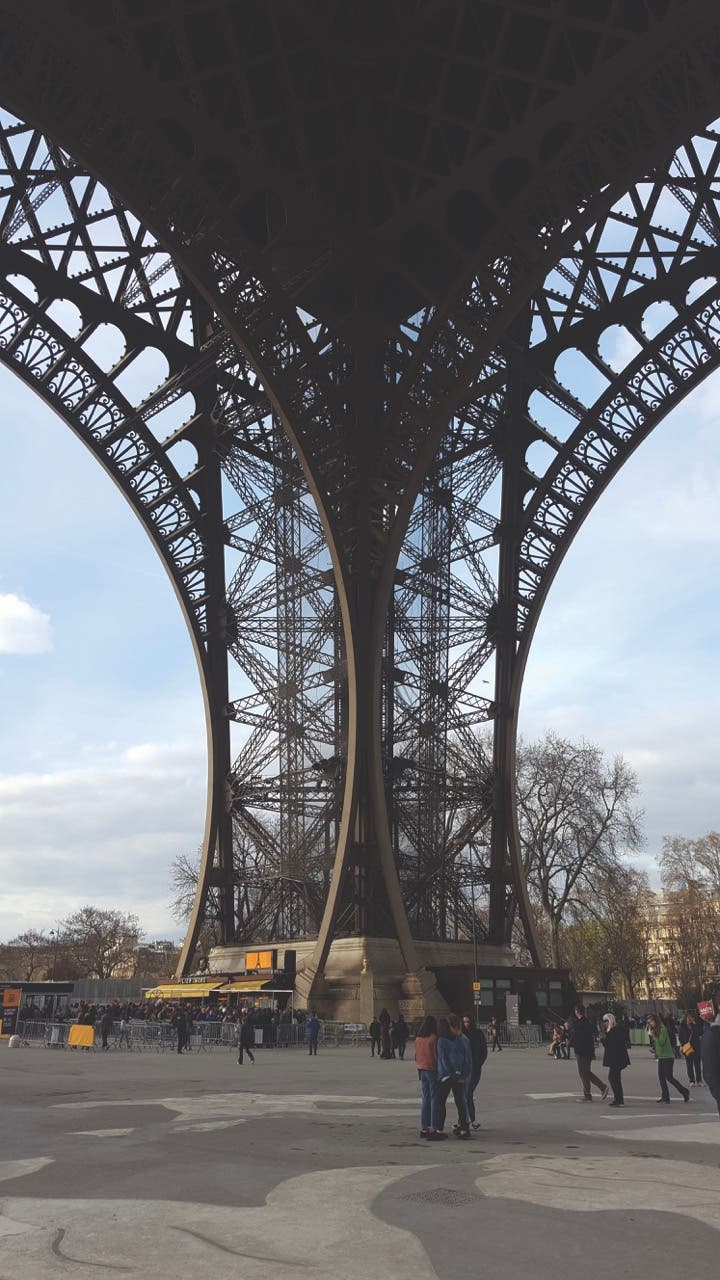
Product Reports
Iron Age
Not all black metal is wrought iron. Wrought iron is iron that is heated and worked repeatedly with tools to make desired shapes. Composed primarily of pure iron (Fe), there is typically minute quantities of slag, consisting of silicon, phosphorous, and aluminum oxides, included in the material. It is a malleable material, made stronger the more it is worked by heating and hammering.
While cast iron is predominantly pure iron, it has 2 to 4 percent added carbon, along with silicon and manganese, and some impurities. It achieves its form by pouring melted iron into a mold and cooling it to a solid state. The resulting cast maintains its original size. While cast iron is very strong in compression, it has a microstructure caused by the carbon, leaving it very brittle. While steel is on the rise for casting, cast iron achieves sharper detail, melts at a lower temperature, and doesn’t react with molds.
Ductile iron is similar to cast iron but has added cerium (Ce), which provides the ductility to resist cracking. Ductile iron provides the same fine detail in casting without shrinking. With heat treatment (austempering), it can achieve even more strength.

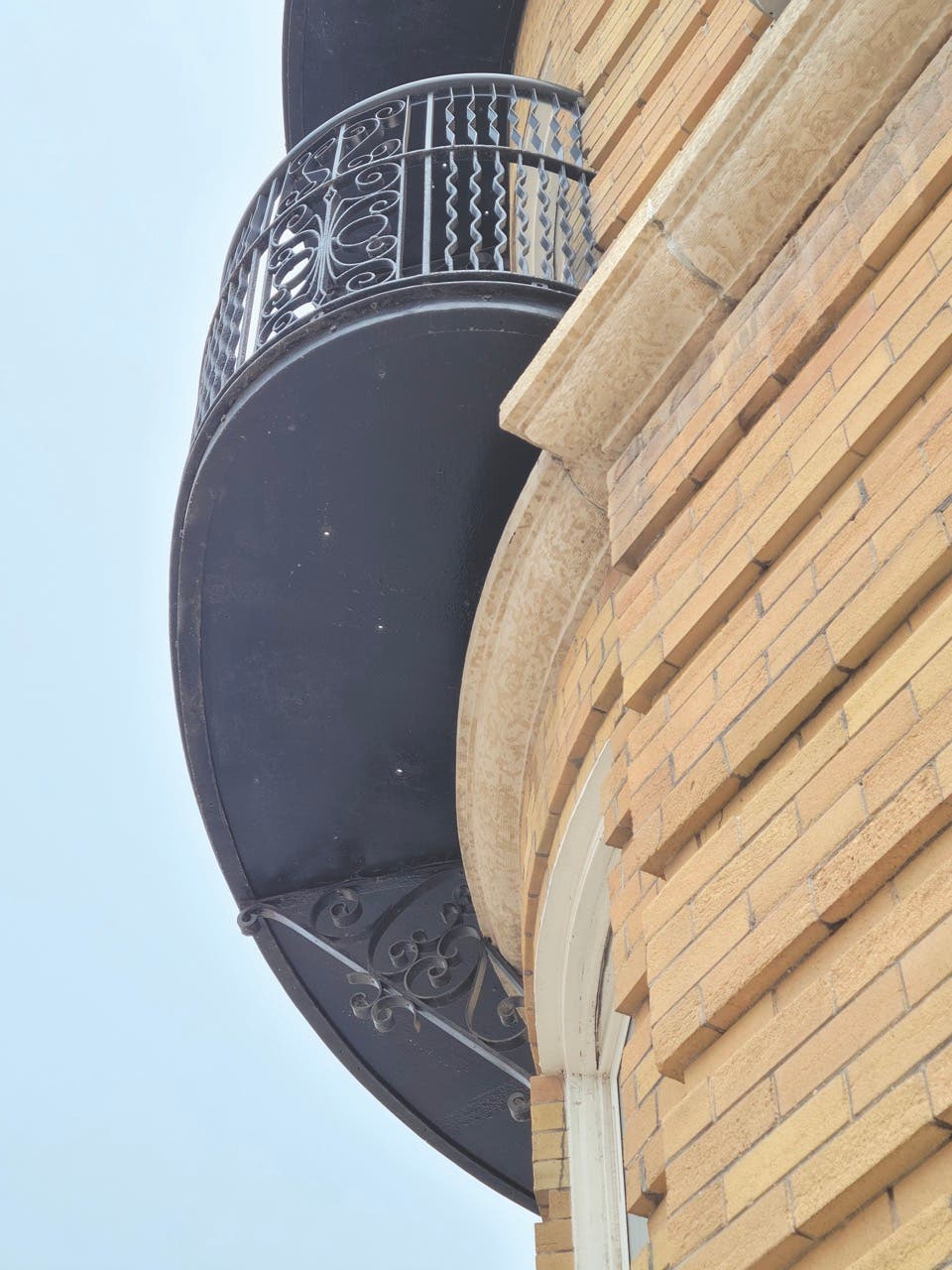
This article will focus on wrought iron, with attention to minimum intervention into historic fabric. The approach to wrought iron restoration projects should include:
Assessment: visual inspection of the ironwork condition, generating drawings for recordation, and a search for maker’s marks
Analysis: determining the causes of the deterioration documented, performing paint chronology to understand what the finish should be, and cleaning tests to determine what method would best serve the project
Research: investigating archives and the property’s records to find historic evidence of the original design and construction
Approach: once the scope is understood, determining how best to perform the repairs—in-situ or off site
Repair methodology: developing final drawings and specifications that incorporate all the information gathered from previous steps, to provide a scope of work document to bid
Bidding: investigate which contractors have a proven track record for the type and scope of repairs for the project being undertaken, and only accept bids from qualified contractors
History
Archaeology has revealed worked iron fragments dating as early as 2000 BC in the Anatolia Peninsula in present-day Turkey. The start of the European Bronze Age ushered in the production of iron of any significant scale. Iron was not smelted in North America until its settlement by Europeans.
A good example of a structural application with iron is the Eiffel Tower, completed in 1889 and fabricated with puddle iron, an early type of wrought iron invented by Henry Cort in 1784. With the advent of the Bessemer Converter in 1850, steel became structural and was used for railroads. In the U.S., the first rolled wrought iron beam was fabricated in 1854 by the Trent Iron Works. The structural capacities for wrought iron shapes were first published in a table in 1873 by Carnegie Kloman and Co. Iron bars are still available, but are not mass-produced, since other methods and materials have become more economical since the 1900s.
Wrought iron was used at all different scales, from nails, fences, gates, rainwater hoppers, and weathervanes, to balconies, bridges, girders, and bow-string trusses. It weathers well, if properly maintained. Failure occurs through these mechanisms:
- Corrosion due to air and moisture: at joints, fissures in paint coverage, failed lead in the stone pocket, vegetation, and galvanic action with dissimilar metals
- Mechanical action, such as rubbing or impact
- Failures of the original design
- Vandalism
Given iron’s susceptibility to environmental exposure, it is important to keep it iron coated, be that with paint or powder coating. Wrought iron doesn’t form a protective oxidation layer; it continues to deteriorate until there is nothing left.
Both cast and wrought iron corrode with exposure to air and moisture. This is problematic, given its prevalent use in exterior environments. When iron is wrought, a grain is introduced into the microstructure of the material. While working the iron distributes the impurities throughout the body of the material and increases the strength, it also creates layers. As the iron is exposed to air and moisture, the iron oxidizes, bonding with 1.33 to 1.5 oxygen atoms per iron atom. Oxidation occurs along the surface of the member, and forms along the exposed edges of the laminations, causing the iron to corrode in layers. Iron oxide occupies between 7 and 11 times the volume of the original component, which can lead to “rust jacking,” where expanding corroded iron that is engaged in masonry or stone causes the substrate to crack.
Maintenance First!
To prevent the need for repairs, it is important to perform regular maintenance of wrought iron. The ironwork should be cleaned annually with water and a cloth or natural bristle brush. This removes deposits of dirt that retain moisture on the surface, which can lead to infiltration through the coating’s minute fissures. Inspect the paint coverage of wrought iron. Where chips or nicks are encountered, touch up the paint in kind.
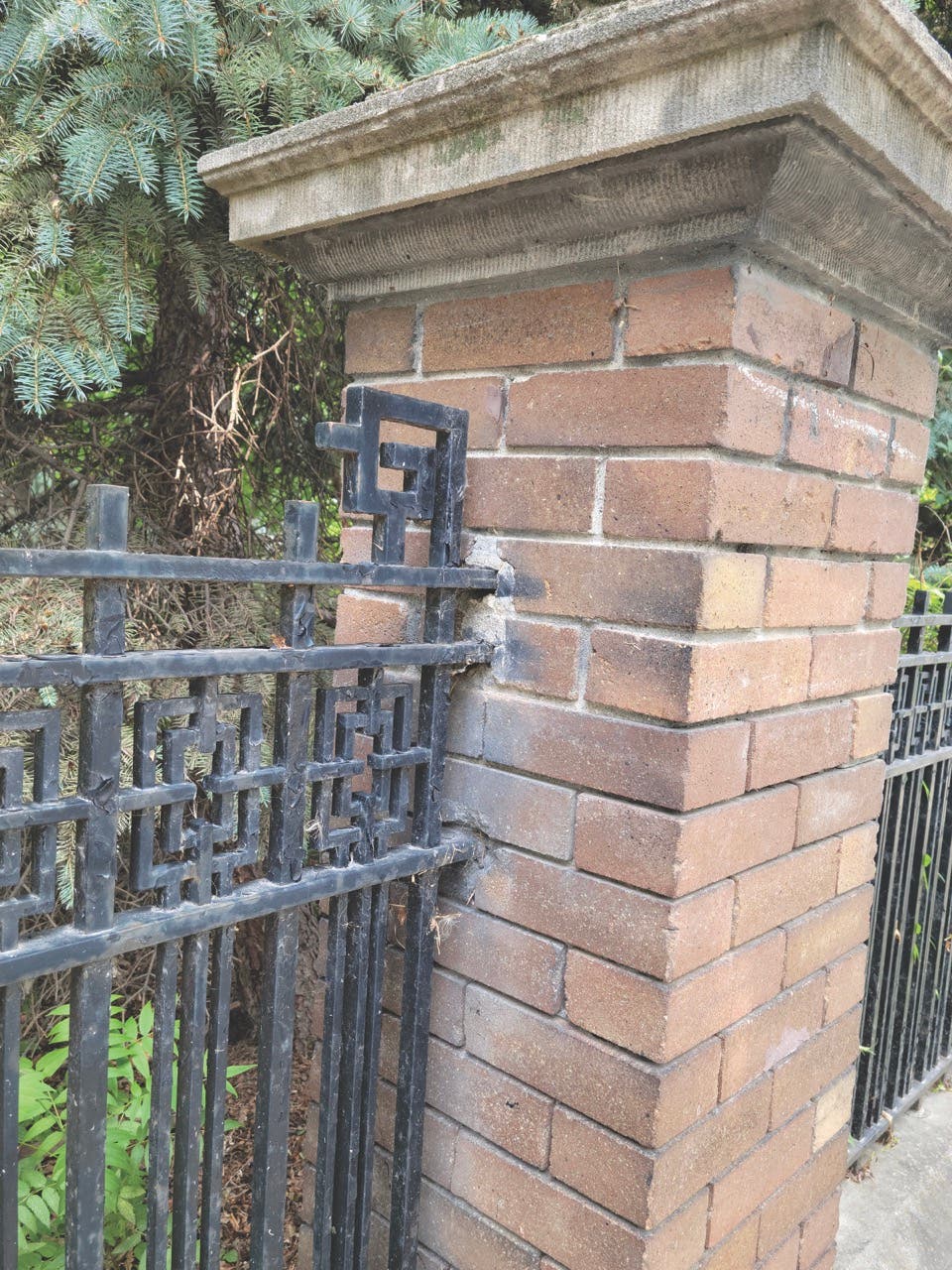

Repairs
When fabricating replacement parts, ensure that historical research is completed. Knowing the most about the building will inform everything from paint colors to determining if missing parts were intentional or the result of a historic event. Analyze the failure being repaired. What is causing the symptom? Once the cause is identified and eliminated or mitigated, the repair of the symptom can commence.
Wrought iron should be repainted about every five years. Whether touching up or a full repair campaign, areas of corrosion should be removed down to bare metal before priming and painting. Most original paint of wrought iron will contain lead; ensure precautions suitable to the cleaning method are taken.
Cleaning methods are ideally dry. It is important to note that wrought iron is frequently produced with a “mill scale” which protects the substrate. Aggressive cleaning should be avoided to prevent removal of this finish or unique historic tool marks. Cleaning methods should be tested, starting with the gentlest method possible, working up to stronger methods. Use the gentlest method that is effective. Cleaning tests should be performed in advance of bidding to provide a comprehensive cleaning specification to obtain consistent bids.
For small areas of repainting, manual cleaning is the most cost effective. Using a chisel, a wire brush, and sandpaper is effective, provided care is taken to avoid nicking or scoring of the substrate. Hand tools, including grinders and rotary brushes, are effective for larger-scale corrosion removal, but mock-ups of the work by each craftsman using these tools is needed to ensure they understand the desired cleaning result. Removal of paint by heat gun or flame is possible. This method should only be used outside, away from all combustible materials, and with precautions for fire prevention. Chemical cleaning, including acid cleaning, while effective, is not recommended. The chemicals can get into the joints between elements, causing corrosion. Rinsing may remove chemicals from the surface but will not remove the residual chemicals hiding in crevices. Further, liquid trapped in crevices can freeze, causing ice jacking in these small spaces, causing further damage. Blast cleaning is a dry method and provides a variety of pressures and materials to be applied. Low pressure rotational vortex cleaning is safe and effective, while higher-pressure sand blasting is not desirable. Blast mediums can range from crushed walnut shells, inert minerals, glass or plastic pellets, and dry ice. Anything containing silica should not be used, as this is identified as an extreme health risk. Ideally blast cleaning should be performed in a shop, if feasible. However, it can be performed on site, provided the building, the surrounding landscape, cars, and pedestrians are protected by dust-proof barriers that contain the media.
If entirely repainting the wrought iron, it is advised to perform a color chronology test. This takes a small section of paint through all the paint layers, down to the substrate. When viewed under a microscope, exact colors of previous color schemes can be documented, to determine the original paint—or any metal leaf—that was applied.
When fully repainting, a three-coat coating system with some flexibility in the dried paint should be used. Each layer should have a minimum dry film thickness (DFT) of 250 microns or more. The base coat should be a zinc-rich primer, followed by a ties coat, then the topcoat. Use contrasting colors each layer, for example orange over the base metal, white over that, and then the black; this will assist in visual inspection of the paint, revealing any gaps in coverage by a previous layer. Where the existing wrought iron has gaps, pock marks, or poor joints, they can be filled using red lead paste, or, if not available, a polysulphide mastic prior to painting.
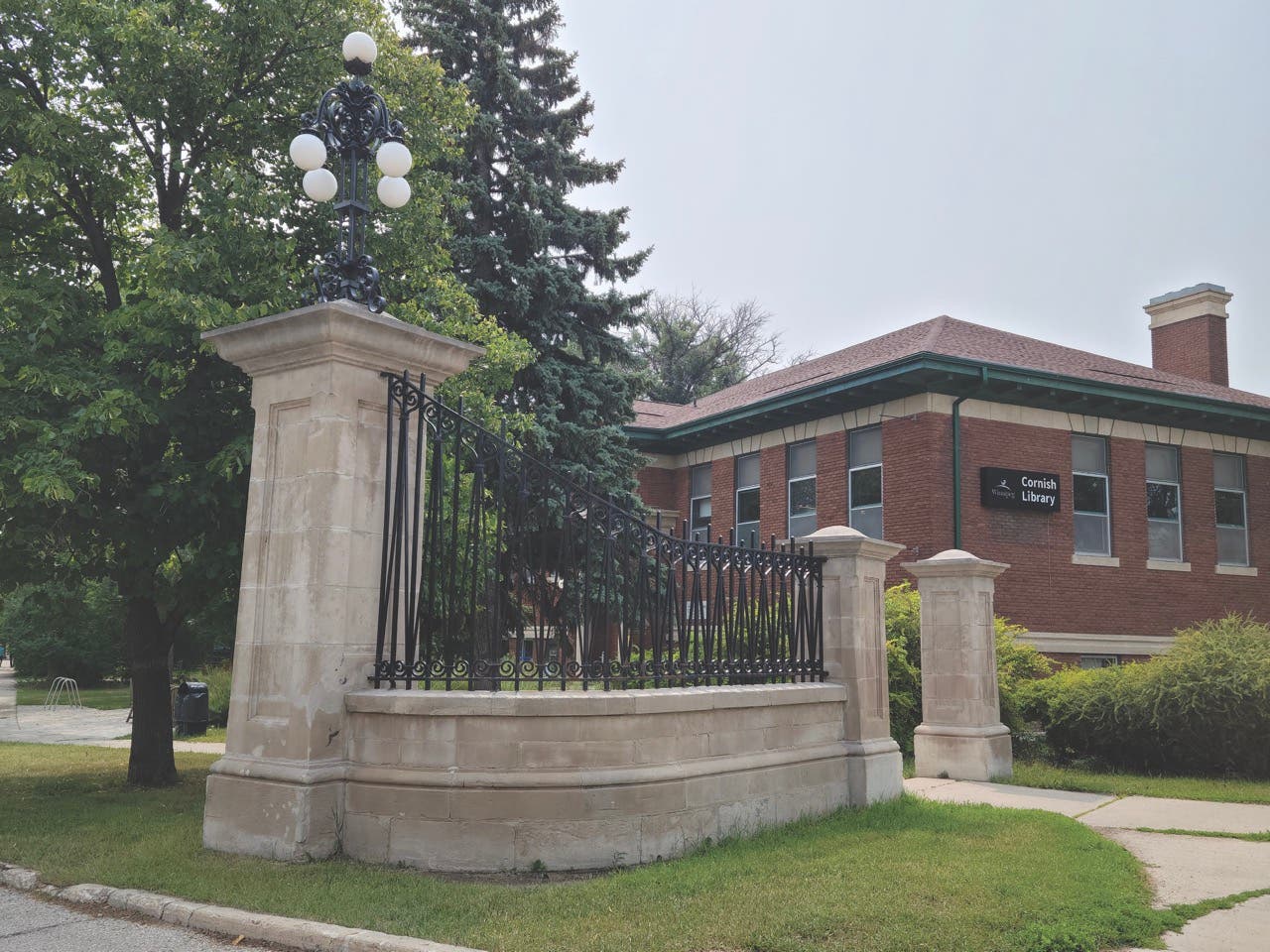
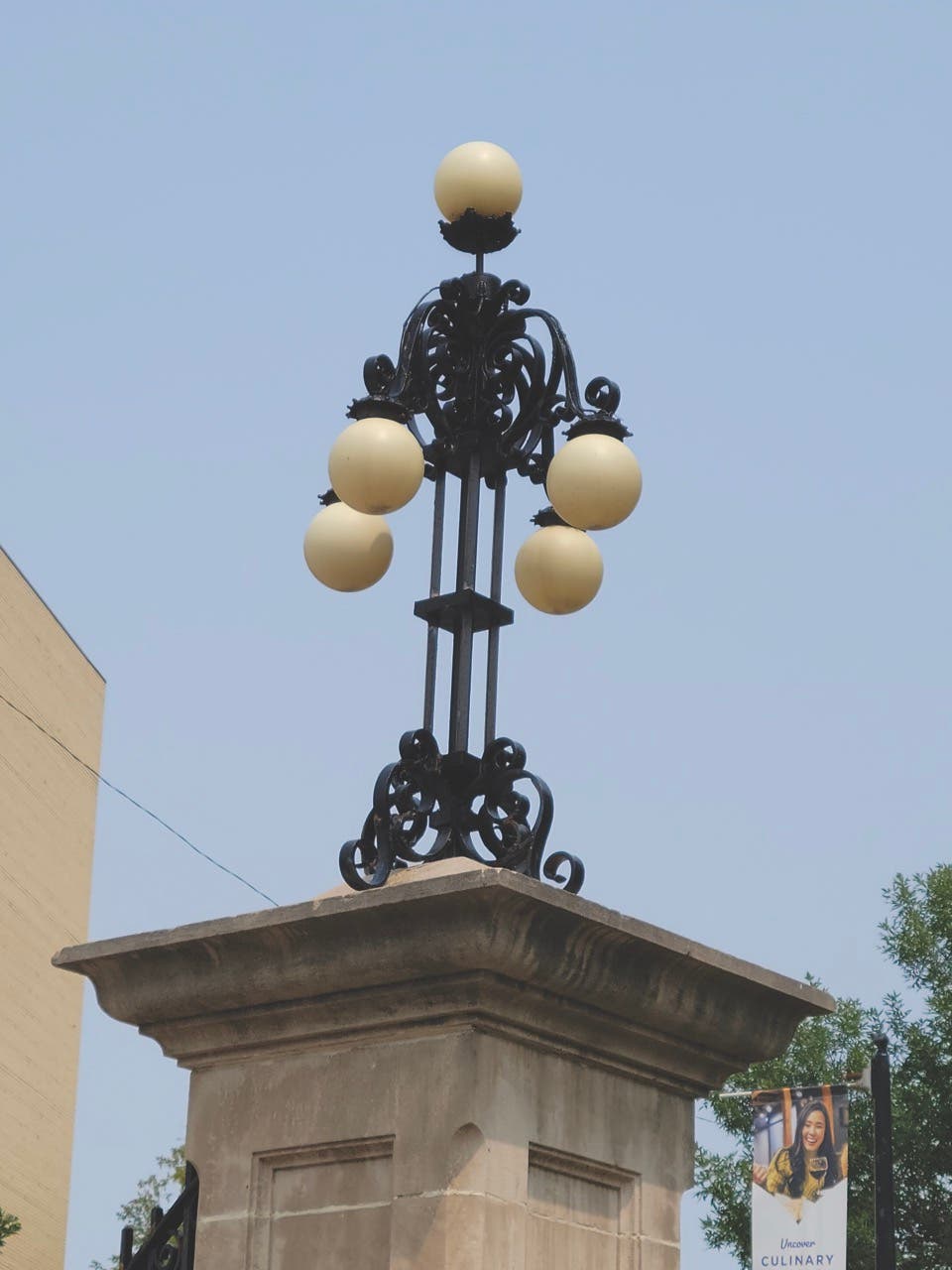
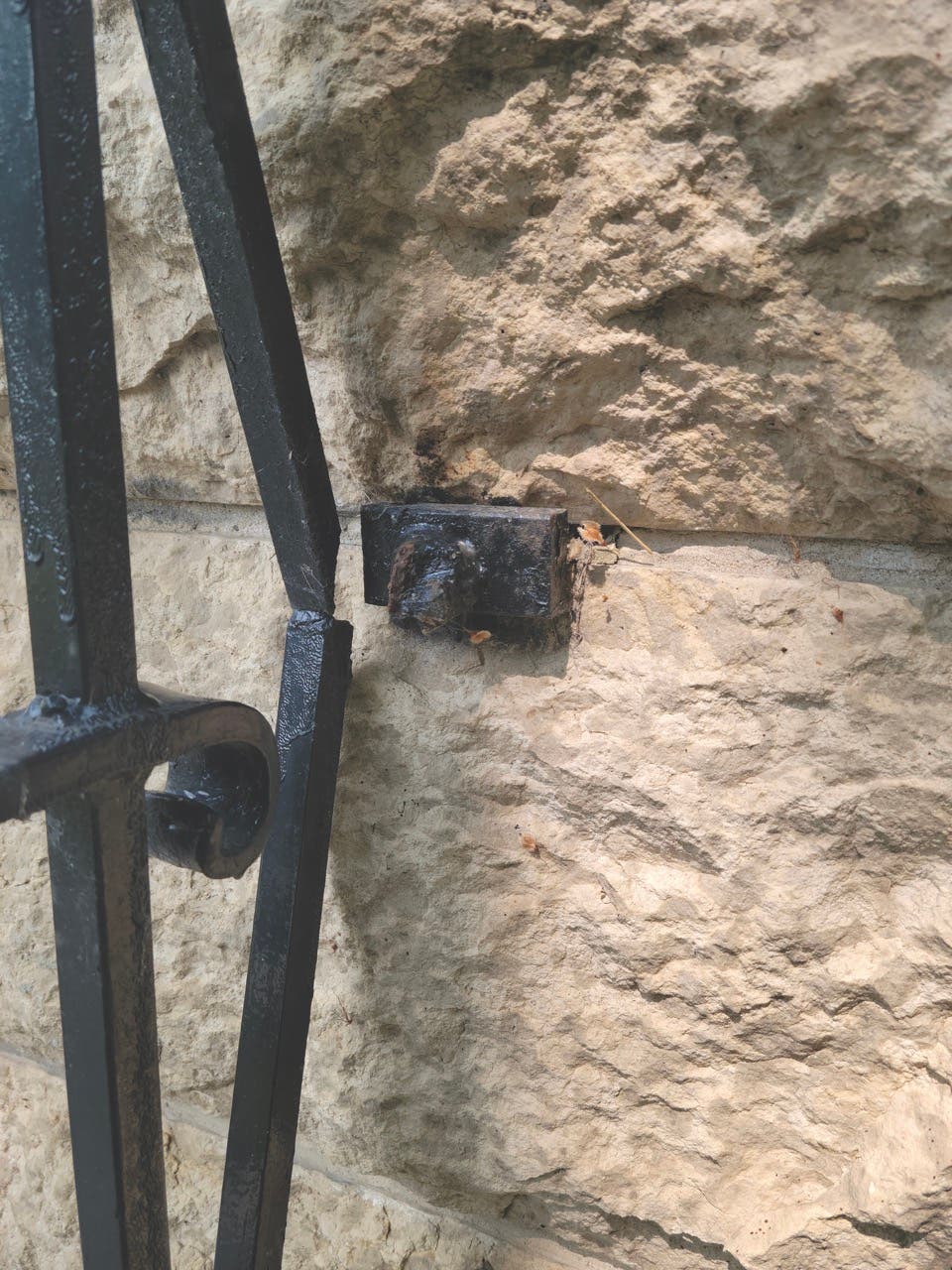
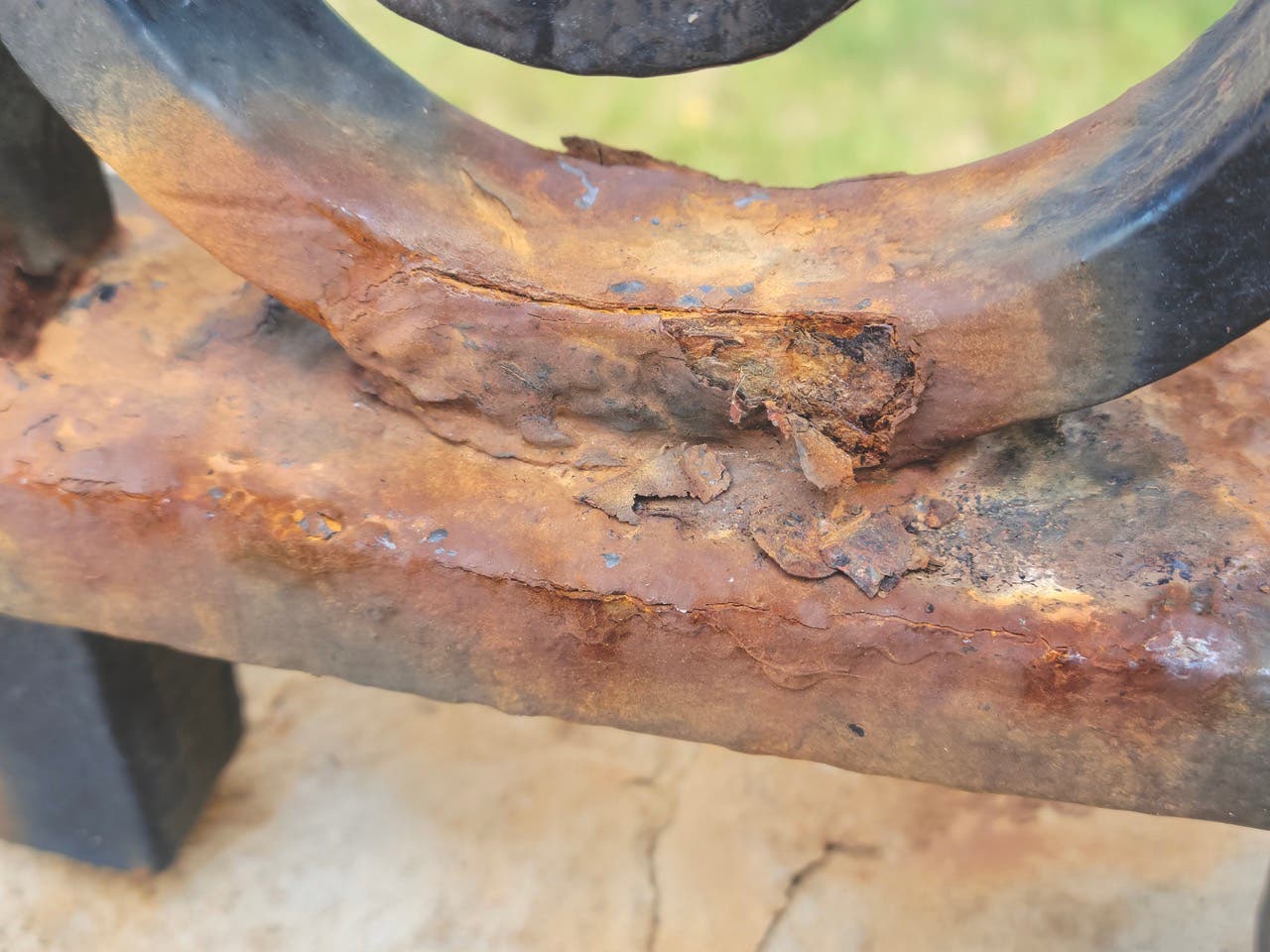
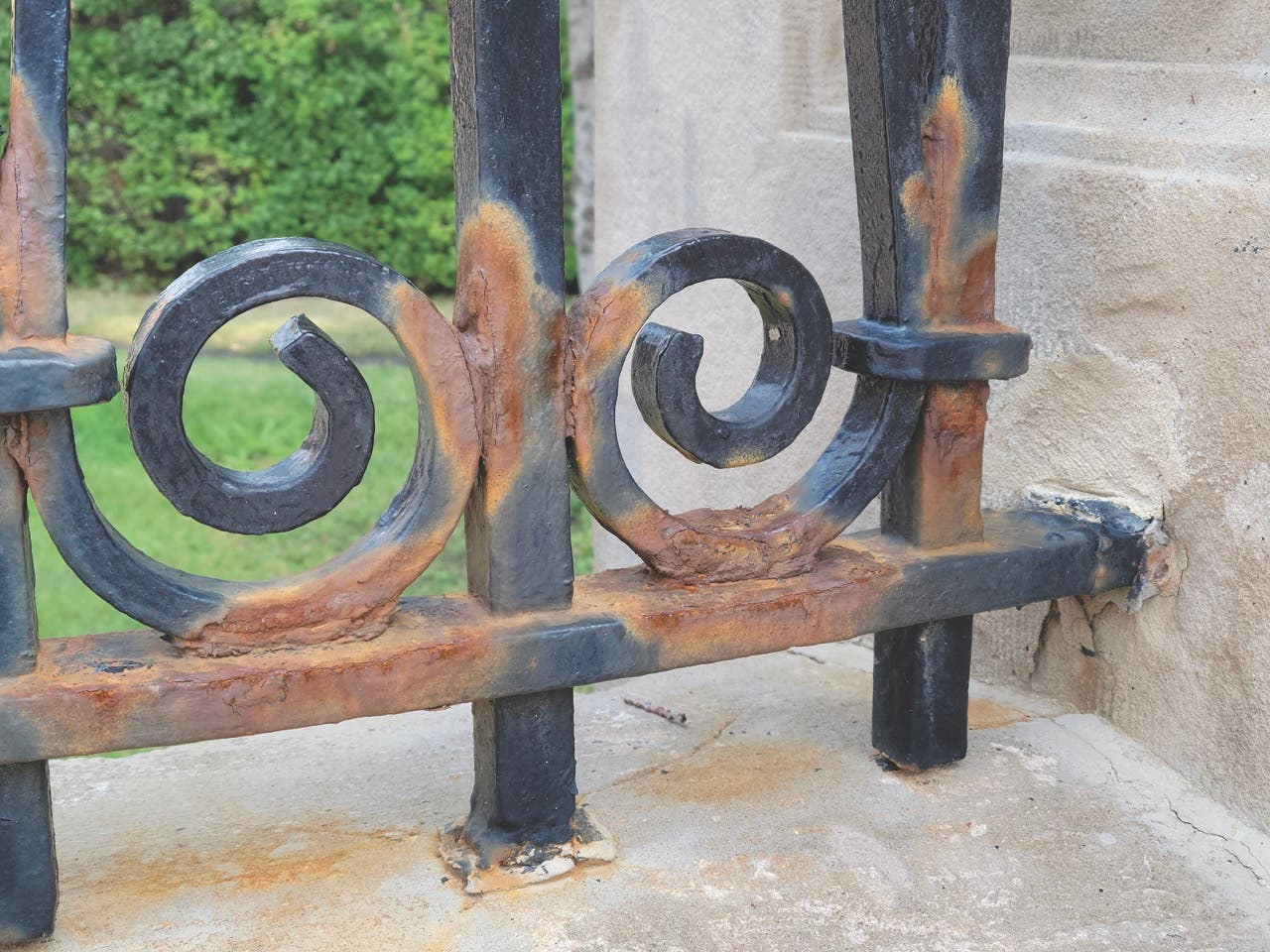
Repair elements before replacing them. Repair work should be performed by professionals who can match the craftsmanship present. When repairing wrought iron, it must be repaired or replaced with wrought iron. Frequently, ill-conceived repairs are made with mild steel, which will corrode more quickly, and fail under loads that the original material still withstands. If replacement using materials from another site is contemplated, ensure any salvaged parts have legal provenance.
Replacements should not be welded to the wrought iron, and cast iron should not come into direct contact with the wrought iron. If cast finials are slotted over the end and hammered in place, the surfaces must be fully painted prior to attachment. If secured by molten lead through a port in the finial, the lead will both bond and separate the cast iron from the wrought. TB
Further reading:
* Davey, Ali Iron: The Repair of Wrought and Cast Iron Work Advice Series, © Government of Ireland 2009
Baker, Don, Restoration of Wrought Iron Ironwork The Building Conservation Directory 2005, reproduced on www.buildingconservation.com Downloaded 7/9/23
Rizzo, Antonello, The Blacksmith’s Project Book Artisan Press 2018 Chapter 21 Restoration An Essay on the Restoration of Wrought Iron by Alessandro Ervas
Topp, Chris Working with metal Wrought Iron Yesterday and Today IHBC Institute of Historic Building Conservation Magazine Context Volume 139 – May 2015
Susan D. Turner is a Canadian architect specializing in historic preservation of national registered buildings. She is the Senior Technical Architect for JLK, a woman-owned business specializing in the repair and preservation of historic buildings. She can be reached at sturner@jlkarch.com