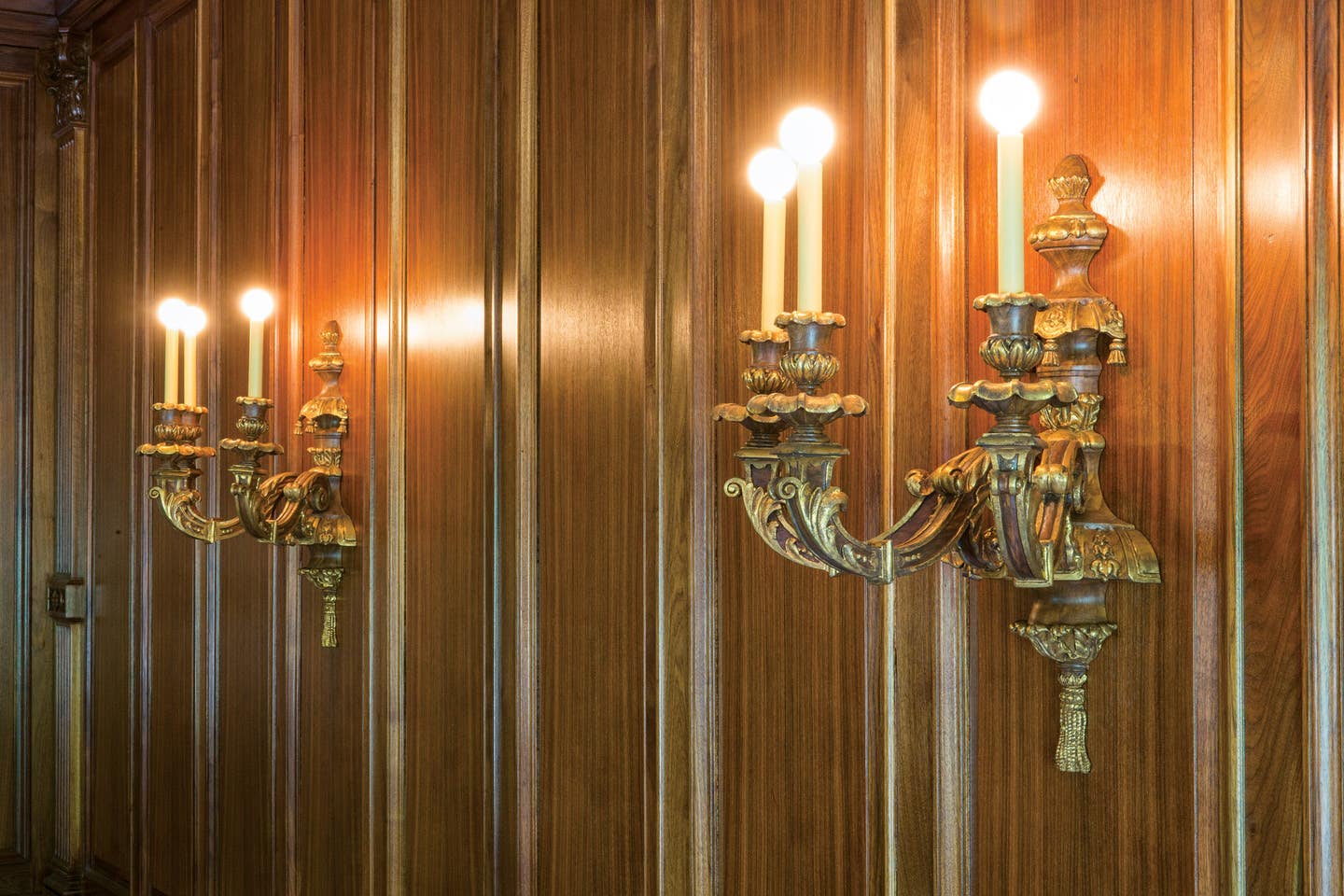
Product Reports
Heritage Metalworks Lights Ford’s Fair Lane Estate
Recreating period lighting fixtures is often part art, part detective work, even when there’s a wealth of original information available.
Since 2001, brothers Matt and Jon White, co-owners of Heritage Metalworks, have been honing their sleuthing skills on a variety of high-profile lighting and metalwork projects for the likes of Winterthur, the Smithsonian Institution, and the Chrysler Museum of Art.
Their work for Fair Lane, the Dearborn, Michigan, estate of Ford Motor Co. founder Henry Ford and his wife, Clara, presented new challenges and creative opportunities.
The Henry Ford Estate | House Museum
The Henry Ford Estate, the nonprofit in charge of the iconic 1915 property that has been converted into a house museum, commissioned them to recreate chandeliers, sconces, and metal smoke stands as part of an extensive restoration that will return the property to its 1919 grandeur.
The 31,000-square-foot limestone mansion, which is a blend of Midwestern Prairie School and English country manor styles, was one of the first sites to be designated a National Historic Landmark. Designed by architects William H. Van Tine and Joseph Nathaniel French and landscaped by Jens Jensen, it presides over 1,300 wooded acres on the River Rogue.
The property, named after an area in Cork, Ireland, that was significant to Ford, originally contained an electrical power plant, a greenhouse, a boathouse, riding stables, a children’s playhouse, and a treehouse.
Through the decades, the house had deteriorated, and some of the important lighting fixtures in the music room, the library, and the billiard room had gone missing. Their images remained only in a series of professional black-and-white photos that the Fords commissioned to show off the estate when it was new.
“The photos were high-resolution,” Matt says, “but these fixtures have a lot of refined details sculpted into them that could not be seen with clarity. And because of the perspective the photos were taken at, it made it a challenge to figure out the scale. We made an educated guess with the assistance of the photos and actual site measurements, overlaying them to try and zero in on actual scale.” Jon added, “Nor could we tell the color of the finishes or whether the patina was polished.”
Replicating Lighting Fixtures
Using the photos, as well as detailed sales receipts, period lighting catalogs, letters, and other correspondence between the Fords and the makers, the artisans at Heritage Metalworks were able to put the pieces together like a jigsaw puzzle.
“We also comprehensively researched metal finishes and studied fabrication processes from other lighting manufacturers of that period,” Matt says. “The rooms were scaled, referencing millwork, molding, plasterwork, and other key elements.”
The team, which did the work in its 12,000-square-foot plant in Downingtown, Pennsylvania, then made concept sketches, CAD drawings, 2D cutouts, and printed patterns. 3D mockups re-created the size of the fixtures as well as their refined details.
“We visited the house twice,” Matt says. “The second time, we took hand-sketched 2D models and held them up in the middle of the room at the same angle they were in the old photos to make sure they were the correct size and scale.”
The library, where Heritage Metalworks reproduced a pair of two-armed wall sconces and a chandelier, was the more challenging part of the project. It required a lot more guesswork because the fine sculpted details were not clear in the old photos.
Replicating the finish on the fixtures was just as difficult. “From the photos, it looked like shiny satin nickel or pewter, but we’ll never know for sure,” Jon says.
Pieces of the chandelier, which is 29-inches high and nearly 34-inches wide, and matching wall sconces were cast in brass using the “lost-wax” process to pick up the refined period details. The brass was then plated with zinc and antiqued.
The eight, three-armed scones in the music room were the most straightforward part of the project, simply because there were existing chandeliers to copy.
“It took us 80 to 90 hours just to figure out the size,” Matt says. “And production took about four months.”
Each sconce Heritage Metalworks designed was 26-inches high, 15-inches deep, and 25-inches wide. The back plate was hand-sculpted for a pattern and molded. The arm, bobeche, and candle cup were molded from the original chandelier, with changes to the arm pattern to fit the size of the sconces. The parts were cold cast in resin and faux painted with several layers by hand, with different techniques, to look like mahogany with 24-karat gold-leaf accents.
“We used resin instead of hand-carved wood to keep costs down,” Matt says. “But the resin still allowed us to pick up the details of the wood texture to maintain the authenticity of appearance.”
“We asked the conservators working on the woodwork in the room of the estate to carefully scrape off some of the top layers of the old paint to help reveal the shadow created by the back plate of the original sconce,” Matt says. “That really helped us get the size and shape accurate.”
Replicating Hand-Forged Smoke Stands
Heritage Metalworks also replicated three 32-inch-high, hand-forged smoke stands for the Field Room and sun porch. “They were formed using metal spinning then shaped to create a scalloped look,” Matt says. “They were fabricated to scale and finished with dark wax, a finish common to the period.”
The team is also creating lighting for the billiard room, floor lamps for the library, and wall lighting for the interior room that used to house an in-ground swimming pool.
“The chandelier in the billiard room is by far the most challenging, with very complex details,” Matt says. “We have four photos taken at different angles, and we always see something that’s not jiving with one photo to the other. It’s like a dance of one or the other. The fixture looks to be more than twice as long as the width, so we’re constantly seeing conflicts when determining the scale.”
Jon says Fair Lane is a “unique project because of the depth of what we have to accomplish with so little information.”
The Whites are eager to see the completed rooms gloriously and fully illuminated as they were when the Fords called Fair Lane home.
The fate of the original fixtures has been buried by time, but Matt and Jon hope the publicity surrounding the public reopening of the estate next year brings them to light again.
“They are not the kind of fixtures that would have been thrown away,” Matt says. “If an original pops up, we’d like to see it to see how close we were to getting it right.”