
Product Reports
Hand-Carved Stone Mantels
As much as modes of production have evolved, certain architectural elements are still created through age-old methods. This may be no more pertinent than in the case of carved-stone mantels, which, according to three fabricators who still create their products with hammers and chisels, are as popular as ever.
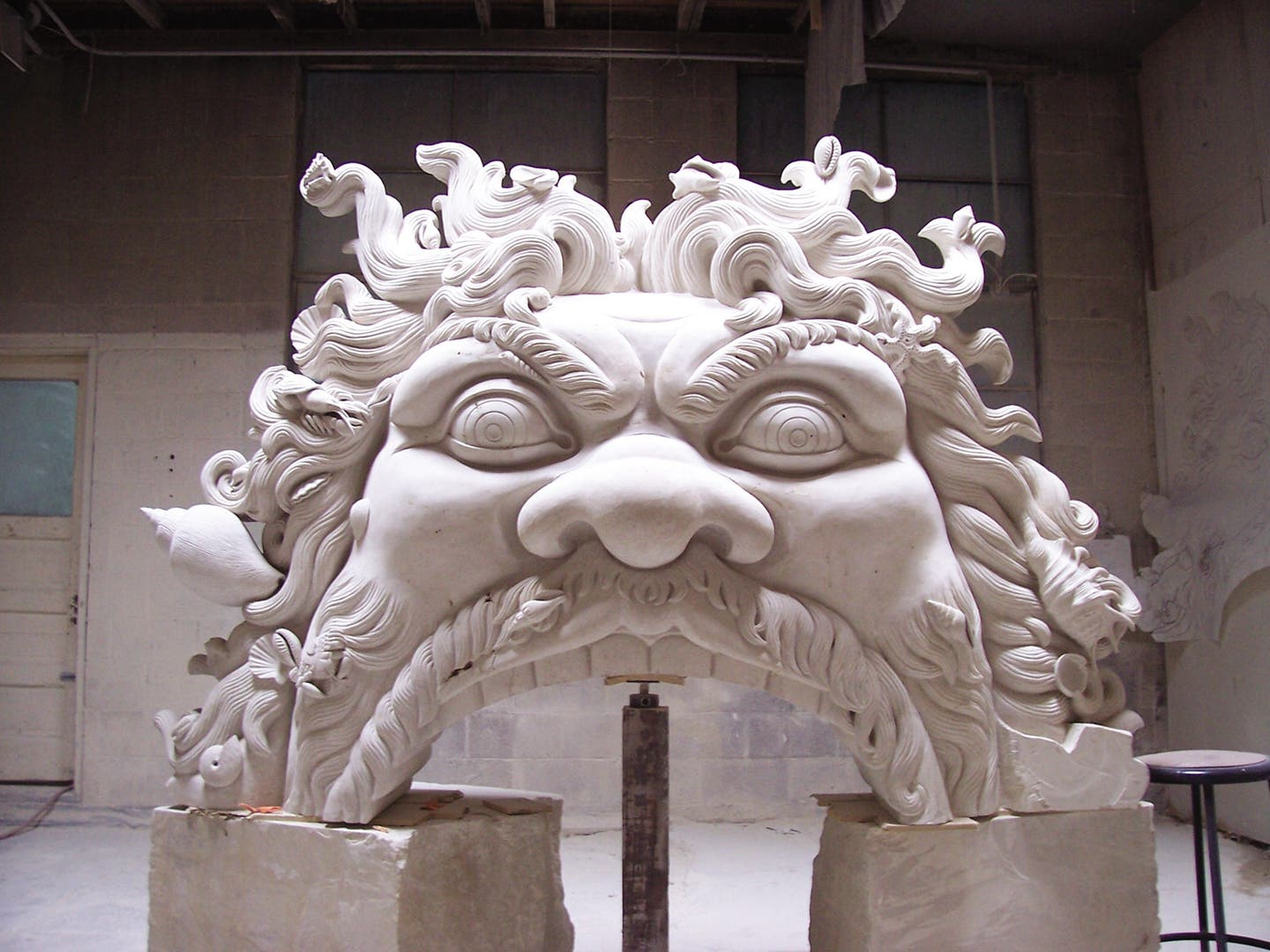



Fairplay Stonecarvers of Oberlin, OH, Traditional Cut Stone, of Mississauga, Ontario, Canada, and DMS Studios, of Long Island City, NY, create carved-stone mantels in a variety of stone types and styles. They specialize in custom work, as mantels are an area where clients generally seek custom designs.
Nick Fairplay, president of Fairplay Stonecarvers, works in marble, limestone and sandstone. At the moment, he says, Gothic and Arts-&-Crafts styles are popular, while there is little demand for French styles. Richard Carbino, vice president of Traditional Cut Stone, also works in marble, limestone and sandstone, creating mantels in custom styles ranging from traditional to modern. “The majority of the fireplaces we have fabricated in the last year have been either in the French or English style and half of those have been embellished with hand carving,” says Carbino. “For the most part, people are choosing medium-toned limestones.”
Dan Sinclair is the president of DMS Studios. He says the process of creating a mantel begins with a general discussion of what the client is looking for – whether, for instance, a Mediterranean-style mantel in limestone or a more formal piece in marble. “From there,” he explains, “we go to the sketch stage, where we provide the client with a few loose sketches to nail down the general feel of what they want and the degree of detail they are looking for. When the client says, ‘Yes, that’s what I want,’ we create a full set of detailed plans and supply the stone – whether it be imported marble or domestic or imported limestone, occasionally granite.”
“Most clients will come in with a photograph of something that they’ve seen or they’ll want us to custom design something,” says Carbino. “We will provide a budget price after our initial meeting. Once we are awarded the project, we will either visit the jobsite or use architectural drawings to confirm all of the relevant dimensions. Then we create a set of shop drawings – which will also be used as placement drawings for the installer – that are sent to the client and architect for approval. The client will send them back to us as approved, or with minor revisions. For detailed carved elements, we’ll submit a rendering as well, and if that’s not enough for approval, we’ll do a full-size model in clay. Once it’s approved, we’ll go from clay to plaster, and from plaster to stone.”
As with any other architectural element, Fairplay stresses that getting the scale of a mantle right is paramount. “Usually we do a full-size set of drawings, so the client can hang that up in the room and get a sense of the scale,” says Fairplay. “That’s really important – often, they give you the dimensions, you make it, and it just doesn’t work in the room.”
While Fairplay Stonecarvers, Traditional Cut Stone and DMS Studios create their products using traditional methods, new technologies are increasingly being utilized in the stone-carving field. “There is a bit,” says Sinclair. “Italy has some very nice and sophisticated CNC [Computer Numerical Control] machines. Most of the molding work could easily be done mechanically – but we don’t have the demand here. Since there’s such a modest demand for this type of thing, it doesn’t pay to buy a half-a-million-dollar piece of machinery for the quantity of stuff we’re asked to do. People are always coming to us to do things that are very unusual rather than usual – things that can’t be done on a CNC machine.”
“We are basically a hand shop,” says Fairplay, “and we’ll farm out some of the CNC work – usually that is quarry based. But people that come to us are looking for hand-tooled stuff.”
Even though their work is hand-carved, Sinclair says that the lead-time is reasonable – generally 60-90 days. “Most of the American customers do not request highly crafted, very detailed mantel pieces,” he says. “So, for the most part, they are not very difficult to do and we can produce a very fine product. Although, on occasion, we get involved in some very complicated, difficult projects.”
Especially in terms of the more complicated projects, Sinclair stresses the earlier his company gets involved in the design process, the better. “Obviously the most important thing to do is to use the knowledge and experience that the craftsmen have,” he says. “In many cases, with the specific ornamental type of thing that the client is looking for, the craftsmen have had much more experience than the architect. Some of the architects that we work with want to have all of the control, and sometimes it comes out okay and sometimes it doesn’t. When we take control, we can assure a client they are going to get really fine, historically accurate work – like for the White House. They asked us to do impossible and perfect, they got impossible and perfect. This is our specialty – the phone rings and someone says, ‘We know this can’t be done anymore, this type of craftsmanship disappeared a long time ago, but maybe you could help us come up with something.’ That’s what I love to hear.”
Fairplay and Carbino agree. “Because we’re custom,” says Fairplay, “people don’t realize we have to order the material if we don’t have it in stock. If they want something like Italian marble, then we have to wait for it to be delivered. That’s the biggest problem – people need to think about the fireplace at least a year in advance.”
“Contract the fabricator as soon as you can,” says Carbino. “If you are going to specify a fireplace that will require a large piece, are you specifying from a quarry that only yields smaller stone? These are things that need to be thought out beforehand. Also, if you want something done right, go to a place that specializes in custom work, as opposed to a place that stocks standard-sized mantels, as you may end up having to make it fit an odd-sized firebox, or the stock sizes may be totally wrong for the room. That could mean the introduction of additional pieces, or a mantel that has to be reduced and looks completely out of scale.”
Once the material is chosen and the appropriate scale is found, Fairplay, Carbino and Sinclair – given their years of experience in the field – can produce a custom carved-stone mantel to just about any specification. From simple to intricate, the mantels that they produce are evidence that some processes are still best done the old-fashioned way.
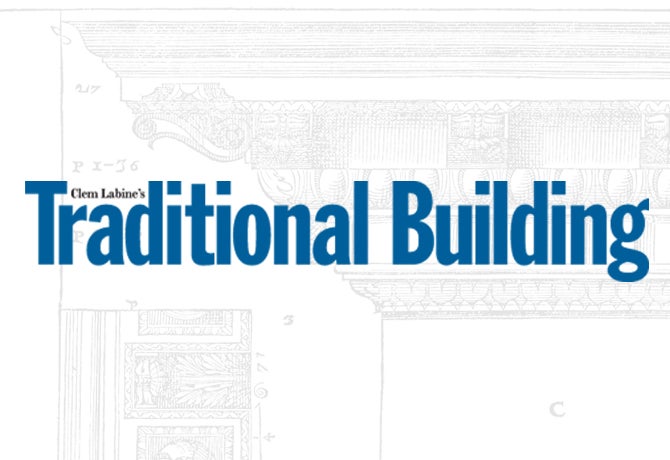