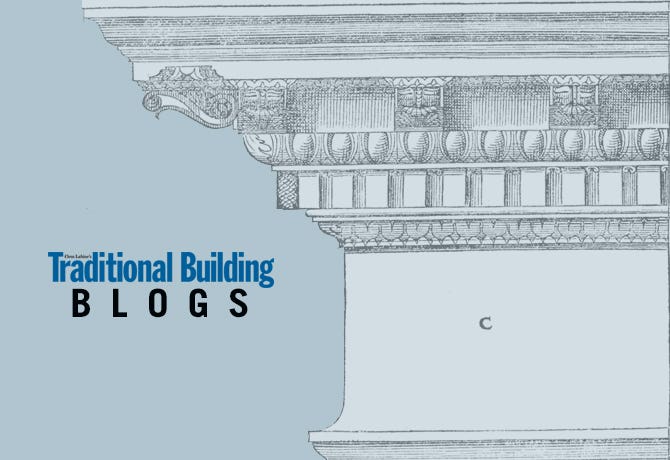
Rudy Christian
Time and Place
Working for the last couple of weeks in New Orleans, directing the 2009 PTN/TSA summer field school in partnership with the Tulane School of Architecture, has brought me back to a confusing reality. In what is arguably one of the most historically significant cities in America, you can’t buy hydraulic lime for restoration work. What’s more, finding a mason with experience or even an interest in using it is just about as challenging.
My first experience with this came in 2006 when PTN held its IPTW in the Holy Cross historic district. The concept was to hold a conference about preservation and traditional trades, in the area devastated by Hurricane Katrina, to offer both local tradespeople and displaced residents an opportunity to watch demonstrations on best practices for restoration work on historic homes. The demonstrations included wooden window repairs, traditional porch bracket making, traditional plaster work and several other disciplines relevant for homes in New Orleans. Four on-site workshops were held as well, including roof repair, decorative wooden porch restoration, lime plaster wall repairs and brick pier repointing.
The workshops involving lime plaster required bringing traditional hydraulic lime from Virginia Lime Works because none of the local suppliers carried the product. The closest thing available was, and still is, a product called “Southern lime type N,” which, unlike hydraulic lime, cures very slowly and reaches a much lower PSI rating. Consequently, masons make it “richer” by adding a little Portland cement, which causes it to act more like hydraulic lime. The local historic district preservation guidelines actually specify “Vieux Carre” mix, which includes type N lime, sand and Portland cement.
Because this has become the product of choice, hydraulic lime is not only unavailable, most of the local masonry supply yards have never even heard of it. In effect, using Portland cement has become the right way to do preservation work in the minds of preservation professionals, historic district managers and local tradespeople. Even the Barthe’ family, which has been plying its plaster trade for five generations, considers leaving out Portland cement to be bad practice.
How did hydraulic lime fall from favor?
Trying to comprehend how this all came to be is a bit beyond my capabilities, but it would appear that what was once standard practice, what literally built historic New Orleans, is now considered to be bad practice. To be fair, the beautiful historic brick buildings of New Orleans were not very likely built with hydraulic cement, but they weren’t built with Portland cement either.
A study of buildings in the ca 1835 Jackson Barracks, on the down river edge of Holy Cross, seems to show that natural Rosendale cement, from upstate New York, was very likely used in its construction. Access to materials from distant places is a part of New Orleans's history, but for the most part, this city was built with lime created by burning oyster shells that were readily available locally, as was the sand it was mixed with to make mortar and lime plaster. When that was the available material, it was the right thing to use.
It’s interesting to me how changing economies can change how we perceive right and wrong when it comes to building and preserving buildings. In reality, a mason working in New Orleans today can’t afford to use lime mortar and plaster because of the slow cure time. To put it in the words of master mason Raphael Perrault, who’s working with our field school students this year (think Southern drawl), “Lime mortar is too poor.”
When the field school program was put together for 2008 and 2009, the decision to use hydraulic lime was based on what the academic and trades education staff considered to be best practice, but working with our local tradespeople has made it quite clear they do not agree. It begs the question, who here needs to be educated?
Rudy R. Christian is a founding member and past president of the Timber Framers Guild and of Friends of Ohio Barns and a founding member and executive director of the Preservation Trades Network. He is also a founding member of the Traditional Timberframe Research and Advisory Group and the International Trades Education Initiative. He speaks frequently about historic conservation and also conducts educational workshops. Rudy has also published various articles, including “Conservation of Historic Building Trades: A Timber Framer’s View” in the “APT Bulletin,” Vol. XXXIII, No. 1, and his recent collaborative work with author Allen Noble, entitled “The Barn: A Symbol of Ohio,” has been published on the Internet. In November 2000, the Preservation Trades Network awarded Rudy the Askins Achievement Award for excellence in the field of historic preservation.
As president of Christian & Son, his professional work has included numerous reconstruction projects, such as the historic “Big Barn” at Malabar Farm State Park near Mansfield, OH, and relocation of the 19th-century Crawford Horse Barn in Newark, OH. These projects featured “hand raisings,” which were open to the public and attracted a total of 130,000 interested spectators. He also led a crew of timber framers at the Smithsonian Folk Life Festival, Masters of the Building Arts program, in the re-creation and raising of an 18th-century carriage house frame on the Mall in Washington, DC. Roy Underhill’s “Woodright’s Shop” filmed the event for PBS, and Roy participated in the raising.
Christian & Son’s recent work includes working with a team of specialists to relocate Thomas Edison’s #11 laboratory building from the Henry Ford Museum to West Orange, NJ, where it originally was built. During the summer of 2006, Rudy; his son, Carson; and his wife, Laura, were the lead instructors and conservation specialists for the Field School at Mt. Lebanon Shaker Village, where the 1838 timber frame grainery was restored. In July and August 2008, Rudy and Laura directed and instructed a field school in the Holy Cross historic district in New Orleans in collaboration with the University of Florida and the World Monuments Fund.
Rudy studied structural engineering at both the General Motors Institute in Flint, MI, and Akron University in Ohio. He has also studied historic compound roof layout and computer modeling at the Gewerbe Akademie in Rotweil, Germany. He is an adjunct professor at Palomar College in San Marcos, CA, and an approved workshop instructor for the Timber Framers Guild.