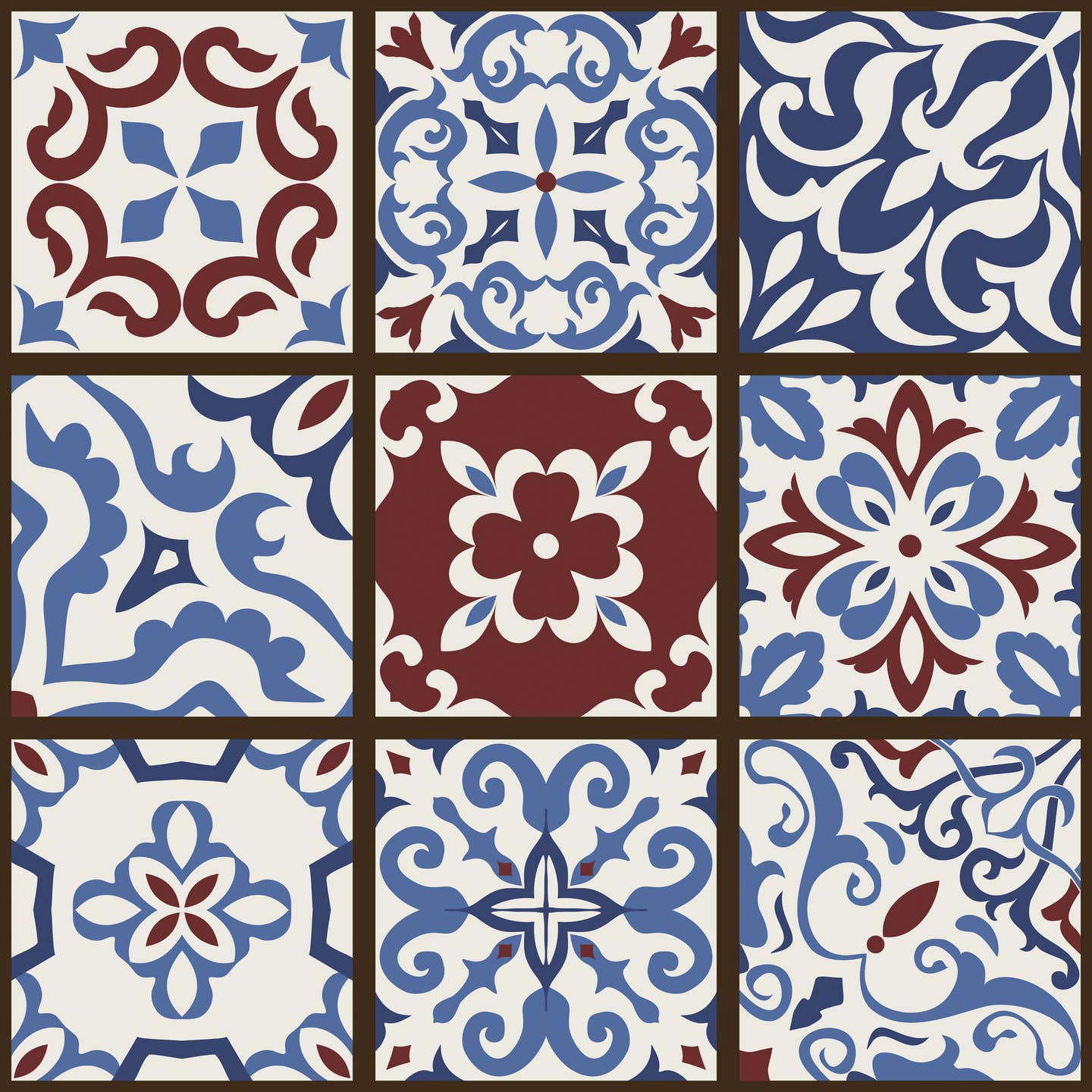
Product Reports
Encaustic Tiles: The Color is in the Clay
Looking down at floors can be an uplifting experience in historic buildings. Parquet, period carpets, marble, and the subject of the article—encaustic tiles—provide a rich legacy underfoot.
Encaustic Tiles, Medieval Craft to Manufacturing
The Gothic Revival in England renewed interest in many traditional crafts of the Medieval period while the country simultaneously became a world leader in manufacturing, playing its part in the Industrial Revolution. The process to make encaustic tiles has its origins in Medieval inlaid tiles. Inlaid tiles were made by stamping a design into the clay and filling the indentations with a white liquid clay or slip. They were covered with clear lead glazes that resulted in a nutmeg-colored background and golden decoration. Tile making thrived in many forms throughout Europe but especially in Holland, Italy, Spain, and France. Faience, Majolica, and Delft exemplified regional traditions as the Renaissance blossomed. The term, encaustic, is something of a misnomer when it comes to tiles. In painting, encaustic refers to mixing pigments with hot wax, but encaustic tiles are created essentially in a dry process with some light moisture. The process capitalizes on the natural colors found in the clays. They often feature two colors in earth tones, but more colors are possible depending on the use of glazes.
Herbert Minton (1793-1858), son of Thomas Minton, a renowned potter from Stoke-on-Trent, recognized a growing need for inlaid tiles for restoration projects of great cathedrals and new Gothic Revival churches. According to author, educator and historian, Hans Van Lemmen, Minton bought a share of the patent taken by Samuel Wright of Shelton, England around 1830. Around 1840, he purchased a share in Richard Prosser’s patent for machine processing of clay dust patterns.
In 1841, Minton got an order to supply tiles to repave the floor in Temple Church in London. Architect Augustus Welby Northmore (AWN) Pugin (1812-1852) began to design tiles for Minton and his own church designs in the 1840s. He designed them for the new Palace of Westminster as well. Prosser’s machine process allowed for the production of tiles with slightly moist clay in large quantities and thus, a craft-based, machine-made industry was born. From country churches to fireplace surrounds in elegant 19th-century parlors, encaustic tiles were in demand. In 1845, he formed Minton, Hollins and Company for the purposes of making tile.
Resources from the UK to aid in research
Van Lemmen maintains a website that features extensive historical information on all kinds of tiles. He is also the president of Tiles and Architectural Ceramic Society (TACS), a UK–based organization that maintains a website, with many resources as well.
Van Lemmen’s website states, “An encaustic tile (sometimes also called inlaid tile) is one in which the design is reliant upon the contrast of coloured clays let into the body of the tile, rather than surface decoration.” He notes that, “Minton & Co and Chamberlain were the first firms to manufacture replicas of medieval tiles successfully. Chamberlain covered their encaustic tiles with a transparent glaze, but Minton devised a method of heightening the effect of the inlaid design with a yellow enamel glaze, leaving the body of the tile unglazed.”
The English companies that dominated the manufacture and worldwide distribution of the tiles certainly shipped tiles to America. For example, Minton tiles are found in the US Capitol.
Tile Production in the United States
According to National Park Service Preservation Brief 40, Preserving Historic Ceramic Tile Floors, at least 25 U.S. Companies produced encaustic tiles prior to 1894. Bennington Pottery in Vermont made encaustic tiles as early as 1853. By the 1930s the Zanesville, Ohio–based American Encaustic Tile Company, founded in 1876, had become the largest tile manufacturer in the world until it closed in 1935, a victim of the Great Depression.
Art pottery flourished in America during the Arts and Crafts movement. According to architect and biographer, Ethan Anthony, Gothic Revival architect Ralph Adams Cram favored Moravian Tile Works’ tiles for their quality and durability even though they were not encaustic tiles; furthermore, they were made in the United States and were less costly to ship, saving his clients’ money. By the turn of the 20th century, encaustic floor tile was eclipsed by white and colored ceramic mosaic tiles. Today encaustic tiles are usually made of concrete, but it is possible to find Victorian reproductions or to source reclaimed period tiles.
Durability, Maintenance, and Repairs
Encaustic tiles are very durable because their color is part of the clay. They stand up well to lots of foot traffic and usually require gentle cleaning with water-even a damp mop will work well after vacuuming. Preservation Brief 40 has guidance on cleaning as does a technical paper prepared by the Leslie Durbin Jackfield Conservation Studio. (The paper is available on the TACS website noted in additional resources.) Both publications stress testing in discreet locations if chemicals are used for cleaning or stain removal. Careful diagnosis of any stains is warranted before attempting treatment. While wax and linseed oil were used historically on encaustic tiles for protection, wax is not really needed but can be used. Linseed oil has proven to attract dirt and cause discoloration; its use is not recommended today.
If the floor requires extensive repair or replacement, contacting a ceramic conservator or experienced tile setter is advised. It is easy to damage adjacent tiles when trying to replace a single damaged tile, so consider your options carefully because repairing with a pigmented epoxy or regrouting may cause less damage. Always try to preserve the historic tiles first.
Encaustic Tile Resources
Judy L. Hayward spends her days pursuing a passion for historic architecture and the ways in which it can be reused to sustain and grow healthy communities. She develops courses in partnership with builders, architects, traditional craftspeople and others to teach both historic preservation and traditional building skills. She has one foot in the nonprofit world as executive director of Historic Windsor and the Preservation Education Institute and the other foot in the world of media and information services as education director for the Traditional Building Conference Series and Online Education Program.