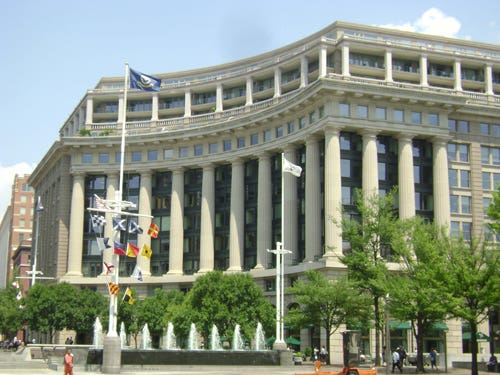
Product Reports
Building Column Construction: Materials and Methods
Contradictory as it seems, perhaps the most ancient and traditional of architectural elements – the column – can now be had in a cornucopia of increasingly high-tech materials, some best known only by confusing acronyms like GFRC and FRP. In reality though, builders have been searching for ways to build a better column since they first swapped tree trunks for rocks several millennia ago. The quest has a history of getting more complicated as time goes on, so if you face making a choice between “Column A” or “Column B,” first take a look at this quick rundown of the basic, non-metal building column materials currently on the market.
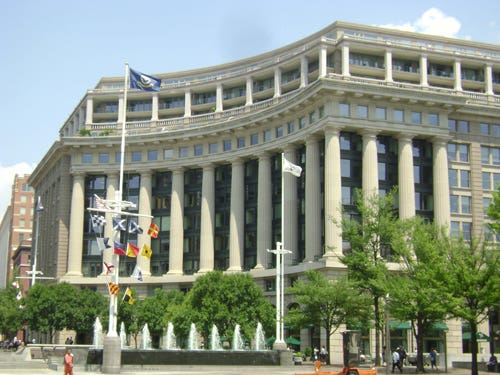

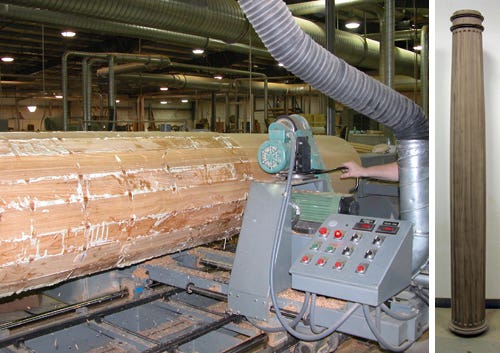

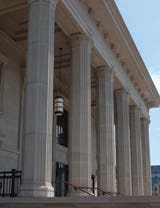
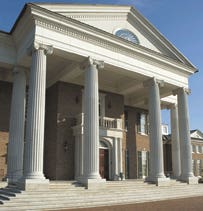
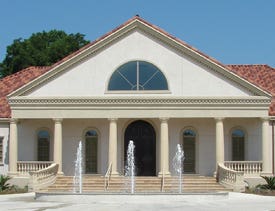
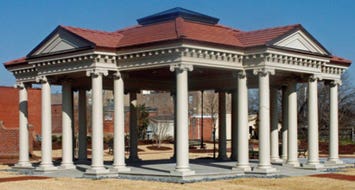
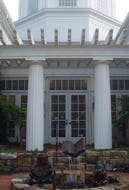
Stone Columns
When ancient Greeks first saw the monumental stone pyramids and structures of Egypt around the 6th century BCE, they quickly abandoned wood-column temple construction in favor of stone, eventually perfecting the sublime vocabulary of Classical column orders. Stone columns still command the timeless appeal of quality and permanence or, as put by William Bybee, president of Bybee Stone in Ellettsville, IN, “Whether the project is public or residential, when a client wants stone, they want stone.” As Bybee explains, if the project is institutional, stone is often specified to follow the rest of the building – to match other columns, for example, or details and materials on the building, such as stone lintels or quoins. However, stone columns are no less popular for new buildings of Classical or totally modern design.
Though solid-stone building columns have supported large structures for millennia, there is no modern rule-of-thumb on their load-bearing capacity and it is important to first consult a structural engineer. Beyond this, the dimensions possible with stone columns are almost as unbounded as their beauty.
Bybee notes that the fluted columns his company fabricated for Market Square in Washington, DC, are a towering 55-ft. tall. His shop works with three different size lathes – the largest of which can turn drums 10-ft. in diameter. Yet equipment is not what keeps stone columns in check. “When we get to bigger sizes,” says Bybee, “the quarry is the issue.” As he explains, quarries usually have a maximum on how big a piece of stone they can supply with a limit on flaws, “and naturally,” says Bybee, “the customer wants as few flaws as possible.”
Wood Columns
Stone may be the material of permanence, but America is a land rich in timber and for most of the 19th and 20th centuries the most commonly available columns were wood. By the 1980s, the introduction of man-made polymers, as well as changes at some of the venerable manufacturers in the industry, began to take their toll on the pre-eminence of the wood column, but several long-time manufacturers still serve the market.
According to Bob McVicker, general manager of Somerset Door and Column Co. in Somerset, PA, people choose wood columns because of the material’s traditional qualities. “If you knock on wood, it feels solid – no ping or hollow sound like metal or fiberglass.” He says that appearance is a big factor too. “In a lot of fiberglass products, you won’t find really square corners; all the details are relieved a little bit so they can be released from a mold. With a wood column, however, there is no mold; the corners and details are crisper.”
Not surprisingly, the clear, rot-resistant, domestic wood species once used to make building columns have changed over the decades. “Years ago, redwood was one of Somerset’s top sellers,” says McVicker, “but of late we’ve been working in Northeastern white pine, cypress, Spanish cedar and African mahogany for exterior columns.” For manufacturers like Somerset, who have been making wood columns for over a century, this has not reduced their capability.
McVicker reports that while Somerset’s traditional columns are single-piece and load-bearing, they can also accommodate modern building codes. “Where steel structure is required, we can manufacture split-for-assembly columns to wrap I-beams or steel posts,” he says. And size is not a hurdle either. Somerset, for example, can custom-manufacture both round and square columns 40-in. in diameter and to an amazing 40-ft. in length. Says McVicker, “As far as I know, we have the largest wood lathe in the United States.”
Cast Stone Columns
As long as builders have coveted the beauty and permanence of stone, they have also sought ways to circumvent its weight and difficulty to work and move. The historic alternative is cast stone, a varied class of masonry materials also called artificial stone and faux stone that is generally described as refined architectural concrete. Early types of cast stone date back hundreds of years, but modern versions became popular in England in the 1820s and incorporate ingredients such as white and grey cement, crushed or natural sand, crushed stone and mineral coloring.
As Mel Fuller, president of Melton Classics in Lawrenceville, GA, explains, “The beauty of a cast-stone column is that it is not solid like natural stone, but essentially a shell, normally 3 inches or 4 inches thick.” In contrast to poured concrete, cast stone is typically made with a “dry” or “earth-moist” mortar consistency – that is, a low water-to-cement ratio. Also, since a cast-stone column is a hand-packed material, it is very consistently dense, so it resists cracking and spalling.
“A precast concrete building column, or other wet-cast product, is inexpensive, but it has to be kept sealed,” says Fuller. “Otherwise, once the concrete absorbs moisture and freezes quickly, the expansion of the ice will crack the product. Cast stone, on the other hand, generally doesn’t have those sorts of characteristics. Because of the way it is manufactured, cast stone is very dense, so it doesn’t absorb moisture much and it holds up over time.”
GFRC Columns
First developed by the Russians in the 1940s, glass fiber reinforced concrete (GFRC) employs lightweight fibers to significantly increase the qualities of precast concrete, a process now common for architectural elements, statuary and exterior building façade components, such as wall panels that simulate limestone. In manufacture, long or short high-strength glass fibers are embedded in a cementitious matrix to add tensile strength and load-bearing capacity. According to Fuller, the mix for making columns “has a little polymer in it, and fiberglass, and concrete aggregate. Then it is sprayed up into a mold to give you the look and feel of stone – and if you want, the color too, but it can also be done in paint grade.”
FRP Columns
After World War II, fiberglass found many new uses, especially when embedded in polyester or epoxy resin. These are generally categorized under the heading FRP (fiber reinforced polymer), though the actual formulations and manufacturing techniques vary with the products, manufacturers and time. Because it is strong and waterproof, FRP helped propel the postwar popularity of leisure products formerly made of wood, such as boats and skis, and by the 1990s it had found a natural application for manufacturing columns. Today FRP columns are made with two basic processes.
Columns that are filament-wound employ a technique widely used to manufacture cylindrical products where, as glass fibers are coated with resin, they are wound around rotating mold or mandrel, often with a carefully controlled orientation. “You are creating a relatively thin shell,” says Fuller, “about 3/16-in. thick in a 24-in. diameter, but it makes an extraordinarily strong column.” Filament winding is used to produce pipes and other industrial products and, Fuller adds, “It’s actually the same material used in ICBM missile cases.” Jeffrey Davis, president of Chadsworth’s 1.800.COLUMNS in Wilmington, NC, adds, “Filament-wound columns are also similar in technology to the large water slides seen at water parks.”
Needless to say, excellent compressive load strength at relatively light weight can be handy. As Fuller explains, “Suppose you need a load-bearing column that’s 36-in. in diameter and 24-ft. tall. With a GFRC or fiberglass composite column, you are talking about a lot of weight and that is not always an option. In such a case you might consider a wound fiberglass column. And if there are uplift or shear considerations, you can install a piece of steel in the column as well. ”
Columns that employ chopped or matt fiberglass are typically manufactured similar to boats, where the glass fibers and resin are laid into a mold, then unmolded when the resin is hard. Chopped/matt fiberglass columns generally are made in halves, so they can be released from the molds. Column halves may be assembled later around a structural member, or they may be assembled in the plant and beefed up to make them load-bearing. In contrast, filament-wound columns are made as an entire cylinder that is completely sealed all the way around.
Composite Fiberglass Columns
The latest advance in the FRP column, which first appeared in the market in the 1980s, is what is often called the composite column. Ingredients and names vary with each manufacturer but, according to Fuller, “We essentially combine limestone marble dust, polyester resin and fiberglass, and then rotocast that into a column.” In rotocasting, the mold is spun so that centrifugal force drives the casting mixture into the outer circumference of the mold – the detailed finished surface of the future column – until the mixture hardens. Including stone dust conserves expensive resin while adding mechanical advantages and improving appearance. “The finished product has a composition similar to a bathroom countertop, but since it contains less resin than a bathroom countertop, it is harder, very impact resistant and will carry a lot of weight,” says Fuller. Composite columns are relatively inexpensive to manufacture, have shown good durability, and therefore have become very popular over the last 20 years. “When you tap on one,” says Fuller, “it even feels like stone.”
Gordon H. Bock is an architectural historian, instructor with the National Preservation Institute, and speaker through www.gordonbock.com.