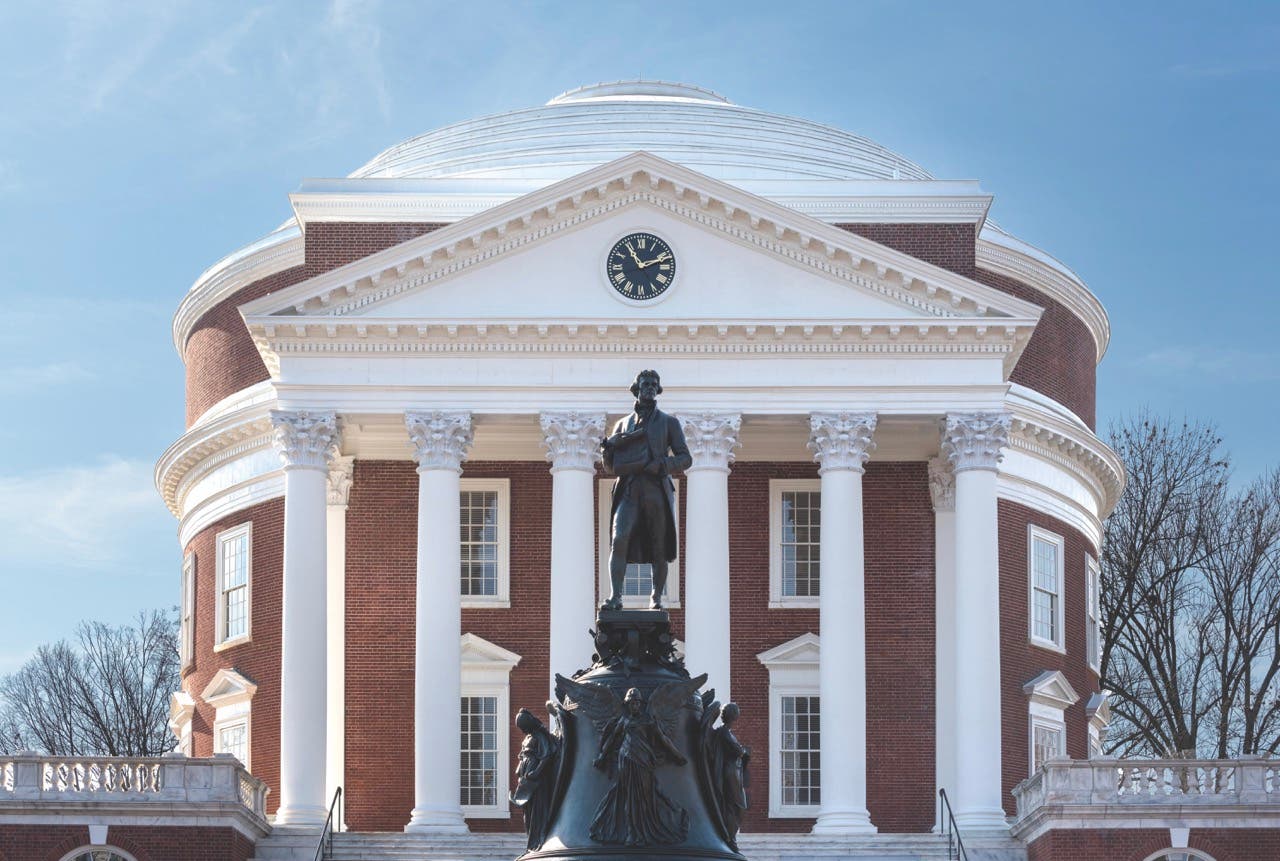
Product Reports
Classic Capitals Come Back
The 1828 Rotunda at the University of Virginia in Charlottesville is not only the centerpiece of the historic campus but also the quintessence of Neoclassical architecture in America. Designed by Thomas Jefferson and inspired by the Pantheon in Rome, it features 16 columns topped by marble Corinthian capitals, all but lost along with much of the Rotunda in a disastrous 1895 fire.
In 2006 when the University began to restore and upgrade the Rotunda, bringing back the immense capitals was a primary goal. “The originals were produced by the Raggi family, notable stone carvers in Carrara, Italy,” according to Rugo Stone in Lorton, Virginia, the company commissioned to recreate them. “The project is an ideal example of how modern machining combined with traditional hand-carving can produce highly ornate stonework in the 21st century.”
After the 1895 fire that left only the Rotunda’s brick walls, the university brought in architect Stanford White of Mead, McKim & White to restore the building. White took down the damaged capitals and put back uncarved blocks of what is believed to be a variety of Vermont marble, probably of pretty poor grade. Because of financial shortcomings, the university didn’t actually finish those blocks into capitals until almost five years later, at which time they were carved in place.
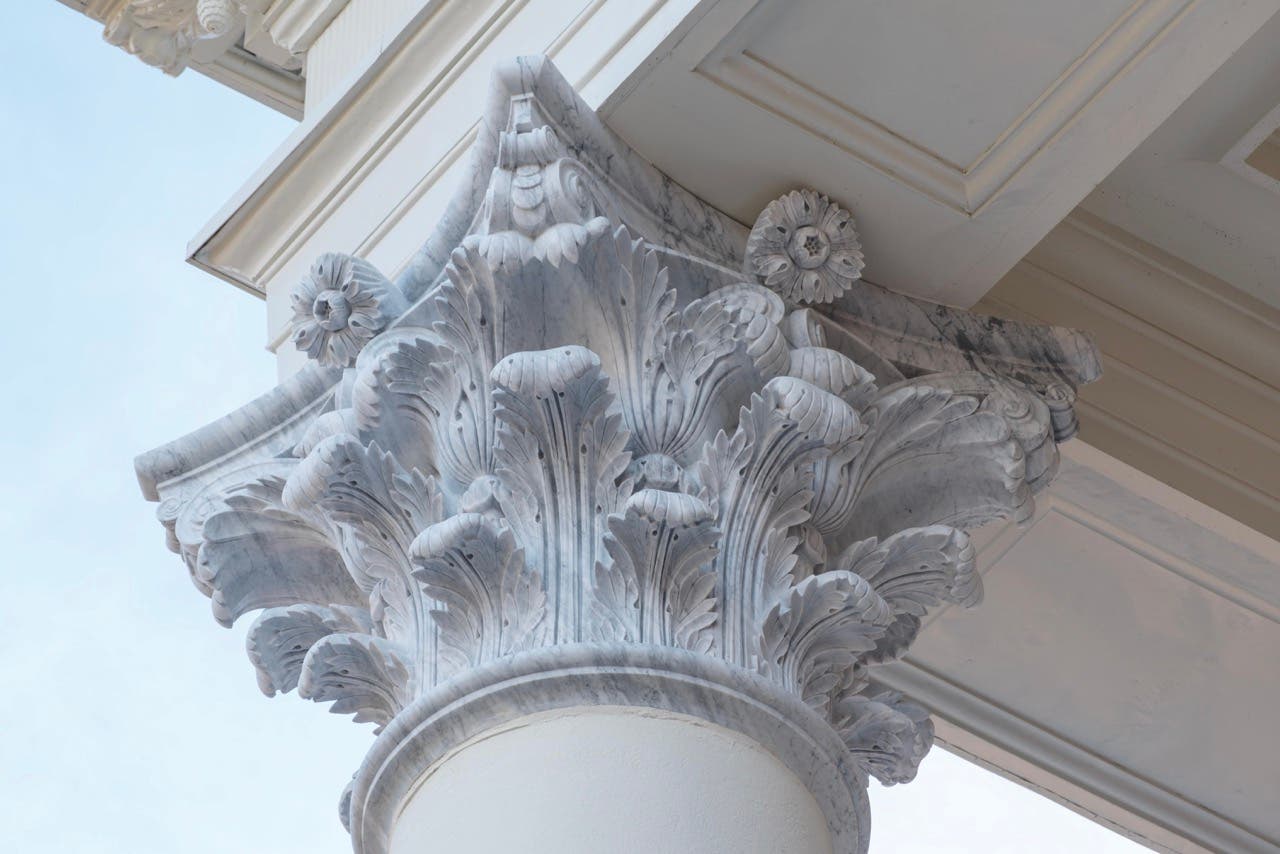
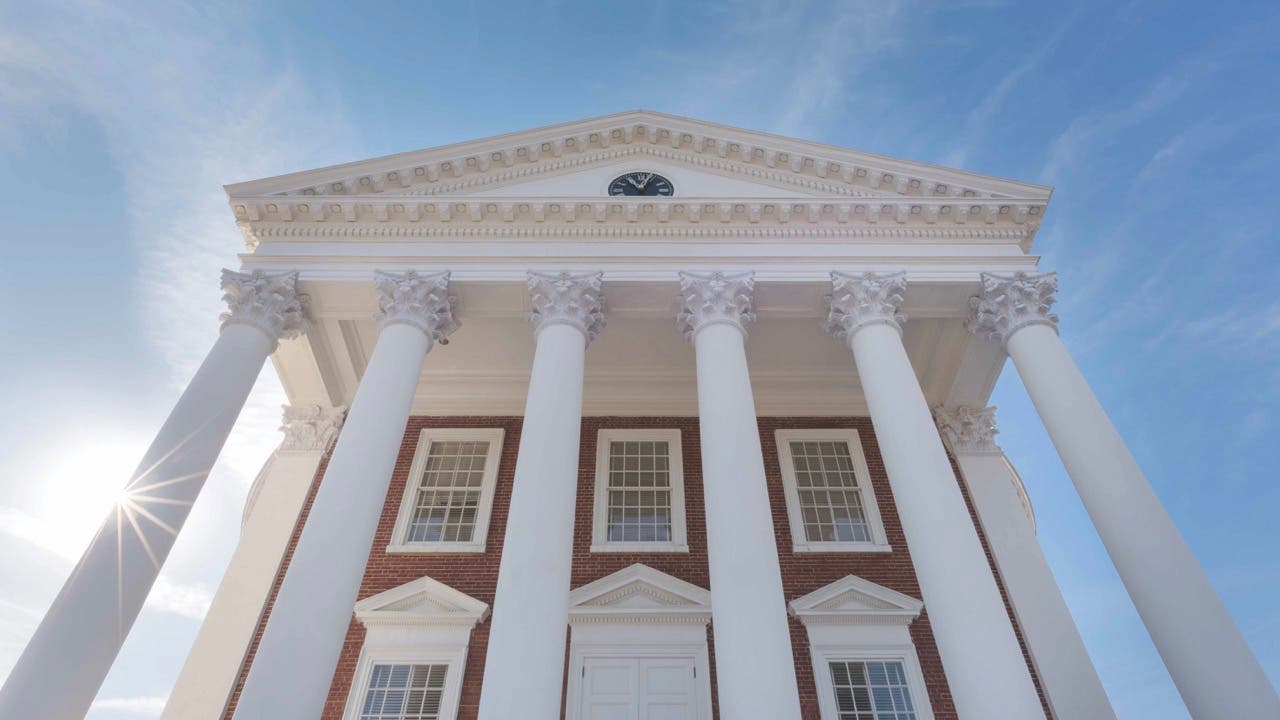
Unfortunately, the capitals did not weather well at all. The acanthus leaves began to fall off, presenting a potential life safety hazard, so the university planned to conserve the capitals and accept their visible deterioration as long as they could be made safe. However, the stone proved to be in such poor condition it became necessary to replace 10 capitals on the south portico and six on the north. In August 2013 Rugo Stone and their Italian partner, Pedrini, prepared a comprehensive proposal to replace the 16 marble capitals.
As the firm explains, since there was little remaining physical evidence of the original capitals, the overriding goal of the project was to replicate what Jefferson would have specified, and what the Raggi family—Jefferson’s contractors in Carrara—would have carved in 1825. Though the Raggi capitals were constructed in two pieces, the preference was to provide each new capital as a single piece of marble.
The hitch was, the best documentation of Jefferson’s capitals was only fragments from 1829 located around the campus. One, representing about one-third of a capital, stood in the university’s art museum, so the Rugo team was able to laser-scan that fragment, then have it replicated by CNC (computer numerical control) machining followed by hand-carving. For all other missing parts, the restorers turned to clay modeling based on surviving Jefferson-era fragments backed by very sharp, 19th-century, glass-negative photographs of intact capitals on the Rotunda.
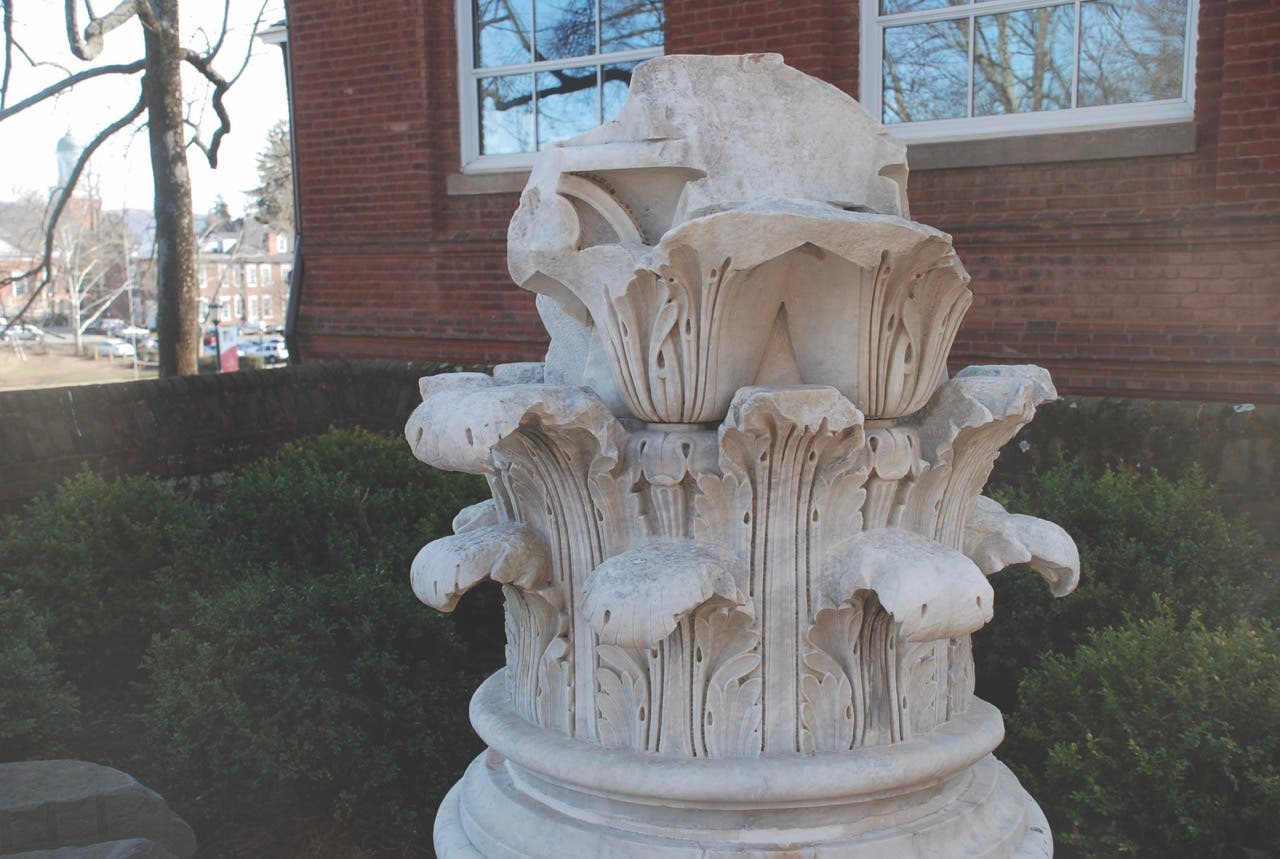
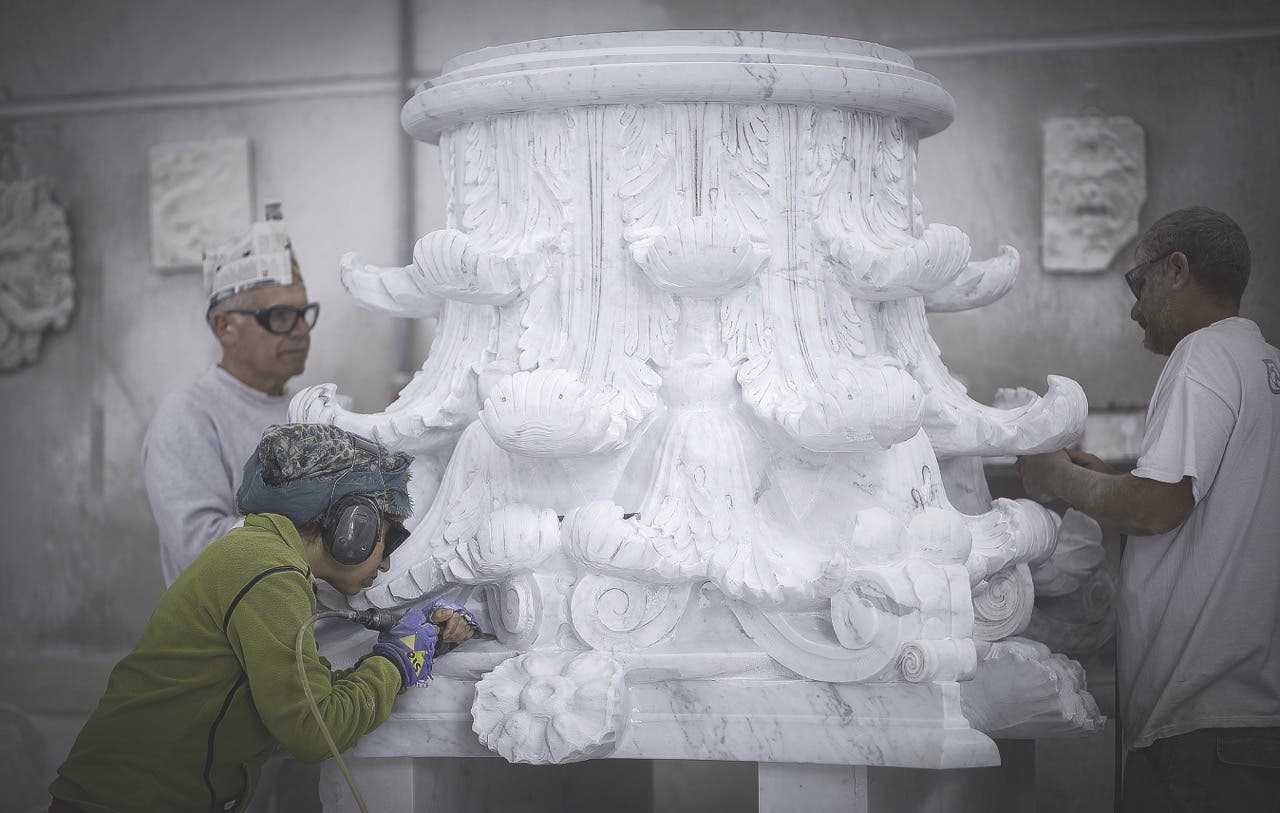
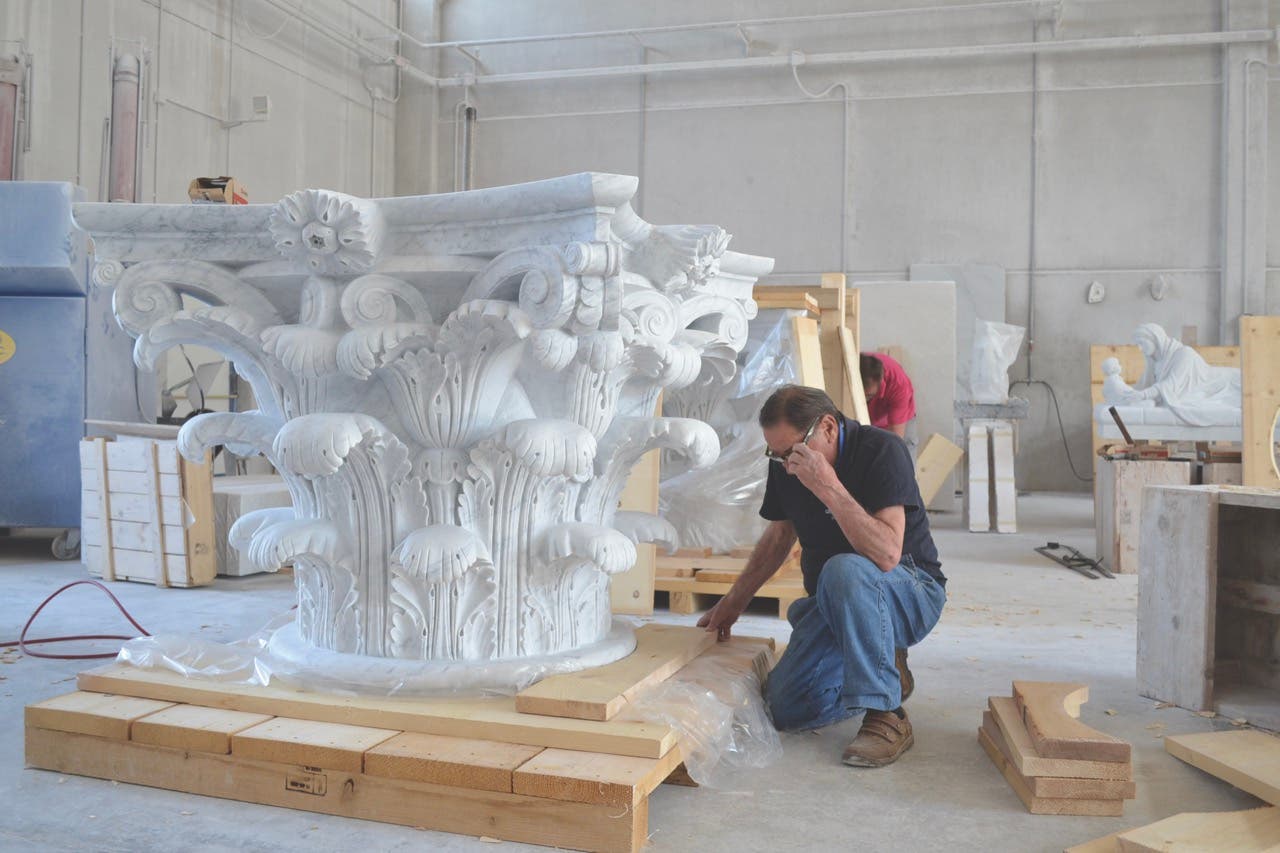
The first step was to 3D scan the existing partial base and fragments. This enabled the restorers to create a working 3D drawing of the lower portion of the capital, so as to size the capital and capture all of the various architectural nuances, such as the fragile acanthus leaves. “Carving these leaves has to create an organic flow,” according to Brett Rugo at the company, “where the spines of the leaves and the delicate tips descend downward.”
After developing the 3D digital drawing, the Rugo team prepared a full-scale, 2D hand drawing of the capital to be used by the design team to develop a proportionally correct upper section, which is more complex than the base portion. After the 2D drawing was approved by the university and a group including designers, architects, preservationists, and Jefferson scholars, the Rugo team carved a marble model of the lower portion of the capital in quarter-round. Then, in clay, they modeled the upper portion of the capital in a quarter-round on top of the lower marble portion to provide a full-height quarter model.
The quarter section composite model of stone and clay was then reproduced in Campanili Carrara C marble. “Campanili is the name of the actual quarry,” explains Rugo, “not a random choice among dozens of Carrara C quarries but a very high-quality type of marble.” He says they selected the best quarry based on decades of trade knowledge. Once the quarter-section marble capital was approved, the Rugo team produced the first full-round Corinthian capital that became the basis of comparison for the following capitals.
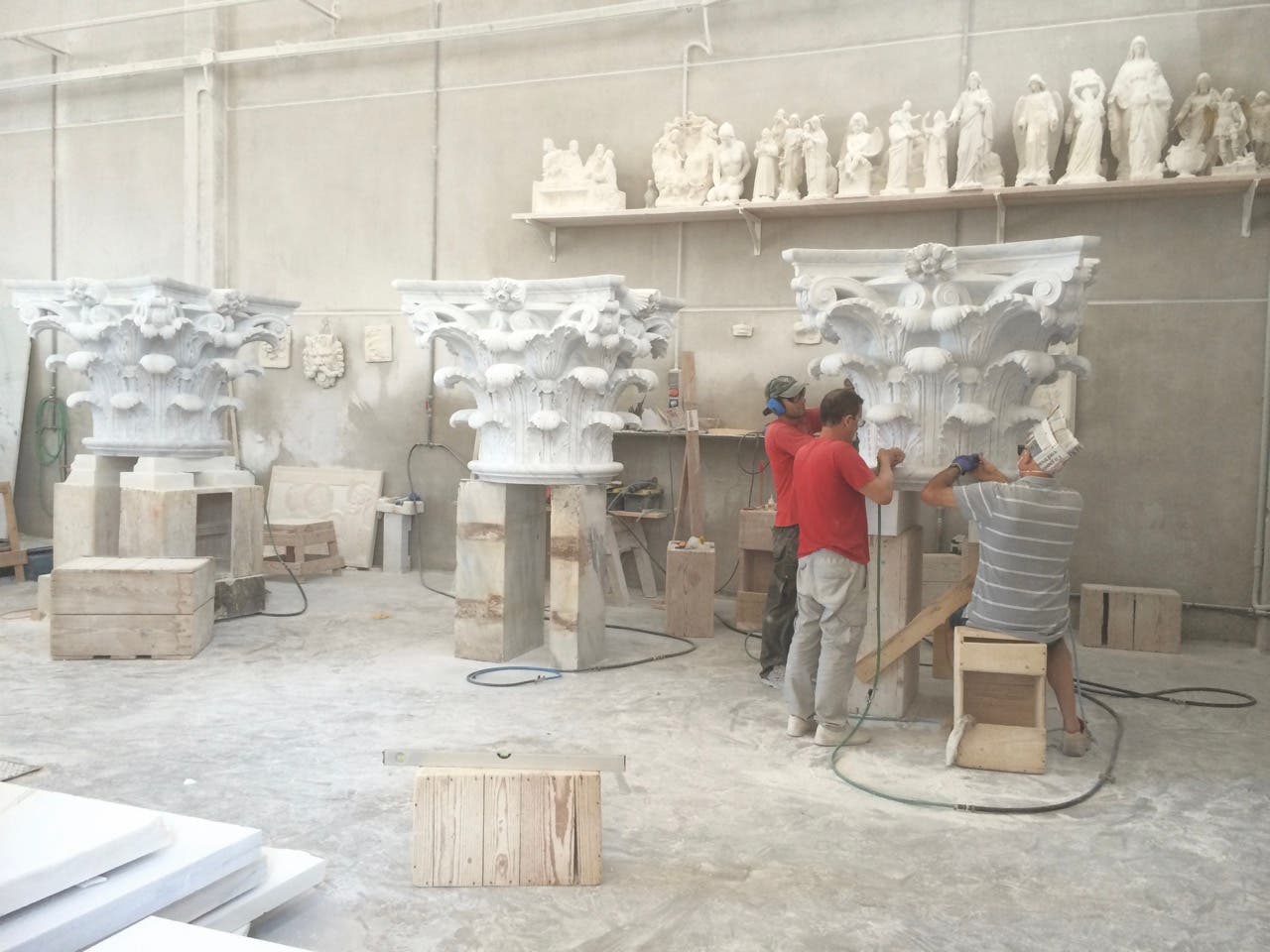
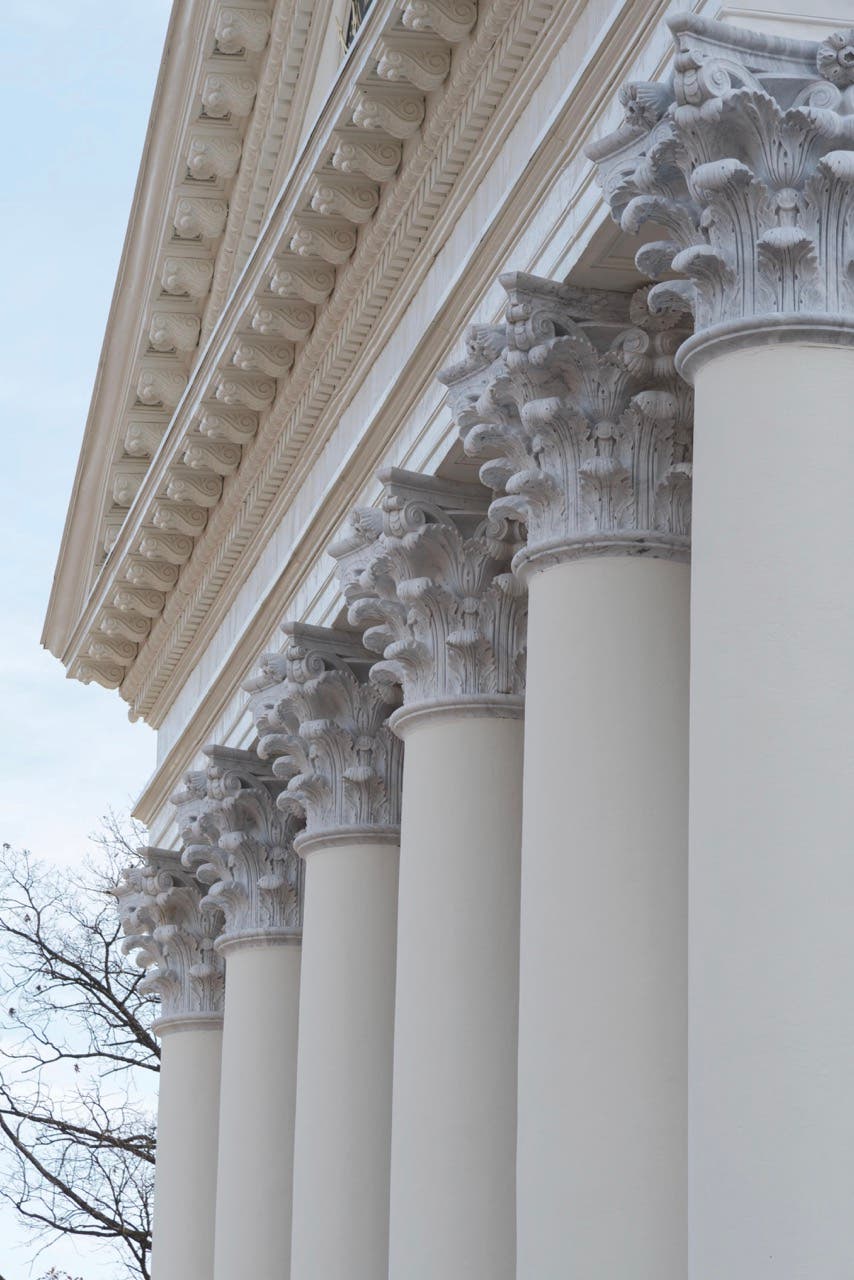
Over the next 10 months, the Rugo team employed two, six-axis robotic machines in Cararra to shape each capital from a 10,000-pound block of marble. “The CNC robotic machines can hold multiple tools and rotary blades to rough out the pieces,” explains Rugo, “but fine detail requires finger bits that have fine points and can more delicately profile the stone.” Machines, however, can only carve about 90 percent of the stone. “The undercuts and organic life are added by eight to 10 skilled carvers experienced in architectural figures,” he explains, using a variety of chisels and rasps to create texture, fine detail, and movement.
The result is about 7,000 pounds of finished marble capital, an architectural sculpture heavier than a large SUV. “A master carver is able to carve and texture where a machine can’t reach because of tool size or pocket depth,” adds Rugo, “but hand-carving also creates the life in the piece.” TB
Gordon H. Bock is an architectural historian, instructor with the National Preservation Institute, and speaker through www.gordonbock.com.