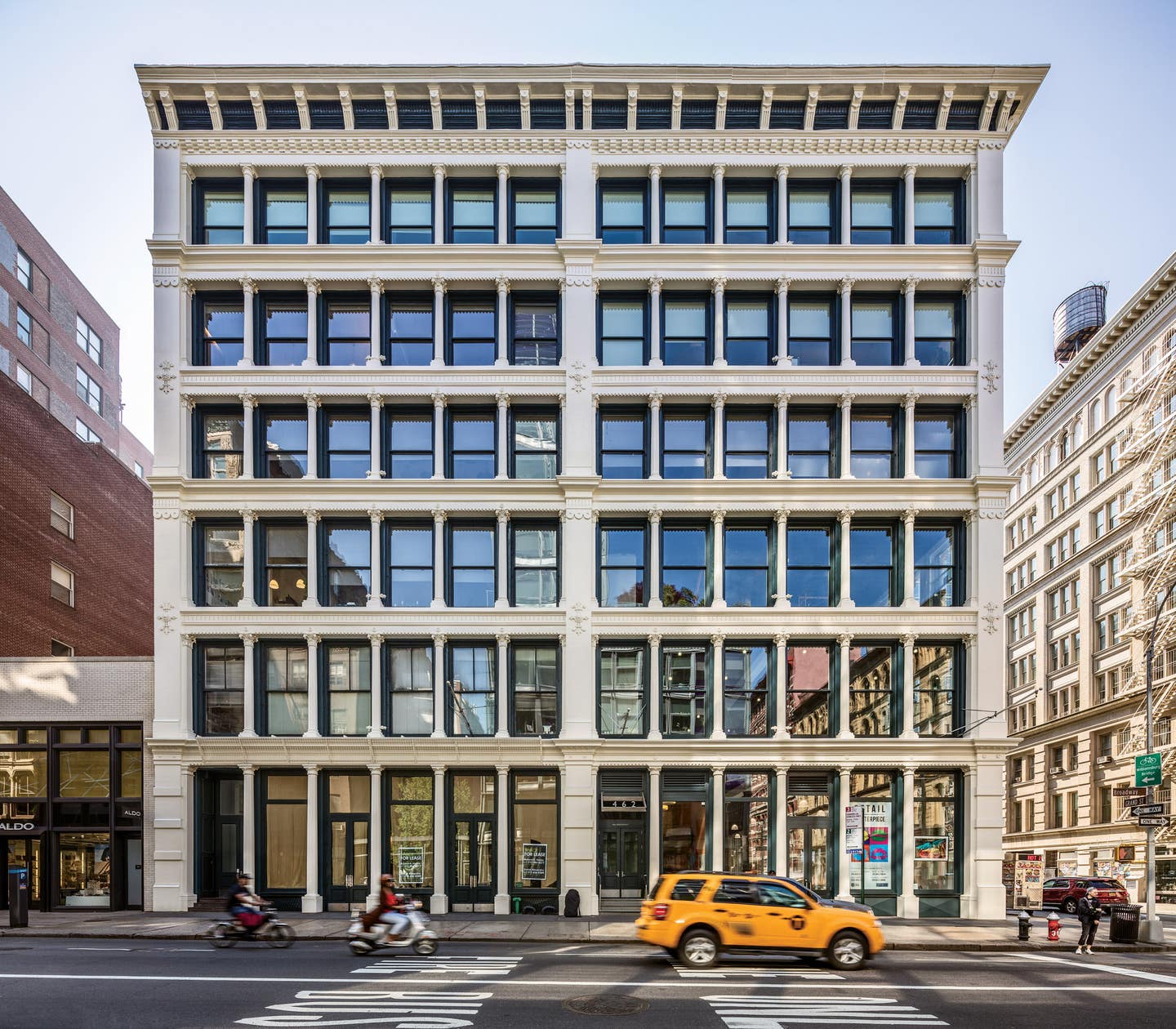
Restoration & Renovation
PBDW Architects’ Landmark Restoration
Project SoHo Cast Iron Building Restoration
Architect PBDW Architects
In the SoHo Cast Iron Historic District of New York City, 462-468 Broadway reigns supreme. The massive white wedding cake of a building—it rises six stories, fronts three streets and has a façade that measures 40,000 square feet—lays claim to being the district’s largest structure that is fully clad in cast iron.
Designed by John Correja as the home for the dry-goods purveyor Mills & Gibbs, it was erected in 1880, shortly before cast-iron facades fell out of fashion in the city. Today, its main tenant is the International Culinary Center, a private school.
The landmark French Renaissance-style building remained largely untouched until its columned façade was restored by PBDW Architects, the half-century-old New York City firm that has brought a variety of houses and institutions, including the Central Park boathouses, the Park Avenue Armory, the Palace Theatre, and the Louis Armstrong House Museum, back to their past lives.
The idea for the restoration began over 35 years ago when real estate developers Stephen Meringoff and Jay Shidler bought the building in 1981.
A restaurant on the ground floor that had a long-term lease stalled the work until 2015, when PBDW partner in charge Sam White, FAIA, and his team, which included project architect Brigitte Cook, AIA, and job captain Adelaide Palum, were commissioned to restore the exterior.
“The building was in pretty good shape and well maintained and preserved,” Cook says. “But the paint was peeling. Once we started analyzing it, we found that there were a few more problems, including one section that was punched in—it looked like it had been hit by a car.”
In addition to repainting the building in its historic color scheme, the PBDW team, which worked closely with New York City’s Landmarks Preservation Commission, repaired the galvanized sheet-metal cornice, removed non-historic roof alterations, restored the ground-level storefront, replaced two floors of 11-foot-high double-hung wood windows, restored fire shutters and reconstructed a variety of original ornamental cast-iron elements.
“Our priority was to maintain the elegance of the original design while preserving as much original material as possible,” White says, adding that he took particular pleasure in watching the removal of a section of red granite that had been added to the street-level facade in the 1960s.
“I had been waiting for 35 years to get it off,” he says. “The original cast iron was still there.”
A detailed paint analysis revealed that the cast-iron elements originally had been faux painted to look like colored marble, and the team decided on using the original base color, punctuating it with windows that have dark green frames.
“We saw evidence that perhaps more than one color of paint was used on the original cast-iron elements,” White says, “but we feel the single color is quite handsome. The green for the windows was an architectural choice that visually separates them from the columns and gives a muscularity to the building.”
Stripping the paint was a painstaking process. “It took a long time,” Cook says. “There were areas that had 10 to 20 coats.”
She adds that even with the new paint, “the texture of the cast-iron still reads. It doesn’t look brand new.”
The columned façade’s alternating window bays have a robust rhythm—AA on Broadway, ABCBA on Grand Street, and DD on Crosby Street—that is accented by Corinthian capitals on the As and Cs and Modified Doric capitals on the Cs and Ds.
It was the 108 Corinthian capitals that created the greatest challenge. When the team removed their 135 years of layers upon layers of paint, the 20 individually cast acanthus leaves that defined each capital became unstable.
The defect lay with the design. The leaves were mechanically attached to the surrounding shaft with a bell housing or cuff that flared at the top, allowing them to project. Packs of rust, built up through the years, caused the cuffs to crack and also compromised the mechanical attachments.
“The bell housings had another design function,” White says. “They allowed a more robust capital to fit on a more slender column shaft, which adds to the delicate detail and hierarchies of the elevations.”
Although the team explored the use of resin capitals, it chose to work with cast iron because it allowed them to maintain the building’s integrity. The team kept the majority of intact decorative elements and only replaced the inner bell housings and the most severely damaged pieces.
“The resin was very beautiful, but the cost of the casting itself wasn’t that different,” White says.
The team restored more than 1,549 of the original 1,976 cast-iron elements on the 108 Corinthian capitals. The cuffs were replaced with newly designed attachments that replicate the intricacy and depth of rhythm of the originals, and the original intact acanthus leaves were restored and reinstalled.
“It was special to see how the original capitals and leaves were put together, which allowed us to improve the details of assembly,” Cook says.
She added that this also allowed the team to give all sides of the capitals three layers of protective paint coatings.
The team erected scaffolding over the whole building, which houses offices on top and retail stores on its lower levels, and worked section by section, using a 50-foot by 200-foot space on one of the building’s lower floors as a workshop.
As the scope of the project widened, so did the time frame—it took over a year to complete everything.
“It’s really a tribute to the owner,” says White, “because you need a cast-iron stomach to allow an architect to do what we did and keep the lower floors of the building out of commission for so long.”
The project has received numerous accolades. It won a Stanford White Award, a MASterworks Award from the Municipal Art Society for Best Restoration, and a Lucy G. Moses Preservation Award from The New York Landmarks Conservancy.
The restoration was part of a master plan made by PBDW that includes multiple configurations for windows and doors on the lower floors that will be modified as new tenants move in.
“In the future, we may put awnings on the second-floor windows as they originally did,” White says. “We have permission from the landmarks commission to do this.”
White calls working on 462-468 Broadway “the chance of a lifetime.”
Unlike some of the firm’s other high-profile restorations, this one is on view all the time. “It dominates the public realm,” White says. “It engages you at street level.”
Key Suppliers
Architect PBDW Architects
General Contractor Archstone Builders
Restoration Contractor MRS
Metal Fabrication Allen Architectural Metals
Window and Door Fabricators Artistic Windows
Coatings Righter Group Tnemec Paint and Elastometal