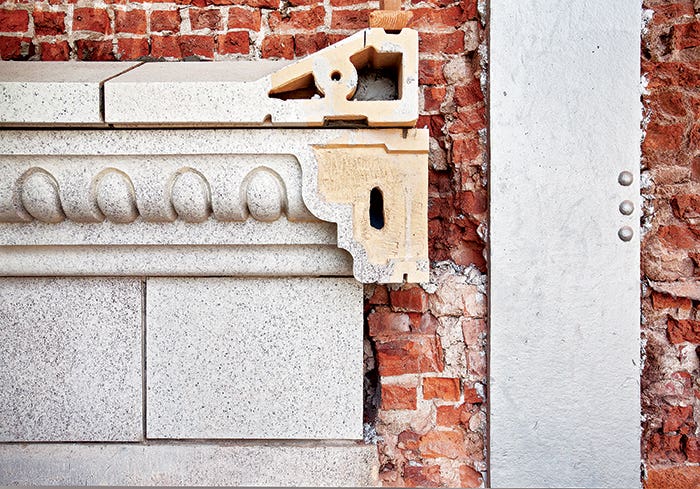
Public Buildings
Historic Courthouse in Brooklyn, NY, Gets an Exterior Facelift
PROJECT
Conrad B. Duberstein U.S. Bankruptcy Courthouse, Brooklyn, NY
OWNER: U.S. General Services Administration, New York, NY
ARCHITECT:Goody Clancy, Boston, MA; Jean Carroon, FAIA, LEED Fellow, principal in charge; Jill Verhosek, project manager
GENERAL CONTRACTOR:Nicholson & Galloway, Bronx, NY
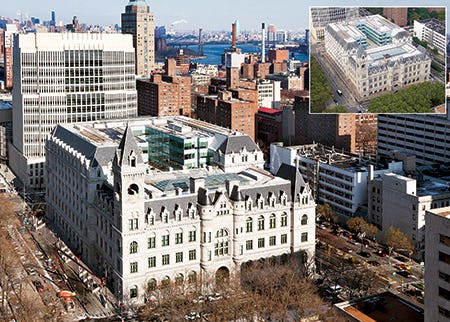
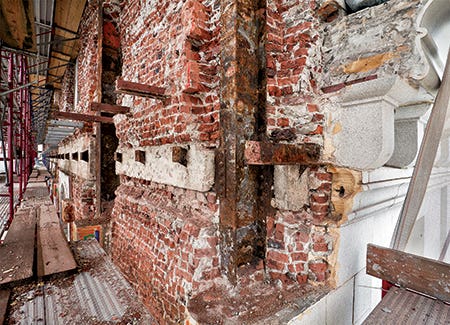
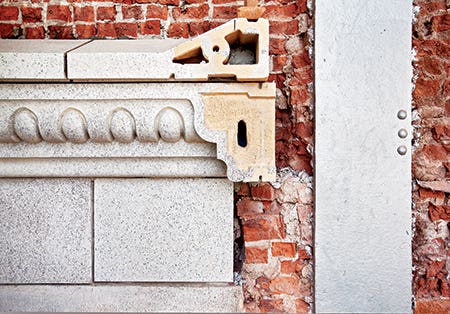
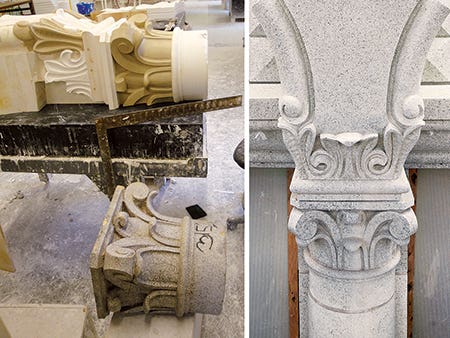
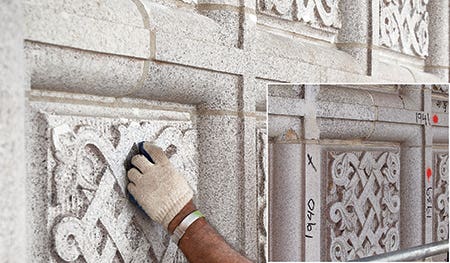
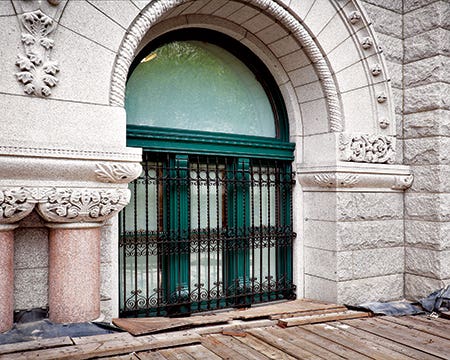

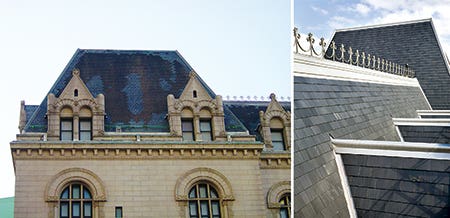
By Martha McDonald
One of Brooklyn’s most elegant historic buildings is the Conrad B. Duberstein U.S. Bankruptcy Courthouse in the heart of the downtown civic area. The original building, measuring approximately 230x130 ft. was designed by Mifflen E. Bell, supervising architect of the U.S. Treasury Department. Planning and design began in 1885 shortly after the opening of the Brooklyn Bridge. Completed in 1892, the four-story Romanesque Revival granite-faced masonry building with bearing walls was built around a central atrium and skylight. It originally functioned as a post office and courthouse with four courtrooms.
By the 1930s, Brooklyn’s postal service needs had expanded and the courthouse was expanded as well. James A. Wetmore, acting supervising architect of the U.S. Treasury Department, designed a seven-story addition in the same style. This approximately 230x190-ft. U-shaped building more than tripled the size of the building, adding two more courtrooms and created a structure that filled a city block. It was completed in 1933.
The original granite-faced masonry building with bearing walls features a slate mansard roof and wood windows. A 180-ft. tower at the southwest corner is one of the notable features and other ornament such as round tourelles, arched windows, belt courses and carved ornament have made the building stand out in the area.
The addition, while similar in appearance, is a different structure. The exposed basement, first floor, second floor window surrounds and transition bays are granite-faced masonry, but the majority of the building is terra-cotta cladding embedded in and anchored directly to brick back-up with ferrous metal fasteners and embedded steel columns. In 1966, the building was designated a New York City Landmark and in 1974 it was listed in the National Register of Historic Places. In 1999, the General Services Administration (GSA) purchased the building.
A $200-million interior restoration led by R.M. Kliment & Frances Halsband Architects of New York City was completed in 2005. This included the insertion of a four-story, 85,000-sq.ft. curtain-wall addition into the courtyard of the Wetmore building. It cannot be seen from the street. (Traditional Building, April 2007)
The next phase was the restoration of the historic exterior, including windows and roofing.
This six-year, $60.96-million project was led by Goody Clancy of Boston. The survey and investigation phase lasted two years; then after three months for bidding, construction took four years and was completed in late 2013.
Vertical Access of Ithaca, NY, was brought in to do a hands-on survey of the exterior, using industrial rope access. Aerial lifts were not possible because of site constraints.
Speaking of the site, it was one of the major challenges. Because the fully occupied building is located in a busy downtown area with lots of pedestrian traffic, the sidewalks and entrances had to be kept clear. To deal with this situation, sidewalk bridges were constructed and all staging, materials storage and trailers were positioned there. In addition, during window repair and restoration, window boxes were built to protect the occupants from noise and debris, and to protect their privacy.
The scale of the job was immense. To summarize, approximately 75,000 sq.ft. of granite and terra-cotta façades were repaired. Approximately 16,000 pieces of terra cotta were replaced as well as 25,000 sq.ft. of slate roofing along with the sheet-metal flashing and gutters. In addition, 1,200 wood windows were restored – and all of this was done while the building was fully occupied.
“This project is quite unique because of the way the GSA structured the process,” says Jean Carroon, FAIA, LEED Fellow, principal in charge. “From the selection of the design team through the Design Excellence Program (which ensured peer review in design and construction) to the innovative contractor selection. The GSA brought the construction manager and three general contractors on early for cost estimating, funded invasive investigation and then had a competitive bid with GCs very familiar with the building and the documents. The GSA also engaged a team for exterior envelope commissioning, which was a relatively new concept a few years ago. The GSA didn’t have to do it this way; it was a very creative and responsible use of our tax dollars and Goody Clancy was proud to be part of the highly collaborative team.”
“With the exception of the curtain-wall addition in 2007, there had been no major alterations, and only piecemeal repair work to the exterior of the building,” says Jill Verhosek, Goody Clancy project manager. “The Goody Clancy team was hired to restore the exterior façades, which at this point required extensive restoration. We are excited to see the potential of this building realized.”
The granite cladding on the 1890s building and at the base of the 1930s building was repaired and restored. The original granite was Bodwell Blue Granite supplied by the Bodwell Granite Company in Vinalhaven, ME. When the addition was built, granite for the exposed basement and second floor window surrounds was Goss Pink Deer Isle granite from a quarry in Stonington, ME, since the Bodwell Granite company was no longer in operation by that time.
During the recent restoration, the original Bodwell Blue Granite was salvaged on-site and used for the 1890s building, while Pink Deer Isle granite from Berkshire Stone in Winsted, CT, was used for the addition.
The restoration of the terra cotta on the addition was one of the largest terra-cotta projects in the country, involving both extensive repair and replacement. All areas were considered to be in fair to poor condition. The team had found extensive glaze failure, open and deteriorated joints, soiling, corroding ferrous metal anchors, and vertical crack systems in the ashlar piers. “The failing roof and façade was becoming a life safety issue,” says Verhosek, “especially above the cornice. Pieces of damaged slate tile and terra cotta were spalling and disengaging from the building. Part of our charge was to determine what could be saved and what could be replaced.”
Replacement Materials
The design team evaluated various alternative replacement materials, including terra cotta, granite veneer, glass-fiber-reinforced polymer (GFRP), glass-fiber-reinforced concrete (GFRC), and cast stone. Ultimately terra cotta was selected as in-kind replacement. Goody Clancy worked closely with the fabricator, Boston Valley Terra Cotta, to replicate the historic profiles, tooling and speckled patterns of glazing on more than 16,000 units. The cementitious patch repair, glaze patch repair and grout injection for crack repair was supplied by Edison Coatings, Plainville, CT.
The existing roof, which was comprised of Monson slate and lead-coated copper gutters and flashing, was in fair to poor condition. Again, the design team evaluated various alternative replacement materials, including slate, rubber tile, ceramic tile and slate/clay reinforced fiberglass. They selected slate for its durability, aesthetics and constructability.
The gutters and flashing, which had been replaced previously in the 1960s, were replaced this time using lead-free alternative sheet metal, Freedom Grey, tin-zinc coated copper, supplied by Revere Copper, Rome, NY. The slate, Unfading Black, was supplied by North Country Slate, Ontario, Canada.
The building’s 1,200 single-glazed wood windows were another significant part of the project. Again, various options were considered. The decision was made to restore in kind and to replace the glazing. Femenella & Associates of Branchburg, NJ, was brought in to restore and repair the windows using Spanish cedar wood (supplied by TBM Hardwoods of Hanover, PA) for replacement elements. New weather stripping was installed, and to improve the thermal performance, the upper sashes were fixed in place and all existing glazing was upgraded.
“The typical window type was double hung,” says Verhosek. “Insulated glazing units (IGUs) were added and the upper sash, sidelites, and transoms were fixed. Only the lower sash remained operable. It was important to the GSA to maintain operability.”
She also points out that this work was done during the economic crisis and was completely funded by the American Recovery and Reinvestment Act of 2009 (ARRA). “This project actually went forward because of the ARRA funding.”
The effort has paid off in many ways. A beautiful building has been restored to serve the community for many more years, and the project just received a 2014 Lucy G. Moses preservation award from the New York Landmarks Conservancy.