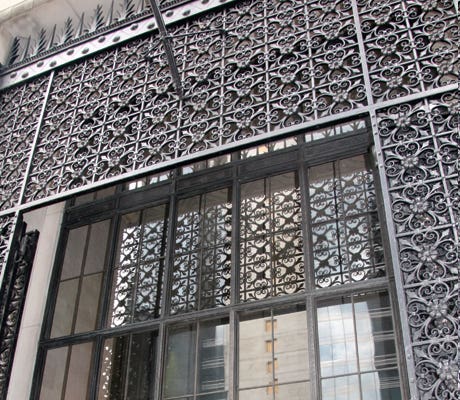
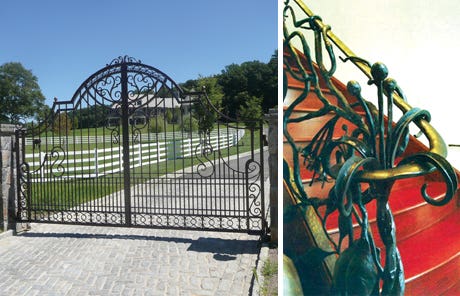
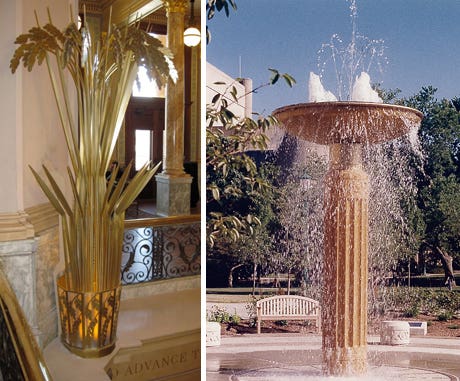
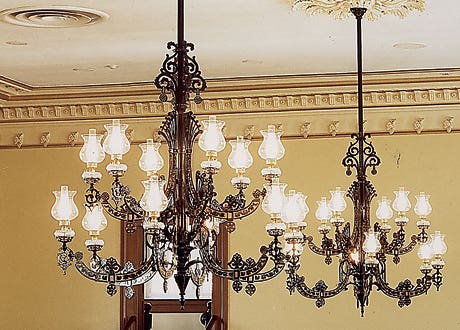
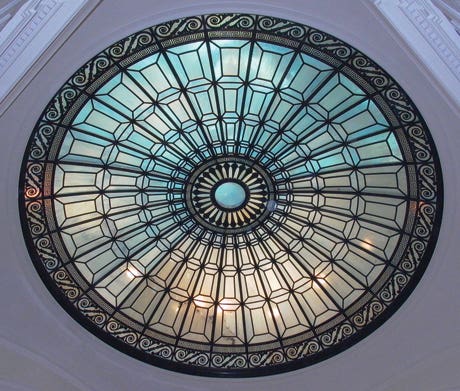
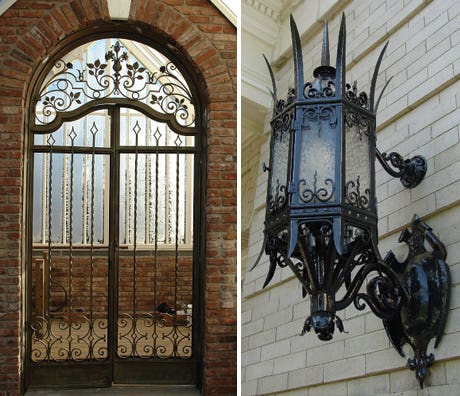

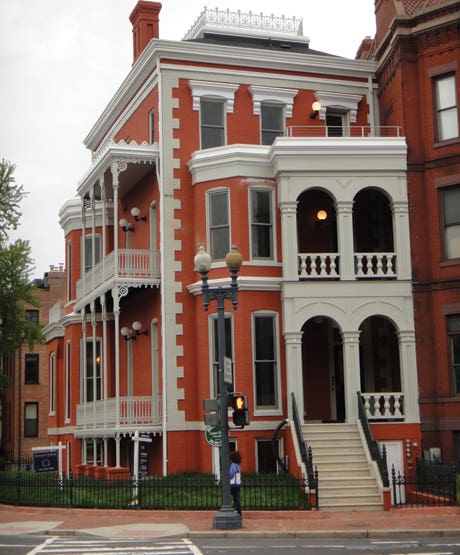
Knowledgeable suppliers explain that custom historic metalwork is worth the time and effort, and will stand the test of time.
By Gordon Bock
From one-of-a-kind, hand-hammered forgings to identical reproduction castings, custom ironwork is among the oldest architectural arts, with skills, materials and traditions that go back centuries. Elemental as it is, ironwork fabrication has always had intangible dimensions, such as designing and scheduling – aspects no less important in today's virtual world of digital spreadsheets and cellphone cameras. So if you're looking to commission ironwork for an upcoming project, consider following points and that there's more to ironwork than meets the eye.
It goes without saying that custom-fabricated ironwork does not flow from off-the-shelf inventory or just-in-time production, so accounting for adequate lead time is an important part of planning. According to Douglas Bracken, president of Wiemann Metalcraft in Tulsa, OK, "The match between shop and project is critical; it comes down to how much labor the shop has available compared to the project demands." In his market, Bracken says the lead times vary widely and depend upon the size and complexity of the project. Small, one-off orders can be handled in a matter of weeks, while larger, more complex orders may need a year or more.
Robert Baird, vice president of operations at Historical Arts & Casting, Inc. in West Jordan, UT, has a similar take. "It depends upon how custom the project is, how involved the design, and what kind of production process is involved." Lead time can also be influenced by the scope of the project and the kind of finish that is desired. He adds that, "Replicating an existing historic element sometimes requires less lead time because you're working from an example, while creating something new involves the design phase, as well as fabricating a sample – all of which takes time."
Another part of the equation is that each ironworks has its own vendors with their lead times. Baird says that for his business, sourcing different metals is not much of an issue but offbeat shapes can be. "We maintain an inventory of our most commonly used extrusions – say for windows and railings" he says, "but special-order shapes may take 16 to 20 weeks to acquire, especially if they're coming from offshore."
Bill Mogavero of Bill's Custom Metal Fabrications in Westbury, NY, says that in his business lead times are hard to generalize and must be evaluated on a job-by-job basis. "Otherwise straightforward work," he explains, "can be delayed by the approval process as it moves through one or more parties."
At Lodi Welding Company, Inc, in Hackettstown, NJ, Richard Buschgans says, "Even though we have work a year out, we're always looking for new and exciting projects."
Putting Numbers Together
Another ironwork intangible is sizing up the cost of a project – ever an issue in building construction but, again, not so simple as totaling up materials. "A lot is job-sensitive," says, Mogavero, "but materials are not really where the costs are; they're in time and labor." Bracken concurs. "In ornamental ironwork and blacksmithing, fabrication doesn't take a lot of specialized or expensive tooling," he says, "and the raw material expense, especially if it is mainly carbon steel, is often quite low. However, it does take a lot of time, so the majority of the job cost is labor."
He adds that there is also a significant portion of that time taken up by activities essential to producing ironwork, but not directly connected with working metal, such as creating drawings, measuring at the work sites, and even loading or unloading trucks. Thus, as a percentage of the whole, smaller projects will have a larger burden of cost devoted to these "non-productive" but essential labor expenses.
Bracken stresses that experience is key. "Estimating repair and refurbishing is even more difficult, because there are so many unknowns for both the tradesman and the architect," he says, "The more experienced the tradesman or fabricator, the more accurate the estimate is likely to be, but as anyone who has worked on old buildings will tell you, there are surprises every day."
Buschgans' company is known for high-quality forged works (interior and exterior handrails and grand gate entrances), but he adds that with repairs and restorations there's often an investment before you can even begin the pencil work. "First, a historic fence or gate has to be broken down into pieces, into its constituent parts, then these parts must be stripped down to bare metal." Not until then, he says, is it possible to know what the conditions are and what metals are present, which in historic work may be some cast iron, some wrought iron, some steel, and even non-ferrous metals such as brass. "Ironwork restoration is like car restoration," he says, "You can do a little, or you can do a lot."
According to Jeff Schiff, owner of Schiff Architectural Details in Chelsea, MA, when someone presents an old photo asking "Can you make this?" his reaction is often, "The short answer is yes, but first let's have a serious discussion about budgets." Then he says the conversation proceeds in part to ascertain whether they have "the resources to achieve their desires."
Schiff says they do a lot of conditions and maintenance reports for local municipalities or institutions like Harvard that have miles of fencing that, due to historic designations, have to be kept up, rather than abandoned if deteriorated. "It all comes down to linear footage in the end," he says, but the project also has to be broken down into its elements to determine unit costs "before you can do an intelligent bid."
Another aspect of repair influencing costs is the location of the work. As Bracken points out, "Whenever possible, it is always better to remove repair or restoration work to the shop where it can be executed in a safer, more efficient, and controlled environment." This is especially true, he says, if the metalwork is fine or delicate, requires a specialized finish that cannot be applied confidently on-site, or the conditions are such that they make field work dangerous or very slow. For these reasons, "There's a point of diminishing returns for working in the field," he adds.
That is not to say that historic ironwork restoration or refurbishing projects are inexorably more complicated or costlier than new work. Indeed just the opposite can be true. For example, Schiff tells of a recent project where his company met with clients about to replace a 20-story spiral staircase made of cast iron and fabricated steel parts. After much discussion the company finally convinced the house architect that they should instead refurbish the existing ironwork. "We replaced some parts, upgraded others with stainless steel," says Schiff, "and, in the end, saved the client a great deal of money; they couldn't believe it."
Forging the Future
Historic ironwork from the 1830s is often partly or wholly cast iron, meaning that repairs can involve tooling – that is making the patterns and molds to reproduce lost parts. Buschgans says that for casting small parts in limited quantities, Lodi does their own foundry work, but for large items or numbers, it's more cost-effective to farm the part out to a larger foundry (though these are increasingly difficult to find). "It's a matter of volume and heat," he says, "of being able to handle larger quantities of molten iron."
He also notes that there has to be the right match between castings and customer. For example, a historic building might value authenticity enough to justify the cost of reproduction castings, but a homeowner may not always feel the same way. "Casting new parts has to pay for itself, so to speak," he says.
Schiff says that part of his company's work is casting authentic cast-iron fencing used in several Boston-area communities and parks. Besides using authentic patterns made from original artifacts, he says they strive to upgrade what has already proved successful for decades. For example, they pour castings in ductile iron, which is stronger and lasts longer than the grey iron typically used in the past, and they assemble parts with stainless steel fasteners. "Why repeat the mistakes of the past?" says Schiff, "And there were indeed mistakes."
Between commissions, Schiff Architectural Details is also the stewards of the tooling. "These patterns are legacy tools for the neighborhoods," explains Schiff, "and with two to three patterns costing about $70,000 a set to make, they need to be protected in curated storage until the next use." Well intentioned as they may be, municipalities typically cannot offer more than a damp garage where moisture and forgetfulness take their toll.
At Historical Arts & Casting, Baird describes a similar practice. "All pattern and tooling costs are inherent in the price of the project, and assigned to the client," he says, adding that, "We also own all the tooling." Such an arrangement actually makes sense for a client, because properly storing patterns until the next use – which may be years in the future – is an ongoing cost. "Is storage cost-effective for the client, or are they equipped to assume this responsibility?"
In fact, one of the least-appreciated characteristics of custom ironwork is that it is all about longevity and the future. This perspective applies to maintenance and restoration as much as it does to new work. "It seems every 100 years, wrought-iron work has to be restored," observes Buschgans. "It depends upon the project of course, but a lot of the jobs that come our way are about a century old." He adds, "If the ironwork is 120 years old, it's sometimes almost beyond repair, where you're replacing two-thirds of the metal."
Schiff concurs, adding that 100 years is not just a benchmark for major maintenance. "New work should be looked at with that kind of life-span," he advises. "Hot-dip galvanizing is the best money you can spend – it's readily available and there are good practitioners. Also invest in a triple-coat paint job."
Mogavero tells of restoring many a fence and railing of similar vintage, such as urban stoop railings with cast-iron newels. "You first remove all the broken parts, then weld and cast," he says, noting that he does a lot of heavy forge work, sometimes for competitors who don't have the time or ability to fulfill the order.
Bracken too believes that traditional ironwork is a long-haul material, and is directly associated with the alloys used. He cites a churchyard in his area with true, low-carbon, wrought-iron fencing from the 1880s. Though in need of restoration – "Miles of cemetery fencing do not normally get a lot of maintenance," he quips – it is nonetheless still standing because true wrought iron is very resistant to corrosion.
However, he adds that, "If this same fence were installed using carbon steel, and not wrought iron, it probably would have already been replaced three or four times during the last 120 years because, left unmaintained, steel starts to dissolve immediately."
Bracken adds that while the tubular steel fences common today are very inexpensive, they're closer to a wood fence in terms of longevity. "We wouldn't have any historic ironwork to celebrate in cities like New Orleans and San Francisco," he says, "if it weren't for the corrosion-resistant properties of cast iron and true wrought iron."
Gordon Bock is the co-author of The Vintage House (www.vintagehousebook.com) and lists his 2013 seminars, courses and lectures at www.gordonbock.com.