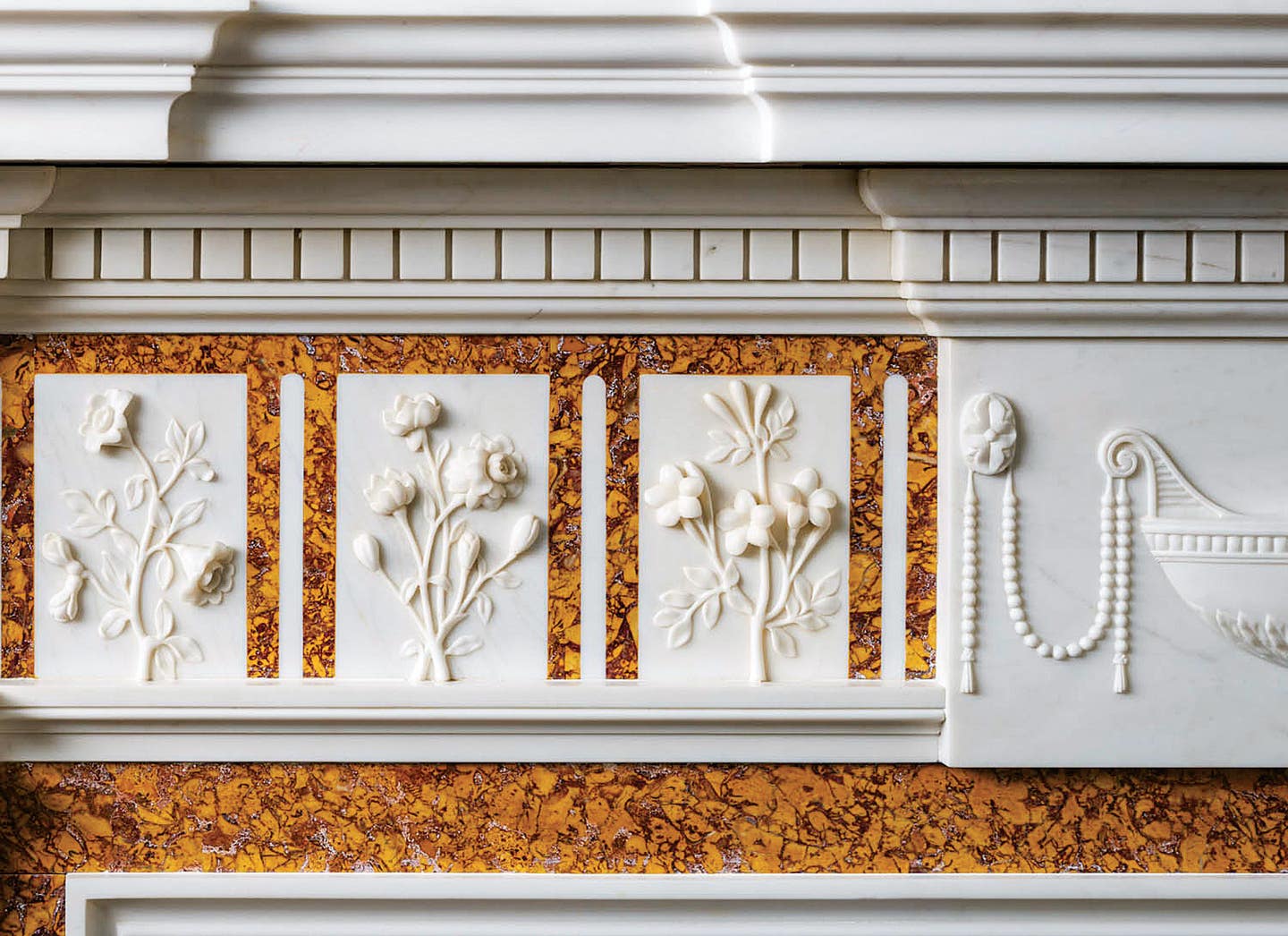
Product Reports
Chesneys Reproduction Mantels
With workshops in Italy, Portugal, and China, Chesneys specializes in the reproduction of authentic period fireplace designs in stone, marble, and cast iron. What began as an antiques dealing venture evolved to include the restoration and ultimate re-creation of museum-quality mantels. Chesneys reproductions are based on designs by preeminent British architects dating to the 18th century. Creative Director Judith Prause explains: “We were the first licensees for the Sir John Soane Museum, which gave us access to all of his drawings. We did the same with Edwin Lutyens’s family trust, so now we have that archive. And because Sir John Soane bought all of the drawings from Robert Adam’s office, we have those, too. It’s the Adam maquette drawings that are used to make some of our reproduction mantels.”
Robert Adam (1728–1792) was a Scottish architect, interior designer, and furniture designer credited with popularizing the Neo-classical style. He applied those stylistic details to fireplaces, which he viewed as “key to the balance and symmetry of a room.” Adam used marble for carved details and for colored inlaid patterning in convent siena, Sicilian jasper, and Spanish brocatelle. The Adam Collection comprises designs for six chimneypieces selected from over 300 original drawings.
Molds taken from original 18th-century mantels are used to caste clay maquettes, or models, which are sent to one of Chesneys’s three workshops. Carvers and polishers use the copies to trace the design onto the stone, which they then cut away at until they get to the various depths needed—at which point they perform hammer and chisel work. “Everything is measured precisely,” says Prause. “There’s no creative license given to anyone. If we are creating an Adam mantel, we have the drawing from John Adam’s offices. The classical details stay exactly as they were drawn and proportioned, which is why they look so good.”
Traditional Materials
Using traditional stone masonry tools and techniques, carvers and polishers work with materials—sourced primarily from Italy, as well as Spain, Turkey, and the U.K.—that are as close as possible to those used in Adam’s time. Of course, the scale of production has changed. “We are buying blocks of marble that weigh 20 tons and are the size of a garden shed,” muses Managing Director Alistair McCowan, noting that the company also carries a stock of inlay materials. The type of material and level of ornament determine where a piece is to be carved. For instance, a French Rococo-style mantel, which has curved detailing but not a lot of intricate carving, will be done in Italy. But something like the “Pattern 40 Brocatella” mantel in the Chesneys New York showroom—featuring ten panels, each measuring approximately four inches wide by eight inches tall, of carved-marble flowers inlaid into a frieze—will be done in China, where commissions requiring finer craftsmanship are sent. “The hand carving that we do in our Chinese facility is likely better than any you’ll find in a high-quality Italian workshop,” McCowan says. “There’s a long tradition of stone carving in China.” (The Pattern 40 Brocatella took one master carver six months to complete. Typical 18th-century reproductions take between 18 and 20 weeks.)
According to Prause, when working with highly figured stones, the carvers select the areas that will yield the most attractive results. “This material is very costly so there is much thought given to the visual and structural result prior to cutting into the stone,” she explains. “When you take a raw block of marble and carve into it, you don’t know what is going on under the surface. It might be beautiful on the exterior but when you cut into you might fine strange coloring or veins. Or vice versa.” For this reason, Chesneys buys the blocks, decides which mantels will look the best in the given stone, and pre-makes and sells them. “That way, people can see exactly how the figuring lays out on the stone.”
Chesneys also buys rare and unusual blocks of material, which are typically smaller in size, yielding four to five mantels total. “Often people want opulent materials but they want simple design—something quite contemporary,” McCowan notes. “Our Limited Edition Range is an 18th-century collection profile but we have modernized it by using these different materials.” Bespoke commissions are another of Chesneys’ offerings. McCowan describes one currently being worked on; it includes ten carved mantelpieces for a single client who has chosen specific floral details that she has had her architect draw up. Those drawings are being used to make clay maquettes for the carvers to copy.
McCowan speaks to the master carvers’ expertise, appreciating the time it takes to develop the skill set. “It takes years to become a really good carver. It’s one of those things—you’ve got to have it in your blood.” Chesneys’s staff includes 25 carvers and five polishers—it is the latter who are responsible for the highest level of detail. The hammer and chisel work is performed with wooden and metal mallets, or dollies, of different sizes and weights to provide consistency in the depth of cuts. It is the combination of historical accuracy and master-level artisanship that has earned Chesneys its reputation. “Our carvers make mantel pieces in exactly the same way as one would construct an original 18th-century marble or stone mantel,” says McCowan. Prause adds: “Because we are fortunate to have a large inventory of antique mantels, we can get the scale and the detail of all of those particular moldings with real depth to it—we’ve got a lot of references.”