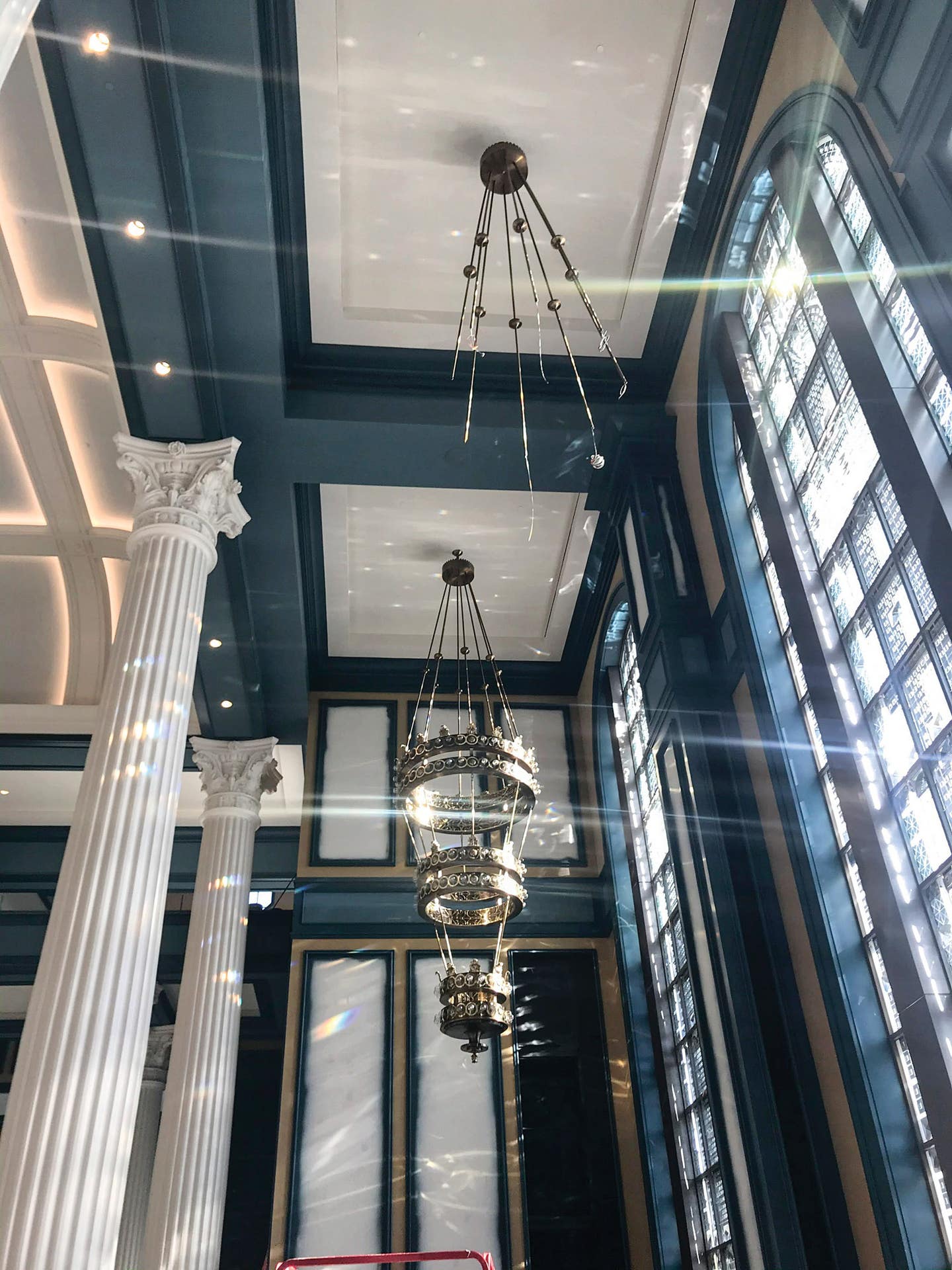
Product Reports
Crenshaw Lighting’s New Fixtures for a Performing Arts Center
Some say size doesn’t matter, but when it comes to creating colossal chandeliers, it can certainly have an impact. That was experience of Crenshaw Lighting of Floyd, Virginia, when commissioned to build towering light fixtures for the new Performing Arts Center at Belmont University in Nashville, Tennessee.
“The sheer size and number of light sources would likely illuminate the room pretty well,” explains Bryan Wood, vice president of operations at Crenshaw, “but each fixture is much more an architectural piece than, say, an example of performance lighting.” Working closely with Randy Burkett Lighting Design, Inc. and ESA architects, he says the thrust of the design is about fitting the space.
Fitting this space, however, was a very tall order. Scheduled for completion in late 2021, the Performing Arts Center will be a 1,700-seat multipurpose facility and “the most extensive suite of venues of any institution of higher education,” according to the University. “The space itself is tremendous, with a three-story high entrance hall,” says Wood, “so obviously to maintain proportional scale, these fixtures have to be huge.”
Indeed, the first hurdle Crenshaw faced is simply handling the gargantuan girth of the largest fixtures. Seven feet at their widest diameter, and 30 feet from the ceiling mount to fixture bottom, the assemblages of brass rings and hardware are massive. “These chandeliers weigh in at around 2,000 pounds apiece, so even their internal structure has to be designed by our in-house mechanical engineer.” As Wood explains, a typical job takes a week in their engineering department; these particular fixtures spent about a month there just due to the weight and size. “We have to make sure these fixtures can hold themselves up to the ceiling, and that Belmont’s building can support this load.”
What’s more, the three largest chandeliers are designed to be part of a family of fixtures, a constellation of sorts. “There are smaller versions of the giant, three-tier RA fixtures that only use two tiers, and there’s a single-tier version,” says Wood. “Soon, we also start production on some very large, two-tier wall sconces that share a lot of the same design elements.”
Creating the mammoth fixture parts had its own learning curve. “Each individual brass ring weighs about 400 pounds and required custom-made cradles so our forklift could move them around the shop.” Just getting them into the building he says meant custom pallets that could support the weight of the fixture, but still be tilted at a 45-degree angle.
The decorative castings were another exercise in invention. “You know, Crenshaw has spent decades in the replication and restoration business, so typically we have originals to go by, but for some of these castings and ornate details we had to start from scratch, making the patterns ourselves.” First, a staff sculptor (also a Crenshaw designer) hand-carved decorative elements from foam, which, after approval, would be 3D scanned. “We do have 3D software to do such modeling,” says Wood, “but when you need this kind of ornate detail, it takes someone’s hands to really bring that to life.”
Producing finishes got complicated too. The initial design concept was for each brass ring to have a two-tone finish—patinated on one element and high-polish brass on the rest. However, this became impractical to execute in a single casting. “So, we switched to layering multiple jet cuts, each with a different finish, to still give the appearance of a single casting,” says Wood. “If you view the fixture from, say, the floor level, you see the nice, patinaed brass in the pattern and then behind it all the polished elements just really pop out. Part of our end goal was to get the parts, each made at different times, all lined up and looking seamless.”
Other decorative details that are more than meets the eye are the rosettes encircling the rings. “They’re actually created from eight different castings,” explains Wood, “then layered and fastened together to look like they’re a single piece.” Each rosette component is made with lost wax casting, an ancient technique for reproducing intricate metalwork, such as jewelry. Here, wax or a similar substance melts away to leave a mold cavity. “Some of these rosettes carry features like 1/16”-thick ridges, which really shows out well, but there’s no way we could have held that detail with sand casting. Lost wax casting was the only option.” He says a Colorado company poured the actual castings, but Crenshaw made the rosette patterns themselves.
As contemporary and state-of-the-art as the fixtures appear, the lighting still evokes an incandescent ambiance. “The client wanted a globe feel to the illumination, so we went with a G-40 lamp. It’s LED technology, but with a medium base style that looks like a traditional globe bulb. This way, we didn’t have to add fitters that create bulk or thumb screws to hold on shades, which are not very pretty.” Circuitry allows the rings to be creatively controlled, selecting light levels or individual rings if so desired.
The result Wood says adds up to a beautiful fixture and an exciting project. “As it initially came to us, it was very well designed, and then we had the freedom to run with it a little bit.”
Gordon H. Bock is an architectural historian, instructor with the National Preservation Institute, and speaker through www.gordonbock.com.