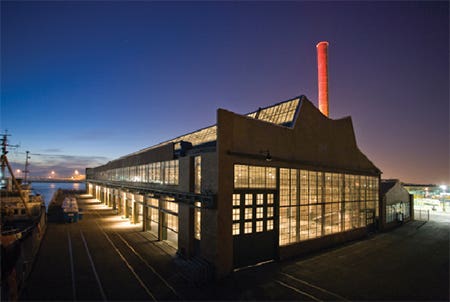
Palladio Awards 2015
Marcy Wong Donn Logan Architects: The 2015 Palladio Award
2015 Palladio Awards Winner
Adaptive Reuse
Winner: Marcy Wong Donn Logan Architects, Berkeley, CA
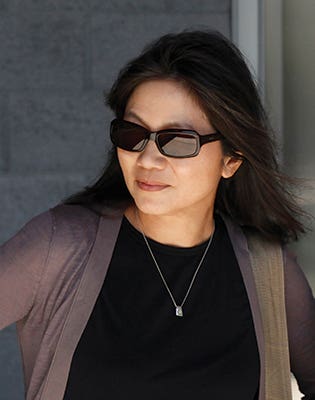
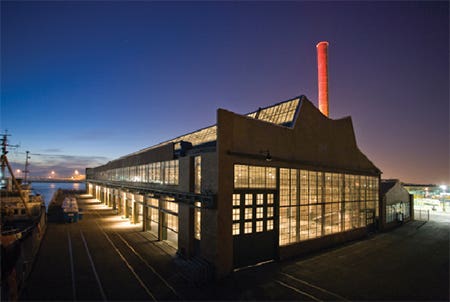

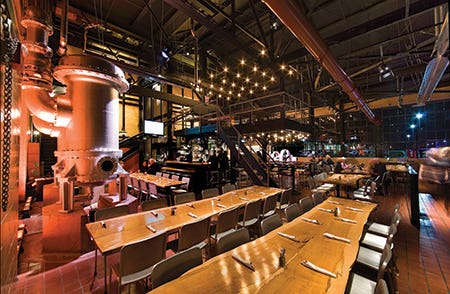
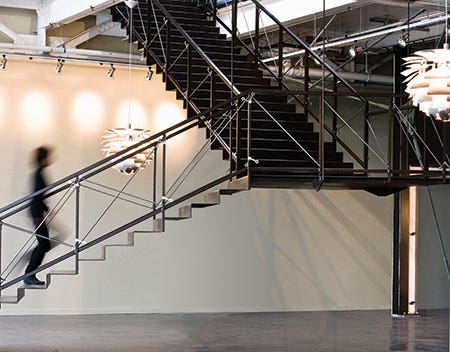
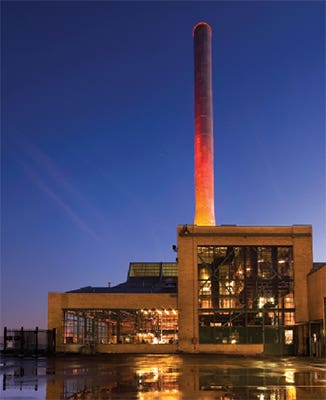
PROJECT:
Ford Assembly Plant, Richmond, CA
Architect: Marcy Wong Donn Logan Architects, Berkeley, CA; Marcy Wong, partner
Client/Owner: Orton Development, Inc., Emeryville, CA
General Contractor: Dalzell Corporation, Oakland, CA
KEY SUPPLIERS
FRP exterior cladding: Kreysler & Associates, American Canyon, CA
Solar panels: SunPower, San Jose, CA
Recycled glass products: Vetrazzo, Tate, GA
Flooring & wall: Plyboo, San Francisco, CA
Polished Concrete: Retro Plate, Provo, UT
Glazing: Supreme glass, Long Island City, NY
Marcy Wong Donn Logan Architects (MWDL) serves a diversity of clients, including private developers, universities and public agencies, for a range of building types, such as visual arts, performing arts, offices, and recreation and education facilities. The projects of Marcy Wong and Donn Logan, have received national, state and local awards for both architectural and technical excellence.
The Ford Assembly Plant in Richmond, CA, at over a half million square feet, was in its day the largest automobile assembly plant built on the west coast. A sterling example of 20th-century Industrial architecture, it was commissioned by Henry Ford and designed by Albert Kahn, best known for his “daylit factory” concept.
Completed in 1931, the 525,000-sq.ft. plant played a crucial role in World War II when President Franklin D. Roosevelt banned the production of civilian automobiles and the plant’s function was switched to assembling jeeps, half-tracked armored personnel carriers, armored cars and putting the finishing touches on tanks. By 1942, the Ford Plant was known as the “Richmond Tank Depot,” one of three in the country; military combat vehicles were transported to the plant for final processing before being shipped out to the deep-water channel of the war zones.
In 1953, the plant closed because of its inability to meet productivity demands and Ford moved its operation to Milpitas, CA. Despite its vacancy, the plant was placed on the National Register of Historic Places in 1988. It was also featured in the movie Tucker: The Man and His Dream. The following year, in 1989, the Loma Prieta earthquake severely damaged the building. The industrial windows and skylights were shattered beyond redemption, the brick and limestone south parapet of the Craneway, some 360 ft. in length and over 6-ft. tall, collapsed onto the waterfront and the building’s structural integrity was devastated. Rehabilitation of the plant was under the jurisdiction of local, state and federal agencies.
The design of the project to adaptively reuse the plant was subject to approval of these agencies and had to adhere to the preservation standards of both the National Park Service and the State of California Historic Preservation Office. In 2004, armed with a design plan by Berkeley, CA-based Marcy Wong Donn Logan Architects, Orton Development Inc. was successful in acquiring the plant from the city after several other developers were unable to execute the project. “The design approach and inspiration was by the existing building itself, adhering to many of the design principals of Albert Kahn,” says partner Marcy Wong.
The developer undertook a massive seismic upgrade by integrating the incomplete “spider-web” system started by a previous developer. Built over the water with views of the San Francisco Bay, the plant’s Craneway Pavilion, close to an acre in size, was rehabilitated as a multipurpose event venue. It is equipped with a state-of-the art sound system by Meyer Sound to accommodate an array of performances.
Roll-up glass doors were introduced on the south façade replacing the existing opaque steel panels to allow for a seamless indoor-outdoor experience. New landscaping complements the San Francisco Bay Trail, which surrounds the Pavilion on three sides.
Approximately, 36,000 sq. ft. of industrial steel sash windows as well as the skylights on the saw-tooth crenulated roofline were restored. In lieu of bricks and limestone, fiberglass-reinforced polymer was formed to match the dimensions, pattern and color of the original parapet. “Our intent was to not make large changes to the exterior,” says Wong.
The design team was also tasked to develop interior spaces for tenants occupying the main portion of the building. “The large open spaces have become offices for companies like solar energy innovator SunPower and outdoor outfitter Mountain Hardwear,” says Wong. “Our vision for the office spaces was to retain the building’s existing industrial features – the massive shell, continuous steel sash windows, floods of daylight and waterfront connection – as much as possible, while imbuing it with a contemporary feel worthy of cutting-edge contemporary companies.”
To accomplish this, the team designed cottage-sized “huts” to house a variety of programs within the large offices; these freestanding buildings also help to create human scale within the cavernous space. Existing concrete floors were polished and wood flooring was salvaged and arranged to indicate “streets” to circulate through the village-like arrangement of the smaller offices, conference rooms and support spaces. Additional lighting, stairs, ramps, platforms and walls were all designed to work with existing building features.
In SunPower’s entrance lobby, for instance, the team designed a folded steel suspension stair as a dramatic statement. The risers and treads of the stringer-less stair were created by folding a steel plate; a series of steel rods and cables were used for handrails. “The existing floor slab could not take the concentrated load of a conventional stair, so by suspending a very light steel stair (half the weight of a typical stair) we could avoid over-loading the floor slab,” says Wong.
In an arrangement between the developer and SunPower, a solar voltaic system was installed atop the south facing surfaces of the saw-tooth roofline, which happened to be at an optimal angle for the panels. The PV solar panels have the capacity to produce an output of one mega-watt solar energy. Under a Power Purchase Agreement, the panels now provide energy for both SunPower and Mountain Hardwear offices, the Pavilion and some common areas.
The original boiler room at the corner L between the pavilion and the main body of the structure has been repurposed as a restaurant. The massive dormant machinery is now a focal point and 20-ft. long family-style tables were cut from salvaged English walnut, which are also used in the Pavilion when the restaurant caters events. The stack of the machinery is lit red at night and has become an iconic representation of the project itself.
In its heyday, the Ford Assembly Plant was an important part of its community by way of providing jobs, particularly in times of economic hardship. After nearly half a century and a decade-long design and construction process, the plant is once again a vibrant part of the community. Completed in 2013, the $70-million project has won numerous awards including this year’s Palladio Award in the adaptive reuse category. Most importantly, “this Bay Area industrial icon is back at work, ready to power a new wave of industrial innovation,” says Wong. TB