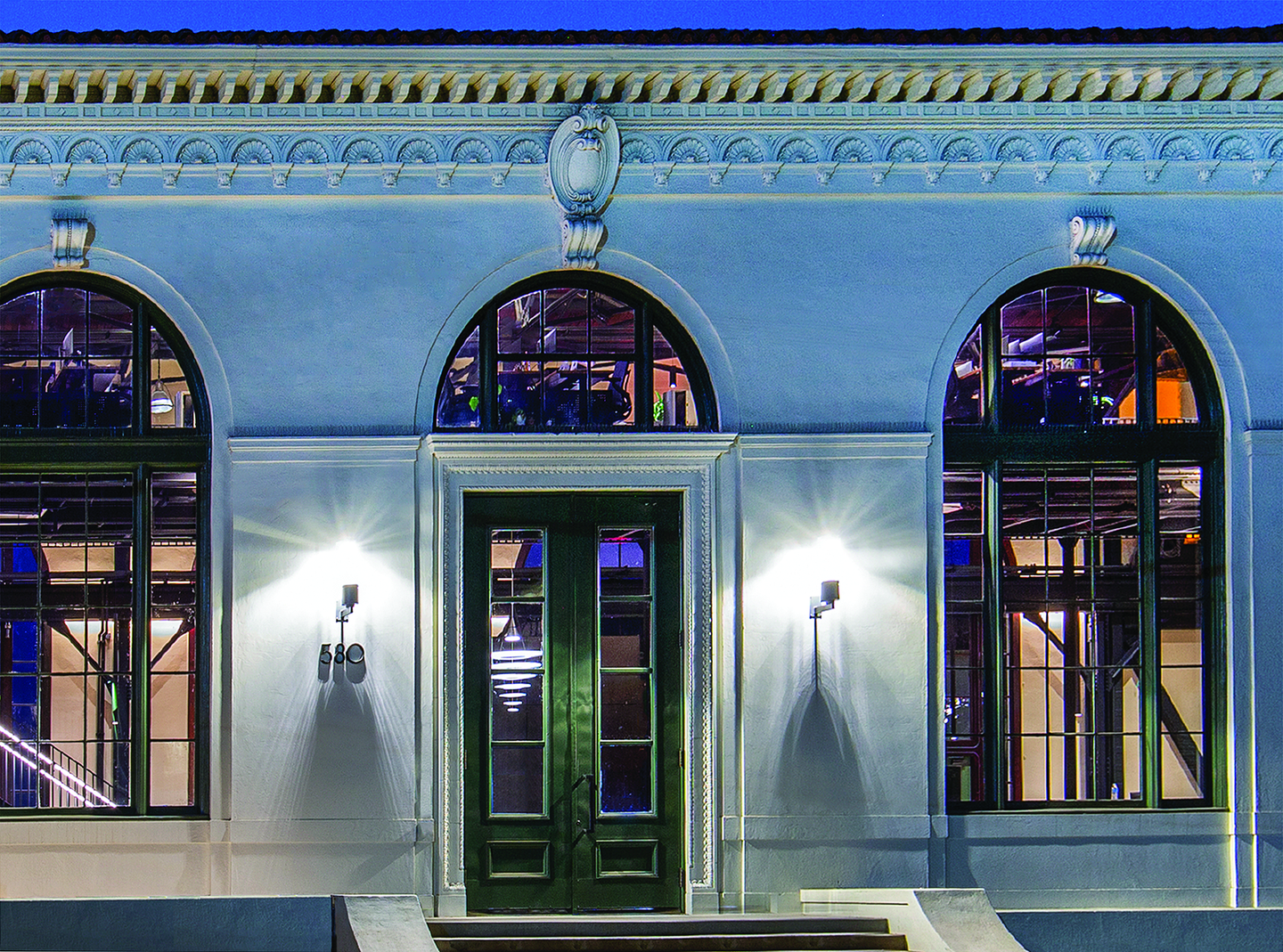
Features
Re-Energizing a Powerhouse
When the Port of San Francisco engaged Orton Development, Inc. (ODI), in collaboration with Marcy Wong Donn Logan Architects to convert the seven-acre site of a former shipyard into what is now called the Pier 70 Historic Core, it became a multiyear, multibuilding project. Adapting the Powerhouse, however, was among the final stages. “It was such a stunning little building when we first saw it, but in pretty bad shape,” explains Kent Royle, AIA, principal at the Berkeley, California, firm. “So, the client, Orton Development, Inc., decided to leave it for last because it was the most demanding in terms of obtaining usable floor area for the amount of investment.”
Indeed, the Powerhouse has an exceptional pedigree. Built in 1912 and designed by Ecole des Beaux-Arts-trained architect Charles Peter Weeks as “Spanish Renaissance architecture,” it features a hipped roof of mission tiles, five 18-foot-tall, arch-topped windows, plus hex tile floors and finishes in hardwood, marble, and brass. For nearly a century it supplied the shipyard’s multiple power needs—principally compressed air for pneumatic tools and forges—through four massive, electrically operated air compressors.
As Royle explains, the challenges with adaptive re-use, historic preservation projects are severalfold. “First, it’s often cheaper to simply knock the building down and start afresh. The key then is to figure out a way to preserve a really great old building, and the same beautiful experience, by getting the most value for every dollar you spend.” The second challenge, he says, is to make upgrades that contribute to an attractive project that pencils out. “In this case, the building was going to be leased, so we really needed to maximize the leasable square footage.”
At first glance, the Powerhouse, with its single large, open space, seemed a reach. “It had a basement, but the majority of it was filled with four huge pylon foundations to hold up four massive compressors through cut-outs in the floor.” In addition, there was an electrical substation built into part of the daylit basement that controlled, basically, the rest of the Pier 70 complex and adjacent properties under rehab. “So that had to remain operational the whole time.”
With the basement almost completely occupied, ODI’s development strategy included removing three of the four huge pylon foundations to reclaim it as usable space. “That would give us area for those kinds of functions that don’t require extensive daylight, such as meeting rooms, bathrooms, janitorial space, storage, and a break room. This allowed us to keep the existing main floor as a big, open work area.”
That 5,342-square-foot main floor is nearly 30 feet high to the top of the walls, and then another ten feet above that. To take advantage of this very tall space, the architects designed an L-shaped mezzanine, with stairs and elevator, to run around two sides of the building. “It stands on tube steel columns, painted black. The mezzanine itself is wood-framed, in keeping with the wood ceiling, and we tried to match the coloring. We were able to add a lot of square feet on that mezzanine.”
Royle says they were able to work with the tenant to design an open furniture layout. “We used distinctive features as room dividers, such as a nice screen wall to mark the entrance/public area from the work area. Then the remaining compressor—which is really stunning—sort of divides off a meeting area.” More informal breakout areas lie under the mezzanine.
For seismic upgrades to a project such as this, Royle says they seek to retrofit in ways that harmonize with the existing structure and don’t stand out noticeably. “We reinforced two of the diagonal corners with braced frames, one of which we were able to hide behind the new mezzanine elevator.” There’s also X bracing across the end wall, he notes, “but it blends in enough with the historic ironwork that it wouldn’t necessarily jump out at a visitor.”
The same goes for adding infrastructure. “The trick with these wide-open spaces is to not muck them up with a ton of new equipment, but rather do it in a way that isn’t obviously invasive.” For example, for HVAC a VRV (variable refrigeration volume) split system was installed that pumps refrigerant around for heating and cooling. “There’s a mass of little lines to each unit, so we worked with the HVAC sub to route the lines on top of the gantry crane, then route them down behind the columns where we could paint them out black.”
Lighting follows the same approach. Royle explains how they worked with lighting designer Darrell Hawthorne to hide as much lighting as possible within the existing structure, all the while highlighting it. “Behind the crane rails we have LED strips that wash the walls to create this nice glow. Likewise, the ceiling: highlight the building structure as a way to light the building.”
The way the Powerhouse sits on a downhill site enabled the architects to work with the National Park Service and California’s State Historic Preservation Office to build a 2,600 sq. ft. addition off the back of the building behind the street. “We planned the addition in such a way that you can just walk out from that main, open work area onto a roof-top deck that looks back toward Mission Bay, the really lively part of San Francisco.” He adds that Orton Development is extremely good at being strategic in how they invest in these properties. “If they’re going to put on an addition, they want it to do double duty to help reinforce the project. The roof deck has a spectacular view of Giants Stadium, the huge UCSF Hospital, and the Bay Bridge, and is just the kind of amenity attractive to the high-tech workers leasing these projects.”
Gordon H. Bock is an architectural historian, instructor with the National Preservation Institute, and speaker through www.gordonbock.com.