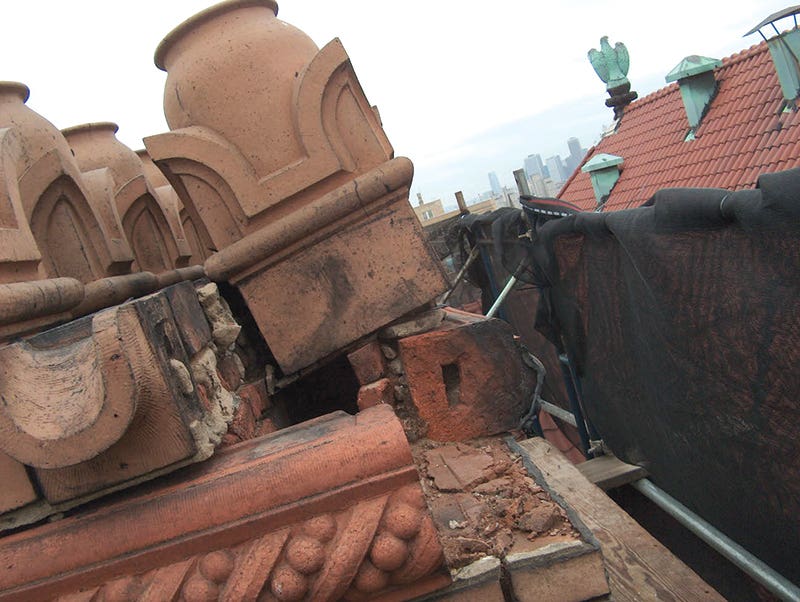
Roofing
Chimney Restoration at Brooklyn’s Montauk Club
In 1891, the Montauk Club opened in Brooklyn, NY, to great jubilation. It was founded by prominent Brooklynites Charles Pratt; Richard Schermerhorn, overseer of the construction of the Prospect Park; and Edwin C. Litchfield, a lawyer and railroad developer who owned a good amount of the surrounding land. Renowned New York City-based architect Francis H. Kimball designed the building, and over the years, the Brooklyn club house has hosted many other prominent figures including Grover Cleveland, Herbert Hoover, Dwight D. Eisenhower, John F. Kennedy and Robert Kennedy.
The building is as impressive as the club’s history. Inspired by the Ca’ d’Oro palazzo along the Grand Canal in Venice, Italy, the turn-of-the-century structure features Gothic-style pointed windows and quatrefoil ornamentation. The mostly brick and brownstone building also employs terra cotta for the columns and the frieze, the latter of which depicts Montauk Indians.
By 2004, the façades, roofing and chimneys were in dire need of repair. New York City-based Building Conservation Associates (BCA), hired on as restoration consultants, designed a stabilization plan and brought in masonry- and roofing-restoration specialists Nicholson & Galloway, Inc., of Glen Head, NY, to address those issues.
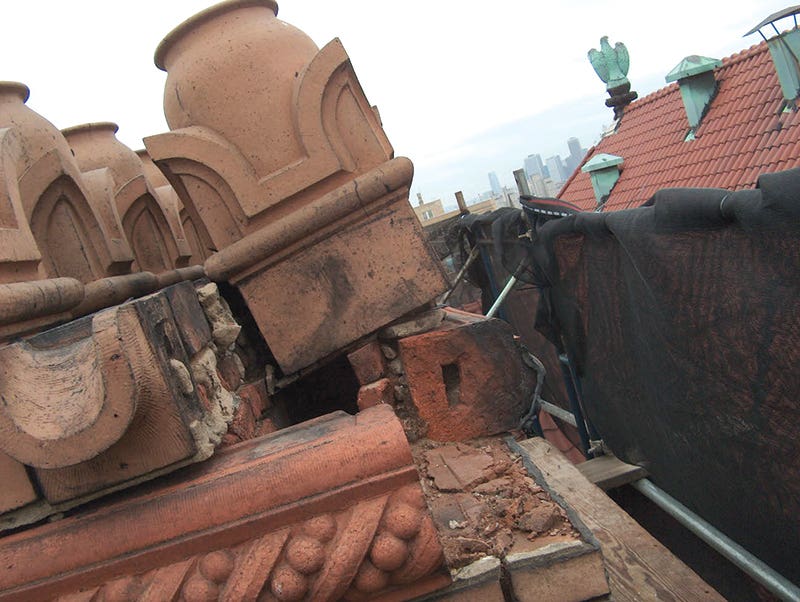
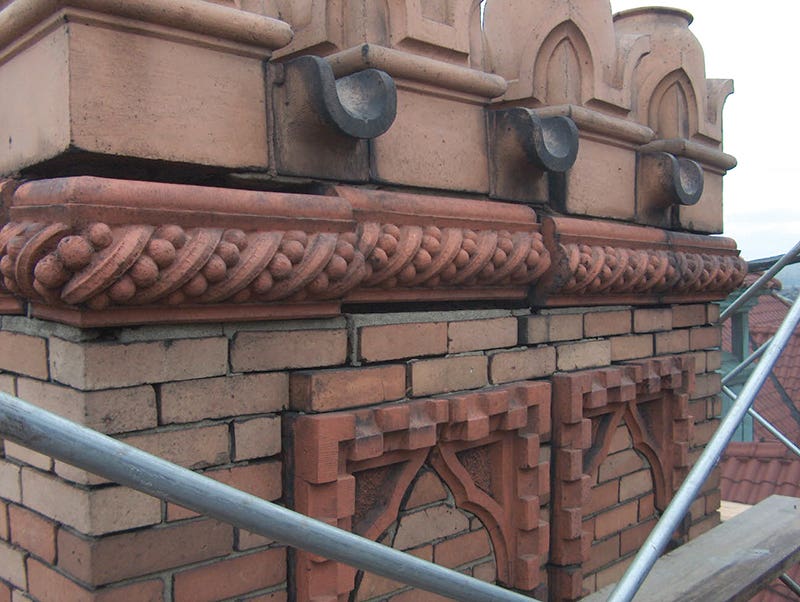
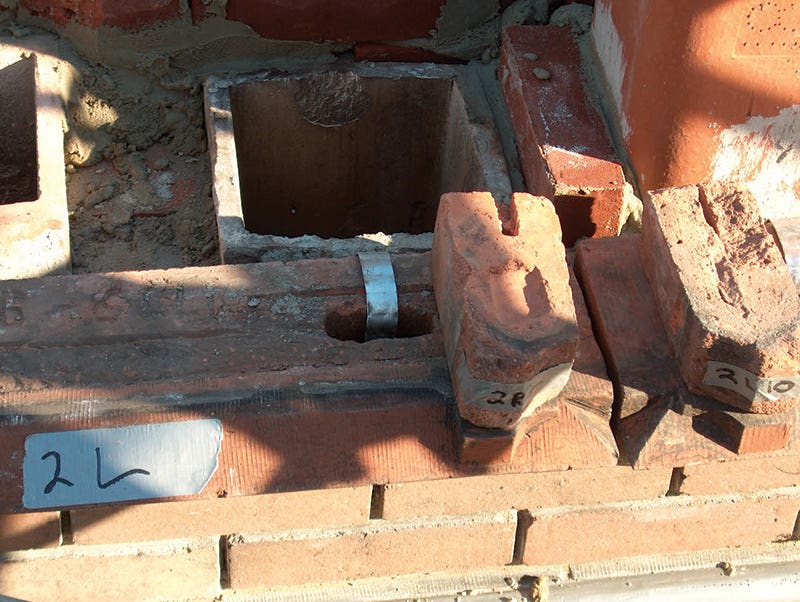
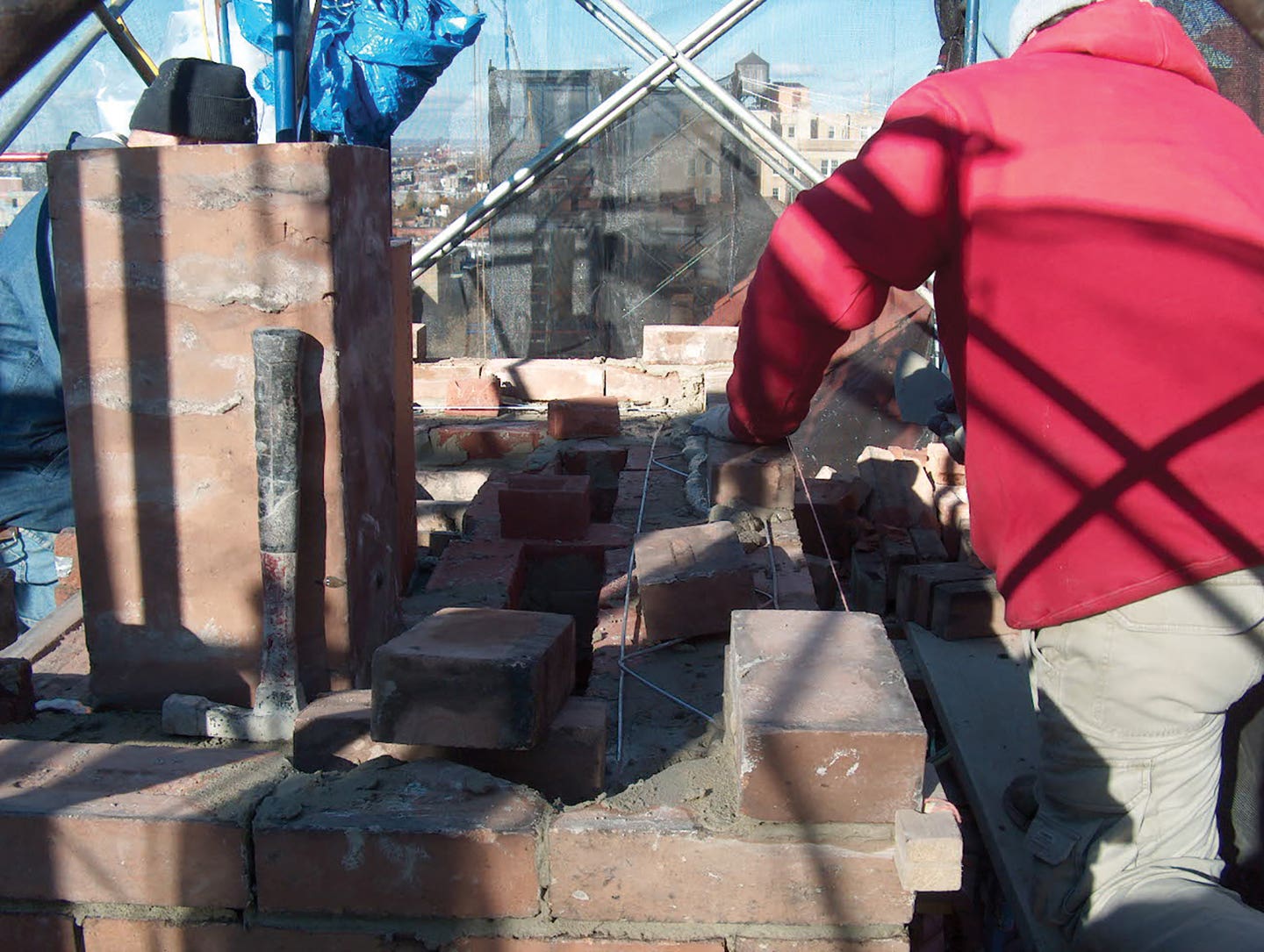
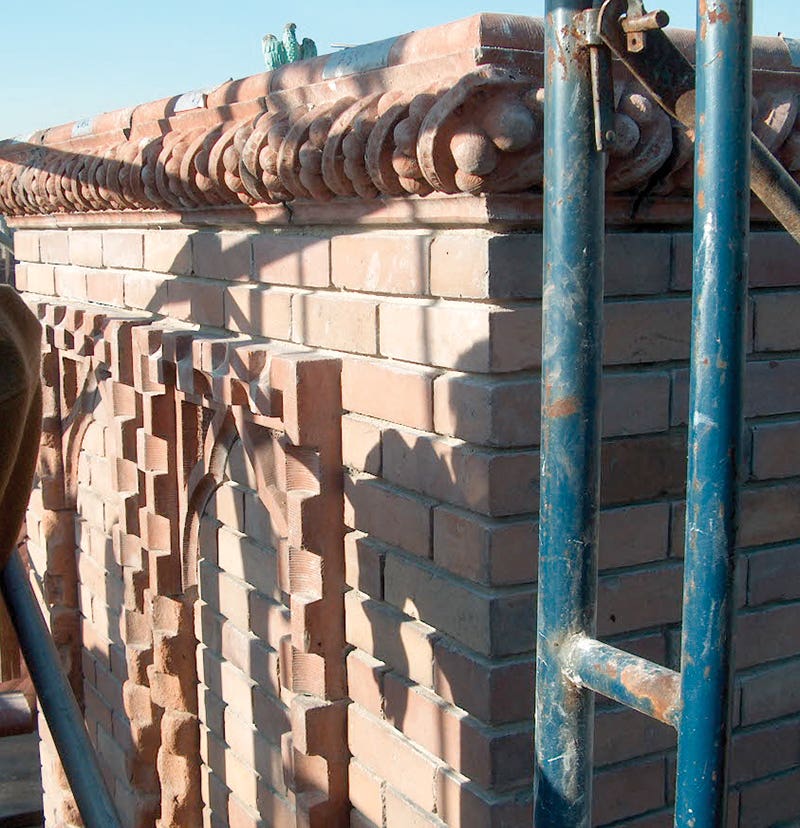
Initial Condition
The three brick and terra-cotta chimneys in particular “were in poor condition,” says Dean Koga, director of technical services at BCA. “Some of the terra-cotta chimney pots, while still on the chimney, were displaced. Also, there were many loose and displaced bricks near the top, because the mortar was disintegrated.”
Koga cites harsh weather conditions as the culprit. Though the chimneys were original to the building – hence more than 110 years old just before the project began – New York City’s climate, not the most forgiving to masonry chimneys, receives the brunt of the blame. “The exposure to wind and rain was the main reason the chimneys had sustained damage, because the original mortar was soft,” says Koga. The freeze-thaw cycle is also bad for chimneys, because the joints will fail from the constant expansion and contraction.
In this case, the fireplaces hadn’t been used in a number of years, which Koga asserts is better for the chimneys than the alternative. “When chimneys are used in the winter, the flues expand from the heat and the outer wythe of brickwork contracts from the cold,” he explains. “This usually causes cracks, but in this case the clay flue liners isolated the inner brickwork somewhat, and the mortar in the brickwork had lost most of its adhesive properties, so the inner and outer wythes were able to move somewhat independently. They became dislodged instead of cracking. More heating would have caused more dislocation.”
Dismantling the Historic Chimneys
Work began in October 2004, an atypical start date for this type of outdoor construction. With a start date so close to winter, Nicholson & Galloway was on a tight schedule – the company worked hard to meet the owner’s requirements before the harsh winter cold was upon it.
Nicholson & Galloway employed seven workers full time to meet this deadline. After they erected scaffolding around all four sides of each chimney, they removed the original terra-cotta chimney pots and panels. Then they dismantled the three chimneys brick by brick. “We took one chimneys almost down the roofline [about 13 ft.],” says Michael Tolan, project manager at Nicholson & Galloway. The other two were taken down about 8 ft.
It was important to do the work by hand, because BCA had specified that as much of the masonry and terra cotta as possible was to be salvaged. “Often on a similar project, [the workers] will save the terra cotta and toss the brick,” says Tolan. “However, BCA opted to reuse the brick as well as the terra cotta in this case. The color of the brick [would have been] very tough to match.”
Once on the ground, all of the old mortar was cleaned off, again by hand. The cleaning and other handwork processes were one of the challenges, says Tolan. While important, they were time consuming, and there was pressure to finish quickly.
In place of the brick that had flaked or was damaged beyond repair, Nicholson & Galloway used new brick that was color matched as closely as possible. To err on the side of caution, the replacement brick was installed on the one side of each chimney that could not be viewed from the street. “Luckily, we had enough brick for the other three sides,” says Tolan. All the terra cotta, on the other hand, was salvaged. Workers cleaned the original setting bed off of the terra-cotta pieces with small chisels and 5-in-1 scrappers. “The terra cotta was so delicate,” says Tolan. “We needed to be extra careful.”
Reconstruction of the Chimneys
To keep track of placement, every brick and terra-cotta piece was numbered to correspond with a field sketch. When it came time to rebuild the chimneys, every brick and panel, except for those bricks on the back side of the chimney, was returned to its original place. The chimney pots were likewise cleaned of all mortar and then reset after the chimneys were rebuilt.
The project was not entirely exterior, though. There had been no chimney covers, so Nicholson & Galloway capped the flues using a cap that fits inside the chimney pot. “The objective was that the caps could not be viewed from the ground,” explains Tolan.
The company replaced damaged clay-tile flue liners with new ones the same size as existing ones. Then a sub-contractor installed prefabricated stainless-steel liners for four of the 28 fireplaces. “Only a number of the residents wanted use of their fireplaces,” says Tolan. For these flues, stainless-steel liners are important, because, explains Tolan, “the prefabricated flues will isolate each flue from the others so that the gases will exit through the chimney instead of move from one flue to another,” one of the pre-restoration problems.
Nicholson & Galloway applied new reinforced membranes at all of the valleys and a membrane lining in the chimney gutter. “The gutter was made of copper as a waterproofing method,” says Tolan, “but over the years there had been leaks. People had been placing tar to stop the gutters and the valley from leaking, but that’s only a quick fix.” This poor waterproofing material was removed before the new cold-liquid-applied flashing was installed.
BCA specified a stainless-steel truss anchor system “to strengthen the mortar joints,” explains Tolan. “It runs horizontal every fifth course, and is used to tie the face brick and the terra cotta to the back-up brick.”
The chimneys were restored and rebuilt in three months – completed in January 2005 – and now look as good as they did when they were originally constructed in the late 1800s.
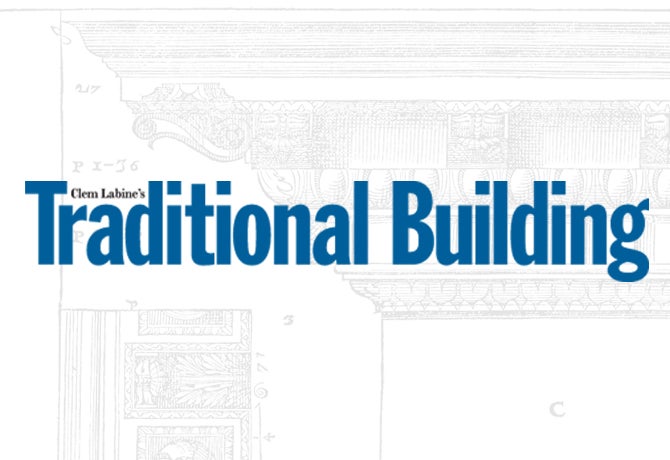