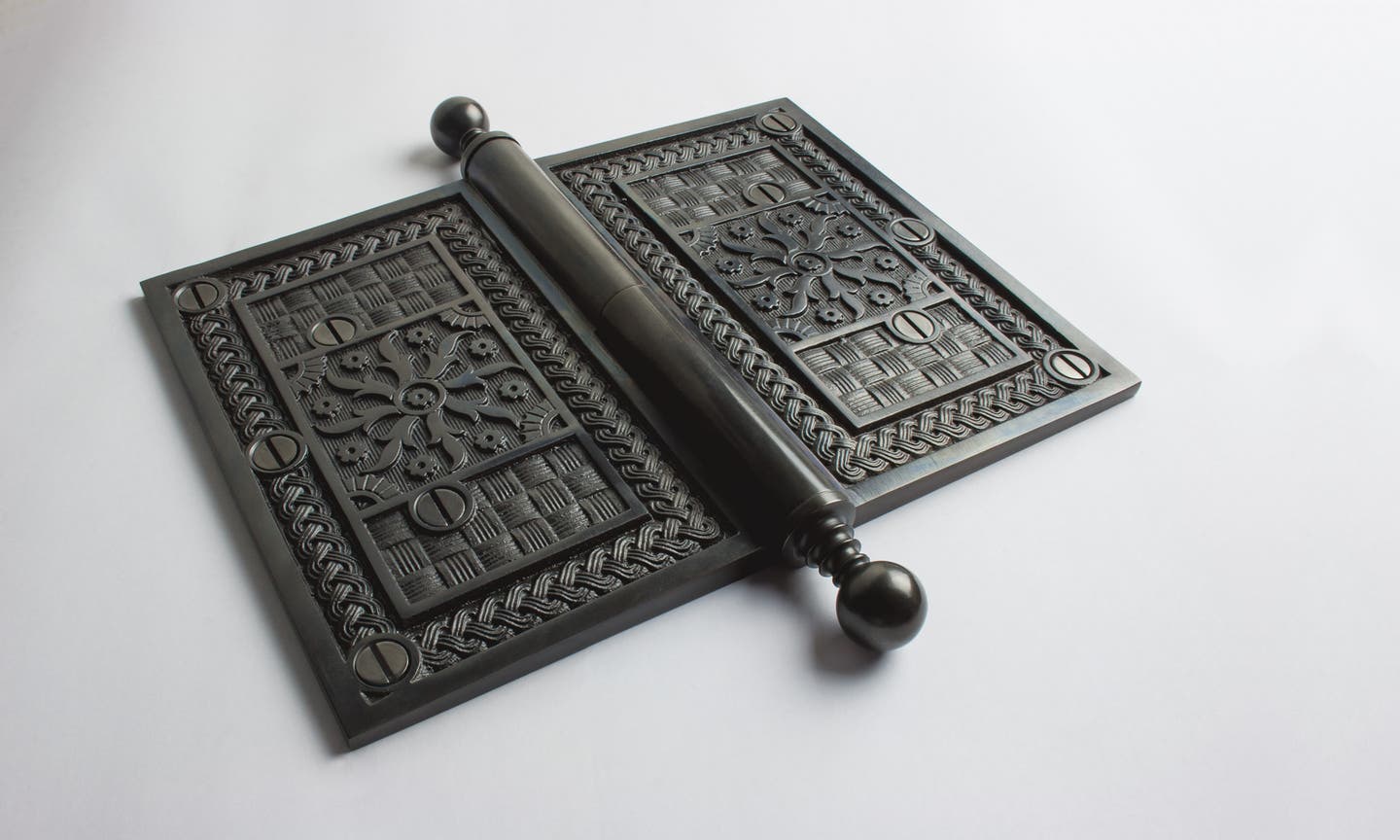
Product Reports
Appropriate Hardware for Historic Restoration Projects
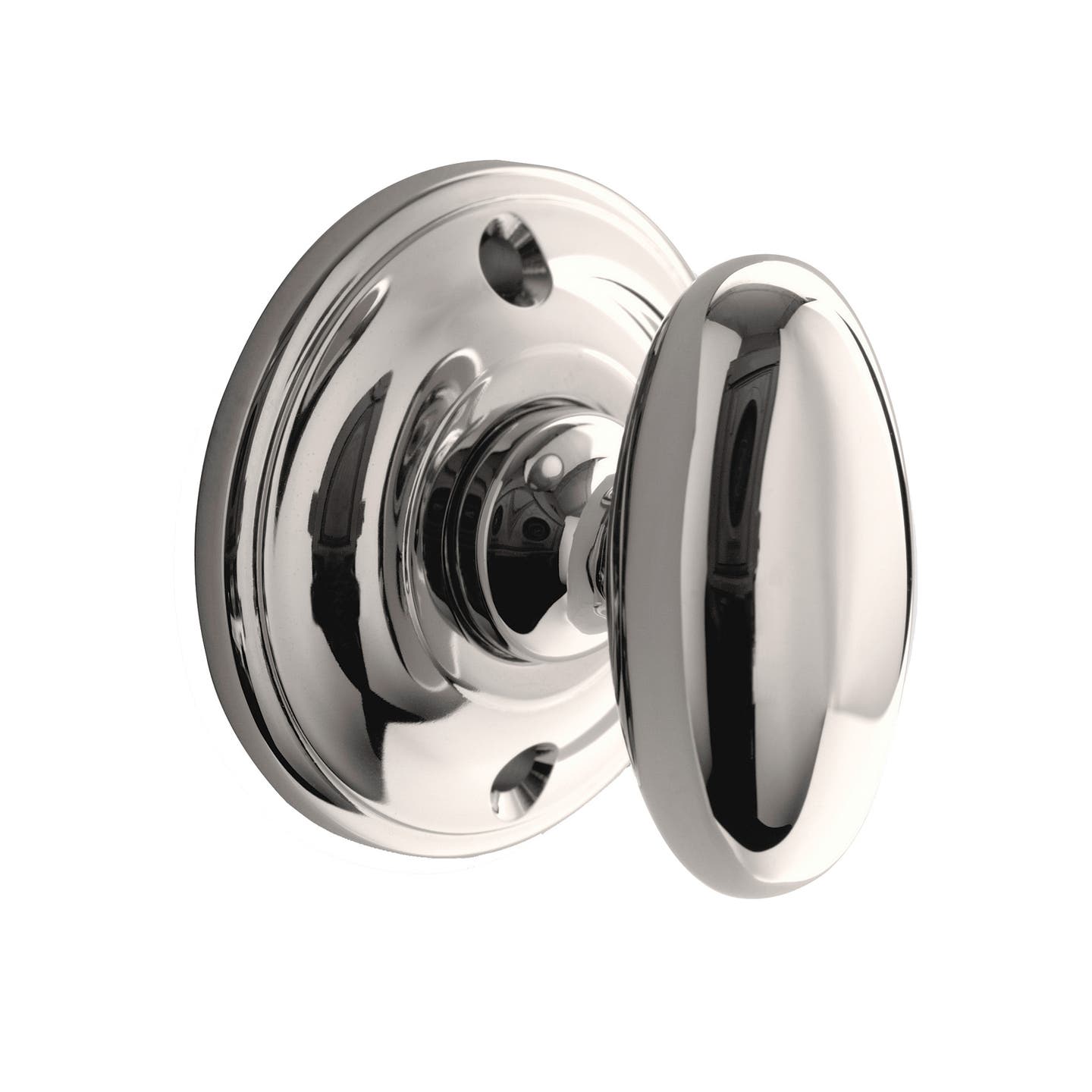
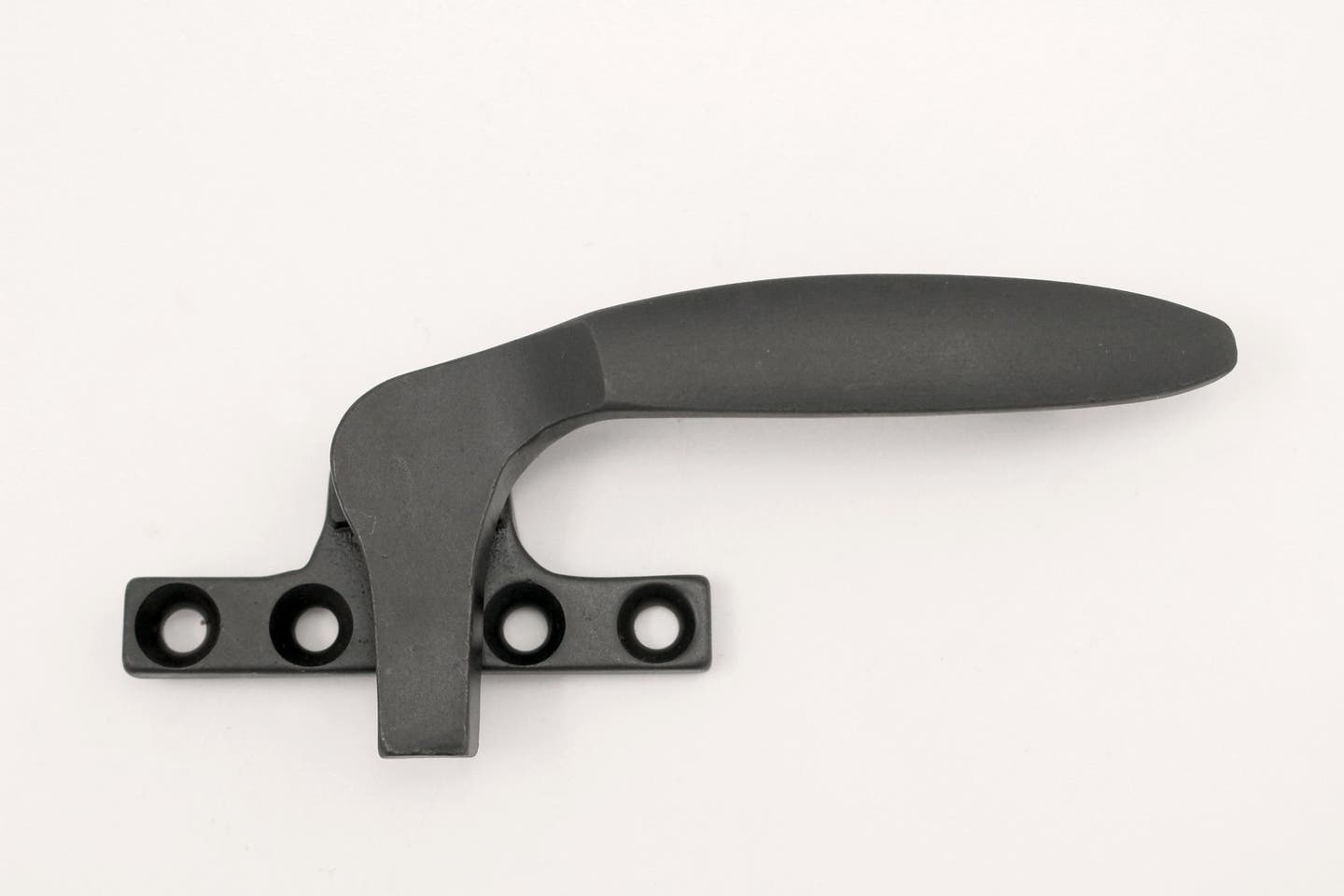
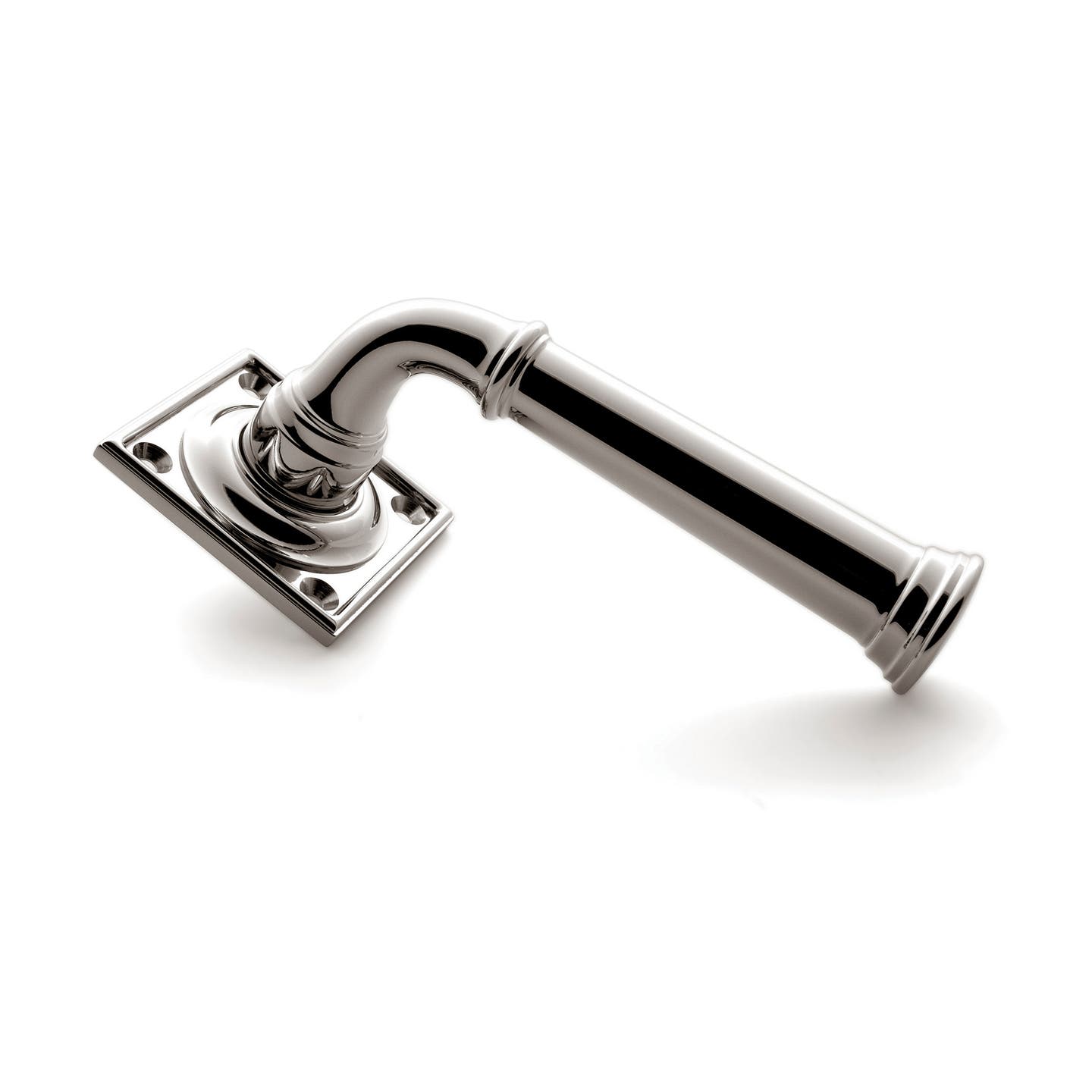
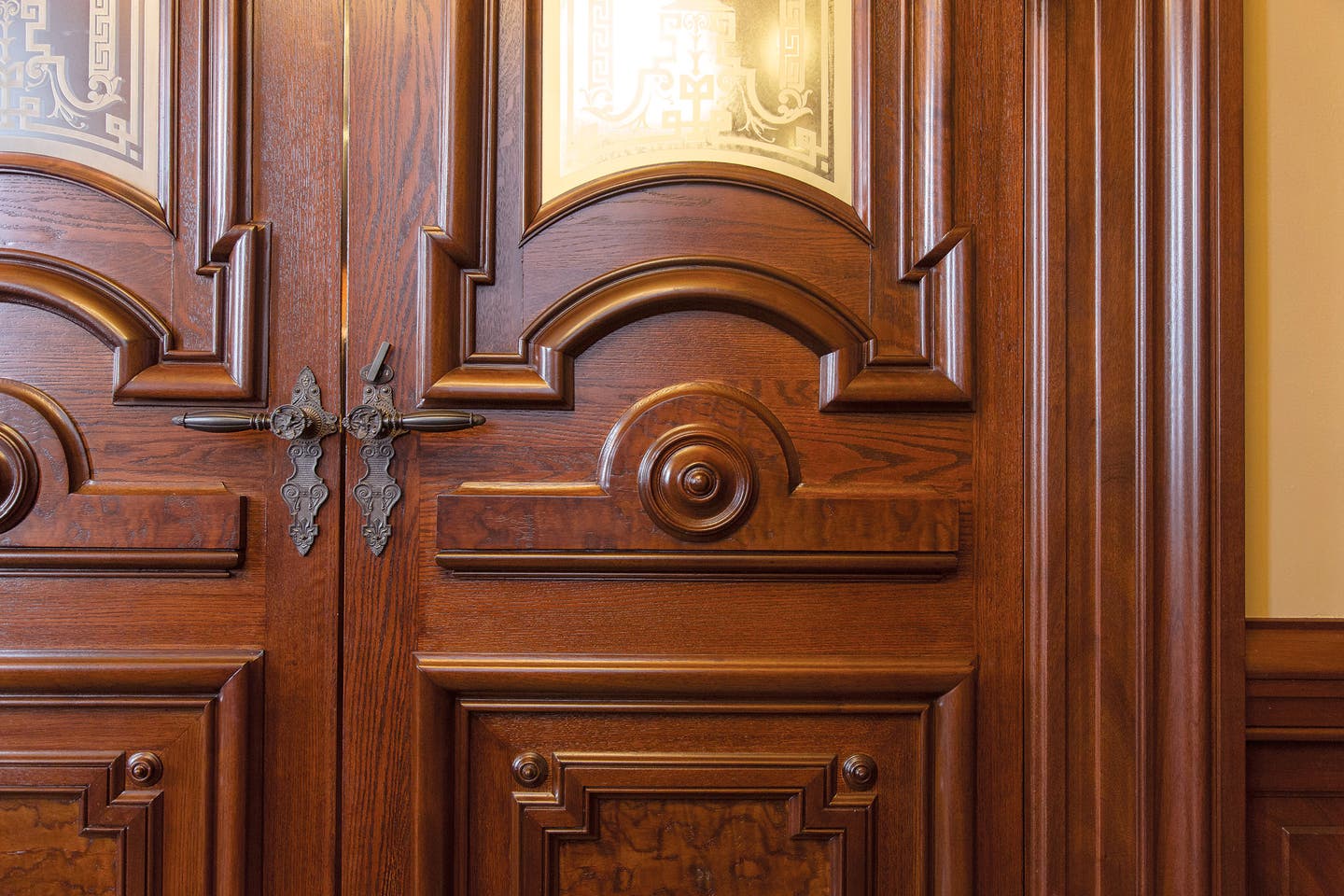
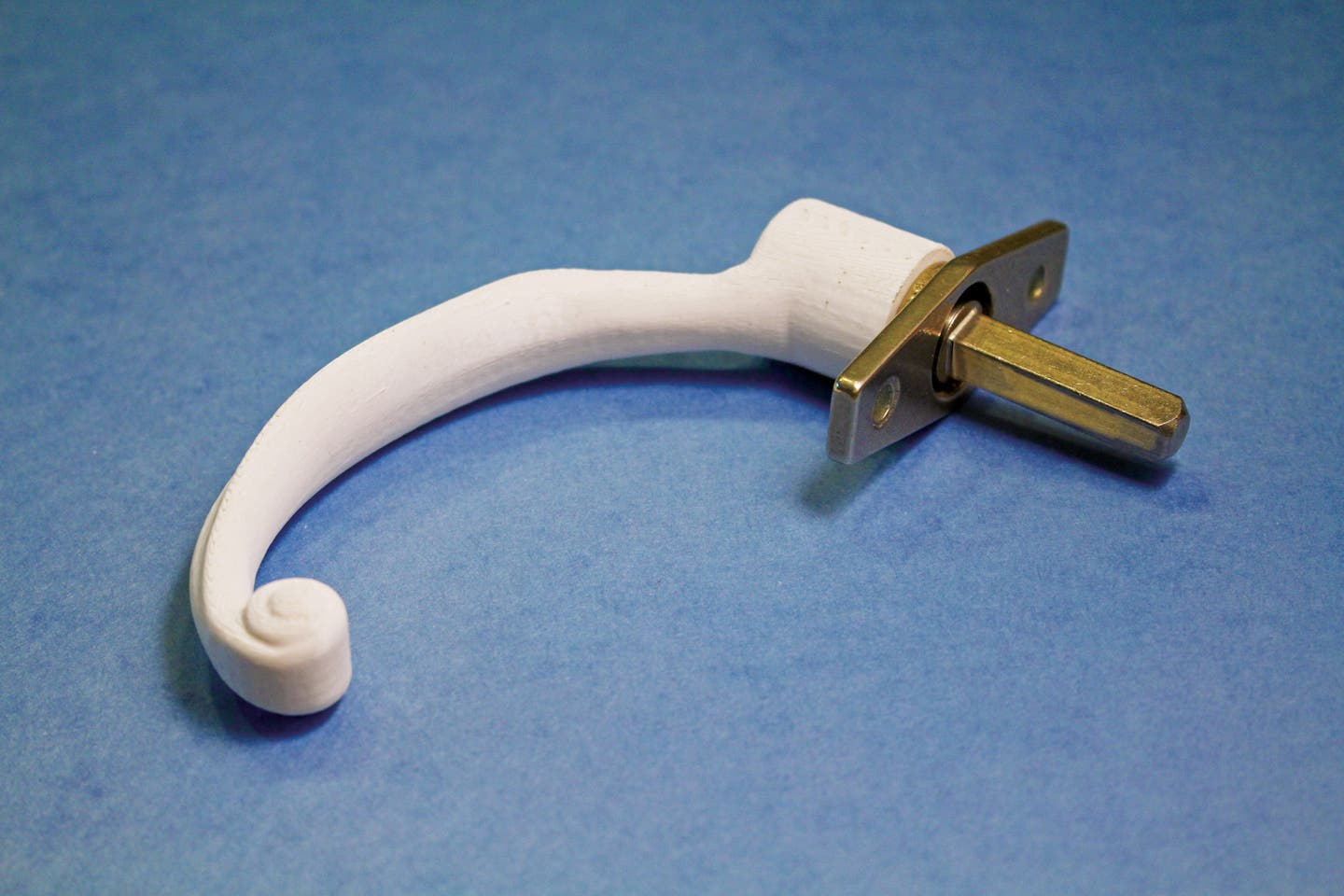
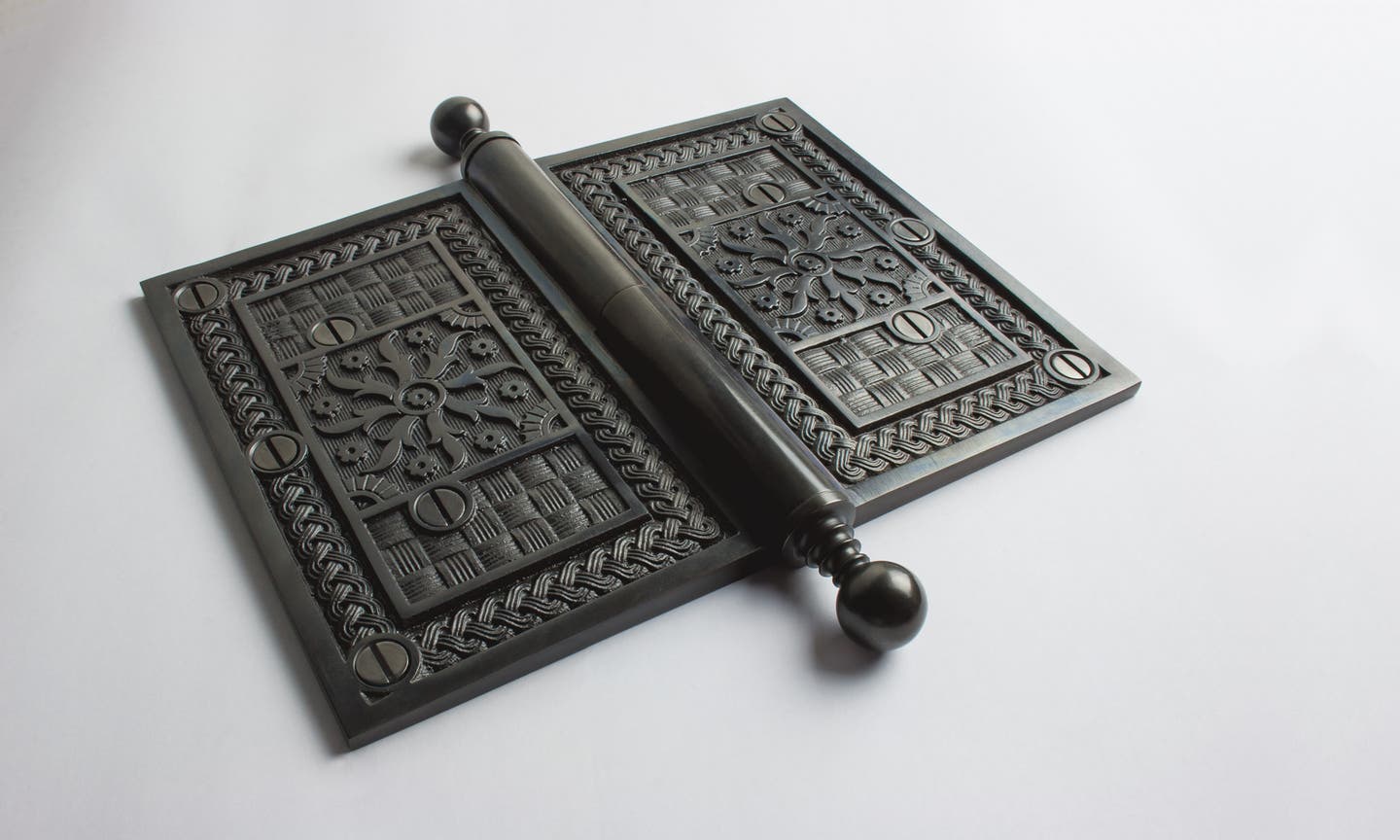
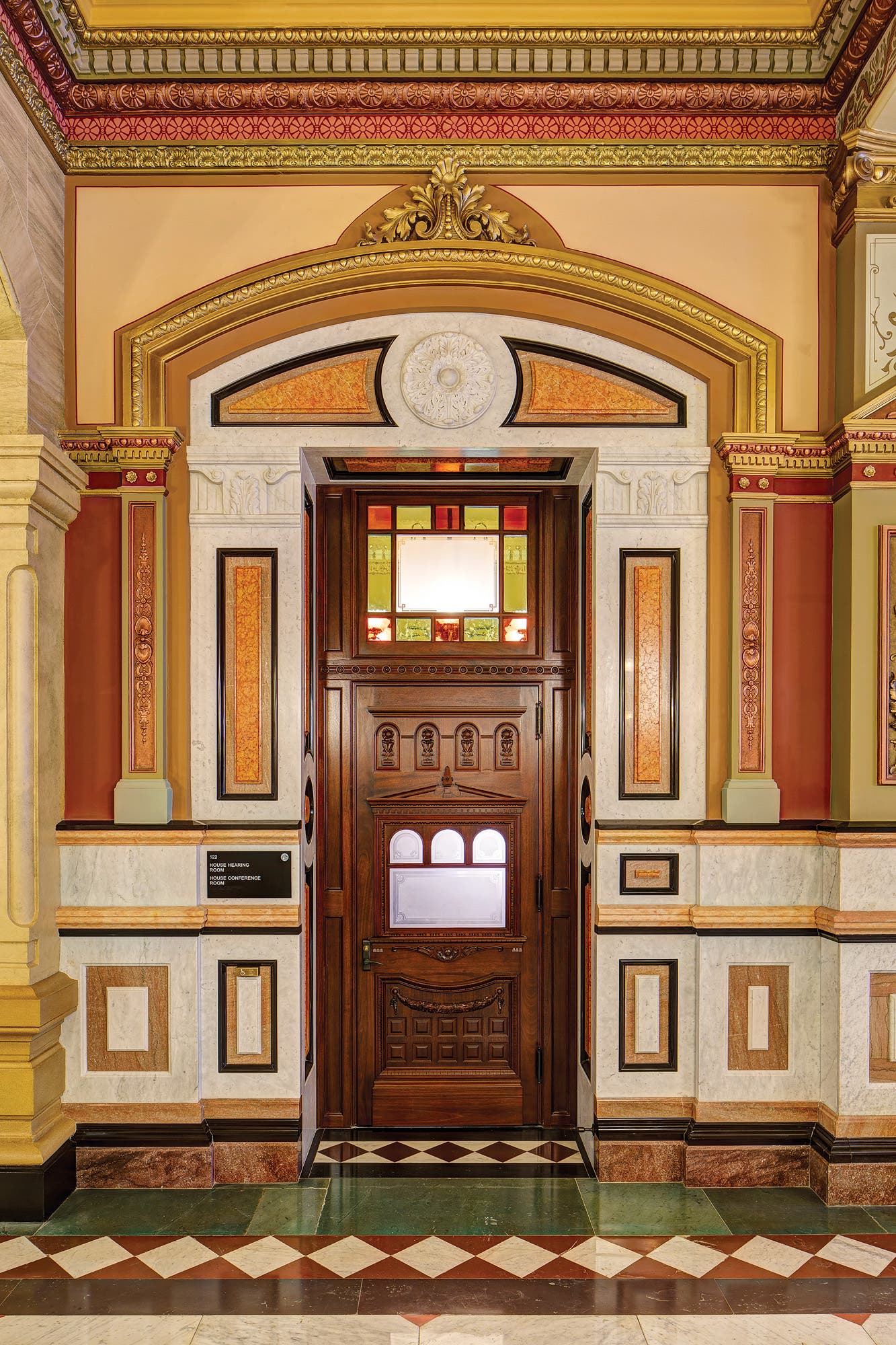
Oftentimes when projects are faced with budget constraints, there is a strong temptation to cut corners on door and window hardware. While it’s usually among the last items installed on a project, door hardware is the first thing a visitor will touch when interacting with the building, and thus it is the hardware that gives the first impression. If the project goal is to convey a sense of excellence, and permanence, the hardware is the perfect vehicle to deliver this message. Featured here are three projects with quality hardware that have either made it to installation or are in its production stages.
Illinois State Capitol: West Wing Renovation
In 2009, plans were made for the $50-million renovation of the Illinois State Capitol’s West Wing. In addition to restoring the back to its original 1870s appearance, they included upgrades for life safety, ADA and security. Like most traditional buildings, the Capitol had suffered inappropriate modifications over the years.
Vinci Hamp Architects (VHA) of Chicago, IL, oversaw the renovation and they worked closely with Al Bar Wilmette Platers of Wilmette, IL, to reproduce the door hardware. “The door hardware had been modified over the years and there were fragments and incomplete pieces all over the place,” says David Hrabal, AIA, senior associate at VHA. “Luckily, throughout the whole we were able to find parts and pieces to form a complete set. Our goal was to take this archaic set of hardware on the original doors and try to make them suit modern needs for a functional office building.”
The VHA team developed a hierarchy for the doors that included doors for main entrances, corridors, and closets. Al Bar fabricated hardware suites for each level. The three sets of copper-clad wooden entry doors, for instance, called for custom-designed hardware. “We created several designs for the VHA team to choose from,” says Greg Bettenhausen, president of . “After a design was selected, our sculptor handcrafted originals to create molds that are injected with wax. The waxed models are placed on a tree and dipped in plaster to create shells. Once the plaster is dried and the wax is removed, bronze is poured into the plaster shells. The last step is to polish and plate the hardware before installation. We used the lost-wax method to fabricate all the hardware for the .”
Completed in 2014, the renovation project was so successful it received AIA’s National Honor Award for Interior Architecture and won Project of the Year from Landmarks Illinois. “Al Bar was great to work with,” says Hrabal. “They had a deep understanding of the hardware, which gave them the confidence necessary to deliver an outstanding product.”
CBS Columbia Square
In 2007, Schofield, WI, based Corporation president Debbie Flood decided to incorporate 3D printing technology into her firm’s manufacturing of sand-cast architectural hardware. “Utilizing 3D printing technology and laser scanning, has been able to condense the product development cycle,” says Flood. This equipment and the ability to produce all tooling has made it possible for the firm to maintain control of the entire process, and thus oversee the full evolution of new hardware.
In the case of historical hardware, 3D printing is often used in conjunction with laser scanning to replicate hardware design. produces functional 3D printed ABS plastic prototypes for approval, and can deliver a cast sample in a matter of weeks, Flood explains. A functional prototype is a high strength plastic assembly that can be coated for client presentation to reflect the original and can be installed on the window or door to test for fit, and function. Aluminum and plastic tooling that can accommodate both large and small custom jobs, is also produced .
Historic hardware replication can be approached in three ways, says Flood. The existing hardware can be exactly replicated, hardware can be replaced with historic hardware from our extensive pattern library, or the historic handle design can be replicated and adapted to work on window systems with modern energy efficiency and functionality.
In 2013, worked with Crown City Hardware to replace the window handles on CBS Columbia Square in Hollywood. Built in 1938, the studio fell into disrepair in the late ‘80s and was slated for demolition after the last radio station moved out. In 2012, it was acquired by Kilroy Realty Group and is now being renovated as part of a 4.7-acre mixed-use project.
“Our client decided to replicate the base of the original hardware so the lock would fit properly
on the existing window, but chose to use a standard handle instead of replicating
the original,” says Flood. “The handle selected was chosen because it has been commonly used for nearly 100 years. We were able to provide the historic look for windows while minimizing tooling costs.”
The Greenwich Lane
Over the last 25 years, The Nanz Company in New York City has established a name for itself as a reliable manufacturer of custom high-end residential hardware. Several years ago, the firm branched out to form the Nanz Contract Division in response to the demands of the high-end real estate development market. “We began exploring alternate methods of manufacture to allow for cost per piece in high quantity runs while maintaining our quality standards and continuing to manufacture domestically in New York,” says Joe Roth, director of the Nanz Contract Division. “The Greenwich Lane project is a testament to our ability for on-time and development projects.”
Located in the West Village neighborhood of New York City, The Greenwich Lane project is a collection of five multi-residential buildings and five townhouses all connected by a large shared basement and common outdoor spaces. The developer, Rudin Management Company, decided to use different architectural styles for each building and requested that the hardware suit. The Nanz team used several hardware suites, one for each building, with a common suite uniting all public and amenity spaces.
“To accommodate high-quantity manufacturing, additional tools were made for holding items within machines to facilitate multiple machining stages for multiple parts simultaneously,” says Roth. “Lights-out manufacturing was introduced for all initial machining stages so we can produce throughout the night and new mechanisms were made to feed brass into these machines. The longest portion of lead-time is the hand-finishing stages, which is the same for standard single-family projects and Contract projects to maintain the Nanz standards. “Although the job is still in progress, we certainly see it as a success so far,” notes Roth. “All buildings are moving smoothly through production (slightly ahead of schedule, in fact) and we are getting ready for our first shipments.”
Select Suppliers
Talladega, AL
Al Bar Wilmette Platers
Wilmette, IL
Arch. Resource Center
Northwood, NH
Bronze Craft Corp.
Nashua, NH
Brusso Hardware
Belleville, NJ
Crown City Hardware
Pasadena, CA
E.R. Butler & Co.
New York, NY
House of Antique Hardware
Portland, OR
by St. Simons
Fullerton, CA
Lowe Hardware
Rockland, ME
Melron Corp.
Schofield, WI
Phelps Hardware
Hinsdale, NH
The Nanz Company
New York City