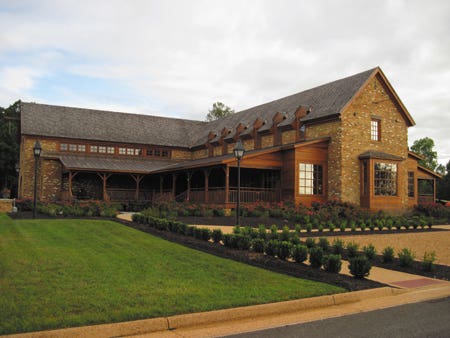
Projects
New Kent Winery by Hopke & Associates
Project: New Kent Winery, New Kent County, VA
Architect: Hopke & Associates, Williamsburg, VA; John A. Hopke, RA, LEED AP, principal
General Contractor: E.T. Moore Manufacturing, Richmond, VA; E. Taylor Moore Jr., president
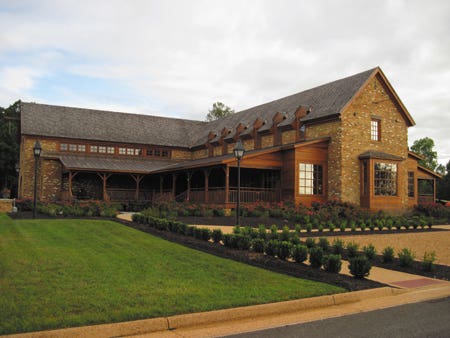
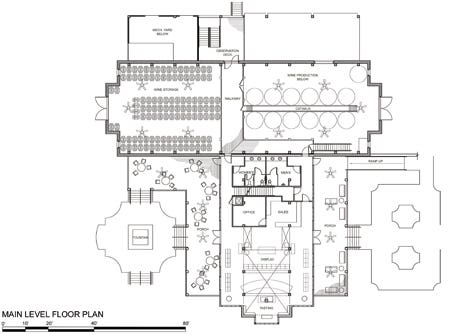
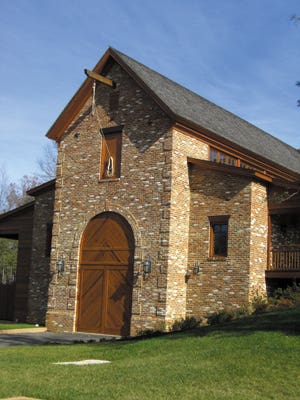
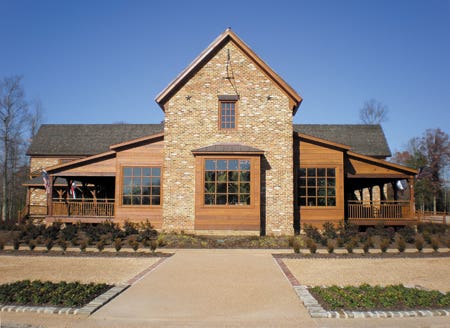
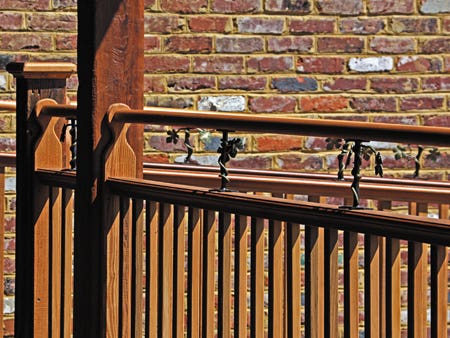
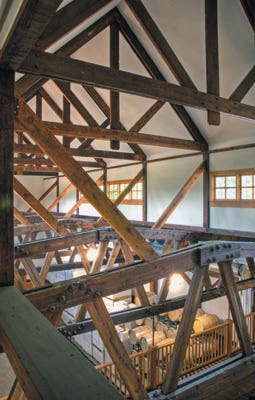
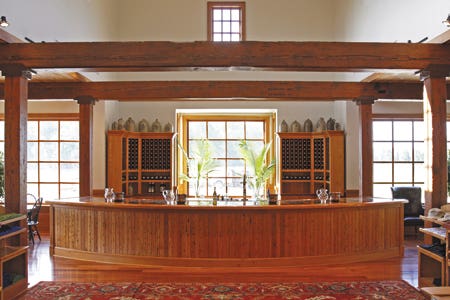
Situated between Richmond and Williamsburg, VA, New Kent County was known until the late 1990s for its scenic stretch of undeveloped land, most of which was privately owned. Boddi-Noell Land and Development of Rocky Mount, NC, and a group of investors teamed up to acquire about 5,000 acres of this land, designating half of it for the New Kent Vineyards.
The master plan aimed to preserve the county's rural atmosphere with deep natural buffers incorporated along the main roads to conceal homes from passersby. Instead of installing traffic lights and stop signs, five roundabouts were built for a new parkway. The development was separated into five land bays, each with clusters of residential neighborhoods surrounding commercial establishments, which would consist of a winery, farmers' markets, shopping centers, a spa and inn, an equestrian center and golf courses. The New Kent Winery was the first project that would set the architectural tone for future buildings.
In 2001, the first grapevines were planted on the 26-acre winery. While the vines matured, plans were made for the winery's design. Pete Johns, the managing partner of the New Kent Winery, envisioned a building that would reflect the history of the region while housing state-of-the-art wine-making machinery. To achieve this, Johns enlisted the help of Tom Payette, an acclaimed wine-making expert, and E. Taylor Moore Jr., president of Richmond, VA-based E.T. Moore Manufacturing, for Moore's extensive supply of reclaimed building materials and construction experience.
"Pete Johns and I have known each other for 22 years. We worked together on another project and Pete knew most of my inventory," says Moore. "Pete had always eyeballed these 40-ft. long trusses and he'd made a comment, 'Don't get rid of them Taylor, one of these days I'm going to have a project to put them in.' The winery was essentially designed around these 1901 railroad trusses that I salvaged from Richmond, VA."
John Hopke, principal at Hopke & Associates of Williamsburg, VA, was hired as the architect for the project in 2006 and formed a design team together with Johns, Payette and Moore. The four toured over 30 wineries in Virginia, Western Virginia and North Carolina to determine the programmatic goals for the building's design. "One of the key concerns was having an environment in which to sell wine and give tours that would provide a good experience but avoid taking tour groups to the working floor," says Hopke. "We saw that some of the other wineries had the tour walk right through areas that had to be maintained clean all the time. Johns also wanted to accommodate a certain number of tanks but with the ability to double that amount in the future."
The winery was built on a knoll overlooking the vineyards. The production wing's wine storage areas could take advantage of the constant cool temperatures underground. It was decided early in the design process that the winery would be a heavy timber post-and-beam construction consisting of two perpendicular wings for the production and retail areas forming a T-shaped floor plan. The retail wing was proportioned to create a uniformed balance to the production wing, whose dimensions were directly influenced by the antique heart pine trusses from Moore's collection – a total of eleven trusses placed 10-ft. apart that determined the 4,800-sq.ft. space in the production area, combined with another 13,000-sq.ft. of retail space and covered porches.
"When we sat down to work on the architecture of this building, one of the things I wanted to accomplish was to make it look like it belonged in New Kent County," says Hopke. "The county was under a lot of pressure to grow and, at the same time, preserve its agricultural character. So, I tried to draw upon traditional agricultural architecture. For example, barns were often built with a continuous raised roof at the ridge for ventilation and light. That form became our starting point for the winery."
The production wing is a three-story, clear-spanned space with a 43-ft high ceiling. The antique trusses support a second set of timber trusses, creating the distinctive roof lines. The lack of columns maximizes useful floor space below, providing efficient working room and potential for additional wine tanks in the future. Between the 12:12 pitched roof and trusses, a band of clerestory windows for natural lighting were custom made by E.T. Moore Manufacturing (as were all windows and doors for this project) using heart pine wood.
Structural insulated panels, a 6- to 8-in. thick wall consisting of Styrofoam placed between two sheets of plywood, were installed outside the timber-frame construction as well as the roof to maintain the production area's required temperature of 50-55 degrees. Suspended from the trusses with reclaimed cast-iron rods is the walkway for tour groups that leads to the retail wing.
"On the front façade, we have a bay window that is like a display window of a Colonial storefront," says Hopke. "In the 18th century, the gables would turn towards the street if it was a business as opposed to a residence. Somewhere on that gabled-façade there would be a bay window to display goods. That's what we were picking up on at the southeastern façade."
Visible through the bay window, a tasting bar was custom made by Moore to serve around two-dozen people at once. The 22-ft. long curved bar top features a unique piece of antique heart pine with a growth defect that frames merlot-colored lyptus, imported from South America, and green Tinos marble insets. The sides of the bar are covered with reclaimed heart pine left unfinished for an industrial appearance, which is contrasted with a bar rail of newly milled wood of the same species.
The sub-floor of the tasting room is made of reclaimed hemlock wood (salvaged from the Utica Hosiery Mill in Utica, NY). It was originally 4½-in. thick, but the faces were sliced off – ½-in. off the top and bottom – and reserved for the ceiling of the porches. The sub-floors were finished with lyptus wood with a heart pine boarder and complementary wainscoting stained in shades of red and yellow.
The original surfaces of the hemlock wood were used to conceal the new lumber on the porches located on the south and north sides of the retail wing. The siding, milled from century-old-cypress logs that had been submerged in North Florida rivers, surrounds large expanses of custom-made French doors and windows. The double handrail system features hand-wrought iron grapevine motif supports that were made by a local blacksmith.
"In Virginia, handrails had to be 42-in. tall," says Moore. "I made a handrail system and put it up but it blocked the views of the outside; it also blocked the view looking inward. I took the handrails off and scaled everything down in proportion and made a 32-in. tall rail with smaller pickets. In order to meet the code, I installed an additional small 1¾-in. round handrail on top, but as it spanned 10-ft. it tended to sag. I was thinking of using mahogany supports but a local blacksmith said he knew exactly what to put there. I like mixing mediums and the hand-wrought look, to my delight the supports were perfect.
"Other reclaimed materials supplied by E.T. Moore Manufacturing included 400,000 wood-molded, sand-casted handmade bricks salvaged from a Richmond warehouse built in 1904; the bricks were previously used on two other projects and are believed to have been molded before the Civil War. The winery's cornerstone was salvaged from a ca. 1904 Colonial warehouse. Standing seam copper roofing on the porches complements the more than 70,000 handmade roof shingles that were milled from smaller pieces of the cypress logs used on the sidings. "The other unique thing about this building is that there is no paint on the exterior," says Moore. "That's highly unusual."
After eight years of planning and building, the New Kent Winery opened its doors for business on May 31, 2008. "Together our design team worked to create this exciting winery that will stand the test of time," says Johns. "This remarkable winery would be at home in Napa Valley or the Bordeaux regions of France. Our guests enjoy this setting; they enjoy the tours of the winery as we explain the history of the materials used in the construction of the building and they enjoy sampling our wines at our beautiful tasting bar. It has achieved our goal of setting a high standard of excellence and certainly is considered a 'must see' for the wine-loving public."