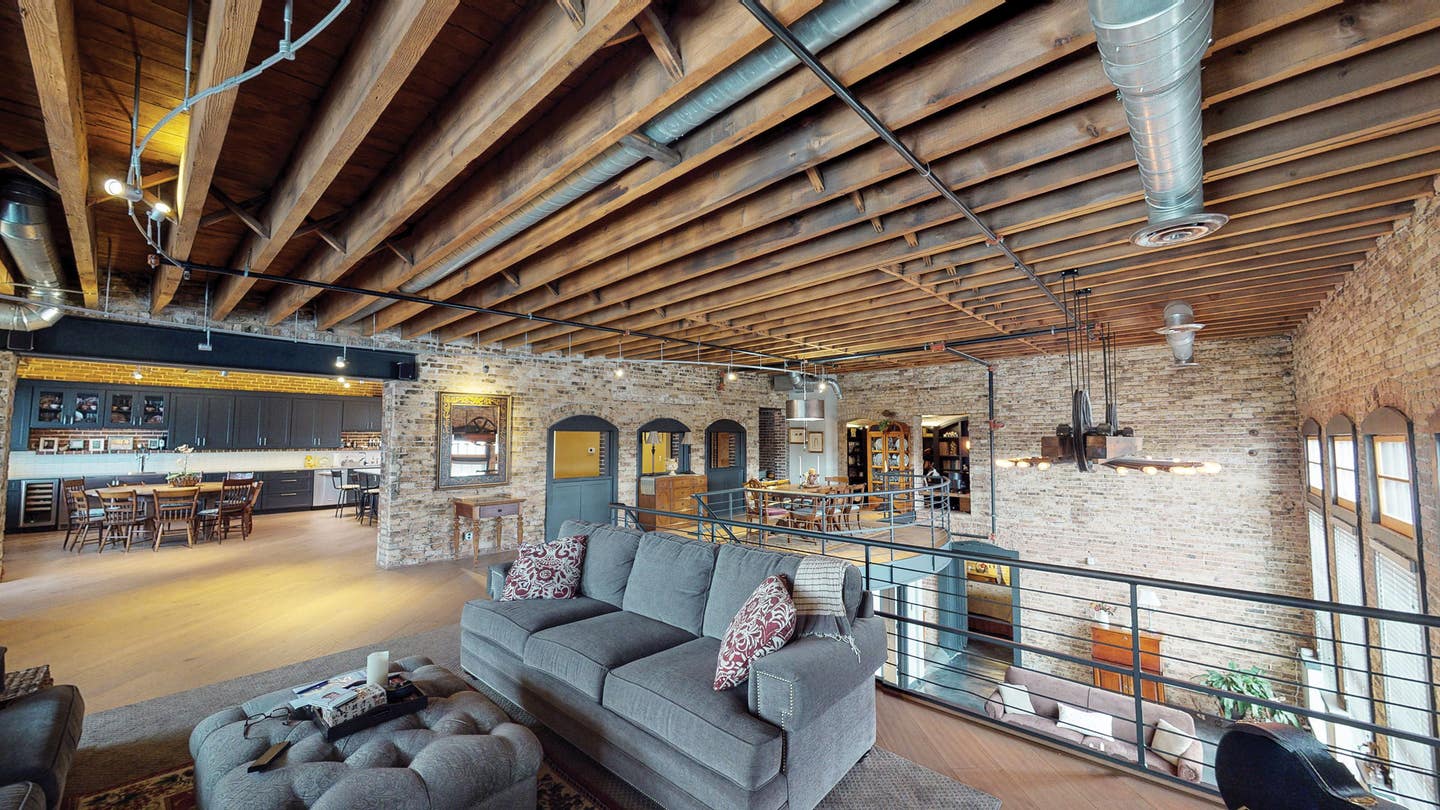
Product Reports
Energy Conservation
The Prairie Street Brewhouse is a remarkable multi-use building on the banks of the Rock River in downtown Rockford, Illinois. Gary W. Anderson, AIA, served as the architect for this 2015 award-winning project that combines a microbrewery, banquet center, and restaurant with offices on the second floor and luxury lofts on the third and fifth floors. The brewhouse comprises 81,000 square feet in the historic Peacock Brewery built in 1857 by English émigré Jonathan Peacock, with seven subsequent additions up until 1920. There have been only four owners in its 163-year history with a temporary closure during Prohibition, but today the site is thriving again with an innovative, adaptive reuse project that qualified for federal and state historic tax credits.
Anderson noted that in the past decade, the City of Rockford has made an intentional effort to get people back into the downtown. The reuse of upper levels for office and housing has gone hand in hand with a revival of restaurants, retail, and riverfront vitality for this city of 150,000 people. What he describes is not so much a story of which came first, but how the mixed-use approach is revitalizing this downtown by bringing people and activity side by side. He says downtown is now as busy on early Saturday mornings as it is during business hours and nighttime recreation. The active presence of people among the renovated structures has changed everything. Anderson even moved his office into the second floor of the brewhouse and became an owner/investor.
Anderson says the results of the geothermal system are even better than he expected. “The biggest hurdle was getting city officials to believe the technology would work,” he says. “This was a complicated project that needed to provide comfort 24-7 for a variety of users on multi-levels. Even on a morning when the temperature outside was flirting with 30 below zero, the building was comfortable. And now with the pandemic, more tenants have opened windows and doors for ventilation, and yet the air conditioning provided by the geothermal system is still working just fine.”
Anderson explains the technical specs of the system and how it was integrated into this industrial giant. “The goal was to reduce energy consumption with an open loop geothermal system. Two 100-foot wells were drilled to reach a shallow aquifer directly below the adjacent river. The pump and dump system is well within the EPA temperature limits of returning the water to the river. It is important to note that the pumps have variable speed drives, and they may only operate 50 to 60 percent in a 24-hour period depending on outdoor temperatures. Balancing the building loads of a mixed-use building have added to the economic return. All the building refrigeration for the restaurants and brewery are on the geo system. The energy costs on a square-foot basis for the past five years have been 60 percent less than a conventional system. The initial installation costs for the open loop system were nearly the same as a conventional system.”
From the Top Down: Insulated Roofing
A good roof is still the best defense against the elements, and combining one with a sound insulating strategy can become the best offense in mitigating heat loss.
Lupton Hall on the campus of Farmingdale State College in Farmingdale, New York, on Long Island was designed by Max O. Urbahn in 1945. Today the 80,000-square-foot, brick and stone building houses the architecture program, construction management studies, and related building technology programs. It was designed with Prairie School features including a roof with a large overhang and contemporary interpretations of clerestory windows. And while the building is not listed on the National Register, the college wanted to keep the historic character of the roof shape—arguably its most character-defining feature. The roof had been plagued with leaks, ice dams, and icicle formations at the perimeter, and there were no gutters or downspouts to divert water away from the building. They were concerned about heat loss through the uninsulated roof. The college commissioned Hoffmann Architects from New York to conduct a thorough building evaluation.
The existing attic space could not easily accommodate continuous insulation, so some increase in the thickness of the roof would be required for a new ventilated and insulated roof assembly secured to the top of the existing roof structure. Architect Richard Off, AIA, noted that the existing framing was in remarkably good condition, consisting of steel rafters with concrete decking. Even the paint was still sound after nearly 75 years of service. The applicable energy code requires improved R-value performance, so the decision was made to install a new, 11-inch-thick assembly to accommodate mineral wool insulation, provide an uninterrupted air cavity, and allow a new nailing surface for underlayment and copper installation. Mineral wool would not be damaged by moisture that might enter the cavity and offers some fire protection of the framing for the new assembly. The new air cavity extends from the eaves to the newly ventilated roof ridge to keep the roof cool and help prevent ice dams from forming. To achieve this continuous ventilated and insulated assembly, a portion of the roof’s eave structure was removed and reconstructed. If this had not been done, the roof overhang would have increased from just over two feet to nearly four, and Off and his team from Hoffmann Architects felt this would alter the appearance of the roof too much. Reconstruction of the eave also allowed for the installation of a new built-in gutter and downspout system to properly address drainage.
There were significant structural challenges. Additional weight was a concern and was addressed by using lightweight galvanized steel framing positively secured to the existing steel structure with stainless steel bolts to reduce the likelihood of thermal bridging and condensation in the new roof assembly. This was done in lieu of heavier fire-treated wood framing, which also allowed insulation batts to be placed more closely and continuously. This new metal framing ensured the new fire-treated sheathing/nailer boards were properly supported and appropriately anchored against high uplift loads found on Long Island, and also allowed for the installation of a brass snow guard system to protect gutters and adjacent paved areas, against potential snow and ice accumulations at the roof. Off explained that “Installing this new framing and increased roof assembly thickness became especially complex around the roof’s existing chevron-shaped dormers, louvered hip ends, and reconstructed eaves and ventilated ridges; however, producing a series of large freestanding mockups of the replacement system during the submittal process allowed the design and construction team to resolve detailing concerns without making costly and irreversible mistakes in the field.”
Given that the existing roof is not currently insulated and has a thin existing assembly with multiple thermal bridges, this copper roof replacement and assembly and structural retrofit not only addresses leaks, drainage, and mitigates winter problems but should also increase the annual energy savings for both heating and cooling, and should help reduce overall operating costs for the building.
Judy L. Hayward spends her days pursuing a passion for historic architecture and the ways in which it can be reused to sustain and grow healthy communities. She develops courses in partnership with builders, architects, traditional craftspeople and others to teach both historic preservation and traditional building skills. She has one foot in the nonprofit world as executive director of Historic Windsor and the Preservation Education Institute and the other foot in the world of media and information services as education director for the Traditional Building Conference Series and Online Education Program.