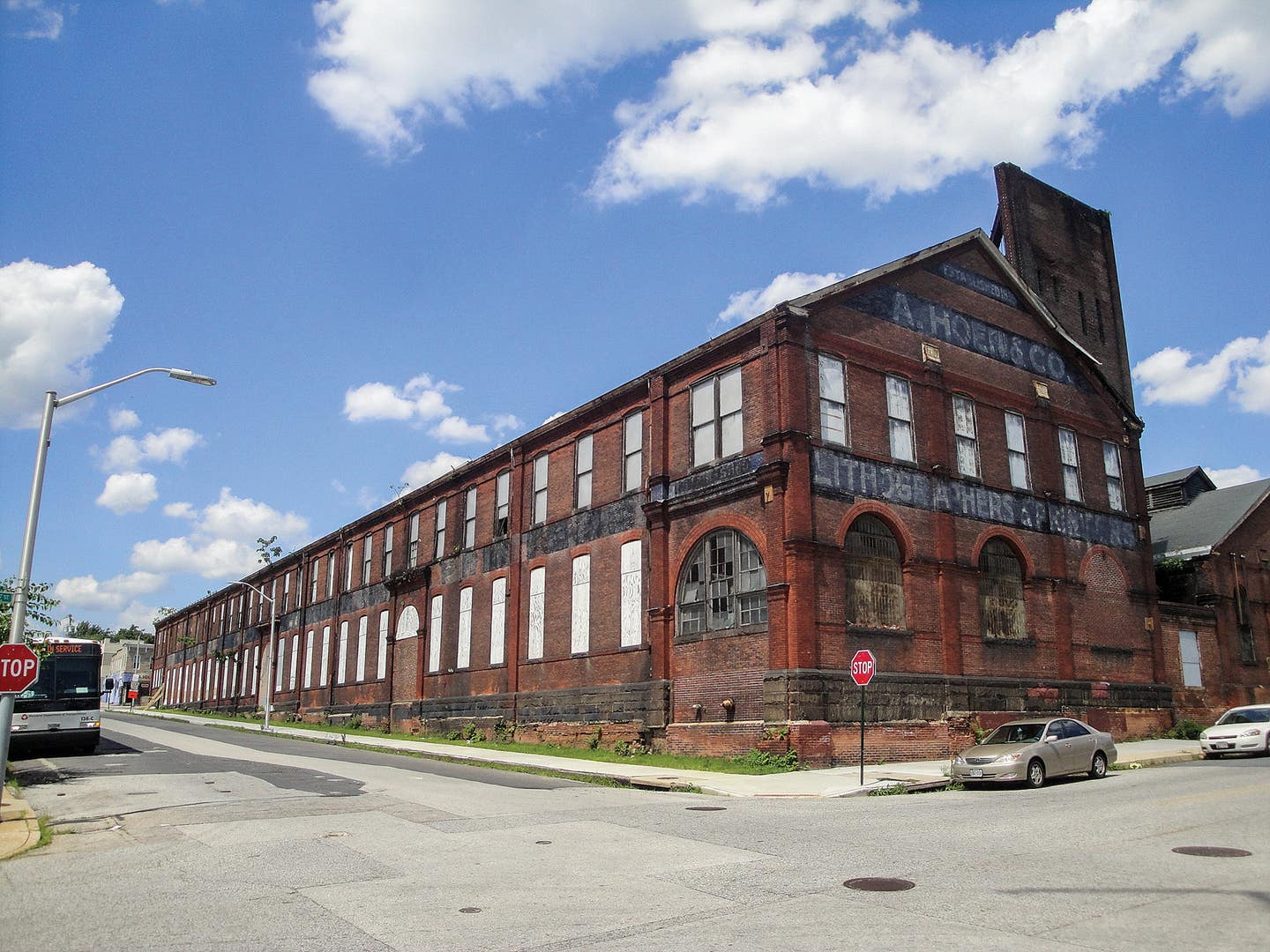
Restoration & Renovation
Ziger|Snead Architects Transforms A. Hoen Lithograph Company
Architect Ziger|Snead Architects
Adaptive re-use projects are something of a chrysalis, and one of the most dramatic rebirths is the steam-era factory that metamorphoses into 21st-century office space, such as the rehabilitation of the A.Hoen & Company site now underway in a former smokestack district of Baltimore, Maryland.
The buildings, which occupy an entire city block in East Baltimore, were a major area industrial center for over a century, but when abandoned in the 1980s joined other sites in the distressed “Amtrak corridor” that’s suffered from lack of investment for a long time. “The A.Hoen Lithograph Company was in some unbelievable buildings,” explains Steve Ziger, FAIA and partner at Ziger|Snead Architects, “the biggest being like a cathedral to industry.” The team goes there a lot, he says, “and the site definitely resonates with the ghosts of workers, the sounds of presses and manufacturing, and an optimism that had disappeared from the area.”
At its peak, A.Hoen & Company was a complex of six buildings. According to Jonathan Lessem, AIA, LEED AP and Principal, “The star of the show is Building One, which is quite long—320 ft. and extending the full length of the lot. Building One and Building Four date to 1885 (built for a previous occupant) and are the original buildings on the site.” Building Two was added a bit later when the Hoens bought the property in 1902, and what the architects call Building Three occupied space between Buildings One, Two, and Four that was filled in 1915-16. “For this project, Building Three, with the exception of its structure, has been removed to allow for a court that will reinforce a sense of community between all of the future offices, and Buildings One, Two, and Four are restored as part of a Historic Tax Credit redevelopment.”
Building One is a textbook example of late 19th-century industrial construction, with heavy, solid-brick masonry exterior walls supporting heavy-timber framing inside. Says Lessem, “There’s a tall first floor with a mezzanine on one end, and a second floor with its own mezzanine above that.” Building Two he says is very similar—a very tall, two-story building, but without a mezzanine on the second floor. “When we first went to the buildings, everything was boarded over and it was hard to see inside without a flashlight. Now that it’s opened up, the view is an exquisite interior longer than a football field with heavy, barn-like framing, thick, exterior masonry walls, and windows on both sides.”
He adds that while the buildings are utilitarian and short on ornate decoration, there is a lot of detail and appeal to the interior. “Because this is a historic tax credit project, brick that was exposed historically cannot be covered. However, that will ultimately be an aesthetic asset.”
In fact, the project benefits from multiple incentive programs: the Maryland Sustainable Communities Rehabilitation Tax Credit, New Market Tax Credits, Federal Historic Tax Credits, Baltimore City Housing & Community Development grants, and a C.O.R.E. grant from the State of Maryland. “All of our materials are being approved by the Maryland Historical Trust and National Park Service,” says Lessem, adding that a lot of their projects that transform historic buildings involve Historic Tax Credits. “If it weren’t for the tax credits, this project probably would not have happened.”
What’s more, the A.Hoen adaptive re-use is something of a snapshot of the Ziger|Snead project list. “A large part of our practice is in Baltimore because there’s so much to do here,” explains Ziger, “and we like to help give back to our community and transform neighborhoods.” He says projects like this—turning an abandoned complex into a community asset—have a lot of meaning for the firm. “They’re not easy. They take a lot of patience, effort, and give and take. But we do these kinds of complex, messy projects really well, and we do a lot of them.”
When completed later in 2019, the buildings will house offices for an uncommon mix of uses. As Ziger explains, the vision of developers Cross Street Partners is to not only transform a blighted property into a community asset, but to also find an opportunity for social services and non-profits to be together, collaboratively, in a campus setting in East Baltimore. “It’s not the same as turning this site back into a printing facility; it’s really recognizing the needs of the community and using the buildings as a catalyst for improvement.” As of now there’s a “critical mass” of social-service non-profits committed to the project, says Ziger. “That provides a kind of anchor tenant, and helps to define the type of culture that’s being sought around what might be called a consortium of non-profit agencies.”
Stemming Deterioration and Invasion
What’s the path from late 19th-century industrial plant to 21st-century office space? Not without speed bumps. Says Lessem, “One of the challenges for a building like this—especially one historically protected—is meeting modern environmental codes.” He says the rehabilitation of the core shell of the building is designed to achieve a minimum of U.S. Green Building Council’s Leadership in Energy and Environmental Design (LEED) Silver, but normally they would also be able to attach insulation to the inside walls throughout the building. “We’re restricted from doing that now and we have to leave the brick exposed.” He says retrofitting building systems into a structure that didn’t originally have them is another challenge, and other limits on what they can do drives decisions about the efficiency of building systems and the like. “Aside from that, there’s a lot of unknowns. With a building the condition of this one, the deeper you get in, the more you uncover.”
Indeed, one might expect a former industrial site to hide a few lingering environmental issues, yet few would anticipate they’d be literally growing out of the woodwork, which is the case with the Paulownia trees. Native to China where they are cultivated for lumber, Paulownia trees are extremely fast growing—as much as 20 ft. a year—and so tolerant of urban environments America considers them an invasive species. As luck would have it, the soft, lightweight seeds of the Paulownia were a popular packing material of Chinese exporters in the 19th century, and some had found a home in the A.Hoen buildings with dramatic consequences.
“The lime mortar in the historic masonry was very favorable for tree growth,” explains John Matteo, PE, Principal 1200 Architectural Engineers “and over time the roots would propagate within the wythes of the brick masonry and the trees would grow right up into the walls—to the point where the walls would start bulging out.” As Matteo recalls, all the buildings were beset by trees, but less so in the more modern, concrete-block buildings. Evidently, water drew the trees towards the outer wythes of the multi-wythe walls. “Sometimes you would just see leaves coming out of the exterior walls, so in several locations we actually had to remove full tree trunks as much as 16 in. diameter that had grown integrally with the wall.” He adds that commonly there were roots propagating along the eaves and gutters where water might be.
“Unfortunately, we found the only solution was to really dig in, track down the roots that were growing in the wall, and remove them because even a small amount left behind would regenerate and start causing problems again.” No surprise, the Paulownia is sometimes called the Phoenix tree because one of its advantages as a cash crop is the roots begin growing again soon after the trees are harvested. Matteo adds that though biocides were contemplated, they were not used for environmental reasons.
For the most part though, he says structurally, the historic buildings remained very robust. “There is a lot of capacity in the historic timber and masonry walls by virtue of the previous industrial application, and we didn’t have to do a general upgrading of capacity for the new uses.”
Problems with the timber framing were mostly the result of moisture damage due primarily to failure of the exterior envelope—leaking roofing, windows, and doorways. “We wanted to keep the repair work consistent with the historic construction, so the timber repairs are typically either additive by sistering with new sawn or manufactured lumber or, in some cases, full replacement of members.” In one area where there was a change in loading, they added new wood bracing members. “For example, we’re adding a new area for mechanical units where a water tower used to be,” says Matteo, “so we’re reinforcing a column with new bracing elements to increase timber column capacity.”
Overall, he says they’re very excited to be involved with the revitalization of a set of buildings like this. “Usually they involve a certain amount of creativity in terms of really maximizing the use of the buildings, but that’s why I’m attracted to them,” adds Matteo. “When you’re working with buildings like these, they’re so massive they’ve got a lot of potential, and are therefore very versatile as far as types of new uses.”
Gordon H. Bock is an architectural historian, instructor with the National Preservation Institute, and speaker through www.gordonbock.com.