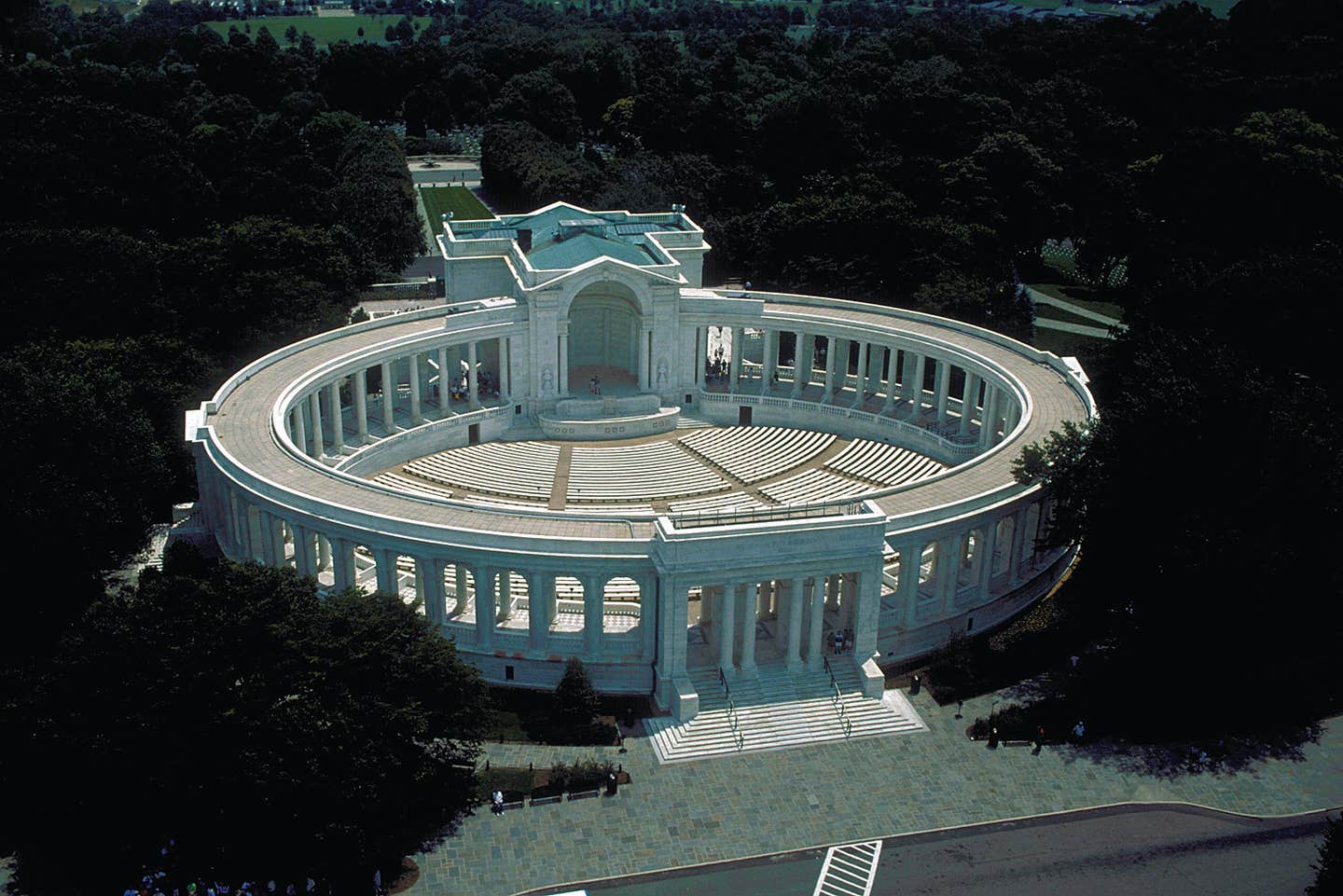
Restoration & Renovation
New Life for Historic Pocket Doors
Key to Arlington National Cemetery Historic District is the Memorial Amphitheater and Reception Building, designed by architectural firm Carrère & Hastings in the Beaux-Arts style. In daily use for ceremonies since the 1920s, the amphitheater is subject to ongoing preservation treatments, including those for balky pocket doors. In 2015, Arlington National Cemetery Division of Engineering commissioned the National Park Service Historic Preservation Training Center Historic Architecture Team to assess window and door conditions at the MARB in preparation for the amphitheater’s centennial celebration in 2020.
Built by the George A. Fuller Company between 1915 and 1920, the amphitheater was a state-of-the-art heavy-masonry construction, but component features—including windows, doors, and associated hardware—were subpar for the time due to World War I-era budget restrictions. For example, records show hardware bids from Yale & Towne Manufacturing Company of Stamford, Connecticut, were too costly by several hundred dollars, so the government selected the lower bid from Russell & Erwin Manufacturing Company of New Britain, Connecticut. Carrère & Hastings might have included pocket doors in their design, as swinging doors would conflict with the building configuration or exterior appearance. Nonetheless, R&E did not specify any hangers for exterior pocket doors.
When pocket doors (aka sliding doors) first appeared in the early 1800s they traveled on rollers built into the bottom of the door, but by the early 20th century, most systems suspended doors from overhead hardware. HPTC identified three types of pocket doors in two pairs of each type, symmetrically arranged around the central axis of the amphitheater. However, the way the contractor built the pocket door mechanisms into the solid masonry construction made it difficult to view the hanging hardware. Fortunately, during the window and door preservation treatment phase, 2019 to 2021, a careful investigation by the HPTC Wood Crafting Team revealed that the pocket doors hung on an enclosed track and trolley wheels made by the McCabe Hanger Mfg. Co. of New York, one of several brands on the market, which advertised “hard, fiber wheels ensuring long life and quiet operation.” While Carrère & Hastings’ large-scale drawings of the doors and their frames show a label reading “hold space for hangers,” who selected the long-gone McCabe product and why remains a mystery.
Upon inspection, it was evident that the door hanger wheels were, indeed, fiber material—now deteriorated, leaving them noisy and difficult to operate. “The original wheels are adhered to bearing raceways containing loose ball bearings,” explains Mike Heacock, HTPC project supervisor. “In most of the hangers, the material had detached from the raceways and was partially delaminated or missing, so we decided to replace all door hanger wheels with modern material.”
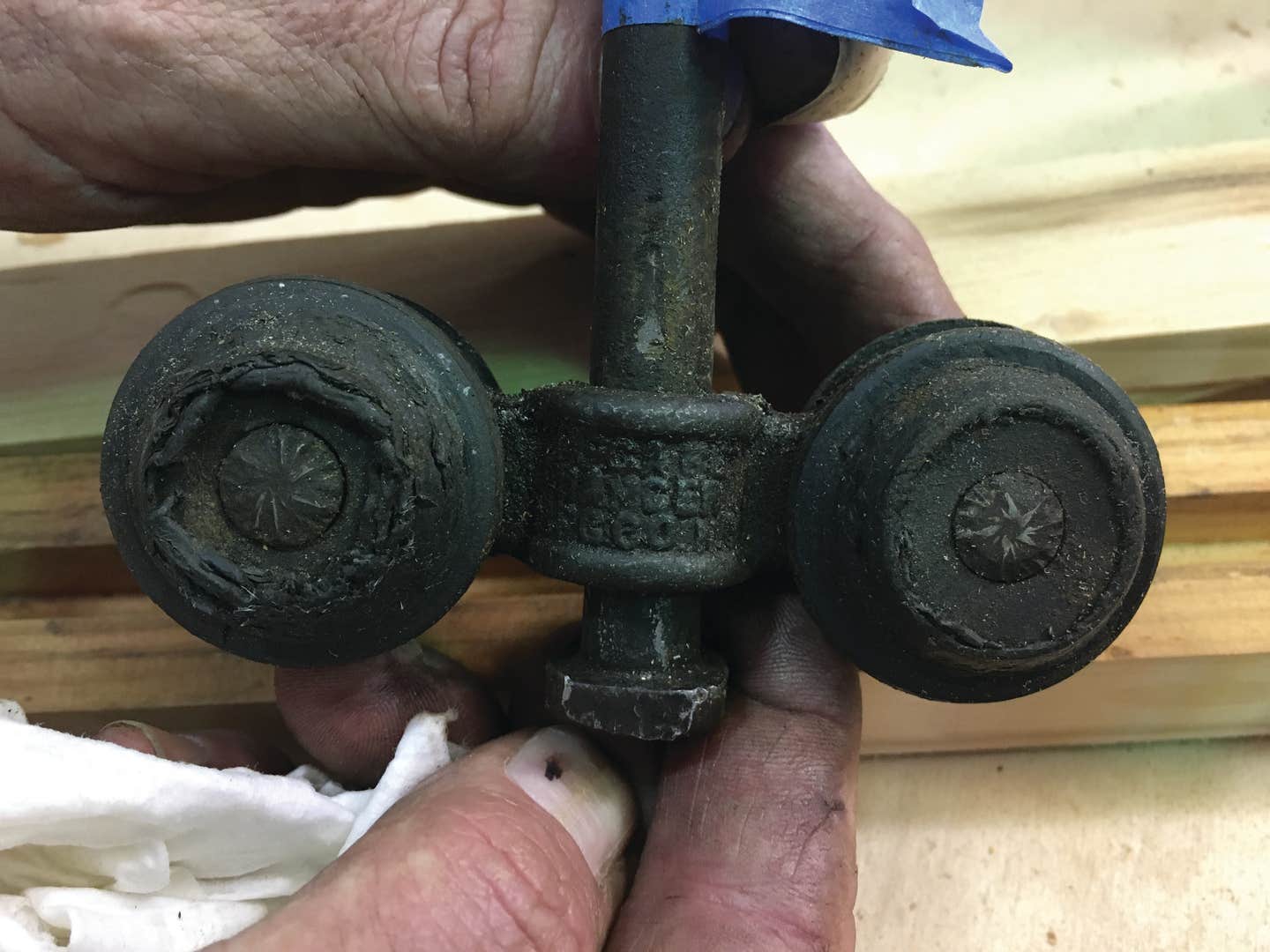
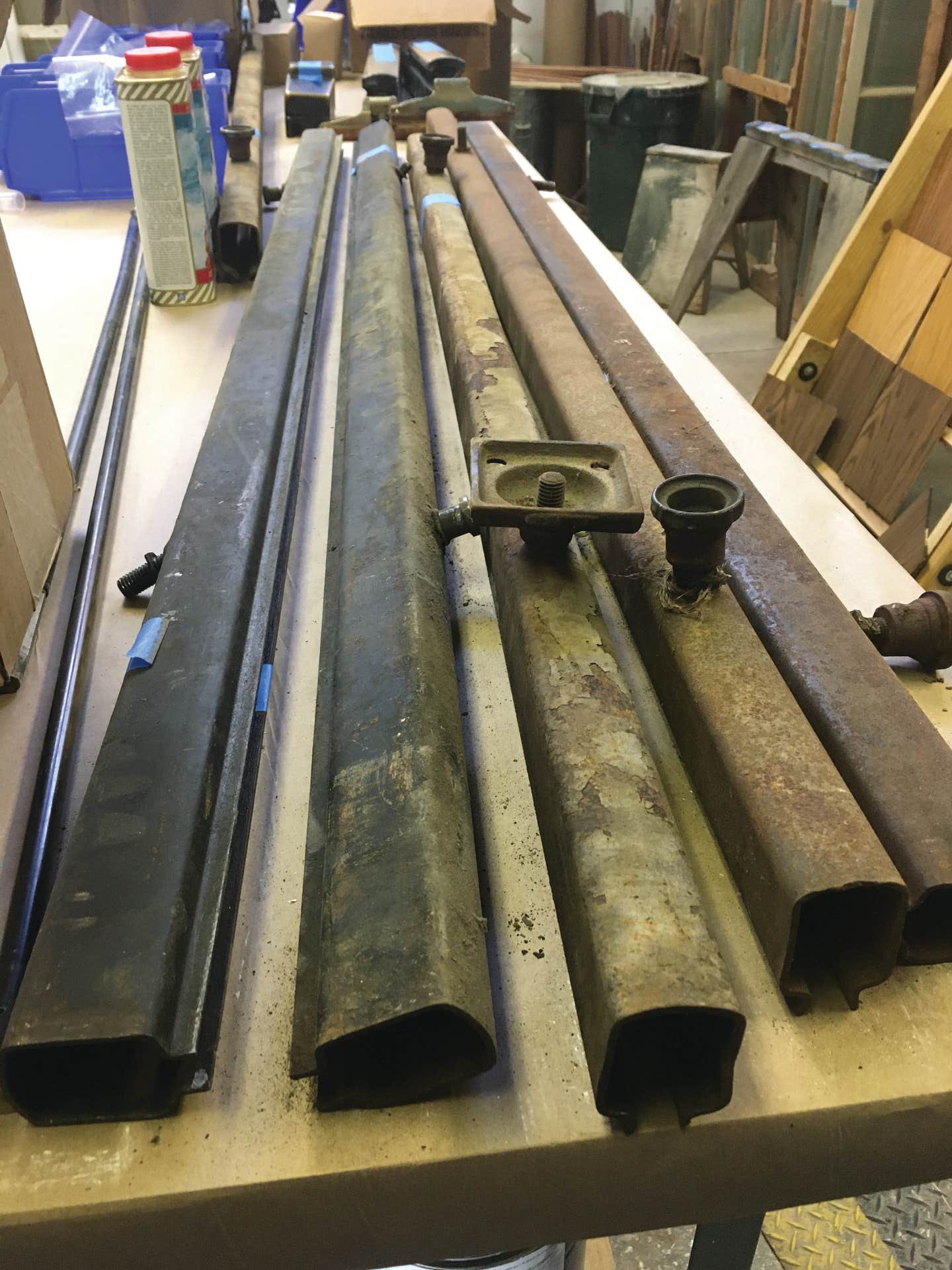
The team took the door hangers to Foltz Manufacturing and Supply in Hagerstown, Maryland, who machined replacement wheels from ultra-high molecular weight polyethylene. The replacement wheels re-used the existing bearing raceways, loose ball bearings, and hanger assembly, but required new axles. The UHMW material will operate in the same manner as the fiber wheels, insuring smooth and quiet operation. Ball bearings were lubricated with a dry lubricant (CRC® Dry PTFE Lube) that does not attract dirt and debris.
The next step was to straighten and reinstall the hanger tracks. In the McCabe pocket door system, the track comprises two independent U-shaped sections that join at the door opening midpoint to enclose the trolleys. Some of the tracks required manipulation to return them to the original shape using various methods, including applying large hammers and words of encouragement. The McCabe system is designed to allow mounting the tracks and hangers during construction without leaving the tracks in place until the doors are ready to hang; track height is adjustable via threaded screws. This was the case at MARB, but no provision was made for access to the trolley adjustment after building finishes were applied. The team’s solution was to mount the tracks at a prescribed height based on the height of the door, the trolley adjustment range, and the track distance from the finished floor. The trolley was then mounted to the door and preliminary height adjustments were made to the trolley and tracks. Next, one section of track was removed and set aside, and a door with trolleys attached was slid into the track. If the door did not slide freely or was not plumb and level, it was removed and adjusted—a very labor-intensive and physically demanding process.
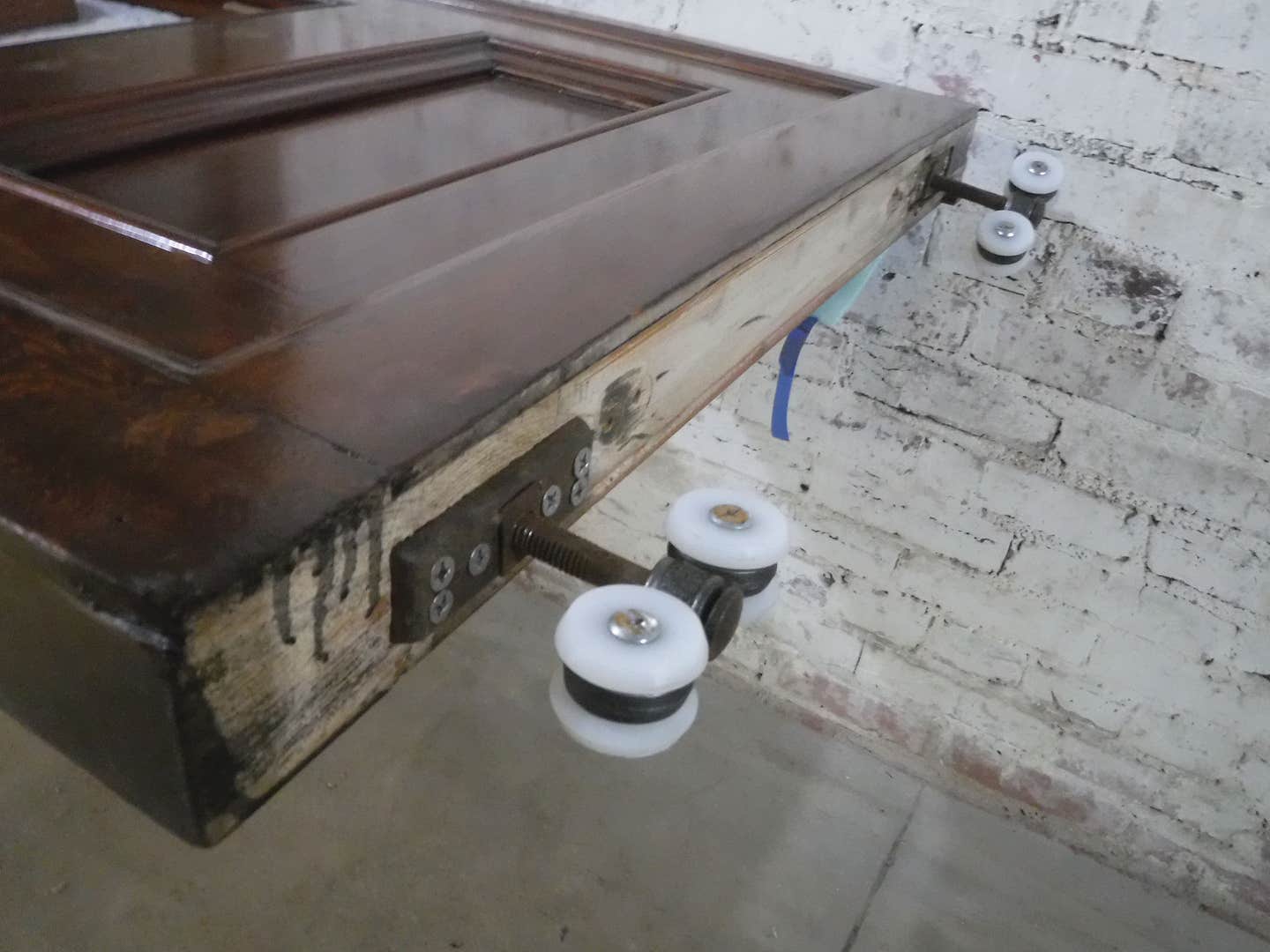
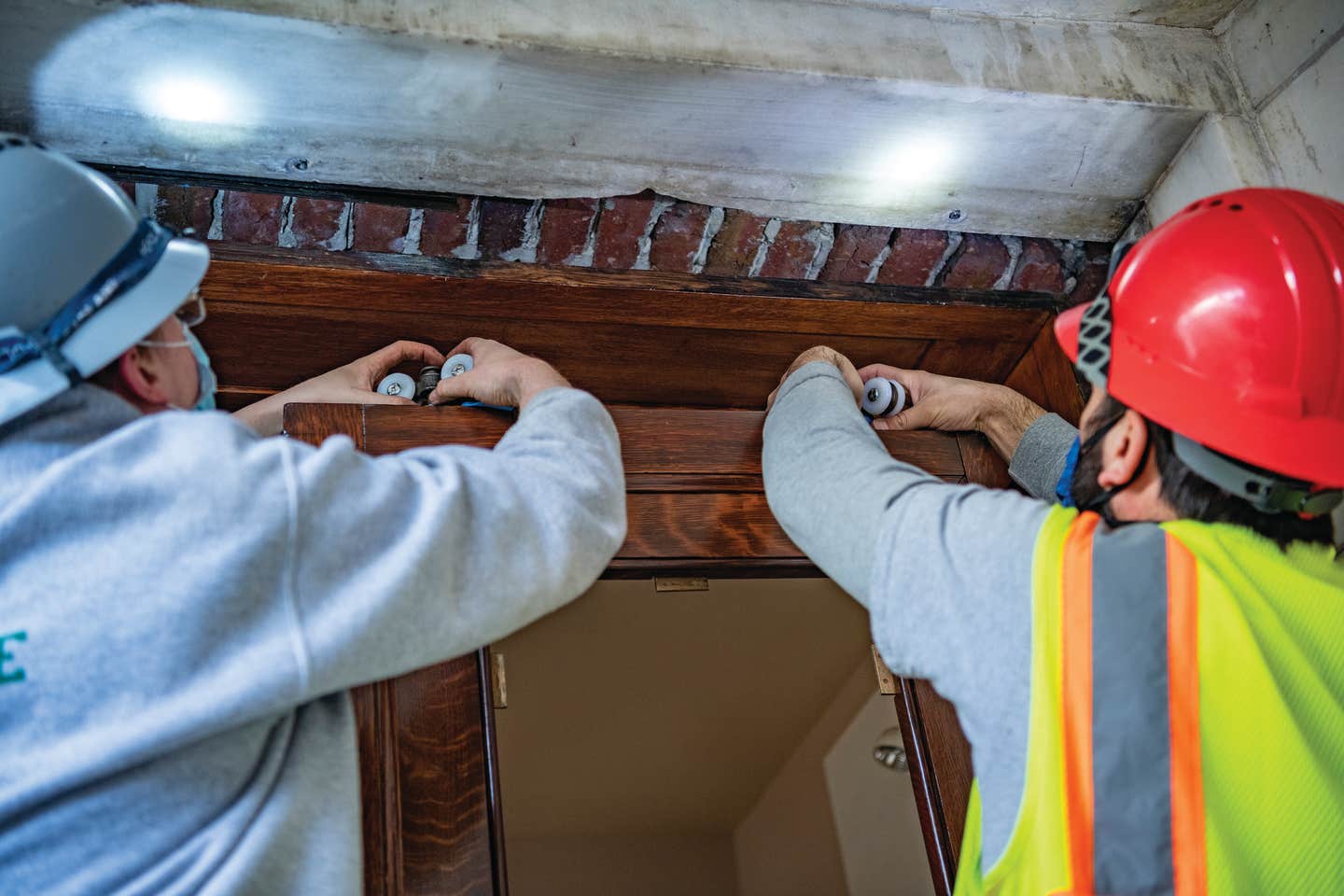
When the first door was complete, it was pushed fully into the pocket and the second door was slid onto the same track. The previously removed section of track was then mounted in its prescribed location, and the second door was slid onto it. After both doors were mounted and adjusted, the team installed door stops in the track center. “These stops are placed so as to limit each door to the closed position of the door opening,” says Heacock, “and were adjusted to insure that the doors latched together correctly.”
The project included rehabilitation and re-use of the existing Russell & Erwin door hardware, including the door pulls, pocket door locksets, and related trims. Avoiding polishing, HPTC cleaned dirt, grease, and unsightly oxidation from all door hardware through gentle abrasion with a combination of mild solvents, synthetic pads, and fine bronze wool to maintain the weathered patina.
Arlington National Cemetery is delighted with the performance and appearance of the restored pocket doors. They are pleased that the original historic hardware has been given new life, and cemetery managers anticipate that, with routine maintenance, the doors will operate using the original hardware for another 100 years.