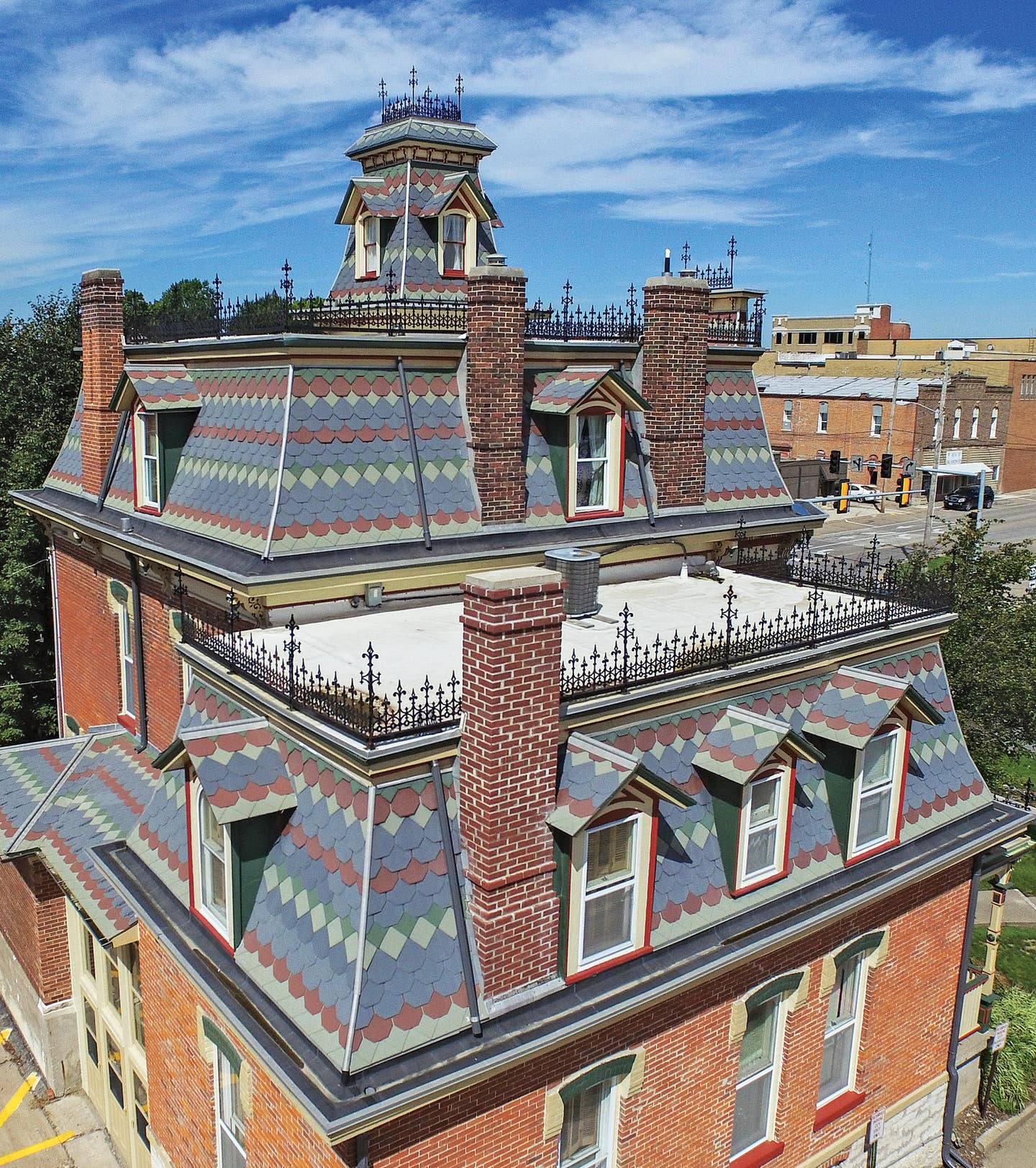
Product Reports
Alternative Building Materials
Whether you call them substitute materials, alternative materials, or simply stand-ins, man-made products crafted to imitate natural substances have a long and complex history among traditional buildings—and one that is changing swiftly. Commonplace for at least 200 years, alternative materials of the past—think cast iron that clones carved stone—were typically driven by a quest for efficiency (quantity reproduction of complex decoration, for example) or economy (cheaper and easier to obtain).
While preservation practice puts a premium on repairing deteriorated architectural features over replacing them, and when the latter is necessary, stresses “the new material should match the material being replaced in composition, design … and other visual properties,” (NPS Preservation Briefs #16) shifting manufacturing technologies, aging landmark buildings, and an increasingly threatening climate are putting that mandate to the test. In some cases, the major challenges go beyond historical accuracy and architectural legacy to simply where to find new materials that might do the job and how long will they last?
What Wood Is Good?
At ground zero, it turns out, wood is the most natural and universal building material in North America. According to Phil Thomason, principal at the preservation planning firm Thomason and Associates in Nashville, “I think there is a great deal of concern about just how long traditional wood products are lasting these days.” He notes that long-lived woods are still out there, but at a cost. “You have to weigh two approaches: Do I pay more for wood I know will be durable, or pay less for a product that I think will look like wood, but don’t know how long it will last?
In some quarters, “concern” is putting it mildly. “We’re a hot, humid climate—constant 90 percent humidity,” explains Becky O’Malley Gipson, Operation Comeback Director at the Preservation Resource Center of New Orleans, “and the big thing we’ve been dealing with is that after Hurricane Katrina in 2005, a lot of building owners replaced old-growth woodwork—features that had been terribly damaged and couldn’t be repaired—with newer wood. What we’re seeing now in 2018 is that a lot of these new woods are breaking down, cupping and decomposing.” As Gipson explains, New Orleans is predominantly a city of wood-frame buildings with wood-detailed trim and wood shutters. “Most commonly we see this deterioration on wood porches and their tongue-and-groove decks; wood shutters, both louvered and board-and-batten, architectural trimwork and wooden handrails, which are commonly called for in our historic districts.”
A similar alarm echoes from the National Trust for Historic Preservation (NTHP) with 27 sites from Illinois to New Mexico. “At the NTHP we’ve had to replace much of the in-kind repairs done in the 1980s to 2000s,” says Ashley Wilson, AIA, LEED, Graham Gund architect for Historic Sites, “because they were in-kind in name only—not in quality.” Wilson, who describes herself as “old-school” about new products versus traditional materials, acknowledges that failures have led to a more practical perspective. “I have fully converted to acetylated wood for exterior carpentry and wet areas because it is the only wood that won’t deteriorate and remains stable.”
Here she is referring to Radiata pine, a species widely cultivated in temperate zones, that is modified with acetic anhydride (a compound related to vinegar) so it resists moisture and insects.
In fact, insects pose another increasing onslaught, most notoriously Formosan subterranean termites, which began attacking Texas, Louisiana, and South Carolina in the 1960s.
Recalls Gipson, “A lot of times, what I find in rehab projects is that the termites go after a new addition first with its softer woods like yellow pines. Only when they’ve decimated the addition will they move into the older, old-growth cypress.”
What’s more, it’s not just Mother Nature that’s coming up short. “Many alternative materials have come online only within the last 15 or 20 years,” says Thomason, “so we’re still assessing their longevity: how long will these materials really hold up?” Gipson agrees. “After Katrina, many local nonprofits used a lot of innovative, sustainable products that unfortunately weren’t tested in our climate and, in some cases, just haven’t survived. It’s tough when you have this much rain; constant humidity takes its toll.”
Durability
As an example, she says for a long time people were using fiber-cement products or some sort of composite for tongue-and-groove porch floors. “The problem was, these products would still expand and contract here—it gets hot, it gets cold, it’s wet—and they would start to buckle and snap up.” Notes Thomason, “These were the materials that were supposed to avoid the failures of traditional lumber that we get these days.”
As if the challenge of choosing a durable material were not enough, suppose it should be sustainable too? “What we’re running up against,” says Gipson, “is, for example, shutters need to be made out of wood that stands up to water, today something like Spanish cedar.”
The trouble is, a lot of these woods are coming out of the Amazon, with all of its sustainable logging controversies, and there’s just less and less of these types of woods available. “So, the question arises, Well, maybe you shouldn’t use these types of woods? Then, there’s the longevity argument: the longer a material is going to last, the less of a carbon footprint it’s going to leave. We wrestle with all these issues.”
Wilson too recognizes the complex provenance behind acetylated wood. “The argument against it is that the product is farm grown in New Zealand and shipped here via Europe. So, it has this uncomfortable transportation/production cycle that is not really as sustainable as you want it to be.” While studied for 70 years, acetylated wood only entered the U.S. market in 2007 and is now sold in 47 countries. “I hope somebody starts farming the wood here so it can be a domestic product, but I’m still happy with it because it lasts at least 50 years and that seems worth the trade.”
Not Just What, but Where and How?
Thomason, whose firm has completed over 70 design guideline manuals for cities over the past 37 years, sees some trends. “I think a lot of our preservation commissions find themselves wanting to be reasonable about approving and experimenting with alternative materials, all the while recognizing that their life expectancies are pretty unknown.” He says lately a lot of historic district commissions he works with have been adding sections in their design guidelines about needing to see sample materials, information on independent testing, or anything else that can give them a comfort level in approving an alternative material. “We’re sort of dealing with a Buyer Beware approach until we get a sense of how long these materials are really going to last.”
He says he sees language to the effect, “These are our criteria, and it is the responsibility of the property owner to convince us that this is a reasonable material to use.” Also, “The architectural review board may request a mock-up of the product installed in the requested location to determine how it will appear on-site.”
Indeed, almost as important as appearance is location. “I’ve seen a lot of commissions consider recycled materials for porch floors on rear elevations,” says Thomason, “and there seems to be widespread approval for cementitious wood products in certain situations, including rear elevations.” In his 2017 survey of eight cities, he notes that cementitious siding was among the most requested alternative materials in historic districts and, in most of these cities, approved for non-primary elevations (and in some cases primary elevations) if it matches historic dimensions and profiles.
Gipson notes that fiber cement siding and trim has been allowed for a long time in her area if the existing siding is in terrible condition. “Usually, the authority requires that it match in dimensions with historic material. For example, if the exposure on your siding was 5 ½ inches, the new siding must match as closely as possible.” She adds, termites are still an issue, and fiber cement is still popular as a replacement instead of new wood.
This is by no means open season for synthetics, though. “They do have certain products that they allow, but they have to be reviewed first by the Historic District Landmarks Commission plans examiner,” says Gipson. “They look at the appearance, scale, and where it is going on the building to determine if it is appropriate for the project.” She adds, that for a long time products like fiberglass and PVC were not permitted in historic districts, “but lately I’m seeing them being allowed—mostly because the products are getting better, with scale and detail truer to the historic forms and decoration that we see in our city.”
Typically, in any preservation situation, she says they’re also going to encourage keeping whatever is original, as much as possible. “For example, if you’re building an addition onto your property, you might pull the old siding off a part of the building you’re demo-ing and move it to a public side of the building, any elevation you can see from the sidewalk.”
Roofing
Man-made roofing has a long history of imitating other materials, and Thomason reports, “I’ve seen a number of commissions approve faux slate materials, if the original materials are clearly deteriorated and beyond repair.” He notes that the authority might want to first ask about the feasibility of doing some repair work.
Wilson, however, takes a broader view. “In most of our buildings, because roofing is so expensive, there’s not enough of a delta between a real tile roof and a fake tile roof.” The cost is usually in the labor and flashing, she points out, “so I use historic materials—slate, copper, tile—on our roofs.”
Nonetheless, she says there’s a place for asphalt shingles, “if it’s not in public view, and it’s not an important building.” As an example, she describes a 1913 shed long roofed in wooden shakes that is now under a grove of trees. “We like it, and we want to keep it, but the pine needles are always dropping and it’s just not cost-effective to put on an expensive roof, so we’re going to use asphalt shingles.”
On the other hand, Thomson says, “I don’t see a lot of love for vinyl columns on primary elevations, or for vinyl fences either. I think, commissions feel they always look plastic and do not resemble wood.” Wilson concurs. “I find that if it’s something tactile, you can tell the difference, especially if it’s juxtaposed to something that’s historic fabric that we’re saving.”
She adds that she’s mostly repairing old buildings that range from 1750 to 1950, and usually trying to work within that existing historic palette of materials. “Preservation is spiritual,” she points out. “Each project has to balance having a building fall apart versus a usable building that might have some changes.”
Gordon H. Bock is an architectural historian, instructor with the National Preservation Institute, and speaker through www.gordonbock.com.