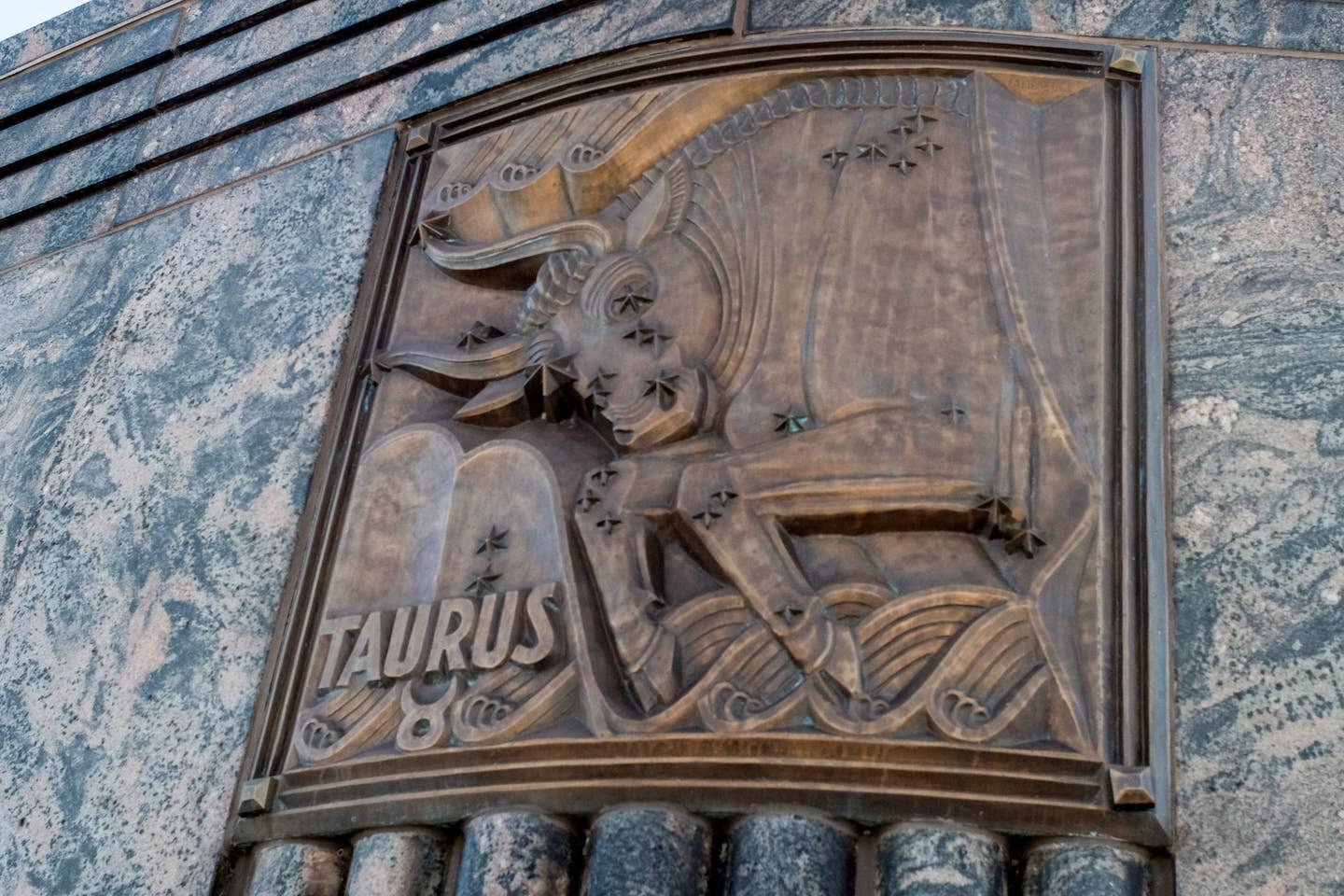
Product Reports
Bronze in Traditional Building
The Bronze Age (C. 5000 to 1100 BC) was defined by the production of bronze by smelting, which combined copper with tin. Bronze was much harder than earlier metals, and its durability is evident in the multitude of bronze artifacts that have endured. While other metal tools were fabricated prior to bronze, they were formed of single metals. Bronze required not only the mining of copper but also trade for tin, which was not available in the same geographic region. It also required separate smelting, and craftsmen who could combine the materials in the right way, at the right temperatures, and form the tools.
Today, bronze is popularly used in sculptures for its excellent casting qualities. In architecture, it can be regularly found in hardware, doors, entrances, fountains, handrails, column cladding, and architectural details such as plaques, medallions, and panels.
History
Bronze artifacts dating back to 5 millennia BC are termed “Alpha Bronze,” since they were produced with ore that naturally contained copper and tin together. Where tin and copper did not naturally occur, bronze was first made by mixing copper with arsenic to get its hardness, but this process created a toxic off-gas. Tin replaced arsenic around 3500 BC, in the height of the Bronze Age, with the transportation and trading of tin in regions without naturally occurring combination ore, making the bronze stronger and easier to cast. The Iron Age followed when iron was combined with carbon to make steel, which was stronger and could hold an edge better. Bronze continued to be used for cast objects and was prized for objects which were exposed to moisture due to its resistance to corrosion, especially salt water, such as propellers, cannons for ships, and public sculptures.
Brass versus Bronze
There are many alloys that are termed bronze, depending on its combination of metals. In rough terms, bronze typically contains 95% copper and 5% tin, while brass is a mixture of 65-85% copper and 15-35% zinc. Visual observation is not definitive as to whether an object is brass or bronze.
Bell Bronze is a type that has an ideal balance of strength for striking, while having the softness to provide a melodious tone, and ease of casting. For example, the Liberty Bell has a recipe of 70% copper and 25-30% tin.
Statuary bronze consists of 97% copper, 2% tin, and 1 % zinc, giving it good casting qualities and fine grain.
Phosphor bronzes are formulated for low brittleness and high strength, ductility, and resistance to wear. They are typically used for gears, pistons, propellers, shafts, and the like.
Silicon bronzes are about 98% copper and 2% silicon, which gives good corrosion resistance while providing good casting, rolling, spinning, and pressing capabilities.
Technically, what is known as architectural bronze with 57% copper, 40% zinc, and 3% lead constitutes a brass.
Nickel silver is sometimes considered a bronze but is not. Its name is a misnomer since it contains no silver at all, consisting of a mix of 70% copper and 30% nickel. This provides excellent corrosion resistance, is used extensively for marine tubing and condensers, architectural decoration and ornamental grilles, and smaller castings.
Lastly, a “bronze” named Monel is a mix of about 70% nickel and 30% copper, resembling stainless steel. Over time, it is possible that the copper will oxidize somewhat, rendering a greenish cast.
Causes of Failure
Corrosion
Bronze will corrode when exposed to acid rain and air pollution. This corrosion from the exposure to oxygen and sulfur in the atmosphere forms a patina on the surface that partially prevents further corrosion. This patina starts with brown copper oxide, evolves to a blackish color as it forms copper sulfide, and finally takes on the familiar blue-green of copper carbonate. This is an aesthetic symptom that does not require action.
Where ongoing acid rain dissolves part of the copper carbonate, it can result in green staining on surfaces below the patina from solubilized copper depositing. Where acid rain is persistent, or a large amount of bird droppings accumulate, it may remove the surface of the bronze. Unpatinated areas can develop carbon-rich black deposits, creating protected cathodes, while areas of green copper carbonate act as anodes. This sets up an electrochemical condition in which deep pitting can occur. These pits further retain deposits of chlorides, which cyclically increases corrosion without the intervention of thorough cleaning.
Abrasion
As hard as they are, bronzes can wear away through handling, such as parts of this statue, here people handle it or sit on it.
Cracking
Bronze castings can include inherent flaws due to inconsistencies in the mold material, the molten bronze being too hot or including air pockets, or flaws in the crystal structure developed in the cooling process. These weak spots permit fractures to occur with the stresses of movement and temperature.
Where statues are reinforced with an armature of a dissimilar metal, or pinned with dissimilar materials, galvanic action occurs, caused by moisture transmission of electrons from the more noble metal to the less noble metal. Further, if liquid water is present, a gray-white sulfate crust could form on the surface. If fastening pins are ferrous, when they are exposed to moisture and corrode, they expand and minimally will cause rust staining on the surface, if not crack the bronze in that location.
With such constructions, sometimes the armature is insufficiently designed to support its own weight, or to resist wind and snow loads, resulting in sagging or cracking.
Sometimes bronze fabrications are not designed to shed water. When water is trapped in cold climates, it freezes, expands, and pushes apart the bronze, sometimes cracking it.
Lastly, the piece may not have been designed to accommodate the expansion and contraction of the bronze with the climate in which it was placed, resulting in cracking.
Repairs
Cleaning Corrosion
Cleaning bronze requires the mildest methods possible. Before commencing, determine if cleaning is absolutely necessary. Assess whether not cleaning the bronze will cause further damage. Identify any corrosion products on the surface, and what causes them. Remove the source of corrosion before commencing any cleaning. Determine what the original finish was: was it intended to have patina? Was it originally coated?
Sandblasting, steel wire brushes, or steel wool are inappropriately strong to clean bronze and will leave it pocked and scratched, with irreparable damage to the finish. Further, steel can leave micro deposits of iron, which will cause rust staining over time.
If cleaning is the course of action decided upon, begin with clean water, or de-ionized water, and a soft natural-bristle brush. If a greasy crust has deposited from exhaust and wind-blown dirt, use a non-ionic detergent, possibly combined with the use of an organic detergent.
Where localized areas of chlorides remain, targeted applications of low-pressure micro-abrasive cleaning can be used, or poultices. Where such means are beyond the budget, bronze wool may be used by hand, using water or oil as a lubricant.
Once cleaned, protective coatings of wax, lacquer, or oil can be used. Where the sculpture has ongoing exposure to the elements, oil is not recommended as it will attract further dirt. Bronzes that experience high handling can be protected with a mixture of 5 ounces of lemon or lemongrass oil mixed with a gallon of high flash point (> 350 degrees) paraffin oil, reapplied on a weekly basis. Alternately, the British recipe is 40% lanolin, 7% paraffin wax, and 51% “white spirit” (turpentine) wherein the turpentine acts to remove the previous coat, and the oil installs a clean wear coat with corrosion resistance. Depending on the level of handling, this can be reapplied, monthly, tri-monthly, but never less than annually. Oil coatings should not be used if appropriately timed ongoing maintenance is not implemented.
Waxes are used for areas where handling can cause localized removal of the patina. When applied directly to bronze, Carnauba wax mixed with synthetic microcrystalline wax creates a higher melting point. This point is important to prevent waxes melting in hot weather; the same wax must be able to perform well at low temperatures without crazing. Cold wax is applied to a heated bronze with a bristle brush with a stippling motion. Waxes can be locally re-applied in areas with localized abrasion, without the removal of the entire coating. Only Carnauba and Brazil wax should be used in their straight formulas since other types can cause acidic reactions on the bronze.
If a stronger protective coating is required, a lacquer called Incralac, formulated by the International Copper Association, can be used, but it is very odorous in its application, and requires several coats. Incralac only lasts one to four years, depending on the level of pollution to which it is exposed. To improve the longevity of the lacquer, a coating of cold wax is applied cold with a stiff-bristle brush.
Repairing Cracking
When bronze castings are hollow or permitting water to collect, proper drainage should be provided by the drilling of small holes in discreet locations. If the formation of ice by this collected water has caused splits in the bronze, they can be cold patched by the use of cored holes and threaded bronze rod. Once installed, the rod is cut off, and the exposed end finished to match the adjacent surface. Where an extensive split occurs, it should be enlarged to a regular shape to take a coupon, with the edges dressed to permit peening of the perimeter for a mechanical keying of the patch.
If the cause of the split is an issue with materials, such as dirt or plaster, which have collected internally and require removal, a hole can be drilled to permit the use of a bent hook on a drill inserted into a split or a hole, to rout out the extraneous material. If, however, the split is caused by corrosion or expansion of the armature, then the armature must be removed. This can mean major surgery, involving the disassembly or cutting of the bronze, repair or replacement of the armature with non-corroding material, and reinstallation of the bronze using brazing of the joints.
Cautions
Epoxy resins or acrylics should never be used to coat bronze. Over time, they will be damaged by environmental conditions and thermal movement, resulting in fissures that trap acid rain. These pockets will expand, causing an unacceptable appearance. The gentlest means to remove these coatings is a micro-abrasive treatment, such as the use of crushed walnut shells, but this will still remove historic material.
When repairing bronzes with new material, it is essential to determine the exact alloy composition, to ensure that no galvanic action can occur between old and new. (To further the surgery analogy, think of it like tissue matching.) Even when the exact composition is noted on historical records, an SEM test (Scanning Electron Microscope) should be used to confirm the exact composition that was actually used.
None of this work should be undertaken by anyone other than craftspeople who have suitable training and experience to effect repairs without damage. Bronze is actually quite soft, and damage to it is permanent. Even if damage is buffed out, or a bad coating removed, it still involves the loss of historic material.
References:
Metals in America’s Historic Buildings, US Department of the Interior, National Park Service, Cultural Resources Preservation Assistance, Washington D.C. © 1980 Margo Gayle and John White
Conserving Buildings Guide to Techniques and Materials by Martin E. Weaver with F.G.Matero © 1993 John Wiley and Sons
The Beginnings of Bronze ©2019 Copper Development Association (Available online)
How to Repair Antique Bronze Statue by Lakeside Pottery Restoration Studio (Available online)
Susan D. Turner is a Canadian architect specializing in historic preservation of national registered buildings. She is the Senior Technical Architect for JLK, a woman-owned business specializing in the repair and preservation of historic buildings. She can be reached at sturner@jlkarch.com