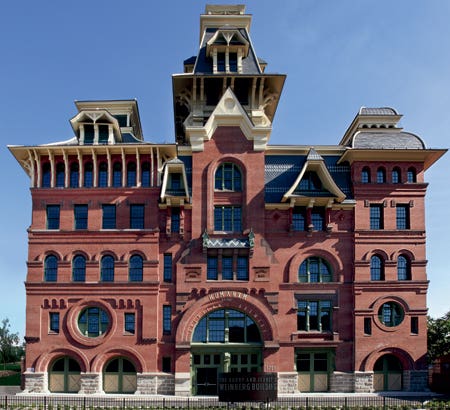
Windows & Doors
The Challenges of Reproducing Historic Wood Windows
Wouldn't it be great if the garden variety windows made today were the same as those made 100 and 200 years ago? No one would have a problem finding good matches for historic buildings but — no surprise — it is not so simple. Not only have architectural styles changed, but also our expectations of how windows should perform. Since the difference between off-target and dead-on often turns on fractions of an inch, here are some insights on the subtle details that can often make or break a historic window project.
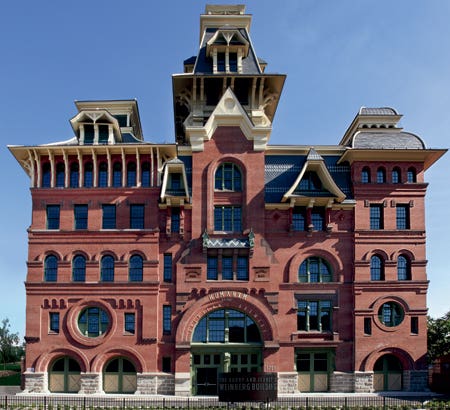
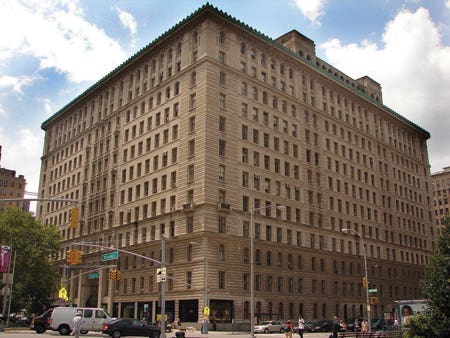
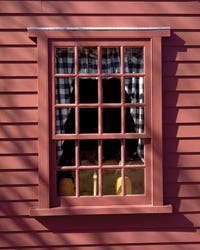
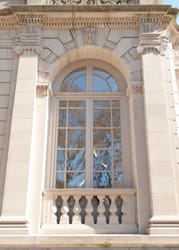
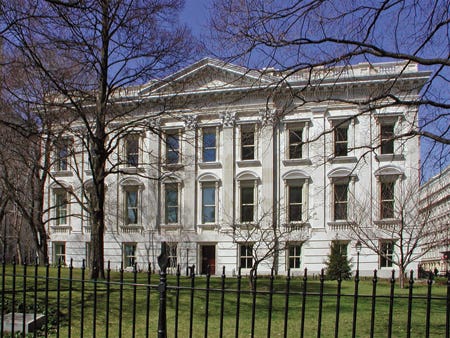
Colonial Construction
What gives Colonial and pre-1840s sash windows their distinctive, intricate identity, is not solely their design, but also their materials and methods of construction – and that of their buildings too. Explains Hap Shepherd of Maurer & Shepherd Joyners in Glastonbury, CT, "The main point to remember is, if you have a plank frame structure from the 18th century, where the whole wall is only 1 1/2-in. to 1 3/4-in. thick, you have a proud window – that is, a window built on the outside of the house."
Shepherd notes that this is noticeably different than stud-frame houses of the 18th century and later, where the window is located in the middle of the wall thickness. Also, such windows are not double-hung but have the upper sash fixed. For a new reproduction to read as authentic for this era, it is important to maintain details like this in a new window and to avoid obscuring them. For example, Shepherd says that instead of adding a storm panel on the outside of the window, which blankets the window in a monolithic envelope of glass, he prefers to upgrade it on the inside with an energy panel. "The energy panel is attached with a press seal, so you can open the window at any time, and it avoids the glassy look of a storm panel on the outside of the house."
Leonard Baum, consulting architect with Maurer & Shepherd, says that one of the biggest issues he finds with today's early-style period windows is the muntin grids. "You see layouts where the proportions are such that they are much more horizontal than the windows we find in historic structures, which were commonly based on 7x9 or 10x12 proportions." As Baum explains, the difference may not be obvious to the passerby, but it can have a strong impact on the overall façade of the building. "Take a mill building that might have 200 windows. If someone selects windows from a catalog with a muntin layout where the proportions are wider than they are tall, which is incorrect for most mill buildings, it just looks ridiculous."
Baum also says it is tricky to find early-style windows where the muntin proportions are related from layout to layout. "When I am designing a project, I often want the muntin layout to be consistent, to have the glass size be all the same throughout all the windows – say an 8/8 and a 12/12 and maybe a 4/4 – but you go to many catalogs and they're not coordinated like that at all." Baum says he has spent hours doing the math on different products to coordinate them for a project.
Glass and Muntins
As glass making became more production oriented throughout the 19th century, window makers were able to use larger panes of glass, reducing not only the number of muntins but also their dimensions. "The muntin bars around the turn of the 20th century varied between 7/8-in. and 1-in. in width," explains Ron Safford of Parrett Windows in Dorchester, WI, "but there may be some modification needed to the original specifications if you are bringing in contemporary and energy-efficiency features."
As Safford notes, the big hurdle is insulated glass. "When you go with insulated glass, the problem you encounter is the depth of the window and the sight lines of the muntin bars, the true divided light bars." Not only does insulated glass add the thickness and weight of more glass, but the manufacturer also has to account for additional beads and seals. "It gets complicated," says Safford, "but the challenge is how narrow can you keep that muntin bar? To get quality insulated glass, you are generally looking at 1 -1/8-in. muntin bar width."
Safford also notes that size comes into play too. "The larger the window, the greater the need for more structural stability in that muntin bar, which causes it to be wider." Nonetheless, he points out that a close working relationship between architect and manufacturer can achieve those objectives. "Architects do not need to compromise or settle for a mass-produced product," he says. "There are companies that will build to those specifications, including modifications that match up to the original windows."
Casings and Exteriors
It is easy to obsess on the minutiae of sash and muntins, but the success of a reproduction window can also hinge on the frame that carries the sash and the trim work that surrounds it. As Christine Marvin of Marvin Windows and Doors in Warroad, MN, explains, "When a project goes out to bid with multiple manufacturers, they are often required to provide their version of what they would supply for the job. It is not uncommon for each manufacturer's window to temporarily go into one of the building openings for further discussion."
Marvin says that by using what they call a rapid prototype machine, they are able to take shop drawings and profiles and, on a fairly quick turnaround, create a corner sample of the exterior design replication. "This enables us to bring it to the job site or architect's office, and even put it in the opening to see how it looks and works in the rough opening."
Marvin also notes that it is important for new windows and doors to be built to accommodate the way buildings have shifted over time, and that requires good measurement of the openings. "Even if the units started off at the same size for the opening fit," she says, "based upon the shifting over time you see some variations, so it is important to get measurements of each opening."
Minimal Meeting Rails
Muntins are not the only sash members that get squeezed. According to Tim Forster of HeartWood Windows in Rochester, NY, "One of the issues that comes up in making reproduction double-hungs is when the client calls for very, very narrow meeting rails or check rails." Throughout the latter-19th century, as the trend grew for larger, more unobstructed expanses of glass, meeting rails grew slimmer, thereby creating one of the weakest members of a sash in a highly vulnerable location. "I've seen rails as narrow as ¾-in.," says Forster, "and there is just no joinery there."
Michael Iwanyczko of Reilly Windows and Doors in Calverton, NY, agrees. "Old double-hung windows typically have a check rail that is very narrow. It is a very commonly requested detail in some municipalities where they really want windows made exactly the way they would have been made 100 years ago." As Forster puts it, "People ask, ‘It was done that way a century ago, why can't you do it again?' Of course you can do it, but the question really is should you do it?" He notes that his company likes to work with a traditional tenon-type detail that is pretty and neat, but that for narrow rails they usually have to go with exposed tenons. "We always caution people that, while it would be nice to have that narrow rail, do you really need it? Is it really going to be important to the project?"
Unequal Sash
By the turn of the 20th century, there was a trend for building double-hung sashes where the meeting rail is higher than the middle of the window. Part fashion, part practicality, the idea was to give occupants a clearer view from the window, unobstructed by the meeting rail falling at eye-level, as well as a more modern look when seen from the street. Iwanyczko sees these windows frequently; "Often times, the window glass proportions are two-thirds on the bottom sash, one third on the top sash."
He notes that sometimes there are smaller decorative panes in the perimeter of the bottom sash, or just a single large pane with multiple panes of decorative glass in the upper sash, from diamond grid patterns to Gothic arches. "We see a lot of different applications, but since most of our projects are in locations where the view is really important, it was definitely a sight-line issue."
Clever as such windows are for increasing unobstructed views, they can create a problem in operation. Says Iwanyczko, "Even though the bottom sash is two-thirds and the upper sash is one-third, when you open the window, normally you actually get a smaller opening, and less air circulation, than with a traditional double-hung where the sashes are equal." To solve this problem, sash manufactures of the past would build what was variously called a box-head, jib-head, or slip-head window. "They would actually pocket the lower sash into the wall above," says Iwanyczko, "so when the lower sash is in the fully up position, it equals the upper sash. We have worked on projects with these windows and it is a very nice detail."
Window Standards Update
Just a year ago, a handful of historic window specialists, Duffy Hoffman, John Leeke, Bob Yapp, David Gibney and Jim Turner, realized that national standards were needed to guide the phenomenal growth in interest to save historic windows. They founded the Window Preservation Standards Collaborative (WPSC) and held the first National Window Preservation Summit in July, 2011, when dozens of advisers and observers joined them. Since then, the Collaborative has grown to include over 100 historic window specialists, advisers and stakeholders who have been working diligently to produce the first National Window Preservation Standards.
Their activity is documented at the online Standards Forum: http://www.ptnresource.org/WPSC_forum/.
The forum has many brisk conversations going on simultaneously as the group develops drafts of maintenance, repair and weatherization methods. The project began with the founders writing many of the standards. Advisers and stakeholders are now submitting methods and topics as well. As each is discussed on the forum it is drafted into a standard by the founders, for all to see and comment on.
This update is being written in mid-April, as the Collaborative is beginning to finalize many of the draft topics and method standards. Final editing will take place in late May, with publication of the National Window Preservation Standards book in the summer. – John Leeke, WSPC Co-founder
Sash-in-the-Round
Another window common in the 19th century, though all but unheard of today, is the curved-in-plan sash — typically found in circular rooms or towers, where the sash actually follows the curve of a wall. "The complexity of these windows really requires experienced craftspeople," says Safford, "to get the radius right, to get the specifications and function right."
Iwanyczko agrees. "There is still a lot of handwork to them. A lot of the work is done the traditional way, taking large pieces of wood, then cutting them into shape; no steam bending. It is all made-to-order, including the glass. There are really only a couple of companies out there that can produce curved-in-plan restoration glass." Iwanyczko adds that computers have made the manufacturing process a little easier than a century ago. "Especially when you get into curved muntin patterns, computers can help you figure out how to do a curved arch on a curved-in-plan window." Nonetheless, curved-in-plan windows are definitely more time-consuming and costly than conventional windows. He notes, "Sometimes where the budget doesn't allow curved-in-plan, you do curved sills and curved-head trim and just straight-across sash. However, we've done a number of jobs where the window was installed that way, and when the owner saw it, he paid to have those units taken out and brand new curved-in-plan windows made."
Select Suppliers
Allegheny Restoration, Inc.
Morgantown, WV
www.alleghenyrestoration.com
Architectural Components, Inc.
Montague, MA
www.architecturalcomponentsinc.com
Bergerson Cedar Windows, Inc.
Hammond, OR
www.bergersonwindow.com
Artistic Doors & Windows
Avenel, NJ
www.artisticdoorsandwindows.com
Crittall Windows
Witham, Essex, UK
www.crittall-windows.co.uk
Grabill Windows & Doors
Almont, MI
www.grabillwindow.com
Green Mountain Window Co.
Rutland, VT
www.greenmountainwindow.com
Heartwood Fine Windows & Doors
Rochester, NY
www.heartwoodwindowsanddoors.com
Historic Doors
Kempton, PA
www.historicdoors.com
Kolbe & Kolbe Millwork Co.
Wausau, WI
www.kolbe-kolbe.com
Marvin Windows and Doors
Warroad, MN
www.marvin.com
Parrett Windows & Doors
Dorchester, WI
www.parrettwindows.com
Pella Windows and Doors
Pella, IA
www.pella.com
Reilly Windows & Doors
Calverton, NY
www.reillywd.com
Wood Window Workshop
Utica, NY
www.woodwindowworkshop.com
The Woodstone Co.
Westminster, VT
www.woodstone.com
Zeluck Windows and Doors
Brooklyn, NY
www.zeluck.com
Gordon H. Bock is an architectural historian, instructor with the National Preservation Institute, and speaker through www.gordonbock.com.