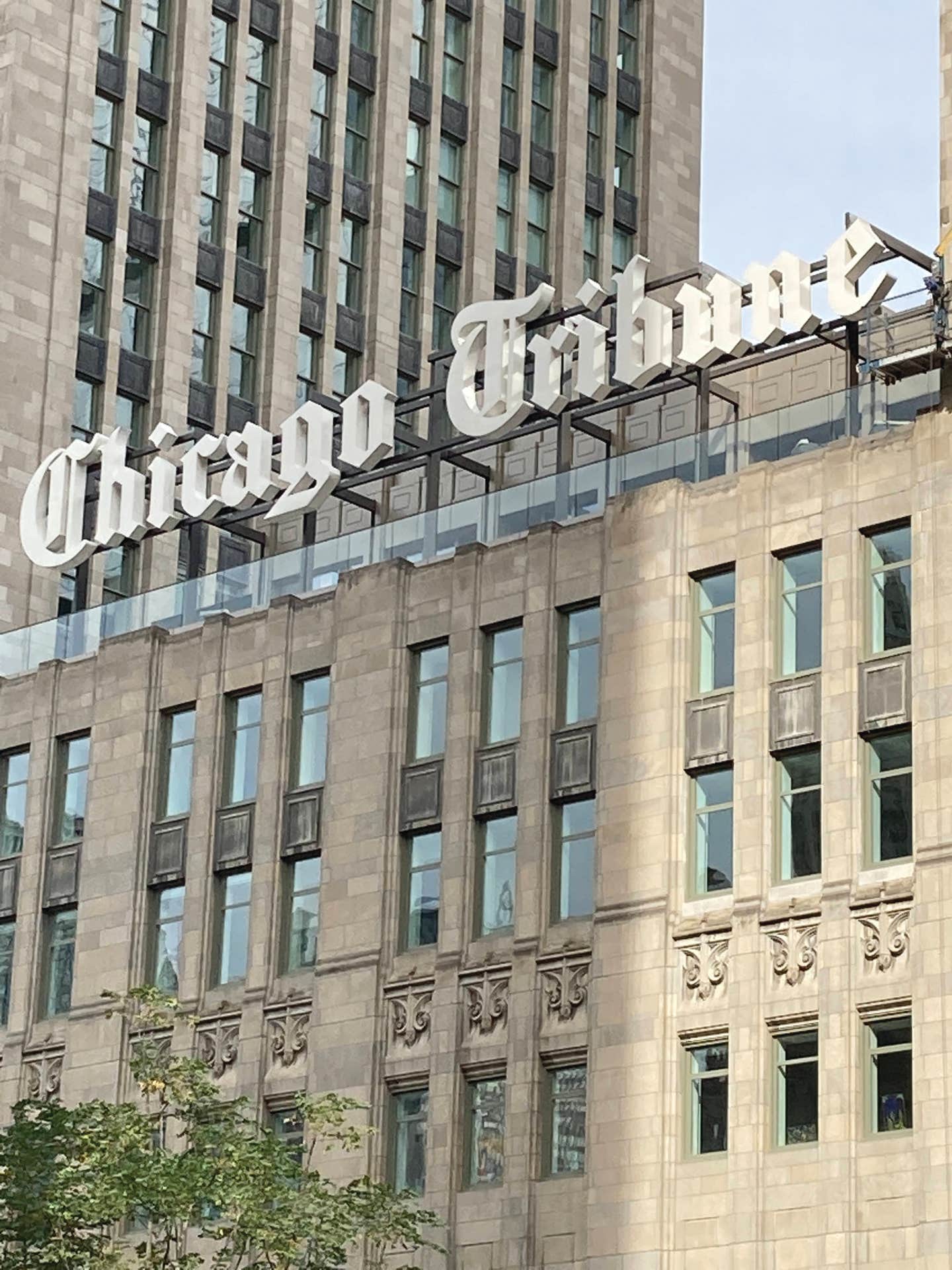
Product Reports
Face Lift
The Tribune Tower stands tall and takes its rightful place in Chicago’s architectural legacy. Designed in response to an international design competition held in 1922 that attracted 264 entries, the Tribune Tower was the home of the Chicago Tribune and in subsequent additions, related media, until 2018.
Raymond Hood and John Mead Howells created the winning design in that competition. And the competition was stiff, with Eliel Saarinen winning second prize and Walter Gropius in the mix. Howells and Hood created a neo-Gothic, 36-story tower with a steel frame clad in Indiana limestone. According to the AIA Guide to Chicago, 90 percent of the entries were based on historical precedent and most were either inspired by the Beaux-Arts style or were neo-Gothic. At the time, Cass Gilbert’s neo-Gothic Woolworth building built in 1913 was the tallest skyscraper in the world. New York had its “Cathedral of Commerce,” but the Second City would have a tower aspiring to the heights of journalistic truth. While historical precedent won this round, the competition inspired great debate about the design and function of skyscrapers in America for decades
to come.
After the Tribune moved out, developers Golub and Company and CIM Group decided to adaptively reuse the tower for luxury condominiums. Solomon Cordwell Buenz was the architect of record for the project, and they retained Klein and Hoffman to undertake a façade assessment. Klein and Hoffman, under the direction of Todd Gorrell, principal, and Michael Naponelli, senior associate, oversaw the assessment, project design, and rehabilitation of the façade from late 2017 until the project was completed in the spring of 2021.
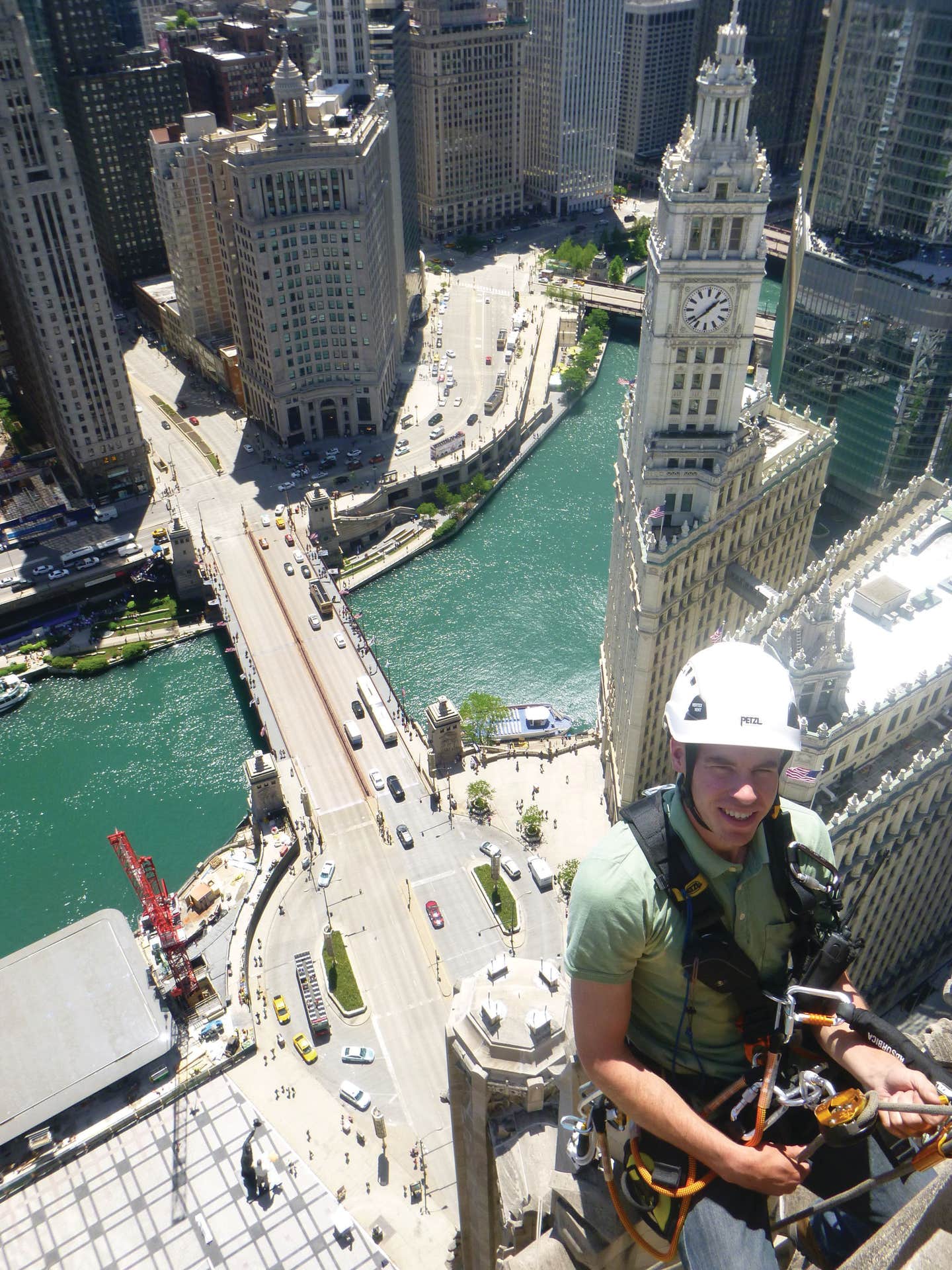
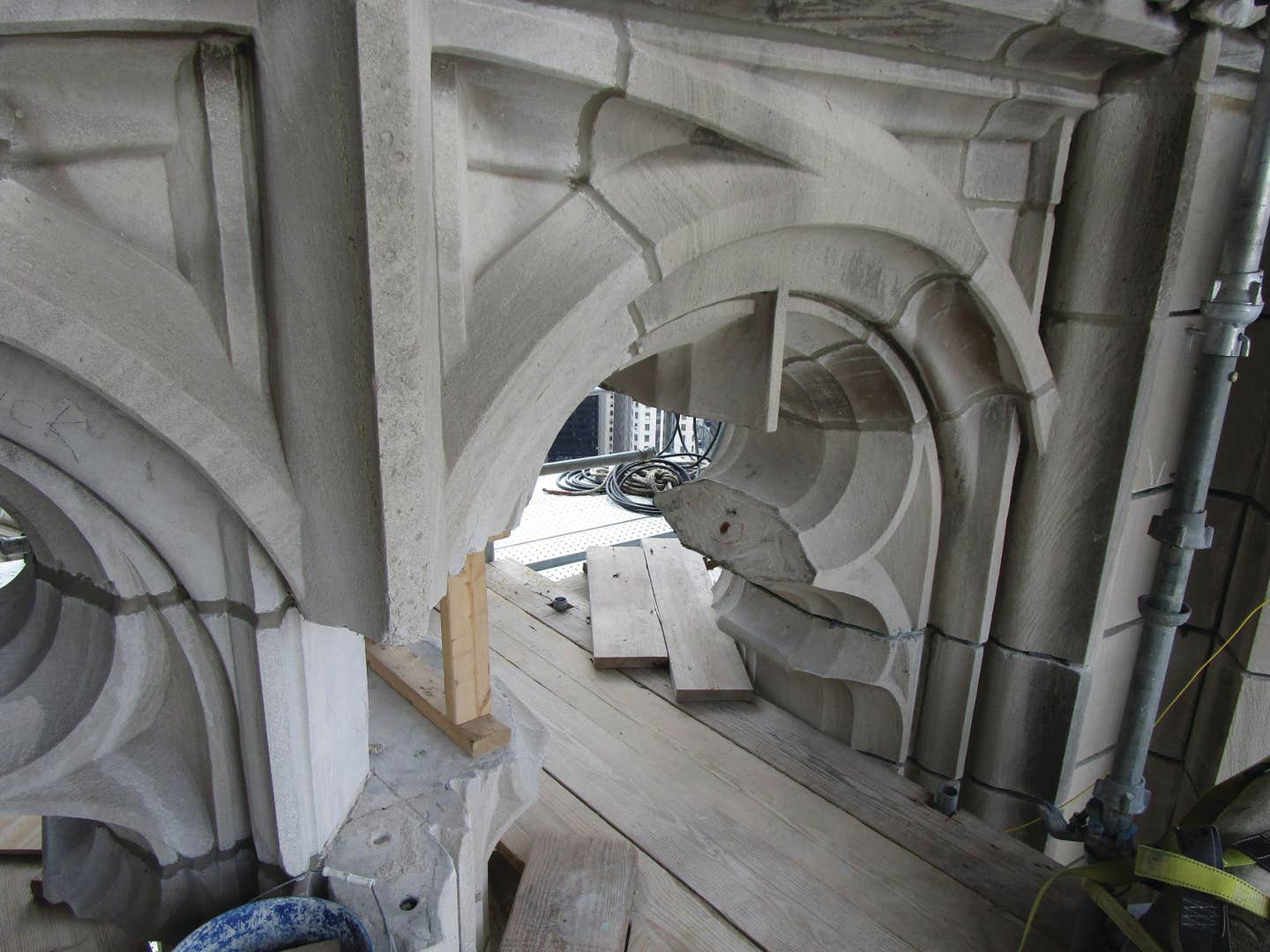
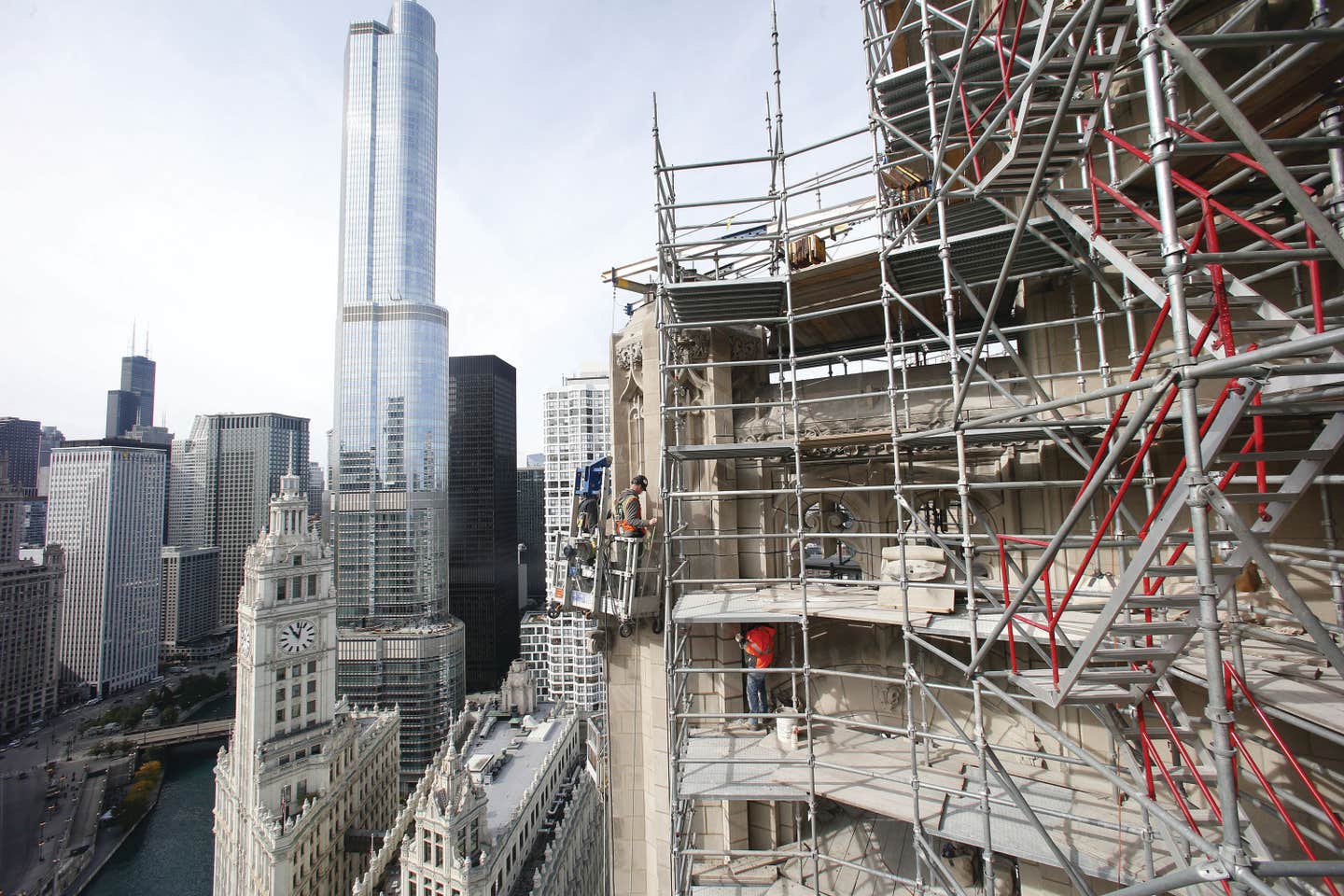

Gorrell and Naponelli explain that the entire project combined traditional building restoration practice and innovative technology from start to finish. The initial review of the project revealed that the steel frame was generally in good condition, with some corrosion. The portion of the building that had suffered the most was the area around the flying buttresses on the 25th floor. The decay was not a surprise given the degree of exposure for the ornamental buttresses at that elevation. They comprise an ornamental sculpture collection, nearly 300 feet in the air, subjected to Chicago’s harsh climate. Swing-stage scaffolding at that height was a costly investment to use during the investigation phase, so the investigation team from Vertical Access rappelled from the building with industrial rope.
Michael Naponelli explains that this process allowed for a very thorough review of the stone and steel deterioration. Targeted solutions could be developed since they were able to examine and photograph each problem and develop very specific recommendations for each repair. This careful attention to detail resulted in fewer unknown variables and better cost control. Removing and resetting all of the buttress stones to access the steel frame was going to be extremely costly, but they determined that the corrosion was not as severe as initially thought, and the team from Klein and Hoffman worked with ECHEM Consultants to develop a strategy for impressed current cathodic
protection (ICCP).
Todd Gorrell says that, essentially, cathodic protection uses a low voltage electrical direct current (DC) to interrupt the electrochemical reactions at the steel surface that causes corrosion and the subsequent accumulation of rust which will crack and displace masonry. At any height, but especially at this height, preventing falling architectural elements over a busy sidewalk is a paramount concern. This system allowed the historic masonry and ornamentation to remain in place, while mitigating corrosion and providing substantial cost savings over a traditional repair. MMO Sintered expanded mesh titanium probe anodes, with a ballast resistor, were selected as the most suitable anodes for historic masonry structures. The DC current is passed from the anodes as ionic current through the masonry to the steel, which receives the electrons and thus no longer self-consumes in the corrosion process. ECHEM Consultants, the designers of the system, continue to monitor conditions on a regular basis at the tower.
The façade assessment included mortar analysis from multiple locations on the project. Testing in a laboratory revealed an existing mortar similar to a Type O mortar was used throughout most of the buildings. Central Building and Preservation served as the masonry contractor on the project.
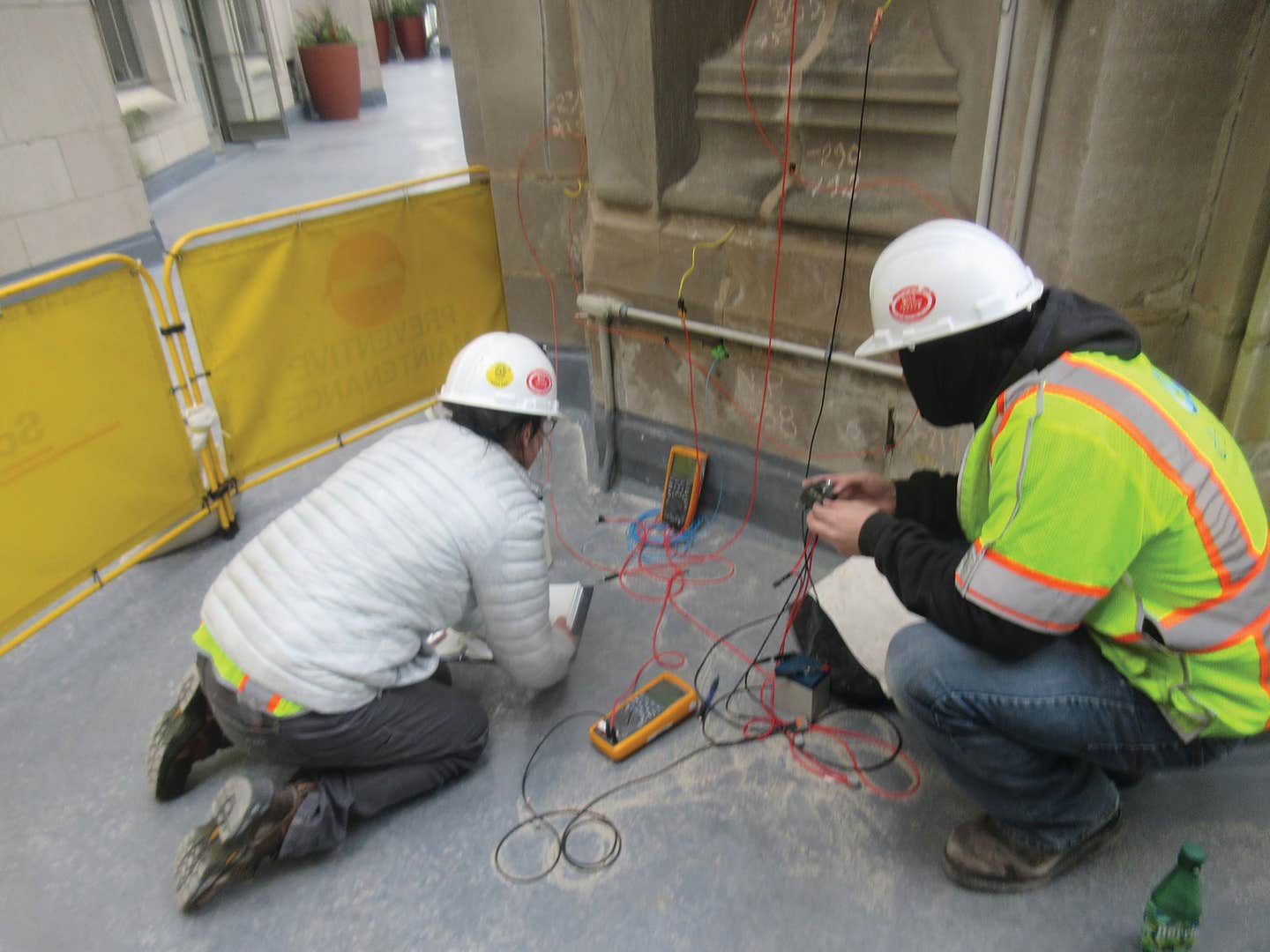
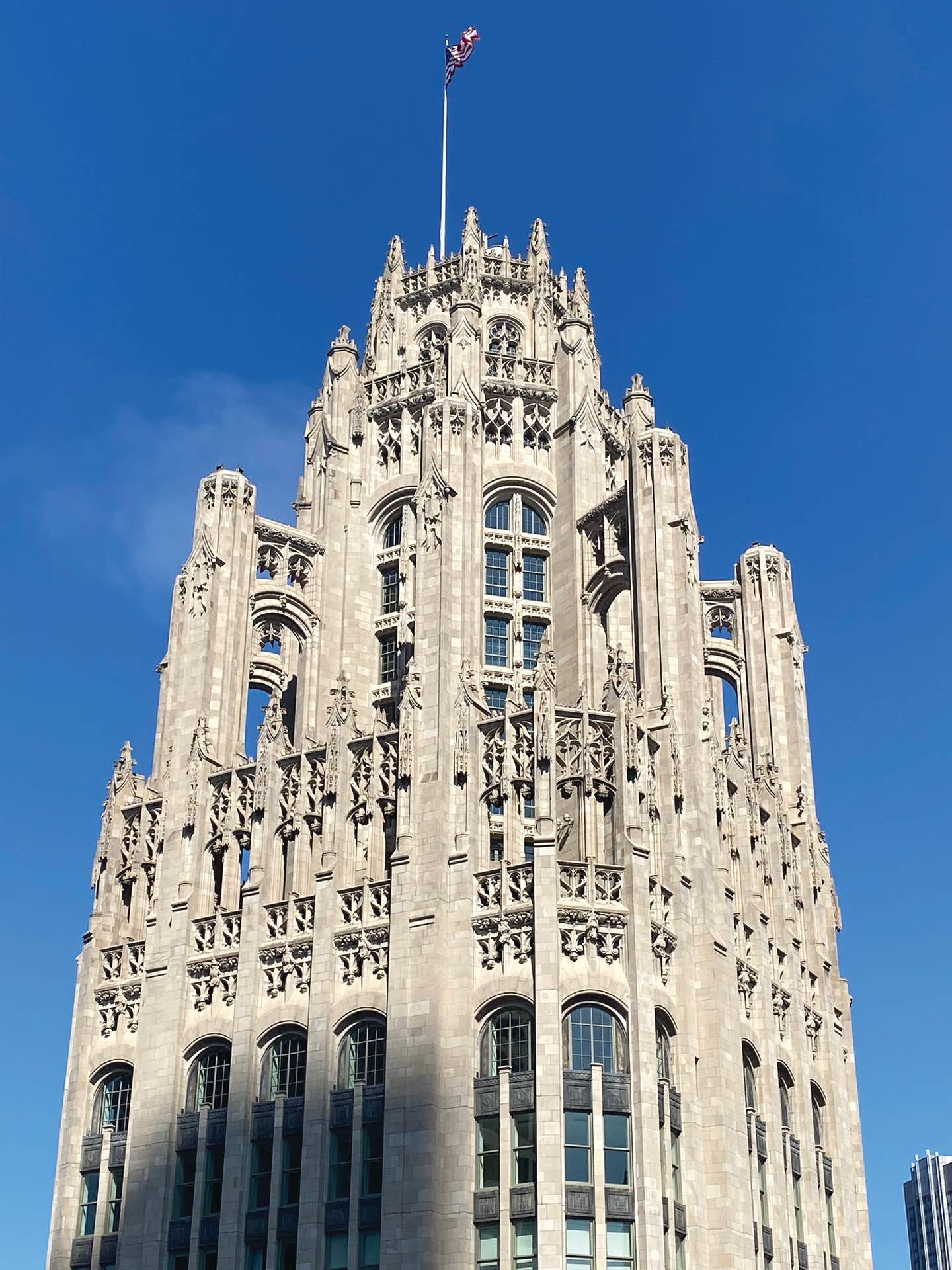

The Tribune Tower was built with random placement of multiple types and grades of Indiana limestone. So, when new stone was integrated into the historic building, multiple types could be used throughout, and the character and appearance of the building was maintained.
Another area of significant decay was found at the street level. Salt was particularly destructive to the limestone cornerstones. The original cornerstones had lost most of their detail, and recognition of the original builder and others involved in the construction of this landmark building was in danger of being lost forever. The team conducted research at the Chicago Public Library and was able to accurately reconstruct the names on the cornerstone. Carbon paper copying of the stones supported the sculptors from Galloy & Van Etten and Gary Galassi, who worked by hand to create exact replicas.
Both Gorrell and Naponelli noted that the extant historic drawings of the building were a big help for much of the project, but they noted that when the decision was made to adapt the street level of the building into retail spaces with 18-foot glass storefronts, the conditions were very different from those depicted on the historic drawings. They had to work with the design team to adjust the structural needs based on the actual conditions found. It was a temporary setback, but one that surprised them, as they have frequently found architectural drawings of the early 20th century to be reliable.
The façade rehabilitation was only one aspect of this multi-year adaptive reuse. The tower has been an important part of the Chicago streetscape for 100 years and this project has given the tower and related buildings the best chance for another 100 years. To get a glimpse of the Tribune Tower’s new life as a luxury residential building, visit tribunetower.com.
Gorrell and Naponelli praised the team of developers, architects, contractors, masons, subcontractors, and sculptors on this project. To learn more about them, visit their websites.
- Klein and Hoffman kleinandhoffman.com
- Solomon Cordwell Buenz scb.com
- Golub and Company golubandcompany.com
- CIM Group cimgroup.com
- ECHEM Consultants echemconsultants.com
- Vertical Access vertical-access.com
- Galloy & Van Etten galloyvanetten.com
- Gary Galassi Stone and Steel ggsas.com
- Central Building and Preservation centralbldg.com
Judy L. Hayward spends her days pursuing a passion for historic architecture and the ways in which it can be reused to sustain and grow healthy communities. She develops courses in partnership with builders, architects, traditional craftspeople and others to teach both historic preservation and traditional building skills. She has one foot in the nonprofit world as executive director of Historic Windsor and the Preservation Education Institute and the other foot in the world of media and information services as education director for the Traditional Building Conference Series and Online Education Program.