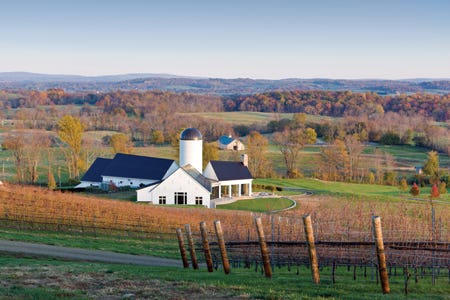
Palladio Awards 2013
Neumann Lewis Buchanan’s RdV Vineyards Winery
2013 Palladio Awards Winner
New Design & Construction – less than 30,000 sq.ft.
Winner: Neumann Lewis Buchanan Architects
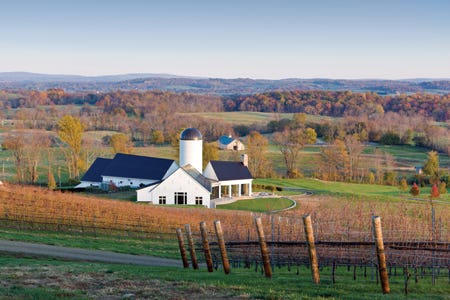
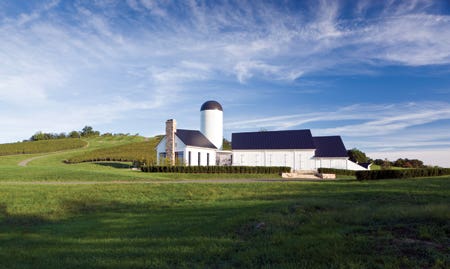
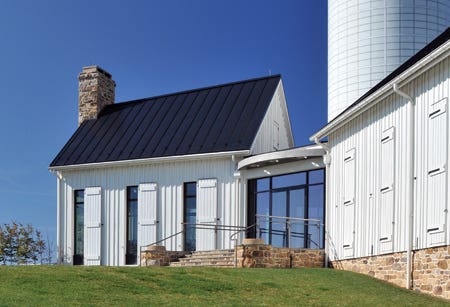
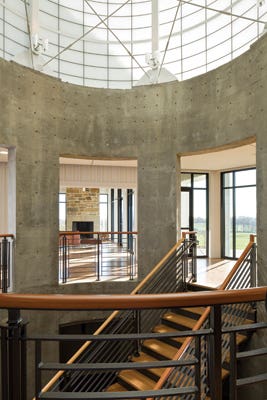
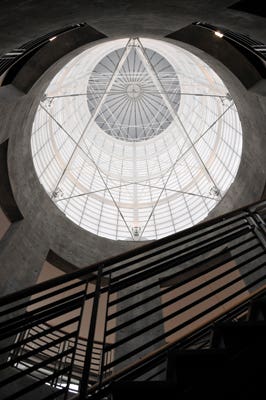
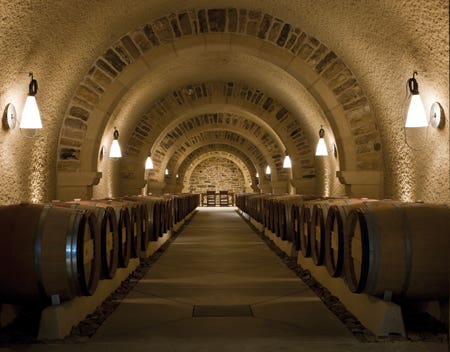
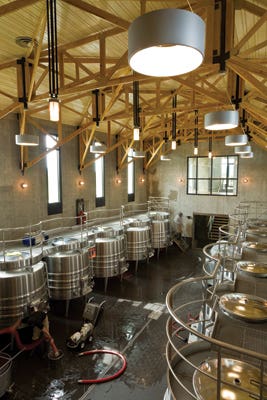
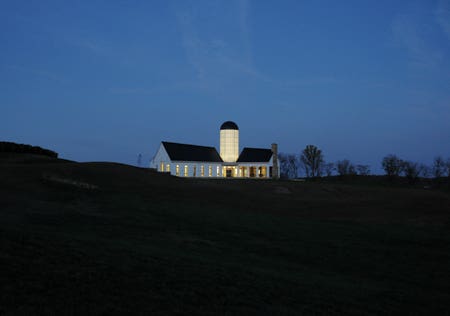
Project: RdV Vineyards Winery, Delaplane, VA
Architect: Neumann Lewis Buchanan Architects, Washington, D.C. and Middleburg, VA; Andrew R. Lewis, AIA, partner.
Contractor: Crenshaw Construction, Culpeper, VA
It is the silo that sets the scene and sets RdV Vineyards apart from the numerous other wineries that make their home among the cow pastures and horse farms of the Virginia Piedmont. The new silo structure, which rises 55 ft. into the sky, is translucent: Look at it, and it doesn't look out of place. And that's the whole point.
The 21,400-sq.ft. winery in the Delaplane area was designed by architect Andy Lewis, AIA, a partner at Neumann Lewis Buchanan Architects, which has offices in Washington, D.C. and Middleburg, VA, to make a statement by seamlessly melding with its surroundings. "The owner, Rutger deVink, wanted to have the architecture of the building mirror his winemaking quality and vision," Lewis says. "The idea was to make gestures to the area's agricultural heritage and architectural vocabulary by blending traditional style and high-tech techniques. And we wanted to make the building, even though it was fairly big, sit quietly in the land and amongst its neighbors."
This was particularly important to deVink, Lewis says, because some of the other wineries in the area announce themselves via their "brash" appearances. "He knew that the presentation of the winery would affect visitors' and wine reviewers' perception and experience of their wine. The winery needed to visually parallel and reflect his winemaking philosophy."
The project, Neumann Lewis Buchanan's first winery, was to house the pioneering company's production and entertainment elements. "DeVink's vision was to create a world-class Virginia wine that could compete with the greatest wines of France and Napa," Lewis says. "His quest required a unique soil mix not easily found in a region known for its dense clays. The site offered the perfect blend of southern slopes and loose rocky soil."
When Lewis entered the project, the vineyard blocks, which cover 16 of the plot's 96 acres, had already been planted. "It would have been better if we had been called upon to make a master site plan before the vines were planted because the only two viable sites for the building were close to the road," Lewis says. "We wanted to minimize the exposure and put as much underground as possible."
The design began with what Lewis calls "a doodle on a Post-it note." He envisioned three wings, each housing one aspect of the winery process, in a pinwheel plan anchored by a silo form:
- winemaking: receiving fruit from the vineyard, pre-chilling, processing and placement into tanks, fermentation, blending and barrel aging;
- bottling: labeling, packaging and administrative support;
- entertainment and wine tasting.
"Each wing was appropriately sized for its function," Lewis says. "The skewed volumes and roof lines evolved to reflect the nature and sizes of the spaces required and echo the landforms beyond. The three-part pinwheel plan also served to reduce the apparent volume of the building as one wing is generally concealed by the other two – the siting of the building places it above the typical horizon line of the adjacent road – further aiding the concealment of the overall mass."
The wine barrel storage cave proved to be a critical driver in the design process. "We did 20 to 30 studies on this aspect alone," Lewis says. "The owner and I even traveled to California to look at other examples. Most of them were drilled into the hills and shotcreted. But waterproofing is difficult when you do that. The ones in California leak; that's part of their charm, but in Virginia, where we have much more rain, it would mean mold. We looked at everything from using highway culverts to building interior vaults using authentic masonry techniques and precast components."
In the end, Charleston-based B-U Corp., a specialist in tunnel construction and engineering, was commissioned to build the raw 300-ft.-long, nearly 5,500-sq.ft. cave, which was dug out of the hills and bolstered with a proprietary steel hoop frame system, shotcreted inside and out then waterproofed and backfilled.
"The cave had to look and feel inviting," Lewis says. "So we played around with different concrete mixes to get a warmer cast, choosing white Portland blend as the finish coat over a colder grey Portland mix. The raw tunnel was a bit long, and even with barrels in place would look a bit boring, so we had to give some scale and rhythm to the space. We worked extensively with Lewis Whitesell Stone Masonry of Middleburg, VA, to create a series of arches made of local rubble stone and site-cast concrete that was pigmented to provide a limestone appearance. Whitesell worked the concrete while still green to add character by softening edges and adding chisel and tool marks. And he cast the colored, reinforced concrete barrel runners that rest on crushed granite harvested from the property."
The design of the winery building was fueled by the owner's philosophy of the winemaking process, which Lewis immersed himself in. "Every winemaker does things differently," he says. "In this case, the wine was to be pumped to the cave's barrels, which don't move, and then pumped back to blending tanks and the bottling line to complete the process. We worked to get as much of the building underground as possible but without making it feel like a dark hole."
Although traditional building forms and materials were chosen, the massing provides a modern edge that, Lewis says, "is at home with the local vocabulary while at the same time suggesting that something new and interesting waits within."
The trio of random-pattern board- and-batten-sided wings, which Lewis has christened "agricultural structures," allow visitors to see all the functions of the winery simultaneously. From the outside, though, only two wings are visible from any vantage point, and the Blue Ridge Mountains, as well as the grapes growing in the vineyard, are always visible.
"Each wing is tapered toward or away from the center silo hall with the ridge lines sloping up or down depending on how you look at it," he says. "There's a functional aspect to this idea because it plays into how the winery uses its equipment. I got the idea from seeing old barns along the highway that either slope with the natural grade or that have roof lines that have been modified or clipped to accommodate highway right-of-way setbacks. In the case of the winery, the wings mirror the slopes of the mountains beyond. It's a playful gesture that's functional and charming."
The wings are linked by the translucent silo, which acts as an axial focus and reference point. "We wanted the silo to be our 'wow!' factor," Lewis says. "When visitors take the stair down through the silo to access the cave, it's a surprise to see it." Some of the "wow!" factor comes from the fact that the 16-ft.-wide silo is translucent. It gets its sheer look from Kalwall cladding that's filled with insulation.
"We could have made it nearly transparent," Lewis says. "But we chose to add enough insulation to make it only 10 percent translucent. Because it's in the country, we didn't want it to glow at night. The winery is primarily a daytime operation, so the silo brings in a lot of natural light to the lower processing areas. A lot of heat goes up into it as well, so it keeps the visitor areas where events and tours are conducted cooler."
Although deVink and Lewis considered incorporating a salvaged barn and silo, that option didn't turn out to be appropriate. "We couldn't fit the winemaking equipment we needed in it," he says. "And the interior had to be a tough, washable surface, which would have meant hiding all the charming old textures."
Building new also allowed Lewis to customize the fenestration, creating large windows covered with traditional tobacco-style shutters. "I avoided the appearance of 'punched' windows," he says. "And I made the windows secondary in appearance to the overall rhythm of the openings. The ganged window frames and jambs are painted or stained black to further minimize their appearance."
The shutters, which were field-built, are made of spaced rough-sawn boards that match the siding and are used on the public-road side of the winery. "They allow the light to enter the building even when they are closed," Lewis says. "They are not only decorative. They are closed often to limit unwanted light and heat gain in processing areas during crucial fermentation phases."
The upper interior walls of the silo were finished with the same random-pattern board-and-batten siding as the exterior to provide texture, character and cohesiveness. "We didn't have a large budget for aesthetics and worked extensively with the owner and building contractor, Crenshaw Construction of Culpeper, VA, to use cost-effective treatments," Lewis says. "For example, we used pre-fabricated residential roof trusses to create an interior motif that was repeated in all three wings. The interior silo wind bracing was designed to also be an aesthetic feature that reinforced the 'theme of threes' that was started with the three wings concept. It was hard to make the silo structural and attractive, but I think it's pretty successful."
The winery's layout is devised to literally lead visitors through the winemaking process. A stair centered in the silo goes to the cave, which links to the interior at two points: a dramatic approach for visitors and a functional access from the bottling area. A third point links to the outdoors through a portal refrigeration and utility building that looks like the many agricultural structures in the region. "The whole project was a balancing act between old and new looks," Lewis says. "When you stand up in the vineyard, you can see 15 to 16 nearby silos. The RdV Vineyards Winery fits right in." TB