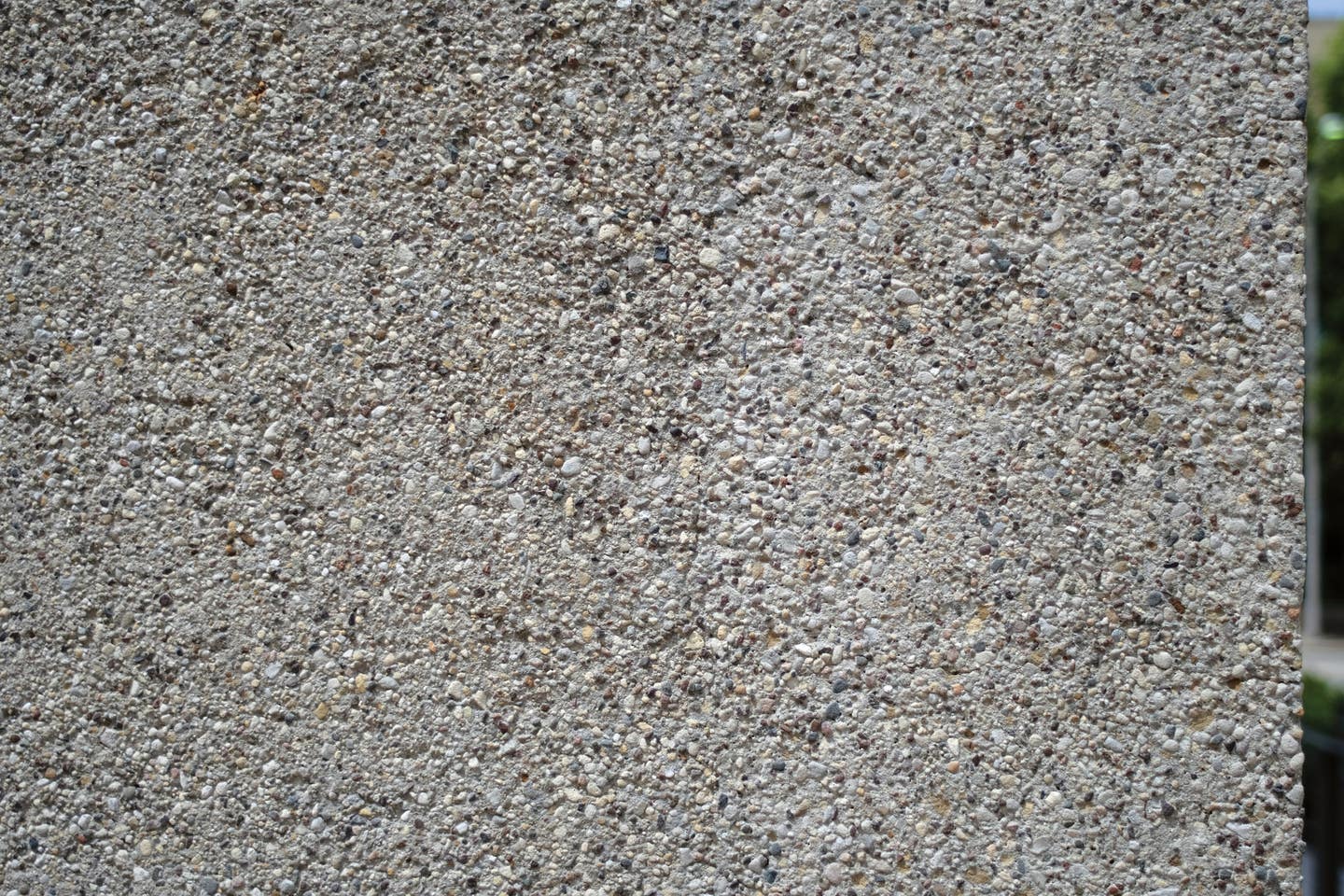
Product Reports
Building with Concrete
Concrete is a monolithic mixture of cement, aggregate, and water that can be poured flat or into raised forms on the jobsite (formed-in-place). Modern cement is typically Portland cement, and the curing time to full strength is 28 days. For the purposes of this article, the focus will be on the formation and repair of cast-in-place concrete. (Precast concrete is fabricated in reusable forms offsite and not covered in this article.)
History
The history of the formation and usage of concrete is very long and has gaps and parallel discoveries continents apart. Relevant to North America, the first manmade cement was created by Englishman Joseph Aspdin, who burned powdered limestone and clay in his kitchen stove in the 19th century to make what he named “Portland” cement. This invention evolved into bagged cement, which could be shipped and mixed onsite.
Today in the 21st century, cement is manufactured through a closely controlled chemical combination of calcium and silica, with small amounts of such naturally occurring elements as aluminum, iron, and magnesium found in the limestone. Making cement is a dry method, which starts with quarrying and collecting the principal raw materials.
The calcium component is derived from limestone, along with shells, chalk, or marl that is combined with shale and clay and crushed. This mixture is placed in a rotary kiln at 2700°F. (See Figure 1) The burning converts the mix to “clinker.” Once cooled, clinker is finely ground to a powder and the resultant cement is mixed with sand and coarser aggregate. When water is added, the cement hydrates and forms a binder for the sand and aggregate, curing the whole into what is known as concrete. Concrete started off as a utilitarian material, being used in roads, dams, and bridges. Over time, it was utilized for building elements such as posts and beams, floor slabs and bearing walls, and as back-up to masonry. Around the 1900s, it began to be used for entire buildings as the exposed finished appearance.
Installation Methods
Poured-in-place concrete uses forms fabricated to the desired configuration from wood, steel, or fiberglass. The material and the fabrication of the formwork play a large part in the final appearance. The resulting appearance can leave exposed form tie holes and seams visible, or the surface can be smoothed out with a thin, cement-based parge coat for a more refined appearance. Further, the form can be designed to provide dimensional thickness resulting in a decorative pattern such as woodgrain, patterns, or even “fins” that can be broken off to make an alternating rough/smooth appearance.
Strengths and Weaknesses
In compression, concrete is very strong. It also meets the air barrier requirements of ASHRAE 90.1 and the 2012 International Energy Code. The downside is that it is very weak in tension—thus the introduction of steel reinforcement, which provides the tensile support. The drawback of reinforcing steel is possible corrosion due to several processes, which results in damage to the concrete, as explained below.
Typical Failure Methods
Concrete can crack due to building differential movement or insufficient design. This can cause a structural issue that could require an engineering repair solution. Shrinkage of the concrete as it dries, or a lack of control joints in the pour, could cause hairline cracks.
The curing process that hardens the concrete is a reaction wherein the calcium silicates in the cement combine with water to create calcium silicate hydrate, calcium hydroxide, and heat. The resulting concrete has a high pH, which protects embedded reinforcing steel by limiting electrochemical transfer. Carbonation occurs as the concrete ages, a process that combines carbon dioxide with moisture in the concrete pores, creating carbonic acid. This lowers the pH to below 8.6, at which point electrochemical migration can occur between cathodes and anodes. (See Figure 2) The ferrous steel reinforcing bars, or rebar, can oxidize (rust) within the concrete due to this cathodic action, or due to shallow embedment, or moisture, which expands the cross section of the rebar. If it has sufficient embedment, the concrete will contain it. However, limited cover over the rebar permits the carbonation to reach the rebar more quickly, and with less concrete to resist the oxidation expansion, it leads to cracks, rust staining, and even pieces spalling off. (See Figure 3)
Approach to Repairs
Survey the building, mapping all the damage found. Previous repairs should be documented as such and checked for soundness. Nondestructive testing, such as ultrasound or ground-penetrating radar are helpful in identifying nonhomogeneous materials and internal distress. Cover meters can identify when the concrete has insufficient depth of coverage over the rebar. Where concrete is suspect, tap it lightly with a stainless-steel hammer. Where concrete has internal delaminations, it will sound “punky” or “soft.” Sound concrete will ring more musically. Identify localized damage that could be caused by an adjacent material, such as a handrail, or brick panels within the concrete.
Testing a shard of the concrete will identify components that comprise the concrete, such as proportions of the aggregate, sand, and cement. This information will reveal the concrete properties that you are trying to match, leading to a long-term, durable repair.
More invasive core testing can determine strength, petrography, chloride content, compressive strength, freeze/thaw properties, and the presence of carbonation. (See Figure 4) If the carbonated concrete is causing electrochemical attach on the rebar, there are ways to neutralize the field using cathodic protection, although this is a very expensive system which requires engineering. An alternate approach to deterring the carbonation process is to coat the concrete. This opens the coating discussion.
To coat, or not to coat? That is the question. When the original architect designs a building later identified for concrete repairs, it is important to understand whether the concrete was intended to be the exposed original finish, or whether it had always had a coating. It is possible to match uncoated concrete with a lot of worthwhile effort, involving tinkering with the cement color, aggregate size, color and exposure, and the surface texture. (See Figure 5) When coatings are determined to be the appropriate solution, such as to arrest carbonation, it is important to ensure that there is a sound substrate. Applying a coating not previously in place will fundamentally change the historic appearance, and it is not reversible. Even a clear water repellant could alter the color or sheen, and it could also change the dew point in the wall. If there is already a coating on the building, it must be tested to ensure it is fully bonded, and the subsequent coating must be compatible with the substrate. (See Figure 6)
There are many types of repairs, depending on the symptom. First, the cause of the problem must be understood, then the cause must be treated before addressing the symptom. Once the cause is addressed, then the repair methods for the symptoms can be selected.
Where cracks are present, they permit water to enter. That moisture will freeze at low temperatures, expanding and causing further cracking of the substrate. If the cracks are not moving, they can be epoxy-injected or sealed with epoxy grout. If the cracks are active, they should be sealed with a more flexible material, such as a non-staining sealant, to permit the movement and prevent water ingress.
Where concrete has spalled and the rebar is exposed, the corroded rebar needs to be cleaned to bare metal and protectively coated to prevent further deterioration, before patching the concrete. If the rebar has experienced significant section loss, ideally, new rebar should be placed. Stainless steel is a good option to avoid future oxidation, if it is compatible galvanically with the existing rebar. If the spall is caused by the rebar being too close to the surface of the concrete, cut back the concrete to a sufficient depth to provide a repair with minimum recommended coverage of the rebar, as published by the American Concrete Institute (ACI). To replace the lost concrete, remove concrete at least ¾-inch back from the rebar to provide a bond, key the edges of the patch, and roughen the concrete bonding surface. To form the patch, the surface of the form needs to match the surface texture of the concrete to be visually successful. (See Figure 7)
What to Do / Not to Do
Always approach the building holistically to ensure that the cause of the problem is understood, whether structural, moisture, movement, or cathodic deterioration. Once the cause is understood, address the cause to either remove it or mitigate it.
Avoid coating a building whose surface was never intended to be coated. It changes the building’s appearance and creates an ongoing maintenance issue. When a coating is required to address moisture issues or carbonation, ensure the coating has the right properties for water shedding, vapor permeance, color, and texture.
Additional Resources:
Preservation of Historic Concrete (Preservation Brief No. 15) by Paul Gaudette and Deborah Slaton
Cleaning Historic Concrete by Deborah Slaton, Concrete Repair Bulletin, January/February 2000
Guide to Concrete Repair (ACI 546R-14) by American Concrete Institute, September 2014
Sustainability for Repairing and Maintaining Concrete and Masonry Buildings by ICRI Committee 160, Sustainability
Concrete Problems Today are Multifactorial—Root Causes by Hamid Khan, Concrete Repair Bulletin January/February 2019
The Repair of Concrete Structures, Second Edition, edited by R.T.L. Allen, S.C. Edwards and J.D.N. Shaw, Blackie Academic & Pro-fessional, an imprint of Chapman & Hall 1993
APT Bulletin: The Journal of Preservation Technology, Vol. 48, No. 4, Special Issue on Documentation (2017), pp. 29-36 Practice Points Number 16 Author(s): Ann Harrer And Paul Gaudette
The History of Concrete by Nick Gromicko and Kenton Shepard © 2006-2019 InterNACHI
Susan D. Turner is a Canadian architect specializing in historic preservation of national registered buildings. She is the Senior Technical Architect for JLK, a woman-owned business specializing in the repair and preservation of historic buildings. She can be reached at sturner@jlkarch.com