
Public Buildings
Restoration of the Martin Luther King Jr. Federal Building
Project: Restoration of the Martin Luther King Jr. Federal Building, Atlanta, GA
Architect:Lord, Aeck & Sargent, Atlanta, GA; Rob Wanderman, associate; Susan Turner, principal
By Lynne Lavelle
On January 15, 1929, just months before prices plummeted on the New York Stock Exchange and the Great Depression began, Martin Luther King Jr. was born on Auburn Avenue in Atlanta, GA. Both events would have immeasurable influence on the 20th century, and are fused in Georgia marble and granite at the Martin Luther King Jr. building on 77 Forsyth Street.

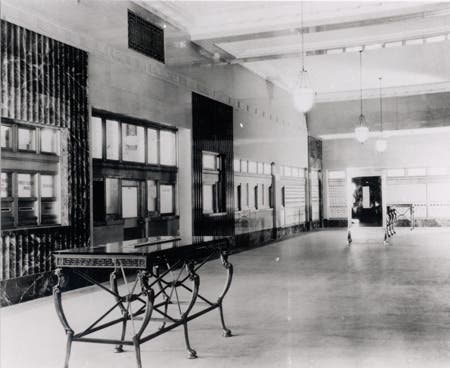
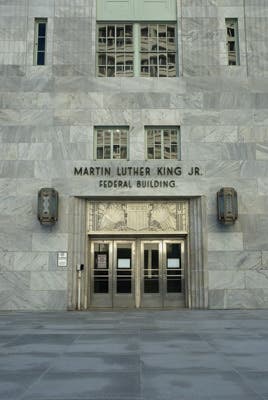
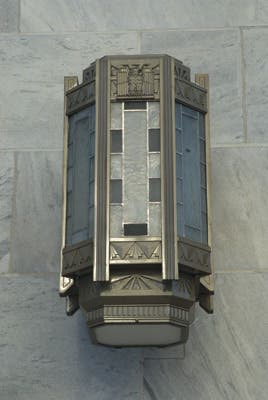
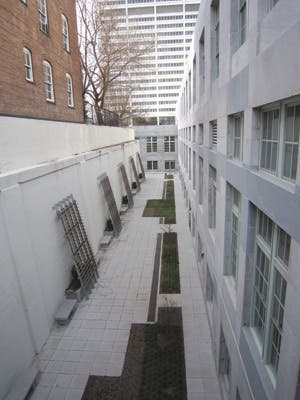
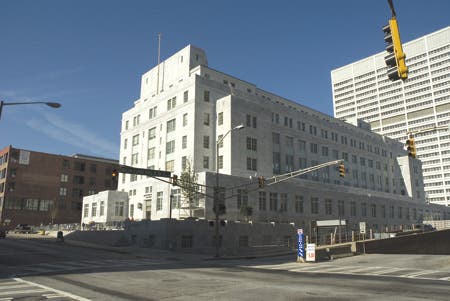
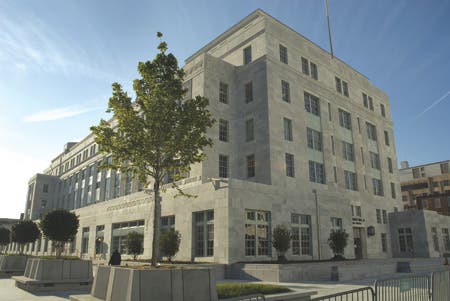
Originally the main U.S. Post Office for Atlanta, the building was constructed in 1933 as part of a Depression-era public works program and in 1988, became the first in the nation to be named in honor of the late civil rights leader. Since 1981, the building has been under the management of the General Services Administration (GSA), which oversaw its expansion from five to seven stories totaling 377,000 sq.ft. by creating interior mezzanine floors. Upon completion of a rehabilitation led by the Atlanta office of Lord, Aeck & Sargent (LAS), it will house the GSA’s Southeastern headquarters.
The Exterior
Since the early 1990s, the three-phase project has been led by LAS’ Historic Preservation Studio, most recently under principal Susan Turner and associate Rob Wanderman. Fusing restoration, rehabilitation, renovation and sustainable design, the firm is targeting LEED Silver certification while preserving character-defining original features. Recently, the firm completed the exterior restoration of two granite base stories (including a day-lit basement) and six marble stories.
The process involved tagging, cataloging and reinstalling 6,000 façade stones at shelf-angle floor lines, plus re-pointing and cleaning. “When we first started, the building was in pretty poor shape,” says Wanderman. “Certain things were done in the ’80s and ’90s that had accelerated deterioration: They had used sealant over all the mortar joints, which had trapped water within and caused a lot of rusting of the steel shelf angles. This rusting had caused expansion, causing the stones to shift.”
Though the original scope of work included removal and reinstallation of all the stone cladding, it was decided upon further investigation that removing strips of stone – two courses above every shelf angle – would be safer in the short- and long-term. “As the building is an urban site, there is very little layout space,” says Wanderman. “And our structural engineer [Wiss, Janney, Elstner Associates, Inc of Northbrook, IL] pointed out that as the bond between the stone and the brick back-up was so strong, removing it all would actually diminish the integrity of the building.”
All of the steel shelf angles were removed and replaced with stainless steel and the parapets surrounding the building were rebuilt. In areas that were stacked-bonded rather than running-bonded, such as the upper-level blond-brick façade on the south side, all of the stone was safely removed. “The south façade was really designed not to be seen by the public, so it didn’t require as elaborate a cladding,” adds Turner.
The exterior character was greatly enhanced by more than 600 original steel windows, in many varieties, which were repaired rather than replaced. Inside and out, the windows were stripped of lead-based paint, repaired, repainted and sealed. Only 106 windows required full replacement, and were designed and fabricated to blend seamlessly with the originals. “They have double-hung, casement, awning-type windows – you name the window type, it is there,” says Wanderman. “It is an absolutely beautiful building. And the windows were such important, character-defining features that we had to keep them.”
All stone, brick masonry, terra cotta, window and roof replacement was carried out by Western Waterproofing of St. Louis, MO. The general contractor was The Beck Group. Replacement terra cotta was suppled by Gladding McBean; replacement stone was supplied by Crystal Marble.
The Interior
With the exterior now completed, interior construction has begun on the building’s first three floors. The first order of business was to reopen a two-story light well that had been closed up in the ’80s; this transformed the under-utilized basement into an attractive terrace level. Allowing light to penetrate the lower stories on two sides opened up the space, physically and otherwise, after two decades in design limbo.
“They had planned to connect all of the government buildings with a passage called ‘Government Walk,’ and this light well was closed in as part of that,” says Wanderman. “Storage was created below, but over time, it leaked and became a dumping zone. Opening it back up was one of the first things we did and it completely changed the quality of the space – the basement became day lit, as opposed to this dank, dark place.” At the bottom of the light well, a new garden visually links the two exterior plazas to the north and south, restored by landscape architect AECOM.
Besides the original postal lobby and a secondary lobby, the firm also uncovered additional historic fabric during the demolition process such as wainscot and historic plaster walls, hidden behind drywall. “We had more historic fabric than we originally imagined when we started the project,” says Turner, “so we reworked the design intent to essentially restore the exterior walls. The modern interiors that are needed for GSA will be held back from these walls, creating a modern insertion within an historic shell.”
That insertion will be a departure from traditional office layouts, whereby the highest rank earned the most daylight – the coveted “corner office.” Instead, the offices will inhabit the interior, with views of the cubicles to the perimeter. “It’s an interesting way of looking at the space,” says Wanderman. “And it really helps for LEED because it lets daylight penetrate all the way into the center of the building, and allows everyone to have access to it.”
LEED Considerations
Other LEED measures include low-flow plumbing fixtures, bike racks, native plantings, water-detention systems, a recycling area, and materials produced within a 500-mile radius. And the building’s location is fortuitous: “We are an urban site, so we are close to three bus lines, which stop right in front of the building, and we are also a block away from the train system,” says Wanderman.
From a distribution standpoint, updating the existing mechanical, elevator and HVAC systems was relatively straightforward. The building’s large open spaces – originally mail sorting rooms – offered a lot of flexibility with running duct work, and few tight, challenging spaces. “It’s fair to say that most of the mechanical equipment is pretty much staying in the same location that it was prior to the work,” adds Turner.
The firm gained another LEED point by replacing the existing roof, which had sustained significant water damage, with a Hydrotech roofing system. Often used on “green roofs,” in this case the system was topped with a layer of insulation and secured by light-colored ballast. “On a sunny day, it adds a glimmer to the building,” says Wanderman. “It’s really pretty. That was an unexpected effect – it just glows now.” Though nobody can claim credit today, the building is in fact an early example of LEED principles, albeit spurred by economic, rather than environmental, concerns. “The building was originally to be constructed in Indiana limestone,” says Wanderman. “But they decided to use Georgia marble and granite. All of the finishes are from Georgia, Tennessee and Alabama. It is all from the south, because they decided to keep the work close to home.” The pre-Depression alternative exists only on paper: “It is funny to look at the drawings and see limestone everywhere,” adds Wanderman, “because there is not one bit of it on the building.” TB