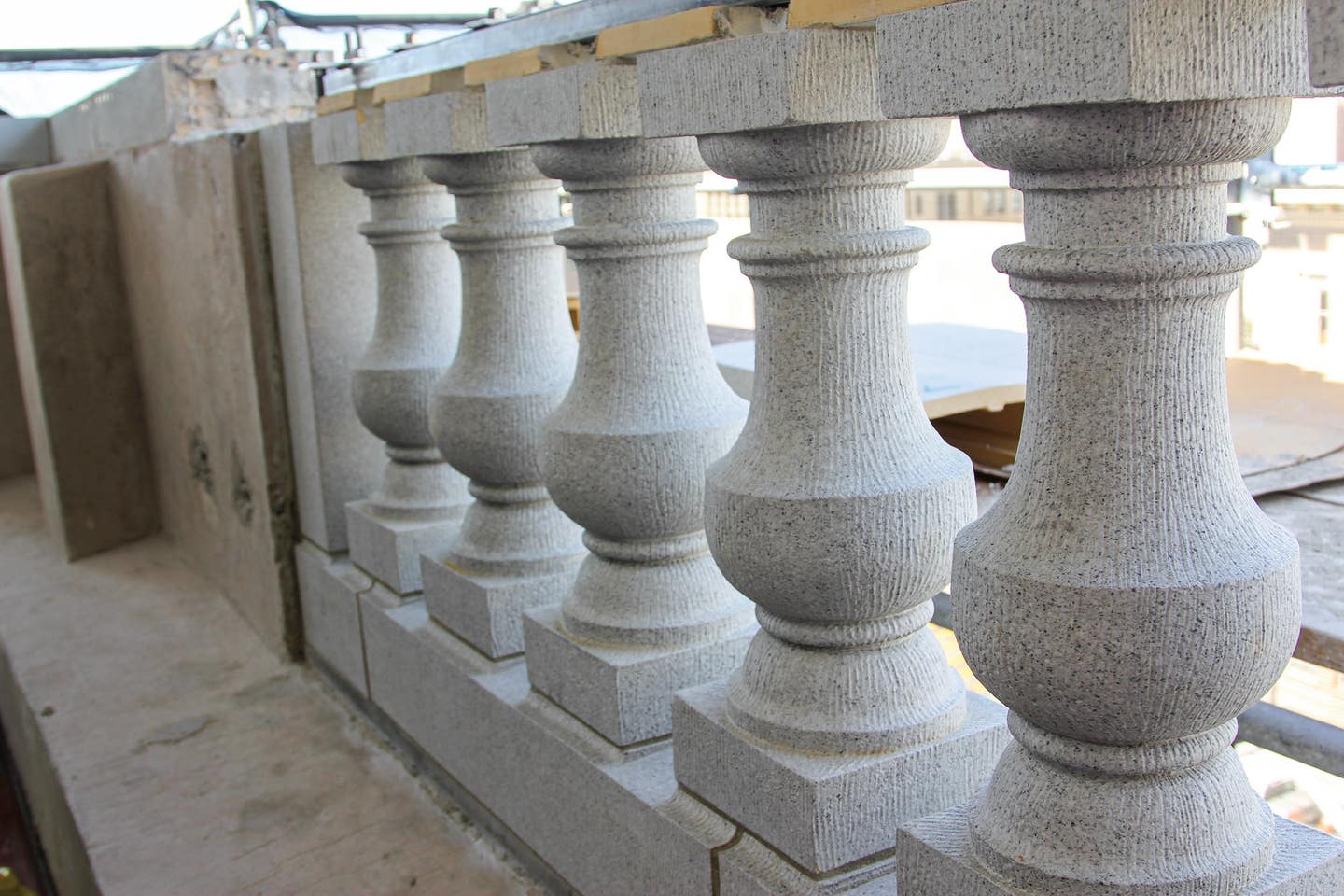
Features
Taking Care of Terra-Cotta
Historic building restoration projects are seldom a pure play, as most any contractor or architect will tell you. “We wear several hats,” says Tom Lewis, president of Lewis Restoration and Consulting in San Francisco. “We’re very good at large, masonry façade restoration—be it granite, terra-cotta, brickwork, or GFRC (glass fiber reinforced concrete)—and we also have considerable experience with waterproofing details and related consulting.”
To illustrate how varied the work can be, Lewis points to their recent project at the War Memorial Veterans Building, an immense 1932 Beaux-Arts performing-arts center in San Francisco designed by Arthur Brown Jr.
Among the key features of the building are 72 terra-cotta balustrades—one running at the second-story level and another across the attic level. “The balustrade assemblies were in very rough condition,” explains Lewis. “Each baluster is reinforced with steel rebar that had corroded, leading to corrosion jacking, which cracked individual balusters and compromised the railings. So we replaced all 72 balustrade assemblies, including railings, bases, and balusters with new terra-cotta to match the existing units.”
By good fortune, they were able to commission new terra-cotta from Gladding, McBean LLC of Lincoln, California, the original manufacturer of all the terra-cotta for the building. “Gladding, McBean supplied much of the historic terra-cotta from California to Chicago during the heyday of terra-cotta construction, and they still have the original drawings for the War Memorial Veterans Building. Using those drawings in combination with the existing conditions, we were able to replicate the terra-cotta and reinstall all 72 balusters and assemblies.”
He says getting the details right required extensive coordination between the manufacturer and the historic preservation architect. “We had to produce mock-ups, so all the granular features of the terra-cotta—the coarse, corrugated graining and what I call the “speckle patterns” had to match precisely.” Much of the terra-cotta on the building is fabricated to resemble Sierra White Raymond granite, a famous California stone used in the base.
Beyond replicating the terra-cotta, there was the challenge of matching the glaze. “Nowadays, in terms of color and patterning, the formulas used back in the 1930s are not the same formulas permitted today because there are environmental restrictions on materials, such as pigments and heavy metals, but I think Gladding McBean’s results were a big success.” The value of manufacturing the terra-cotta was approximately $500,000, a large portion of the work.
A third aspect of the project was repairing the glaze and bisque spalls in the original terra-cotta. “A bisque spall is where the actual clay substrate of the terra-cotta is eroded, missing, or cracked,” explains Lewis. “Here we replaced any broken clay with polymer-modified mortar to match the existing in compressive strength.” With a glaze spall, on the other hand, it’s the surface glaze that’s missing. This allows moisture into the clay and permits bio growth to form and with it continued deterioration of the terra-cotta. “So one large goal in the project was to recoat the missing glazing—especially much of the frieze at the top of the building where there’s a lot of exposure. After cleaning the exposed bisque and removing and patching loose material, they treated any bio growth with a biocide. To match the original glaze in color and pattern, Lewis’ company carefully painted on a custom 100 percent acrylic glaze with a suspension of black granular speckles. “The ‘reglazing’ dramatically improved the building visually,” explains Lewis, “and also enhanced the waterproofing and conservation of the terra-cotta.”
Inside the building, the lobby is built with beautiful cast stone blocks, which Lewis’ company cleaned and repointed. “The joints are very small, almost like tile joints, so the repointing was very intricate.” Even more intricate was the task of removing selected blocks in order to make cut-outs for adding outlets and electro-mechanical utility boxes in the walls of the lobby. “These blocks are very large—roughly 12” x 24”—and pulling the stones out without damage to the blocks or the surrounding blocks, and then putting the stones back in place, was very challenging.”
Unfortunately, the Southwest corner of the lobby had not been as lucky—in fact, a whole section of the sandstone had delaminated from the substructure and collapsed onto the floor of the lobby. “The right-side wall in that lobby, roughly a mirror image of the original wall on the left, was still intact, so I had a company come in and laser scan the wall on the right. With the laser scanning information we knew exactly how everything was placed.” After hiring a company to replicate the damaged stone, Lewis’ company reproduced the wall on steel framing. “If you’re in the lobby, you wouldn’t be able to tell the difference by looking at it.”
The natural finishing touch was to clean the terra-cotta and the granite. “Using hot-water assisted power washing, and we cleaned the entire exterior of the building, producing a dramatic visual change and enhancing a lot of features, like the lions on the ground floor.” After all the meticulous work, Lewis adds “it was really rewarding to see the building sparkle like new again.”
Gordon H. Bock is an architectural historian, instructor with the National Preservation Institute, and speaker through www.gordonbock.com.