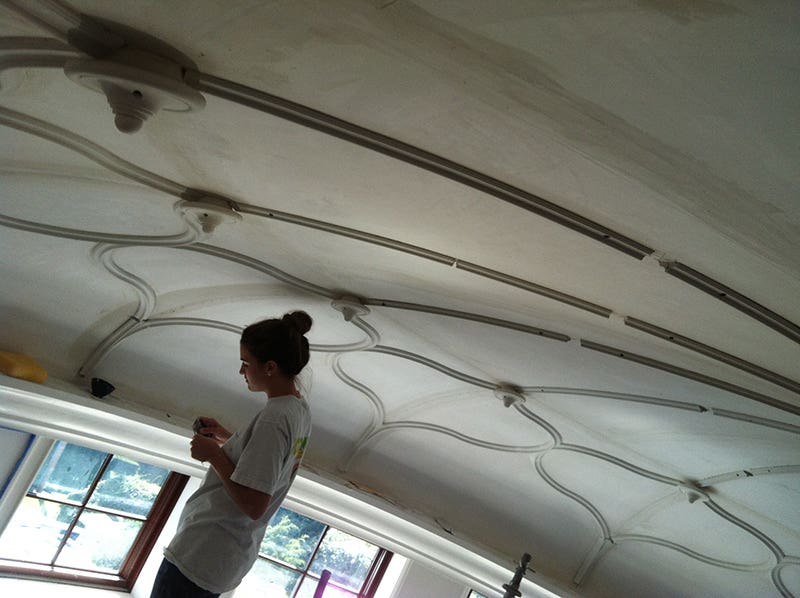
Features
The Practicality of Traditional Plaster Work
By Patrick Webb
As a British colony, the United States inherited a fully developed plaster tradition that would expand considerably from the mid-19th century until the 1940s. Fine plasterwork can still be enjoyed in public settings such as period railway stations, banks, courthouses and capitals across the nation. Many enriched plaster ceilings enduringly grace private residences in historic neighborhoods such as Brooklyn Heights and Peninsular Charleston.
Largely due to the predominance of architectural Modernism and industrial, factory-produced construction systems, there is a common misconception that traditional plaster work only exists as a historical curiosity, impractical if not impossible to specify today. In truth, traditional plaster has been making a steady comeback in new construction for the past 20 years. Below are a few helpful insights for architects, designers, contractors and owners on the advantages and possibilities of using traditional plastering in contemporary practice.
Traditional Plastering
Although gypsum drywall has largely displaced traditional plastering for interior walls and ceilings. I would like to highlight a few specifications where traditional plasters should be considered as a practical alternative:
- Monolithic substrates
- Curvilinear surfaces
- High durability
Monolithic substrates (as opposed to cavity wall systems) are solid substrates, common examples being brick masonry, cast concrete or CMU blocks. Exterior plaster or “stucco” will invariably be a practical solution in the exterior. However, interior plaster applied directly to the substrate is likewise a practical alternative to furring strips and drywall. With a carefully selected binder (clay, gypsum, lime, hydraulic lime or cement) a plaster can be formulated that closely matches the thermal, expansive, permeability and other characteristics of the substrate resulting in a far superior surface that is completely integrated into the substrate.
Curvilinear surfaces which may include walls but are often horizontal ceiling surface such as domes, vaults and the underside of staircases are a logical consideration for plaster specification. I’ve been on many projects where vaults are painstakingly framed out with what is commonly called “ship hull framing” to receive multiple layers of ¼-in. drywall that has to be cut into small strips, soaked and scored in the back to adjust to the curvature. This is completely unnecessary and an inferior construction to traditional plaster over lath, requiring only nominal framing.
High impact and abrasion resistance may not be expectations of walls surfaces for a residential home; however, for commercial and institutional specifications of hotels, museums, shopping centers, universities, airports and similar settings, durability and low maintenance are long term advantages to weigh against initial cost.
Cast Moldings and Ornament
As the millwork industry became increasingly sophisticated, soft “paint grade” woods such as pine and poplar began to displace plaster as the economic plain molding specification. The integration of ornament enrichment into moldings slowed this transition until ornament itself was largely stripped from architectural design in the mid-20th century. Nevertheless, there are many strong arguments for utilizing plaster moldings with the following specifications often being competitive or less expensive.
- Medium to large curvilinear profiles
- Non-radial curvilinear profiles
- Large, complex crown moldings
- Curvilinear oriented moldings
- Ornament
- Low maintenance
Straight moldings can be produced just fine in plaster but it excels like no other medium in being able to contour to curvilinear shapes. I say curvilinear as opposed to radial because plaster is not constrained physically or economically to arcs of circles but can readily accommodate ellipses, hyperbolae, or free formed curves. The process helps to explain this property.
The first step in creating a plaster molding is hand-cutting a reverse metal profile from a template. The profile is mounted on a jig and the plaster is built up in successive layers on a table or ramp. For plaster, it matters little if the profile is large or small, complex or composed of non-radial curvilinear elements. In fact, the molding itself can be curvilinear such as vertically for architraves surrounding arches, or horizontally as for molding applied against a curvilinear surface or even complex helix shapes as sometimes encountered in the stringers of descending staircases.
With a return to interest in traditional architecture there has been a corresponding interest in ornamentation. As with plaster molding profiles, the work of plaster ornamentation is by hand so there are no mechanical constraints. Often much time is invested in a single model of high quality from which a mold is produced. Multiple plaster casts can be easily and economically produced. The more detailed the enrichment and the more units produced, the more value can be achieved with ornamentation.
If you are an architect, designer or contractor seeking to understand and properly specify traditional plaster, I would recommend that you include an experienced plasterer in the design development phase of your project. It will open up beautiful design opportunities while supporting you in fulfilling your fiduciary responsibility with you or your client’s budget.
Patrick Webb is a heritage and ornamental plasterer, an educator and an advocate for the specification of natural, historically utilized plasters: clay, lime, gypsum, hydraulic lime in contemporary architectural specification.